
103 Mineral Resource Classification Mineral Resources were classified as Inferred, Indicated or Measured depending on increasing levels of geoscientific knowledge and confidence. The main sources of uncertainty are structural disturbance, reef variability, sampling, laboratory analysis, data processing and estimation error. Drillhole data quality is similar across all Mineral Resource classes (Inferred, Indicated and Measured) as common sampling, laboratory analytical methodologies and data processing have been used and the entire database was subjected to common rigorous validations, which enabled the identification of spurious data and its remediation or exclusion from the evaluation database. Therefore, data quality was not a contributing factor in the classification of the Mineral Resources. However, the localised thickness and grade variability of the J-M Reef is a major source of uncertainty in the estimates. Considering the long-range continuity and the high localised thickness and grade variability of the J-M Reef, diamond core drillhole spacing and proximity to areas that have been or are being mined (where reef characteristics have been confirmed from underground exposures and ore processing) were the main variables influencing the Qualified Persons' assessment of level of geoscientific knowledge and confidence in the J-M Reef mined at Stillwater and East Boulder Mines. Furthermore, the Qualified Person also considered the quality of estimates, which is highest for the estimates obtained by the first search and lowest for the estimates obtained by the third search, and confidence in the structural model. In general, the classification criteria ensured that surface diamond drillhole data is only sufficient for the assessment and classification of Mineral Resources as either Indicated or Inferred (depending on drillhole spacing) and that no Measured Mineral Resources were classified based on surface drillhole data only. Therefore, the availability of definition drillhole data and proximity to areas that have been or are being mined were key factors in the classification of Measured Mineral Resources. There are uncertainties in the thickness and grades due to high localised variability and, as a result, grade and tonnage estimates for all areas were influenced by the domain global means which were key inputs to the simple kriging interpolation method used. The Qualified Persons support the use of domain means as these reduce the uncertainty in the tonnage and grade estimates caused by the high localised variability of the J-M Reef across all Mineral Resource categories (Inferred, Indicated and Measured). There are also uncertainties in the structural interpretation in areas that do not have closely spaced definition drillhole data, which are classified as either Indicated or Inferred depending on data spacing which affects the confidence in the structural model. Small-scale geological structures will become known after definition drilling and an unknown geological loss is applied to tonnage estimates in areas with no definition drillhole data, which are classified as Indicated or Inferred. The Qualified Persons employed the following criteria for the Mineral Resource classification: Measured: The 50ft drill station spacing (i.e.,

107 Using the parameters in Table 20 provided by Sibanye-Stillwater, the Qualified Person initially determined the minimum 2E grades required to pay for the extraction and processing of a ton of high-grade ore at East Boulder Mines of at least 0.34opt. This scenario excludes low-grade (0.05-0.34opt) material which is inevitably mined to access the high-grade material. The cost of mining of this low-grade material is already accounted for in the mining cost for high-grade material. Furthermore, there is sufficient hoisting and milling capacity for the processing of the mined low-grade material without displacing any high- grade material. Historically, this low-grade material has been mined and milled profitably together with the high-grade material and together these materials constitute the run of mine ore (RoM) reported as Mineral Reserves. Using the incremental cost of hoisting and processing the low-grade material, the Qualified Person determined an indicative 2E minimum grade of approximately 0.05opt (Table 20). Since all the material grading at least 0.05opt is processed at East Boulder Mine, the Qualified Person considered a 2E cut-off grade of 0.05opt to be appropriate for Mineral Resource reporting and this matches the cut-off grade for mechanised ramp and fill employed for Mineral Reserve reporting at East Boulder Mine. Applying the same grade cut-off calculation logic to Stillwater Mine, an indicative minimum 2E grade of 0.51opt was obtained for the mining and processing of high-grade ore while a minimum 2E grade of 0.08opt was determined under the incremental cost scenario. The higher cut-off grades reflect the higher operating costs associated with the current production ramp-up than those for East Boulder Mine. Due plant capacity constraints, Stillwater Mine milled material above 0.20opt and the mined low-grade material was not hoisted to surface. Accordingly, the 2E cut-off grade of 0.20opt which was applicable for the mining and processing of high-grade ore was used for Mineral Resource reporting at Stillwater Mine; this was also the cut-off grade used for Mineral Reserve reporting. However, the planned commissioning of additional mill capacity at Stillwater Mine in 2024 will remove the historical capacity constraints allowing for the hoisting and milling of low-grade material inevitably mined through to access high-grade ore. Accordingly, the reporting of Mineral Resources at a 2E cut-off grade of 0.11opt at Stillwater Mine is justified. While a higher 2E cut-off grade has been used for reporting the Mineral Resources at Stillwater Mine than for East Boulder Mine, the Qualified Persons consider it more appropriate and therefore recommend the reporting of Mineral Resources at the 2E cut-off grade of 0.05opt at both mines. Aligning the cut-off grade will more fully reflect the Mineral Resource potential of the J-M Reef than the 0.11opt used at Stillwater Mine which is driven by high operating costs during the production ramp up phase. Mineral Resource Estimates 31 December 2023 Mineral Resource Statements The Mineral Resource estimates for Stillwater and East Boulder Mines as at the end of the fiscal year ended 31 December 2023 are summarised in Table 21 and Table 22. The Mineral Resource estimates in Table 21 are reported inclusive of Mineral Reserves while the estimates in Table 22 are reported exclusive of Mineral Reserves. These estimates are in situ estimates of tonnage and grades (point of reference) 108 reported at a minimum mining width of 7.5ft, which is applicable for the dominant ramp and fill underground mining method at Stillwater and East Boulder Mines. Furthermore, the Mineral Resources are reported at 2E cut-off off grades of 0.11opt (3.44g/t) and 0.05opt (1.71g/t) at Stillwater and East Boulder Mines, respectively. Individual metal grades are based on prill splits (metal ratio) data routinely collected at the concentrators, which are summarised in Table 47. No metal equivalents are reported as these are irrelevant to Stillwater and East Boulder Mines. The Qualified Persons with responsibility for reporting and sign-off of the Mineral Resources for Stillwater and East Boulder Mines are Jeff Hughs and Jennifer Evans, respectively. Jennifer and Jeff are Professional Geologists with more than five years of experience relevant to the estimation and reporting of Mineral Resources and mining of the J-M Reef at Stillwater and East Boulder Mines. Table 21: Mineral Resource Estimates Inclusive of Mineral Reserves at the End of the Fiscal Year Ended 31 December 2023 Based on Pd and Pt Price of $1 500/oz Description Mineral Resources Inclusive of Mineral Reserves Imperial Category Mine Tons (Million) Pd (opt) Pt (opt) 2E (opt) 2E Content (Moz) Measured Stillwater 30.7 0.38 0.11 0.49 15.1 East Boulder 18.3 0.28 0.08 0.36 6.6 Subtotal/Average 49.0 0.35 0.10 0.44 21.7 Indicated Stillwater 25.7 0.38 0.11 0.49 12.5 East Boulder 28.4 0.27 0.08 0.35 10.0 Subtotal/Average 54.1 0.32 0.09 0.41 22.4 Measured + Indicated Stillwater 56.4 0.38 0.11 0.49 27.6 East Boulder 46.8 0.28 0.08 0.35 16.6 Subtotal/Average 103.1 0.33 0.09 0.43 44.1 Inferred Stillwater 64.0 0.27 0.08 0.35 22.4 East Boulder 61.5 0.27 0.08 0.35 21.3 Subtotal/Average 125.5 0.27 0.08 0.35 43.7 Metric Category Mine Tonnes (Million) Pd (g/t) Pt (g/t) 2E (g/t) 2E Content (Moz) Measured Stillwater 27.8 13.15 3.75 16.90 15.1 East Boulder 16.6 9.65 2.68 12.33 6.6 Subtotal/Average 44.5 11.84 3.35 15.19 21.7 Indicated Stillwater 23.3 12.96 3.69 16.65 12.5 East Boulder 25.8 9.40 2.61 12.01 10.0 Subtotal/Average 49.1 11.09 3.12 14.21 22.4 Measured + Indicated Stillwater 51.1 13.06 3.72 16.79 27.6 East Boulder 42.4 9.50 2.64 12.13 16.6 Subtotal/Average 93.6 11.45 3.23 14.68 44.1 Inferred Stillwater 58.0 9.35 2.66 12.01 22.4 East Boulder 55.8 9.29 2.58 11.87 21.3 Subtotal/Average 113.8 9.32 2.62 11.94 43.7 2E Cut-off Grade Stillwater Mine – 0.11opt (3.77g/t) 2E Cut-off Grade East Boulder Mine – 0.05opt (1.71g/t) Pd Price – $1 500/oz Pt Price – $1 500/oz 2E Recovery Stillwater Mine – 91.48% 2E Recovery East Boulder Mine – 90.33% Pd:Pt Ratio Stillwater Mine – 3.51:1 Pd:Pt Ratio East Boulder Mine – 3.60:1 109 Table 22: Mineral Resource Estimates Exclusive of Mineral Reserves at the End of the Fiscal Year Ended 31 December 2023 Based on Pd and Pt Price of $1 500/oz Description Mineral Resources Exclusive of Mineral Reserves Imperial Category Mine Tons (Million) Pd (opt) Pt (opt) 2E (opt) 2E Content (Moz) Measured Stillwater 16.1 0.27 0.08 0.34 5.5 East Boulder 7.2 0.25 0.07 0.32 2.3 Subtotal/Average 23.2 0.26 0.07 0.34 7.8 Indicated Stillwater 11.4 0.20 0.06 0.26 3.0 East Boulder 9.8 0.22 0.06 0.28 2.7 Subtotal/Average 21.3 0.21 0.06 0.27 5.7 Measured + Indicated Stillwater 27.5 0.24 0.07 0.31 8.5 East Boulder 17.0 0.23 0.06 0.30 5.0 Subtotal/Average 44.5 0.24 0.07 0.30 13.5 Inferred Stillwater 64.0 0.27 0.08 0.35 22.4 East Boulder 61.5 0.27 0.08 0.35 21.3 Subtotal/Average 125.5 0.27 0.08 0.35 43.7 Metric Category Mine Tonnes (Million) Pd (g/t) Pt (g/t) 2E (g/t) 2E Content (Moz) Measured Stillwater 14.6 9.15 2.61 11.76 5.5 East Boulder 6.5 8.61 2.39 11.00 2.3 Subtotal/Average 21.1 8.99 2.54 11.53 7.8 Indicated Stillwater 10.4 6.98 1.99 8.96 3.0 East Boulder 8.9 7.47 2.07 9.54 2.7 Subtotal/Average 19.3 7.20 2.03 9.23 5.7 Measured + Indicated Stillwater 24.9 8.25 2.35 10.60 8.5 East Boulder 15.4 7.95 2.21 10.16 5.0 Subtotal/Average 40.4 8.13 2.30 10.43 13.5 Inferred Stillwater 58.0 9.35 2.66 12.01 22.4 East Boulder 55.8 9.29 2.58 11.87 21.3 Subtotal/Average 113.8 9.32 2.62 11.94 43.7 2E Cut-off Grade Stillwater Mine – 0.11opt (3.77g/t) 2E Cut-off Grade East Boulder Mine – 0.05opt (1.71g/t) Pd Price – $1 500/oz Pt Price – $1 500/oz 2E Recovery Stillwater Mine – 91.48% 2E Recovery East Boulder Mine – 90.33% Pd:Pt Ratio Stillwater Mine – 3.51:1 Pd:Pt Ratio East Boulder Mine – 3.60:1 Mineral Resource Reconciliation Table 23 and Table 24 show a reconciliation between the 31 December 2023 and the 31 December 2022 Mineral Resource estimates for Stillwater and East Boulder Mines. Both estimates were reported at the same cut-off grades and minimum mining width and disclosed by the Registrant. The reconciliation shows year-on-year changes where positive and negative values respectively indicate increases and decreases from the 31 December 2022 figures disclosed by the Registrant. The reconciliation indicates modest year-on-year change in tonnage, grade and 2E metal content resulting from the combination of mining depletion between the two reporting periods (0.7 million tons at Stillwater Mine and 0.6 million tons at East Boulder Mine), grade block model updates and changes in Mineral Resource classification boundaries as a result of additional definition drilling. 110 Table 23: 31 December 2022 to 31 December 2023 Mineral Resource Reconciliation (Mineral Resources Inclusive of Mineral Reserves) Description Year-on-Year Change in Mineral Resources Inclusive of Mineral Reserves Imperial Category Mine Tons (Million) Pd (opt) Pt (opt) 2E (opt) 2E Content (Moz) Measured Stillwater 2.2 0.04 0.01 0.06 2.7 East Boulder (0.1) 0.02 0.00 0.02 0.4 Subtotal/Average 2.1 0.03 0.01 0.04 3.0 Indicated Stillwater (0.8) 0.05 0.01 0.06 1.2 East Boulder (0.7) 0.02 0.01 0.03 0.5 Subtotal/Average (1.5) 0.03 0.01 0.04 1.7 Measured + Indicated Stillwater 1.4 0.05 0.01 0.06 3.9 East Boulder (0.8) 0.02 0.01 0.02 0.8 Subtotal/Average 0.6 0.03 0.01 0.04 4.8 Inferred Stillwater 0.1 (0.01) (0.00) (0.01) (0.5) East Boulder (0.3) (0.01) (0.00) (0.01) (0.6) Subtotal/Average (0.2) (0.01) (0.00) (0.01) (1.1) Metric Category Mine Tonnes (Million) Pd (g/t) Pt (g/t) 2E (g/t) 2E Content (Moz) Measured Stillwater 2.0 1.50 0.43 1.92 2.7 East Boulder (0.1) 0.57 0.16 0.72 0.4 Subtotal/Average 1.9 1.20 0.34 1.54 3.0 Indicated Stillwater (0.7) 1.63 0.47 2.10 1.2 East Boulder (0.6) 0.67 0.19 0.86 0.5 Subtotal/Average (1.3) 1.12 0.32 1.44 1.7 Measured + Indicated Stillwater 1.3 1.57 0.45 2.01 3.9 East Boulder (0.7) 0.63 0.18 0.81 0.8 Subtotal/Average 0.6 1.17 0.33 1.50 4.8 Inferred Stillwater 0.1 (0.22) (0.06) (0.28) (0.5) East Boulder (0.3) (0.22) (0.06) (0.28) (0.6) Subtotal/Average (0.2) (0.22) (0.06) (0.28) (1.1) 2E Cut-off Grade Stillwater Mine – 0.11opt (3.77g/t) 2E Cut-off Grade East Boulder Mine – 0.05opt (1.71g/t) Pd Price – $1 500/oz Pt Price – $1 500/oz 2E Recovery Stillwater Mine – 91.48% 2E Recovery East Boulder Mine – 90.33% Pd:Pt Ratio Stillwater Mine – 3.51:1 Pd:Pt Ratio East Boulder Mine – 3.60:1 Table 24: 31 December 2022 to 31 December 2023 Mineral Resource Reconciliation (Mineral Resources Exclusive of Mineral Reserves) Description Year-on-Year Change in Mineral Resources Exclusive of Mineral Reserves Imperial Category Mine Tons (Million) Pd (opt) Pt (opt) 2E (opt) 2E Content (Moz) Measured Stillwater 1.5 0.03 0.01 0.03 1.0 East Boulder 0.5 0.02 0.01 0.03 0.4 Subtotal/Average 2.0 0.03 0.01 0.03 1.4 Indicated Stillwater (0.5) 0.03 0.01 0.04 0.3 East Boulder 0.7 0.03 0.01 0.04 0.6 Subtotal/Average 0.2 0.03 0.01 0.04 0.9 Measured + Indicated Stillwater 1.0 0.03 0.01 0.04 1.3 East Boulder 1.2 0.03 0.01 0.04 0.9 Subtotal/Average 2.2 0.03 0.01 0.04 2.3 Inferred Stillwater 0.1 (0.01) (0.00) (0.01) (0.5) East Boulder (0.3) (0.01) (0.00) (0.01) (0.6) Subtotal/Average (0.2) (0.01) (0.00) (0.01) (1.1)

111 Description Year-on-Year Change in Mineral Resources Exclusive of Mineral Reserves Imperial Category Mine Tons (Million) Pd (opt) Pt (opt) 2E (opt) 2E Content (Moz) Metric Category Mine Tonnes (Million) Pd (g/t) Pt (g/t) 2E (g/t) 2E Content (Moz) Measured Stillwater 1.4 0.91 0.26 1.17 1.0 East Boulder 0.4 0.82 0.23 1.05 0.4 Subtotal/Average 1.8 0.88 0.25 1.13 1.4 Indicated Stillwater (0.5) 1.00 0.28 1.28 0.3 East Boulder 0.7 1.12 0.31 1.43 0.6 Subtotal/Average 0.2 1.07 0.30 1.36 0.9 Measured + Indicated Stillwater 0.9 1.02 0.29 1.32 1.3 East Boulder 1.1 0.99 0.28 1.27 0.9 Subtotal/Average 2.0 1.01 0.28 1.29 2.3 Inferred Stillwater 0.1 (0.22) (0.06) (0.28) (0.5) East Boulder (0.3) (0.22) (0.06) (0.28) (0.6) Subtotal/Average (0.2) (0.22) (0.06) (0.28) (1.1) 2E Cut-off Grade Stillwater Mine – 0.11opt (3.77g/t) 2E Cut-off Grade East Boulder Mine – 0.05opt (1.71g/t) Pd Price – $1 500/oz Pt Price – $1 500/oz 2E Recovery Stillwater Mine – 91.48% 2E Recovery East Boulder Mine – 90.33% Pd:Pt Ratio Stillwater Mine – 3.51:1 Pd:Pt Ratio East Boulder Mine – 3.60:1 112 MINERAL RESERVE ESTIMATES Mineral Resource to Mine Reserve Conversion Methodology Mineral Resources Available for Conversion Prior to commencing the planning process at Stillwater and East Boulder Mines, the first stage was to define the Mineral Resources available for conversion to Mineral Reserves – these being Indicated and Measured Mineral Resources. The Mineral Resource model identified the tonnages, grades and 2E content available for conversion. Mineral Reserve Estimation Methodology Mineral Reserves for Stillwater and East Boulder Mines were prepared from a business and LoM planning process which converted Indicated and Measured Mineral Resources to Mineral Reserves. The Mineral Reserves were classified using criteria set out in Section 12.2. The conversion took into consideration all the modifying factors for the various disciplines relevant to Mineral Reserves, namely mining methods, mining and surveying factors, ore processing and metallurgical recoveries, infrastructure engineering and equipment, market conditions, environmental and social matters, and capital and operating costs (Section 12 to 18). The LoM plan production schedules generated were tested for economic viability using a set of reasonable economic parameters prior to the declaration of Mineral Reserves (Section 19). Despite the common estimation methodology employed for Indicated and Measured Mineral Resources, different approaches were followed for the scheduling of Indicated and Measured Mineral Resources to derive the LoM production schedules underpinning the Mineral Reserves for Stillwater and East Boulder Mines (Section 13.7). This is due to different levels of confidence between the Mineral Resource classes resulting from different drillhole data point spacing given the high microvariability of the J-M Reef. Scheduling of the Measured Mineral Resources and conversion to Proved Mineral Reserves benefitted from the high abundance of geological information available to accurately constrain thickness, tonnage and grades. However, the scheduling of the Indicated Mineral Resources and conversion to Probable Mineral Reserves relied on statistics and key metrics extrapolated from the Proved Mineral Reserve areas per domain and mining block. The Mineral Reserves were estimated for each of the sub-areas at both Stillwater Mine and East Boulder Mines. The conversion of Mineral Resources to Mineral Reserves at the mines follows a methodology that was developed in 1990 and adjusted as required over the years as more geological and mining information became available. The methodology accounts for the different reef facies and the sub- areas that exist at the mines and the fact that a single set of parameters within a sub-area can be used to confidently project surface and underground drilling for Mineral Resource estimates. Mining experience and reconciliation between Mineral Reserve estimates and actual production figures have demonstrated the robustness of the methodology in making estimates of tonnages and ounces that have historically been reported as Mineral Reserves. 113 The following key technical parameters, assumptions and mining modifying factors were utilised to develop the mine designs and LoM production schedules as discussed in Sections 12 and 13: Cut-off grade; Percentage ore recovered; Geotechnical and geohydrological considerations; Mining method and applicable minimum mining widths; Dilution (planned and unplanned overbreak); Deletion; Extraction rate; Extraction sequence; Planned productivity; Equipment and personnel equipment requirements; and Fill requirements (type and quantity). The LoM planning and subsequent production scheduling was developed utilising historical productivity parameters inclusive of the following: Stoping tons per miner per month per mining method; Ore tons generated per foot of footwall development; Primary development productivities, feet advance per month; and Secondary development productivities, feet advance per month; Historical analysis of mine planning and production data revealed that a recovery factor of 75% was required to reconcile blasted and removed tons in the sub-level extraction stopes. Therefore, a 75% recovery factor was applied to all sub-level extraction tons and ounces to Mineral Reserves. Furthermore, mineability block factors (MBFs) indicated in Table 36 were applied to tonnage estimates when converting Indicated Mineral Resources to Probable Mineral Reserves. A MBF is calculated as the percentage of the fully diluted ore grade tonnage within a mineable area compared with the total fully diluted ore grade tonnage within the boundary area of a block or percent of material historically extracted from the block. Initially, scheduling included all primary development (footwall lateral drifts) to access the stope blocks in the Measured Mineral Resource areas. Thereafter, the development design and scheduling were extended into the Indicated Mineral Resource areas where primary annual development rates were derived through the utilisation of historical ratios. The scheduling of the stoping was dependent on the completion of the footwall access and the necessary diamond drilling to form an outline of the stopable areas in terms of grade and tonnage. In addition, the scheduling was also dependent on the mill feed requirements. On the completion of the lateral development schedule, the starting dates for the development of the stoping blocks were defined based on when access will be attained and the mines’ requirements in terms of RoM ore production. It is also during this process that the true width was corrected for dip and a minimum mining width was applied dependant on mining method and type of equipment to be employed. 114 For each stope block, a proposal (business plan) was drawn up which included, amongst other information, primary and secondary development requirements, reef widths, tonnage and forecasted grade, expected percentage ore recovery, applied cut-off grades, overall stope design, mining method to be employed, ventilation requirements, backfill requirements extraction sequence, and manpower and mining equipment requirements. Once the technical inputs were defined, each stope block was subjected to an economic test. This economic test used technical and financial parameters to determine the economic viability of the planned stoping operations. It accounted for all costs associated with the ore extraction and balanced the total costs against the revenue generated by the block. From the process, a Net Present Value (NPV) of the planned stope was determined. Where required (e.g., if a stope does not meet the required financial returns), the stope was optimised to return the best value. The tonnage and grades in the LoM production schedules were aggregated to derive Mineral Reserve tons and grades, with the tonnage and grades scheduled in the Measured Mineral Resources supported by definition drillhole data classified as Proved and those in the Indicated and Measured Mineral Resources supported by surface drillhole data but no definition drillhole data classified as Probable. The Qualified Person can confirm that the process followed to convert the Measured Mineral Resources into Proved Mineral Reserves was based on historical performance and reconciliations, with input and outputs reported within the accuracy level of ±15%. The process followed to convert the Indicated and Measured Mineral Resources to Probable Mineral Reserves utilised statistics from the Proved Mineral Reserves and a geological block model at a lower level of confidence resulting in the outputs reported within ±25% accuracy. Point of Reference The aggregated scheduled tonnages and grades reflected in the LoM production schedules and delivered to the concentrators for processing at Stillwater and East Boulder Mines are the tonnage and grade estimates reported as the Mineral Reserve estimates. Therefore, the mill head is the point of reference for Mineral Reserve reporting. Cut-off Grades The 2E cut-off grades for Mineral Reserve reporting are 0.20opt (6.86g/t) for Stillwater Mine and 0.05opt (1.71g/t) for the East Boulder Mine. All diluted blocks within the individual stope outlines that are above the cut-off grade were included in the Mineral Reserves. The 2E cut-off grades were selected as the optimal cut-off grades that ensure continuity of the mineable portions of the reef and enable achievement of targeted production efficiencies while optimising NPV. Using the parameters in Table 20, the Qualified Person determined the minimum 2E grades required to pay for the extraction and processing of a ton of high-grade ore at Stillwater and East Boulder Mines of 0.51opt and 0.34opt, respectively. This approach leaves the mined low-grade material underground, which would be inappropriate if there is unused hoisting and ore processing plant capacities. As a result, the Qualified Person also determined the 2E cut-off grades based on the incremental cost of hoisting
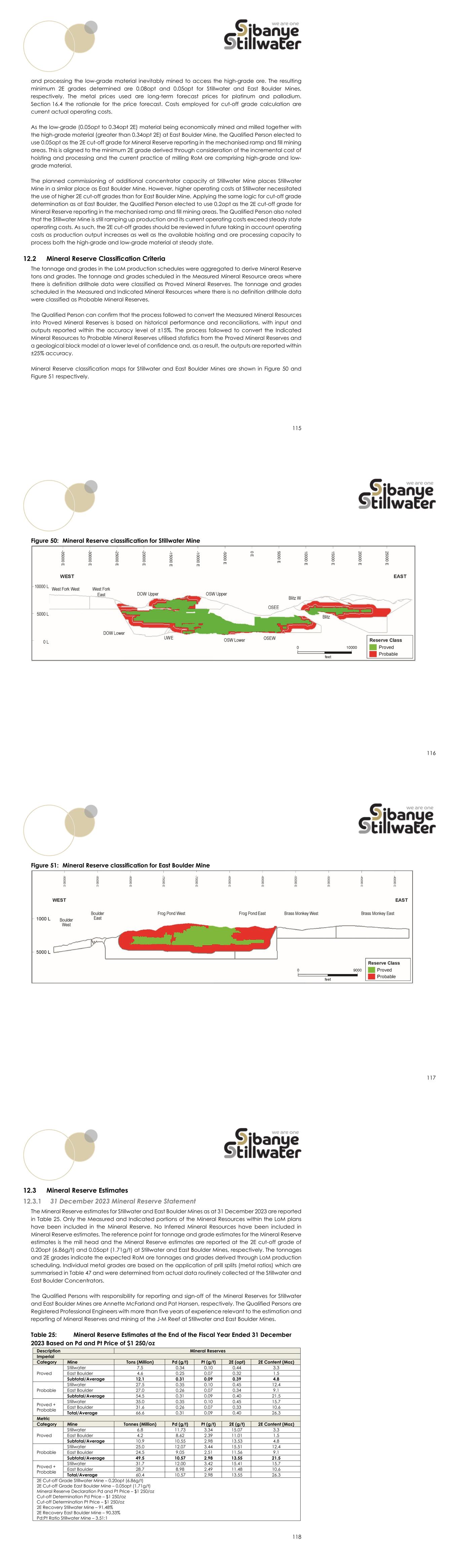
115 and processing the low-grade material inevitably mined to access the high-grade ore. The resulting minimum 2E grades determined are 0.08opt and 0.05opt for Stillwater and East Boulder Mines, respectively. The metal prices used are long-term forecast prices for platinum and palladium. Section 16.4 the rationale for the price forecast. Costs employed for cut-off grade calculation are current actual operating costs. As the low-grade (0.05opt to 0.34opt 2E) material being economically mined and milled together with the high-grade material (greater than 0.34opt 2E) at East Boulder Mine, the Qualified Person elected to use 0.05opt as the 2E cut-off grade for Mineral Reserve reporting in the mechanised ramp and fill mining areas. This is aligned to the minimum 2E grade derived through consideration of the incremental cost of hoisting and processing and the current practice of milling RoM ore comprising high-grade and low- grade material. The planned commissioning of additional concentrator capacity at Stillwater Mine places Stillwater Mine in a similar place as East Boulder Mine. However, higher operating costs at Stillwater necessitated the use of higher 2E cut-off grades than for East Boulder Mine. Applying the same logic for cut-off grade determination as at East Boulder, the Qualified Person elected to use 0.2opt as the 2E cut-off grade for Mineral Reserve reporting in the mechanised ramp and fill mining areas. The Qualified Person also noted that the Stillwater Mine is still ramping up production and its current operating costs exceed steady state operating costs. As such, the 2E cut-off grades should be reviewed in future taking in account operating costs as production output increases as well as the available hoisting and ore processing capacity to process both the high-grade and low-grade material at steady state. Mineral Reserve Classification Criteria The tonnage and grades in the LoM production schedules were aggregated to derive Mineral Reserve tons and grades. The tonnage and grades scheduled in the Measured Mineral Resource areas where there is definition drillhole data were classified as Proved Mineral Reserves. The tonnage and grades scheduled in the Measured and Indicated Mineral Resources where there is no definition drillhole data were classified as Probable Mineral Reserves. The Qualified Person can confirm that the process followed to convert the Measured Mineral Resources into Proved Mineral Reserves is based on historical performance and reconciliations, with input and outputs reported within the accuracy level of ±15%. The process followed to convert the Indicated Mineral Resources to Probable Mineral Reserves utilised statistics from the Proved Mineral Reserves and a geological block model at a lower level of confidence and, as a result, the outputs are reported within ±25% accuracy. Mineral Reserve classification maps for Stillwater and East Boulder Mines are shown in Figure 50 and Figure 51 respectively. 116 Figure 50: Mineral Reserve classification for Stillwater Mine 117 Figure 51: Mineral Reserve classification for East Boulder Mine 118 Mineral Reserve Estimates 31 December 2023 Mineral Reserve Statement The Mineral Reserve estimates for Stillwater and East Boulder Mines as at 31 December 2023 are reported in Table 25. Only the Measured and Indicated portions of the Mineral Resources within the LoM plans have been included in the Mineral Reserve. No Inferred Mineral Resources have been included in Mineral Reserve estimates. The reference point for tonnage and grade estimates for the Mineral Reserve estimates is the mill head and the Mineral Reserve estimates are reported at the 2E cut-off grade of 0.20opt (6.86g/t) and 0.05opt (1.71g/t) at Stillwater and East Boulder Mines, respectively. The tonnages and 2E grades indicate the expected RoM ore tonnages and grades derived through LoM production scheduling. Individual metal grades are based on the application of prill splits (metal ratios) which are summarised in Table 47 and were determined from actual data routinely collected at the Stillwater and East Boulder Concentrators. The Qualified Persons with responsibility for reporting and sign-off of the Mineral Reserves for Stillwater and East Boulder Mines are Annette McFarland and Pat Hansen, respectively. The Qualified Persons are Registered Professional Engineers with more than five years of experience relevant to the estimation and reporting of Mineral Reserves and mining of the J-M Reef at Stillwater and East Boulder Mines. Table 25: Mineral Reserve Estimates at the End of the Fiscal Year Ended 31 December 2023 Based on Pd and Pt Price of $1 250/oz Description Mineral Reserves Imperial Category Mine Tons (Million) Pd (g/t) Pt (g/t) 2E (opt) 2E Content (Moz) Proved Stillwater 7.5 0.34 0.10 0.44 3.3 East Boulder 4.6 0.25 0.07 0.32 1.5 Subtotal/Average 12.1 0.31 0.09 0.39 4.8 Probable Stillwater 27.5 0.35 0.10 0.45 12.4 East Boulder 27.0 0.26 0.07 0.34 9.1 Subtotal/Average 54.5 0.31 0.09 0.40 21.5 Proved + Probable Stillwater 35.0 0.35 0.10 0.45 15.7 East Boulder 31.6 0.26 0.07 0.33 10.6 Total/Average 66.6 0.31 0.09 0.40 26.3 Metric Category Mine Tonnes (Million) Pd (g/t) Pt (g/t) 2E (g/t) 2E Content (Moz) Proved Stillwater 6.8 11.73 3.34 15.07 3.3 East Boulder 4.2 8.62 2.39 11.01 1.5 Subtotal/Average 10.9 10.55 2.98 13.53 4.8 Probable Stillwater 25.0 12.07 3.44 15.51 12.4 East Boulder 24.5 9.05 2.51 11.56 9.1 Subtotal/Average 49.5 10.57 2.98 13.55 21.5 Proved + Probable Stillwater 31.7 12.00 3.42 15.41 15.7 East Boulder 28.7 8.98 2.49 11.48 10.6 Total/Average 60.4 10.57 2.98 13.55 26.3 2E Cut-off Grade Stillwater Mine – 0.20opt (6.86g/t) 2E Cut-off Grade East Boulder Mine – 0.05opt (1.71g/t) Mineral Reserve Declaration Pd and Pt Price – $1 250/oz Cut-off Determination Pd Price – $1 250/oz Cut-off Determination Pt Price – $1 250/oz 2E Recovery Stillwater Mine – 91.48% 2E Recovery East Boulder Mine – 90.33% Pd:Pt Ratio Stillwater Mine – 3.51:1

119 Description Mineral Reserves Pd:Pt Ratio East Boulder Mine – 3.60:1 Mineral Reserve Reconciliation Table 26 shows a reconciliation between the 31 December 2023 and the 31 December 2022 Mineral Reserve estimates for Stillwater and East Boulder Mines which were reported at the same cut-off grades and minimum mining width and disclosed by the Registrant. These also show year-on-year changes where positive and negative values respectively indicate increases and decreases from the 31 December 2022 figures. The reconciliation shows modest year-on-year change in the tonnage and grades resulting from mining depletion between the two reporting periods (0.7 million tons at Stillwater Mine and 0.6 million tons at East Boulder Mine), block model update, Mineral Reserve classification boundaries and refinements to the modifying factors used for the conversion of Mineral Resources to Mineral Reserves during mine planning. Table 26: 31 December 2022 to 31 December 2023 Mineral Resource Reconciliation Description Year-on-Year Change in Mineral Reserves Imperial Category Mine Tons (Million) Pd (g/t) Pt (g/t) 2E (opt) 2E Content (Moz) Proved Stillwater 0.8 0.01 0.00 0.01 0.5 East Boulder 0.2 (0.02) (0.01) (0.02) (0.0) Subtotal/Average 1.1 0.00 0.00 0.00 0.4 Probable Stillwater (1.2) 0.01 0.00 0.02 0.0 East Boulder 0.3 (0.02) (0.00) (0.02) (0.4) Subtotal/Average (0.9) (0.00) (0.00) (0.00) (0.4) Proved + Probable Stillwater (0.4) 0.01 0.00 0.02 0.5 East Boulder 0.5 (0.02) (0.00) (0.02) (0.5) Total/Average 0.2 (0.00) (0.00) (0.00) 0.0 Metric Category Mine Tonnes (Million) Pd (g/t) Pt (g/t) 2E (g/t) 2E Content (Moz) Proved Stillwater 0.7 0.37 0.11 0.48 0.5 East Boulder 0.2 (0.67) (0.19) (0.85) (0.0) Subtotal/Average 1.0 0.01 0.01 0.01 0.4 Probable Stillwater (1.1) 0.51 0.15 0.66 0.0 East Boulder 0.3 (0.53) (0.15) (0.68) (0.4) Subtotal/Average (0.8) (0.03) (0.01) (0.04) (0.4) Proved + Probable Stillwater (0.3) 0.48 0.14 0.61 0.5 East Boulder 0.5 (0.55) (0.15) (0.71) (0.5) Total/Average 0.1 (0.03) (0.01) (0.03) 0.0 2E Cut-off Grade Stillwater Mine – 0.20opt (6.86g/t) 2E Cut-off Grade East Boulder Mine – 0.05opt (1.71g/t) Mineral Reserve Declaration Pd and Pt Price – $1 250/oz Cut-off Determination Pd Price – $1 250/oz Cut-off Determination Pt Price – $1 250/oz 2E Recovery Stillwater Mine – 91.48% 2E Recovery East Boulder Mine – 90.33% Pd:Pt Ratio Stillwater Mine – 3.51:1 Pd:Pt Ratio East Boulder Mine – 3.60:1 120 Risk Assessments The Qualified Persons have completed a high-level semi-quantitative risk analysis of the Sibanye- Stillwater US PGM Operations discussed in this TRS. The risk analysis sought to establish how the Mineral Reserve estimates for Stillwater and East Boulder Mines could be materially affected by risk factors associated with or changes to any aspect of the modifying factors. For the high-level risk analysis, the Qualified Persons have assessed a material risk identified as an issue for which there is a substantial likelihood that a reasonable investor would attach importance in determining whether to buy or sell the securities registered for Sibanye-Stillwater. A material risk should also have a high chance (likelihood) of occurrence. If an issue does not satisfy both criteria, it has been identified as a low to medium risk depending on its impact if it occurs and the likelihood of occurrence. Sibanye-Stillwater has a risk management process in place at the Sibanye-Stillwater US PGM Operations that identifies risks, assesses the materiality of the risks, and provides risk mitigation measures where possible. The Qualified Persons participate in the risk assessment for the LoM plans and Mineral Reserves. Sibanye-Stillwater’s risk management process identified various material risks to LoM plans and Mineral Reserves relating to geotechnical and geohydrological uncertainties, inability to execute LoM plans, metal price downturns, inadequate tailings storage capacity, unplanned production cost escalation, unplanned power outages and restricted access to the operations caused by extreme weather events. Sibanye-Stillwater has mitigated (and not eliminated) these risks as per its risk management protocols to reduce the likelihood of occurrence and/or impact (severity) when the risk occurs which resulted in a reclassification of the residual risks as low to medium risks. The Qualified Persons consider the risk management process robust and sufficient to identify material risks that should be mitigated to enhance the achievability of the LoM plans. From their appraisal of the residual risks after mitigation, the Qualified Persons could not identify any unmitigated material risks to the LoM plans and Mineral Reserves associated with the modifying factors or resulting from changes to any aspect of the modifying factors. The Qualified Persons provide the following opinions relating to the low to medium risks identified in the modifying factors and the mitigation measures in place to minimise the impact of the risks: Geotechnical: Stillwater and East Boulder Mines have accumulated an extensive geotechnical database and developed ground classification (ground control districts) and support measures that are suited to the rockmass conditions for each of the ground control districts. These measures have significantly reduced major falls of ground at Stillwater and East Boulder Mines. However, there is always a degree of residual low risk relating to excavation failures. The extensive support systems and standards in place at both mines are sufficient to minimise the potential impact of any geotechnical associated risk. Geohydrological: Mining operations at Stillwater and East Boulder Mines have not experienced material interruptions due to groundwater problems, with both mines being relatively dry in the upper sections. However, a significant amount of groundwater was encountered at the Stillwater East Section during the development of the main access adits and the decline, but conditions have improved significantly with further development. Despite the declining groundwater inflow, the groundwater poses a low risk in terms of excavation stability and the management and disposal of the water generated. Stillwater Mine has already initiated a multi-pronged approach to mitigating this risk which involve the following: o The drilling of probe holes well in advance of any advancing development end; 121 o Carrying out hydraulic tests of probe holes drilled prior to drift advancement whenever practically possible; o Cementation (grouting) ahead of those advancing development ends where the potential for significant water intersections have been identified; o Probe and definition drilling before developing new production areas to evaluate water inflows, with some of these drillholes converted into drain holes for dewatering purposes; and o Evaluating, engineering, and permitting expanded water handling and disposal facilities on surface to manage excess mine water. Inability to execute LoM plans: Although mining experience at the Stillwater and East Boulder Mines has provided improved understanding of the mineralisation, modelling ability and understanding of the modifying factors, estimation errors cannot be eliminated. The major expected sources of error in the Mineral Reserve estimates include understating production costs, slower than planned production build-ups, understating manpower requirements, regulatory changes, grade and tonnage underestimation and unknown geological conditions. These factors are partially mitigated by using a significant amount of historical data in the LoM forecasting of key elements of the operations, namely RoM ore production levels, RoM ore grades and operating costs. Furthermore, the mines have systems and personnel in place that monitor the mining operations daily (short interval control) to enable the implementation of timeous interventions and, therefore, correction of deviations to the plans. Unplanned production cost escalation: In recent years since 2019 until 2023, there has not been significant escalation of the production costs. The production costs were mainly affected by the quantities of ore and waste produced each year from each mine and the mining methods employed, with the cost-effective mechanised ramp and fill methods utilised for most stopes at both mines. Continuous improvement initiatives adopted to contain cost escalation included the increasing use of mechanised mining methods thereby improving productivities and reducing operating costs, the optimisation of the mining fleets (reducing active units) to reduce maintenance costs and increase mining volumes through mining footprint expansion at Stillwater Mine (Stillwater East Section) and optimal utilisation of available hoisting and milling capacities at East Boulder (Fill The Mill Project). Since 2020 and coinciding with the COVID-19 pandemic, the operations have experienced significant cost pressures due to external and internal factors which were compounded by production disruptions caused by the COVID-19 pandemic. The operations have embarked on recovery efforts and production ramp up to reverse the adverse impacts on production due to the COVID-19 pandemic. Power losses: The loss of power at the mining operations during the winter months (due to excessive snow and high winds) is the single low to medium risk identified relating to mining infrastructure. The power losses are infrequent and are mitigated by using backup generators. The generators have sufficient capacity to power communication systems and shaft conveyances to ensure that personnel can be safely withdrawn. Inadequate tailings storage capacity: Tailings storage facilities at Stillwater and East Boulder Mines have adequate storage capacity for the medium term (seven to ten-year range). Production increases at both mines have shortened the lives of the tailings storage capacities. Tailings storage capacity upgrade through elevation lift is a mitigation measure that has been adopted while permitting for the construction of new tailings facilities is being pursued. Permitting for the construction of a new tailings storage facility may require periods of three to five years. Sibanye- Stillwater is aware of the long approval timeframes and has already completed the necessary technical studies and submitted the required permit applications to initiate the permitting processes. It is unlikely that the operations will run out of tailings storage facility capacity before Sibanye-Stillwater receives approvals for the construction of new tailings storage facilities or the upgrading of the existing tailings storage facilities. 122 Metal price downturns: The prices for palladium and platinum fluctuate depending on global supply and demand. Demand for palladium and platinum primarily depend on their use in auto- catalytic converters for both gasoline and diesel engines. The use of platinum and palladium in the hydrogen economy is anticipated to become an additional key demand driver for these metals. Sensitivity analysis of the NPV for the Sibanye-Stillwater US PGM Operations for variation in metal prices indicates robust economics due to the high-grade nature of the J-M Reef and that significant revisions of the Mineral Reserves for Stillwater and East Boulder Mines would only result from a significant metal price decrease. The estimated revenue per combined ounce of palladium and platinum over the LoM plans varies depending on which parts of each of the mines are being exploited. This offers the mines the flexibility to delay the mining of sub-economic areas during times of price downturns. Restricted access to the operations caused by extreme weather events: Freezing temperatures in winter and snow can pose adverse operating conditions, although avalanches from the steep mountain slopes have never directly affected operations at the mines. Snow removal and road maintenance by Sibanye-Stillwater has effectively been used to maintain mine access even in winter storms. On 13 June 2022, a 500-year flood resulting from the combination of warm weather triggering an unusual ice melt and incessant rains in Montana destroyed parts of State Highway 419 used to access Stillwater Mine. The damage caused restricted access to the mine, temporary suspension of the mining operations for seven weeks. A temporary road was built to reestablish access to and from the mine to support full operations at the mine while repairs were being carried out on the damaged parts of the highway resulting in access restoration through the highway in July 2023. The Qualified Persons consider the likelihood of a recurrence of another 500-year flood low which makes flooding due to incessant rains and destruction of access roads a low to medium risk.

123 MINING METHODS Introduction Stillwater and East Boulder Mines are mature operations extracting the J-M Reef using well-established mining methods. Most of the permanent infrastructure required to access the underground operations is already established and being upgraded where necessary to accommodate production increases anticipated in the LoM plans for the operations. The LoM plans for Stillwater and East Boulder Mines, which underlie the Mineral Reserves, were constructed internally by Sibanye-Stillwater’s Qualified Persons supported by Technical Experts and utilising modifying factors and capital and operating costs which are informed by historical experience at the mines. Accordingly, the technical inputs, modifying factors, staffing levels, capital and operating costs utilised for LoM production planning and conversion of Measured Mineral Resources to Proved Mineral Reserves are within ±15% accuracy and the costs allow for up to 10% contingency. However, for the LoM production planning and conversion of Indicated Mineral Resources to Probable Mineral Reserves, the inputs and costs are within ±15% accuracy and the costs allow for up to 10-15% contingency. The economic viability of the LoM plans was assessed through detailed cash flow analysis. Mining recovery (stope extraction) factors are discussed in Section 13.2.4 of this TRS. Mine Design Mining Method Rationale The J-M Reef outcrops over a 28-mile strike length on the Sibanye-Stillwater Mining Claims but the topography, altitude and thickness of the reef preclude economic exploitation of the reef through open pit mining methods. Accordingly, waste stripping which would be applicable to an open pit mining is not required. At Stillwater Mine, the dip of the J-M Reef varies from 40° to 90° to the north, with an average of 60°. Reef thickness varies from 3ft to more than 9ft but averages 6ft. The J-M Reef at East Boulder Mine dips 35° to 55° (averaging 50°) to the north. The shallowest dip (35°) is observed in the far west area accessed by the 6500 Level Footwall Lateral. Both Stillwater and East Boulder Mines employ the following underground mining methods, which are suited for the variable steep dips and narrow widths of the J-M Reef: Mechanised ramp and fill (also referred to as cut and fill) using overhand or underhand approaches; and Sub-level extraction by longitudinal hole open stoping with subsequent backfill. The captive cut and fill stoping method which was also being used at the mines has been phased out. The mining method mix is adjustable and largely driven by geotechnical considerations as well as mineralisation grade and the requirement to minimise dilution. The percentage distribution (frequency of use) of the two mining methods within each of the mines is shown in Table 27. Mechanised ramp and fill stoping (which includes on-reef sub-level sill development) is the predominant mining method at both mine-sites. The mechanised ramp and fill method allows for maximum selectivity for separating ore and waste. Sub-level extraction long hole stoping is utilised typically in narrow continuous ore zones. Except for open stoping, the mining methods employ high-quality sand or paste as backfill, with limited use of Cemented Rock Fill (CRF) and/or other backfill materials. 124 Table 27: Mining method frequency of use at Stillwater and East Boulder Mines Mining Method Frequency of Use Stillwater Mine East Boulder Mine Mechanised Ramp and Fill 86% 83% Sub-level Extraction Long Hole Open Stoping 14% 17% Mechanised Ramp and Fill Method Mechanised overhand ramp and fill stoping is the predominant mining method at the Stillwater and East Boulder Mines while 11% to 20% of the stopes at the Stillwater Mine are extracted through mechanised underhand ramp and fill stoping. The two ramp and fill applications practiced at the mines are illustrated in Figure 52. The backfill for the mechanised overhand and underhand ramp and fill stoping are predominately sand (classified coarse fraction mill tailings) and paste, respectively; in the past CRF was utilised for limited applications but has been phased out due to logistical constraints. Where ground conditions permit, the overhand method is preferred as it is more cost effective. Where less stable ground conditions dictate, mechanised underhand ramp and fill is applied, with the more expensive paste backfill also used. Up to 12% cement is used in the paste fill, as needed, to provide a stable overhead cemented paste material. Furthermore, development ramp gradients should not exceed 18%. Breast holes are drilled on most of the mechanised ramp and fill stopes areas using single-boom drill jumbos and, after blasting, the broken rock material is loaded by 2.0 cubic-yard LHDs. Figure 52: Mechanised Overhand and Underhand Ramp and Fill Mining Methods Sub-level Extraction and Sub-level Development Where the J-M Reef and hangingwall are competent and the reef has good continuity, sub-level longitudinal open stoping using relatively shorter “long holes” compared to those in other mining districts is applied. This extraction method is illustrated in Figure 53. The sub-levels are driven on the reef plane at 125 20ft to 50ft intervals. Considerable tonnage generated by driving sub-levels in the reef is accounted for as Sub-level Development tonnage; this is accounted for in the “Mechanised Cut and Fill” percentage. Figure 53: Sub-level Extraction (Longitudinal) Long Hole Open Stoping In the sub-level extraction longitudinal stoping method, sub-level sills are driven with narrow single-boom jumbos. The long holes are drilled by long hole pneumatic and electric hydraulic drill rigs. Once the sub- levels are advanced, a drop raise is drilled from the upper sub-level to the lower sub-level and blasted at the end of the stope over the full width of the reef at that point. Blast holes are then drilled downward on a pattern between the sub-levels and blasted towards the open cavity of a slot raise. Support pillars are left in place on approximately 80ft to 100ft intervals on the reef in the stope to minimise hangingwall failure and ore dilution. The broken ore is mucked from the sub-level below using remote-controlled, diesel-powered LHDs and then trammed to the nearest ore pass. In addition to sub-level panel extractions, backstops are extensively utilised. The process is similar to sub-level extraction except that all activities take place on the bottom as there is no access at the top. Stope Extraction Ratios The regional and local extraction ratios computed from actual data for Stillwater and East Boulder Mines are shown in Table 28. The Qualified Person notes that the regional extraction ratios in Table 28 are low as large areas of the reef were previously left unmined due to the use of high cut-off grades when palladium prices were low. Extraction ratios are set to increase as Mineral Reserve 2E cut-off grades have been lowered to 0.20opt and 0.05opt at Stillwater and East Boulder Mines, respectively, in response to increases in the palladium price and increased production output at both mines since 2017. 126 Table 28: Stope Extraction Ratios Scale Mining Method Extraction Ratio (%) Stillwater Mine East Boulder Mine West Section East Section All Sections Local (Stope) Mechanised Ramp and Fill 90 90 95 Long Hole Open Stopes 60 60 60 Regional (Mine) Overall 40 40 50 Hydrogeological Model Stillwater Mine Based on the hydrogeological models for the Stillwater East and West Sections discussed in Section 7.9.1, no known major changes in groundwater conditions are expected in the Stillwater West Section, with this section expected to remain dry on average. For the purposes of mine-water treatment and discharge, the groundwater inflows generated in both sections of the mine are combined. The underground inflows are currently managed using a series of collection sumps, ditches, pipelines and pumping stations that are primarily located in the Off-Shaft West area of the West-Side Mine. Sibanye- Stillwater has considered forecast of groundwater inflows to ensure that the overall water-management system is appropriately designed to handle the anticipated flow rates and is constructed and operational before the mine inflows substantially increase. Furthermore, Sibanye-Stillwater uses these forecasts to ensure operational compliance with permitted water-discharge limits. Stillwater Mine has completed evaluating, engineering and permitting to handle increased flows which may be in the order of 1 600gal per minute maximum and consider the Itasca estimate of 3 790gal per minute in seven years and continuation at rates between this peak and 3 600gal per minute to be overstated. Furthermore, the Itasca estimate is inconsistent with empirical data from the Stillwater East Section indicating inflows of 900gal per minute to 1 500 gal per minute. Stillwater Mine has introduced the following operational interventions to assist with the management of groundwater intersections in underground excavations: Drilling of probe holes well in advance of any advancing development end; Carrying out hydraulic tests of probe holes drilled prior to drift advancement whenever practically possible; Full cover grouting ahead of development that has the potential to intersect significant quantities of groundwater; Carrying out additional monitoring/testing as warranted if the identified basins exhibit notably different groundwater conditions; Evaluating groundwater inflows from definition drillholes before developing new production areas and, where appropriate, converting these drillholes into drain holes for depressurisation/dewatering purposes; and Manifolding drain holes together, wherever possible, to collect the discharge water into a smaller number of flow points that can then be monitored and directed to pumping facilities and setting up all drain holes to record the line pressures and discharges (cumulative volumes rather than instantaneous rates) from separate/individual areas.

127 The Qualified Person is satisfied that most of the potential sources of groundwater have been identified and accounted for in the mine design while appropriate operational interventions have been proposed for the management of groundwater at Stillwater Mine. The designs prescribe direction for development or the placement of crown and rib pillars to protect the underground excavations from uncontrolled water in rushes. The Qualified Person also notes the importance of continuous monitoring using probe drillholes to facilitate early detection of any potential unidentified water sources. East Boulder Mine Mining at East Boulder Mine is planned in areas situated adjacent to active mining fronts that have not experienced any groundwater issues as the host rock has low permeability. Furthermore, these areas are located at a higher elevation than the lowest level of the mine (the 6500 Level) which currently acts as a drawdown point for surrounding groundwater levels. Inflows are likely to be similar or lower than those experienced by historical mining operations, with the average mine-wide water inflow only likely to increase slightly with the increase in development and production activity associated with the higher than historical production in the current LoM plan. One fault system encountered at the 71300 area that bears water and has been slowing development efforts has been accounted for in the mine plan. Significant water will also likely be encountered in other significantly faulted and jointed areas or when encountering alluvial systems associated with surface channels as mining gets within 500ft of surface. The Qualified Person is satisfied that the mine designs for East Boulder Mine prescribe direction for development or the placement of crown and rib pillars to protect the underground excavations from uncontrolled water in rushes. Furthermore, the standard practice at East Boulder Mine of drilling water probe holes prior to any development work to mitigate the risk of encountering water has been adequate in detecting groundwater inflows while diamond drilling on 50ft centres results in a good understanding of water potential before mining activity begins. Geotechnical Model Geotechnical Characterisation The J-M Reef and its immediate hangingwall and footwall consist of varying assemblages of norite, anorthosite, leucotroctolite and peridotite. As the lithological sequence is similar at Stillwater and East Boulder Mines, a universal approach is adopted for support designs at both mines. The rock units contained within the J-M Reef, Footwall and Hangingwall Zones are classified as strong based on UCS ranging from 60Mpa to 85Mpa. Mining and support designs are adjusted accordingly is areas of lower strengths commonly associated with olivine cumulates or when geological structures are identified in the drillcores. The Q-values obtained for Stillwater and East Boulder Mines ranging from 1 to 13 indicate poor to good rock mass conditions, where the overall area split for fair, good and poor conditions is 50%, 25% and 25%, respectively. Support Design The ground support requirements for the primary development are described in the standard operating procedures, which detail the requirements for the three main ground types termed Type 1, 2, and 3. 128 Type 3 ground types has two variants (Type 3 and 3+). Table 29 provides the classification criteria for the ground types while Figure 21 and Figure 22 (Section 7.10.3) show the ground classification maps for Stillwater and East Boulder Mines, respectively. Table 29: Stillwater and East Boulder Mine Ground Types Ground Type Q-Rating RMR Rating Description Minimum Maximum Minimum Maximum Type 3+ 0.1 0.39 23 36 Very poor or poor with water present Type 3 0.4 0.99 36 44 Poor Type 2 1 3.99 44 56 Fair Type 1 4 100 56 85 Good Ground conditions that are assessed by the operations using geotechnical drilling data to be poorer than Type 3 ground will be re-assessed by the Geotechnical Engineer as the many variables causing poor ground mean that it is unlikely that a standard approach can be applied. The Geotechnical Engineer will recommend appropriate support for such areas. Rock mass characteristics determined for the assessment of geotechnical data is used to delineate geotechnical domains of similar characteristics. The ground type domains and applicable ground support requirements are integrated with other design and planning information. Areas which are prone to anomalous rock-related risks are then identified for every planned stope within a “Stope Proposal” document. Ground support employed on the reef is typically pattern-bolting with mesh, which is a combination of friction stabilisers and resin anchor rebar bolts. Due to the requirements to maintain the minimum mining width, it is not possible to drill and install rockbolts in the typical stope envelope with the commercially available mechanised bolters. For this reason, bolts are installed with either jacklegs or CMAC support drill rigs. Support rib pillars are left in place as the stope retreats along strike to keep the hangingwall stable in areas mined through the sub-level extraction long hole stoping method. In general, low-grade areas of the reef excluded from mining provide additional regional pillar support. Mine personnel are appropriately trained to perform routine basic checks on ground support or changes in ground conditions as part of their daily inspection of the work areas. Internal and external Geotechnical Engineers are then requested to assess geotechnically complex areas. When necessary, Stillwater and East Boulder Mines engage the services of external consultants to provide geotechnical oversight functions related to ground support performance, stope performance and design. Both mines currently use a Trigger Action Response Plan (TARP) in regard to ground conditions and ground support. With progression from a TARP 1 to TARP 3, the plan is escalated to higher levels within the organisation for review. Support designs for the Benbow Decline which was completed in FY2021 in the Stillwater East Section incorporated primary development support designs employed at the Stillwater West Section and East Boulder Mine. The opening up of new areas in the Stillwater East Section has afforded the opportunity to assess actual ground conditions in this part of Stillwater Mine. A higher frequency of Type 3 ground 129 conditions and variants has been observed than expected, with the available geotechnical data indicating area split for Type 1&2 (fair and good), Type 3 (poor) and Type 3+ (very poor conditions) conditions of 50%, 25% and 25%, respectively. The Type 3 and 3+ ground types encountered have necessitated the use of cemented rock fill or the overhand ramp and fill method with extensive support, which have affected the development advance, mining cycles and the economics of mining in these areas. A fall of ground incident related to poor ground conditions was reported in a stope (5600E 18400). As a result, the establishment of a paste plant (SWE Paste Plant) in the Stillwater East Section in FY2027 has been prioritised in the LoM plan. It is anticipated that the use of paste-fill in areas of poor ground conditions will improve mining and cost efficiencies. The LoM plan has been updated to minimise mining Type 3 and 3+ ground types and prioritise Type 1 and 2 ground types (in the 5600E and 6000E Levels) until the SWE Paste Plant has been constructed. A dedicated support team has been established for the limited Type 3 and 3+ ground types that will be mined in the interim. Poor ground conditions have also been encountered in the Lower Off Shaft West and Lower Off Shaft East areas of the Stillwater West Section. In the former, the poor conditions are due to stress resulting from approximately 5 000ft of overburden (mountain apex). The stopes in this region are primarily mined using the underhand ramp and fill method with paste to mitigate the stress issues. Less stress is expected as the mining front progresses westwards in areas where the burden will reduce. As for the Lower Off Shaft East area, poor ground conditions occur in bounded by the Stillwater Valley Fault to the west and A-Fault to the east. The use of paste fill for support and the underhand ramp and fill method has historically allowed for mining in this area. East Boulder Mine has not experienced any significant ground events or changes in ground support methodology in recent years. In general, the mechanised ramp and fill mining method has widely been used, with sub-level long hole extraction performed after geotechnical analysis on potential stresses. Furthermore, sub-level long hole extraction is not used in the far west areas of East Boulder Mine where Type 3 ground conditions due to high stresses have been interpreted from field evaluations (Figure 22). The Qualified Person is of the view that the current rock reinforcement as prescribed in the ground control standards are adequate for mining throughout the LoM but will be reviewed and updated when necessary. The Qualified Persons are of the opinion that support designs for primary development and stopes utilised at Stillwater and East Boulder Mines for decades are appropriate for the ambient rock mass conditions encountered and mining methods used at both mines. A wealth of geotechnical data (Section 7.10) exists for the mines upon which appropriate stope sizes and support practices have been designed through detailed engineering. These support designs and operational practices have also been accounted for in the overall mine designs for the Stillwater East section of Stillwater Mine. However, a higher-than-expected frequency of poor ground conditions encountered in the Stillwater East Section necessitate expedited establishment of a paste plant in this area to improve mining cycles and efficiencies as well as the economics of mining in this area. 130 Surface and Subsidence Control Regulatory permits have been issued to Stillwater and East Boulder Mines by the Department of State Lands, State of Montana regarding the minimum size of crown pillar to be left from surface and the shallowest depth of stoping activities. These permits specify a 20ft to 50ft crown pillar of competent bedrock for mining below surface terrain that does not contain water courses otherwise a 200ft crown pillar of competent bedrock should be used. The Qualified Persons have confirmed that appropriately sized crown pillars have been incorporated in the mine designs for Stillwater and East Boulder Mines. Backfill 13.4.4.1 Overview Hydraulic sandfill comprising a coarse fraction of the tailings is the backfill used in most stopes mined through the mechanised ramp and fill method. However, cemented tailings paste is only used in stopes mined through the mechanised underhand ramp and fill method to provide sufficient backfill strength for support when this approach is employed. The use of tailings as backfill is also important for tailings volume reduction, with approximately 44% to 50% of the tailings material generated at Stillwater Mine and 46% to 48% of tailings generated at East Boulder Mine used as backfill. No additional steps are necessary to treat any tailings placed back into the mine. 13.4.4.2 Stillwater Mine For the Stillwater West Section, tailings from the Stillwater Concentrator scavenger circuit are pumped to the sandfill plants, where up to 60% is used in the mine backfill process (via the use of cyclones for segregation of -45µm material). A paste fill plant is situated on surface close to the portal from where paste is pumped into the mine via the 5150W from where it is then distributed to the workings requiring fill. The section also has three sandfill plants, with two (i.e., the 4900 Level and 5000 Level Sandfill Plants) situated close to the portal area and the third situated on the 5500W Level providing sandfill for the Upper West mining area. The supply of tailings to the 5500W Level Upper Sandfill Plant is passed through a booster pump in the 5500 Level Portal and cyclones to remove the fine fraction (-45µm) after which the coarse fraction is placed in storage silos. Sandfill is dispatched to the stopes requiring fill mainly by gravity to the Off Shaft mining areas and by high pressure positive displacement pumps for the workings above the 5000 Level; it should be noted that many levels can be serviced from more than one plant- either gravity fill from the 5500 Plant or high-pressure pump from the 5000 Plant. The fines fraction of the tailings is returned to surface via centrifugal pumps for storage at the TSF. To support the mechanised overhand ramp and fill mining in the Stillwater East Section, hydraulic sand backfill is delivered from the 5600E Sand Plant. A 4-inch sand delivery pipe installed from the 5000W pump to the Stillwater East Section serves as the main feed to the 5400E-10400 Sandfill Plant. The Qualified Person notes that Sibanye-Stillwater is currently engaged in an engineering study to deliver thickened tails to the Stillwater East Section for the production of paste for use in mechanised underhand ramp and fill stoping blocks that have poor ground conditions. It is anticipated that a dedicated paste plant for this section will be commissioned in FY2027.

131 13.4.4.3 East Boulder Mine Stopes at East Boulder Mine are backfilled with whole mill tailings delivered from the East Boulder Concentrator on surface to an underground sand plant located on the 6500 Level from where the sandfill is distributed by booster pumps to two other sandfill plants on the 7200 Level and 8200 Level. Similar to Stillwater Mine, the tailings material is pumped through cyclones to remove the fine fraction and the coarse fraction is placed in six underground storage silos while the fine fraction is returned to surface via centrifugal pumps for storage at the tailing storage facility (TSF). Sandfill is dispatched to the stopes requiring fill by positive displacement pumps. All decant and flush water reports into the mine wastewater system, which reports to the main pump station on the 6450 Level. Stillwater Mine Operations Background Established in 1986, Stillwater Mine has produced approximately 60 000 tons of RoM ore per month from a single section – the Stillwater West Section – with the RoM ore processed at the onsite concentrator. A planned step change in production output to approximately 106 000 ton per month necessitated mine expansion into the Blitz area – the Stillwater East Section. Development of the Stillwater East Section (i.e., the Blitz Project) commenced in 2011 with the excavation of access adits and this has been ongoing to date. Development of the capital infrastructure (access drifts, decline and ramps, and ventilation shafts) required in the Stillwater East Section was completed in FY2022. The combined monthly ore production from Stillwater Mine after the inclusion of output from the Stillwater East Section from late FY2017 has gradually been ramping up until a peak of 80 000 tons in FY2020 before the ramp up pace was interrupted by the COVID-19 pandemic restrictions in 2021 to 2022, access restrictions due to the 2022 500-year flood event and a shaft incident (i.e. structural damage to the shaft headgear, winder house and winder rope preventing access to production areas below the 5000 Level for four weeks and disrupting the mine’s ability to haul rock out below 5000W by eight weeks) in the Stillwater West Section in FY2023. The production ramp up is planned to resume in 2024 towards a steady state monthly production level of approximately 100 000 tons (1.2 million tons per annum) by approximately FY2029 and thereafter. Key Operational Infrastructure Stillwater Mine includes the mining operations and ancillary buildings that contain the concentrator, workshop and warehouse, changing facilities, headframe, hoist house, paste plant, water treatment, storage facilities and offices. All surface infrastructure and TSFs are located within the Stillwater Mine Operating Permit, which covers an area measuring 2 450 acres. Stillwater Mine has developed an approximately 9-mile-long segment of the J-M Reef encompassing the Stillwater West and East Sections in the eastern part of the Stillwater Complex. Mine Layout The underground mine layout for Stillwater Mine is illustrated in Figure 54 and this also shows the final mine outline. 132 The Stillwater West Section has been divided into three large mining areas, namely the Off-shaft, Upper West and Lower Far West areas, using geological domain boundaries. These domains have been subdivided into mining blocks as follows (Figure 9): Block 1 and Block 2 in the Upper West area, which is above the 5000 Level in the Dow Sector; Blocks 1 and 2 in the Lower Far West area, which is below the 5000 Level in the Dow Sector; Blocks 3 and 6 in the Off Shaft West area; and Blocks 7 and 8 in the Off Shaft East area. The Stillwater East Section has been divided into two large mining areas, namely Blitz West and Blitz. 13.5.3.1 Stillwater West Section Access to the reef in the Stillwater West Section is by means of an approximately 2 000ft Vertical Shaft and a system of horizontal adits and drifts driven parallel to the strike of the J-M Reef at vertical intervals of between 150ft and 400ft. Ten main adits have been driven from surface portals on the west and east slopes of the Stillwater Valley at various elevations between 5 000ft and 5 900ftamsl. Five principal levels have been developed below the valley floor by ramping down from the 5 000ft level to extract ore from the J-M Reef down to the 3 800ftamsl elevation. Five additional major levels below the 5 000ft level are accessed principally from the vertical shaft and shaft ramp system. The mine has developed a decline system from the 3 200ft elevation to access and develop deeper areas in the central part of the mine below those currently serviced by the existing shaft. The decline system currently accesses the 2900, 2600, 2300, 2000, 1700 and 1600 Levels. It was the objective to keep these footwall developments approximately 100ft to 150ft from the J-M Reef, so that a fan of diamond drillholes could be drilled across the J-M Reef at 50ft intervals. The footwall laterals were originally driven on 200ft vertical intervals, but this spacing was increased to 400ft due to the dip of the hangingwall being similar to the Stillwater East Section which allows for the 400ft vertical section to be drilled from a single FWL. The Vertical Shaft system provides access to the workings below 5000W Level. It serves as a conduit for the transport of men and materials while also hoisting broken rock (ore and waste) to surface. The Stillwater West Section currently uses its 300ft spaced laterals, six primary ramps and vertical excavations to provide personnel and equipment access, supply haulage and drainage, intake and exhaust ventilation systems, muck haulage, backfill plant access, powder storage and/or emergency egress. The footwall lateral and primary ramp systems will continue to provide support to production and ongoing development activities. In addition, certain mine levels are required as an integral component of the ventilation system and serve as required intake and or exhaust levels, or as parallel splits to maintain electrical ventilation horsepower balance and to meet the Mine Safety and Health Administration (MSHA) Regulations. MSHA Regulations also contain requirements for alternate (secondary) escape-ways from mine workings and these levels also meet this need. These levels serve as permanent mine service-ways and are used for road and rail transportation, dewatering and backfill pumping facilities. 133 13.5.3.2 Stillwater East Section The Stillwater East Section is currently under development, with footwall lateral level spacing of 400ft being used. The 5000E TBM drift serves as the main access to this section and this is being driven 600ft south of the JM-Reef. It is a dedicated haulage-ventilation drive and not a normal FWL. Therefore, the drive has also been equipped with rails and serves as the main gathering haulage where ore and waste are transported out of the mine using trains. The development of the 5600E Footwall Drive, which is positioned 600ft above the 5000E Footwall Drive, is currently ongoing. This drive provides access to the stoping blocks. In the eastern part of the Stillwater East Section, the Benbow Decline has also intersected the 5600E Footwall Drive for the provision of additional egress access and as a ventilation intake. The first holing with the 5600E Level from the western portion of the Stillwater East Section was completed in Q3 FY2022. East Boulder Mine Operations Background East Boulder Mine was established in 1997 and started producing ore in 2002 at approximately 55 000 tons per month. In 2016, the steady state monthly RoM ore production level for East Boulder Mine was planned to be approximately 65 000 tons per month after ramping up from the historical levels which were lower than 54 000 tons in line with the Fill the Mill Project which was implemented to utilise the historically unused capacity of the East Boulder Concentrator. During FY2020, several key elements required to increase production levels and take advantage of the unused mill capacity were put in place. The 72 740-production ramp system was developed, and production mining was initiated. An incline was developed to meet the existing Frog Pond Adit which serves as both a ventilation path to surface as well as a secondary egress with a surface shelter. In Q3 FY2020, the Fill the Mill project was completed. Monthly production out rose from approximately 54 000 tons in FY2017 to FY60 000 tons in 2021. The production ramp up momentum reversed in FY2022 to approximately 45 000 tons per month due to the COVID-19 pandemic restrictions and associated operational factors but remained at 47000 tons per month in FY2023. According to the current LoM plan, mining output will ramp up to the revised steady state level of approximately 53 000-63 000 tons per month in FY2024, which is equivalent to approximately 631 000-760 000- tons per annum. Key Operational Infrastructure East Boulder Mine includes the underground mining operations and surface support facilities such as the concentrator, workshop and warehouse, changing facilities, water treatment, storage facilities, office and TSF. All surface infrastructure and the TSF are located within the East Boulder Mine Operating Permit, which covers an area measuring 1 000 acres. East Boulder Mine has developed an approximately 5- mile-long segment of the J-M Reef encompassing the Frog Pond East and West Sections in the western part of the Stillwater Complex. 134 Mine Layout The underground mine layout for East Boulder Mine is illustrated in Figure 54 and this also shows the final mine outline. The predominant mining method is mechanised overhand ramp and fill method complemented by limited sub-level extraction long hole stoping. The J-M Reef at East Boulder Mine is accessed by two access drives, each 3.5 miles long and 15ft in diameter, developed perpendicular to reef strike to intersect the J-M Reef from the north. The access tunnels from surface intersect the reef at an elevation of 6 450ftamsl. Footwall haulages have been developed east and west from this intersection point to open the strike extent of the deposit. The stopes are accessed up-dip by ramps and footwall lateral drifts on 200ft to 400ft vertically spaced levels located approximately 150ft to 200ft from the J-M Reef. Measured Mineral Resources converted to Proved Mineral Reserves are delineated by definition diamond core drilling from these headings, which are also used for stope access and development. The current mine occupies a 5-mile-long footprint which is 2 300ft in vertical extent. The mine plan anticipates the 9400 Level to be the ultimate upper level in the mine. The main adit haulage level is the 6500 Level with the 670 Ramp system having been developed to the 9100 Level. Except for the adit rail haulage, the mine is operated as a trackless mining operation. The 6500 Level footwall haulage extends laterally for a nominal 21 000ft, and the 6700 Level footwall haulage extends laterally for a nominal 18 000ft. The levels are connected by spiral ramps and the reef is accessed by crosscuts. Between 2010 and 2015, the west end of the 6500 Level was extended further west to the Graham Creek area to connect to the Graham Creek vertical raise.
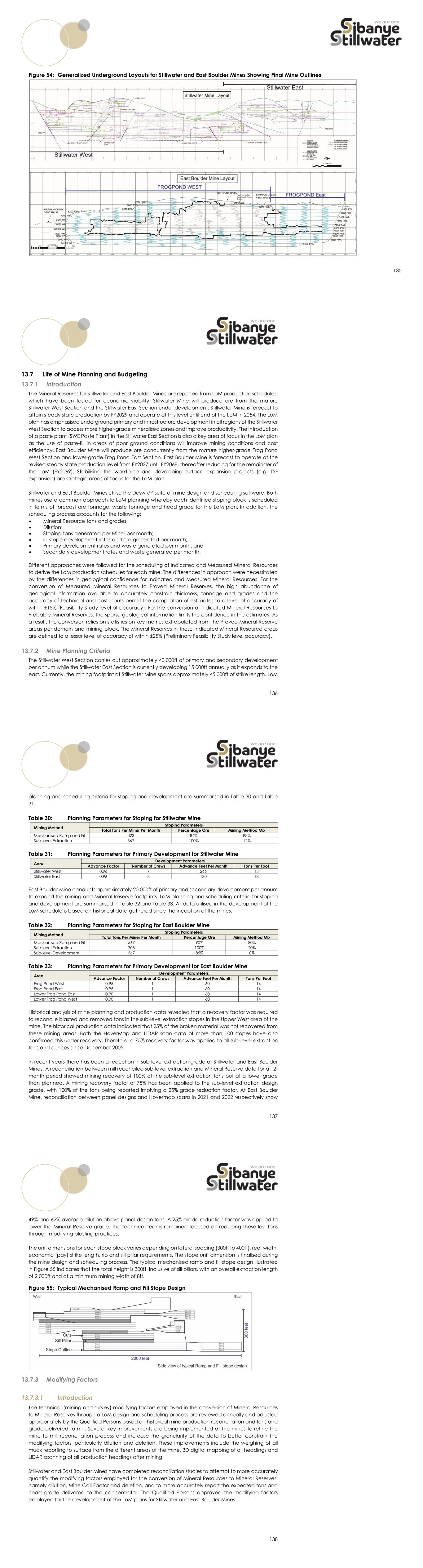
135 Figure 54: Generalized Underground Layouts for Stillwater and East Boulder Mines Showing Final Mine Outlines 136 Life of Mine Planning and Budgeting Introduction The Mineral Reserves for Stillwater and East Boulder Mines are reported from LoM production schedules, which have been tested for economic viability. Stillwater Mine will produce ore from the mature Stillwater West Section and the Stillwater East Section under development. Stillwater Mine is forecast to attain steady state production by FY2029 and operate at this level until end of the LoM in 2054. The LoM plan has emphasised underground primary and infrastructure development in all regions of the Stillwater West Section to access more higher-grade mineralised zones and improve productivity. The introduction of a paste plant (SWE Paste Plant) in the Stillwater East Section is also a key area of focus in the LoM plan as the use of paste-fill in areas of poor ground conditions will improve mining conditions and cost efficiency. East Boulder Mine will produce ore concurrently from the mature higher-grade Frog Pond West Section and lower-grade Frog Pond East Section. East Boulder Mine is forecast to operate at the revised steady state production level from FY2027 until FY2068, thereafter reducing for the remainder of the LoM (FY2069). Stabilising the workforce and developing surface expansion projects (e.g. TSF expansion) are strategic areas of focus for the LoM plan. Stillwater and East Boulder Mines utilise the DeswikTM suite of mine design and scheduling software. Both mines use a common approach to LoM planning whereby each identified stoping block is scheduled in terms of forecast ore tonnage, waste tonnage and head grade for the LoM plan. In addition, the scheduling process accounts for the following: Mineral Resource tons and grades; Dilution; Stoping tons generated per Miner per month; In-stope development rates and ore generated per month; Primary development rates and waste generated per month; and Secondary development rates and waste generated per month. Different approaches were followed for the scheduling of Indicated and Measured Mineral Resources to derive the LoM production schedules for each mine. The differences in approach were necessitated by the differences in geological confidence for Indicated and Measured Mineral Resources. For the conversion of Measured Mineral Resources to Proved Mineral Reserves, the high abundance of geological information available to accurately constrain thickness, tonnage and grades and the accuracy of technical and cost inputs permit the compilation of estimates to a level of accuracy of within ±15% (Feasibility Study level of accuracy). For the conversion of Indicated Mineral Resources to Probable Mineral Reserves, the sparse geological information limits the confidence in the estimates. As a result, the conversion relies on statistics on key metrics extrapolated from the Proved Mineral Reserve areas per domain and mining block. The Mineral Reserves in these Indicated Mineral Resource areas are defined to a lessor level of accuracy of within ±25% (Preliminary Feasibility Study level accuracy). Mine Planning Criteria The Stillwater West Section carries out approximately 40 000ft of primary and secondary development per annum while the Stillwater East Section is currently developing 15 000ft annually as it expands to the east. Currently, the mining footprint at Stillwater Mine spans approximately 45 000ft of strike length. LoM 137 planning and scheduling criteria for stoping and development are summarised in Table 30 and Table 31. Table 30: Planning Parameters for Stoping for Stillwater Mine Mining Method Stoping Parameters Total Tons Per Miner Per Month Percentage Ore Mining Method Mix Mechanised Ramp and Fill 323 84% 88% Sub-level Extraction 367 100% 12% Table 31: Planning Parameters for Primary Development for Stillwater Mine Area Development Parameters Advance Factor Number of Crews Advance Feet Per Month Tons Per Foot Stillwater West 0.96 7 266 13 Stillwater East 0.96 3 130 18 East Boulder Mine conducts approximately 20 000ft of primary and secondary development per annum to expand the mining and Mineral Reserve footprints. LoM planning and scheduling criteria for stoping and development are summarised in Table 32 and Table 33. All data utilised in the development of the LoM schedule is based on historical data gathered since the inception of the mines. Table 32: Planning Parameters for Stoping for East Boulder Mine Mining Method Stoping Parameters Total Tons Per Miner Per Month Percentage Ore Mining Method Mix Mechanised Ramp and Fill 567 90% 80% Sub-level Extraction 708 100% 20% Sub-level Development 567 85% 0% Table 33: Planning Parameters for Primary Development for East Boulder Mine Area Development Parameters Advance Factor Number of Crews Advance Feet Per Month Tons Per Foot Frog Pond West 0.95 1 60 14 Frog Pond East 0.95 1 60 14 Lower Frog Pond East 0.90 1 60 14 Lower Frog Pond West 0.90 1 60 14 Historical analysis of mine planning and production data revealed that a recovery factor was required to reconcile blasted and removed tons in the sub-level extraction stopes in the Upper West area of the mine. The historical production data indicated that 25% of the broken material was not recovered from these mining areas. Both the HoverMap and LIDAR scan data of more than 100 stopes have also confirmed this under recovery. Therefore, a 75% recovery factor was applied to all sub-level extraction tons and ounces since December 2005. In recent years there has been a reduction in sub-level extraction grade at Stillwater and East Boulder Mines. A reconciliation between mill reconciled sub-level extraction and Mineral Reserve data for a 12- month period showed mining recovery of 100% of the sub-level extraction tons but at a lower grade than planned. A mining recovery factor of 75% has been applied to the sub-level extraction design grade, with 100% of the tons being reported implying a 25% grade reduction factor. At East Boulder Mine, reconciliation between panel designs and Hovermap scans in 2021 and 2022 respectively show 138 49% and 62% average dilution above panel design tons. A 25% grade reduction factor was applied to lower the Mineral Reserve grade. The technical teams remained focused on reducing these lost tons through modifying blasting practices. The unit dimensions for each stope block varies depending on lateral spacing (300ft to 400ft), reef width, economic (pay) strike length, rib and sill pillar requirements. The stope unit dimension is finalised during the mine design and scheduling process. The typical mechanised ramp and fill stope design illustrated in Figure 55 indicates that the total height is 300ft, inclusive of sill pillars, with an overall extraction length of 2 000ft and at a minimum mining width of 8ft. Figure 55: Typical Mechanised Ramp and Fill Stope Design Modifying Factors 13.7.3.1 Introduction The technical (mining and survey) modifying factors employed in the conversion of Mineral Resources to Mineral Reserves through a LoM design and scheduling process are reviewed annually and adjusted appropriately by the Qualified Persons based on historical mine production reconciliation and tons and grade delivered to mill. Several key improvements are being implemented at the mines to refine the mine to mill reconciliation process and increase the granularity of the data to better constrain the modifying factors, particularly dilution and deletion. These improvements include the weighing of all muck reporting to surface from the different areas of the mine, 3D digital mapping of all headings and LIDAR scanning of all production headings after mining. Stillwater and East Boulder Mines have completed reconciliation studies to attempt to more accurately quantify the modifying factors employed for the conversion of Mineral Resources to Mineral Reserves, namely dilution, Mine Call Factor and deletion, and to more accurately report the expected tons and head grade delivered to the concentrator. The Qualified Persons approved the modifying factors employed for the development of the LoM plans for Stillwater and East Boulder Mines.

139 13.7.3.2 Mining Dilution Dilution factors applied for the conversion of Mineral Resources to Mineral Reserves are based on historical reconciliation for each mining method and results of the recent studies reviewing the modifying factors. Based on historical data, a dilution factor has been introduced which is the amount of material added to the ore at zero grade during stoping operations. For example, 15% more tons than planned in the case of Dow UG Upper are added to the ore tons delivered to the concentrator at an assumed 2E grade of 0opt. The result is that 15% more ore tons are delivered to the concentrator but at a lower head grade. Table 34 summarises the dilution factors and methodology utilised in the Mineral Resource to Mineral Reserve conversion for the mechanised ramp and fill and sub-level extraction mining methods in each of the sub-areas at Stillwater Mine. While Mineral Resources are reported at a single minimum mining width (MMW) of 7.5ft given the predominance of the mechanised ramp and fill method at Stillwater and East Boulder Mines, a different approach to the application of the minimum mining width was followed for mine planning. Instead of using the diluted block model employed for Mineral Resource estimation, which assumes 100% mining via the mechanised ramp and fill method, the original undiluted (channel) block model for the reef channel was used. To the channel block model, minimum mining widths adjustments based on the mining method per reef domain were applied in the Proved Mineral Reserve areas. The minimum mining widths set a standard for the best-case recovery of a Mineral Reserve for a given mining method and stope location, which can be used to measure mining performance. An extra 1.5ft hangingwall and footwall dilution is added to the ore width for areas mined using the 2.0-cubic yard LHDs but an extra 1.0ft of dilution was added for all other mining methods. In addition, if the ore width plus the extra dilution is less than or equal to the applicable minimum mining width, then the diluted width would be equal to the minimum mining width, but if the ore width plus the extra dilution is greater than the minimum mining width then the diluted width would be adopted. Since 2020, additional dilution has been added to the Mineral Reserve at Stillwater Mine, on top of the best-case recovery. This dilution was added by reef domain with the goal of aligning the Proved Mineral Reserve grade with the mill head grade. The dilution is shown in Table 34. Table 34: Mining Dilution Factors and Dilution Methodology for Stillwater Mine Domain Equipment/Process Horizontal Width (ft) True Width (ft) Dilution (%) Deletion (%) Off Shaft West Upper 1.5yd LHD – Ramp and Fill 7.4 6.5 15 16 2yd LHD – Ramp and Fill 8.5 7.5 15 16 4yd LHD – Ramp and Fill 12.0 10.6 15 16 Sub-level Extraction 5.1 4.5 15 9 Off Shaft West Lower 1.5yd LHD – Ramp and Fill 7.4 6.5 15 16 2yd LHD – Ramp and Fill 8.5 7.5 15 16 4yd LHD – Ramp and Fill 12.0 10.6 15 16 Sub-level Extraction 5.1 4.5 15 9 Off Shaft East- West 1.5yd LHD – Ramp and Fill 7.4 6.5 15 16 2yd LHD – Ramp and Fill 8.5 7.5 15 16 4yd LHD – Ramp and Fill 12.0 10.6 15 16 Sub-level Extraction 5.1 4.5 15 9 140 Domain Equipment/Process Horizontal Width (ft) True Width (ft) Dilution (%) Deletion (%) Off Shaft East- East 1.5yd LHD – Ramp and Fill 7.0 7.0 15 16 2yd LHD – Ramp and Fill 7.5 7.5 15 16 4yd LHD – Ramp and Fill 12.0 12.0 15 16 Sub-level Extraction 5.0 5.0 15 9 Blitz West 1.5yd LHD – Ramp and Fill 7.2 6.5 15 16 2yd LHD – Ramp and Fill 8.3 7.5 15 16 4yd LHD – Ramp and Fill 12.0 10.9 15 16 Sub-level Extraction 5.0 4.5 15 9 Blitz 1.5yd LHD – Ramp and Fill 6.7 6.5 15 16 2yd LHD – Ramp and Fill 7.8 7.5 15 16 4yd LHD – Ramp and Fill 12.0 11.6 15 16 Sub-level Extraction 4.7 4.5 15 9 Upper West East 1.5yd LHD – Ramp and Fill 7.5 6.0 15 16 2yd LHD – Ramp and Fill 9.4 7.5 15 16 4yd LHD – Ramp and Fill 12.0 9.6 15 16 Sub-level Extraction 5.0 4.0 15 9 Dow Upper 1.5yd LHD – Ramp and Fill 7.9 5.5 15 16 2yd LHD – Ramp and Fill 10.8 7.5 15 16 4yd LHD – Ramp and Fill 12.0 8.3 15 16 Sub-level Extraction 5.0 3.5 15 9 Dow Lower 1.5yd LHD – Ramp and Fill 7.9 5.5 15 16 2yd LHD – Ramp and Fill 10.8 7.5 15 16 4yd LHD – Ramp and Fill 12.0 8.3 15 16 Sub-level Extraction 5.0 3.5 15 9 Table 35 presents the dilution factors and methodology for the two mining methods used at East Boulder Mine. This also shows the minimum horizontal width for the mechanised ramp and fill and the sub-level extraction methods. A total of 10% of unplanned hangingwall and footwall overbreak (dilution) is added to either of the minimum horizontal widths in respect of the mechanised ramp and fill mining method whereas no unplanned dilution is anticipated in areas mined through the sub-level extraction method. Table 35: Mining Dilution Factors and Dilution Methodology for East Boulder Mine Domain Method Minimum Horizontal Width (ft) True Width (ft) Dilution (%) Deletion (%) Frog Pond East and West Sub-level Extraction 6.5 5.0 0 5 Mechanised Ramp and Fill 9.8 7.5 10 7 13.7.3.3 Deletion Deletion is applied to account for the loss in 2E ounces between the planned stopes and surface RoM stockpile feeding the concentrator. The two most common sources of deletion related to ore left on the floor of the stope and when reef material is left in situ when the actual stope shape deviates from the planned shape. The recent mine production reconciliation studies concluded that the loss in metal ounces is approximately 9% for sub-level extraction stopes and 16% for mechanised ramp and fill stopes at Stillwater Mine and 5% for sub-level extraction stopes and 7% for mechanised ramp and fill stopes at East Boulder Mine as shown in Table 34 and Table 35. These are the deletion factors applied to all blocks 141 across Stillwater and East Boulder Mines. Deletion will be monitored and revised annually when necessary. 13.7.3.4 Low Grade Reef Material It is common practice at both Stillwater and East Boulder Mines to ship material to the concentrator that is below the cut-off grade for high-grade ore when there is excess hoisting and milling capacity. This low-grade reef material (internally referred to as reef sand) is mined to access high-grade reef material. The low-grade and high-grade reef material is hoisted and milled together when there is sufficient hoisting and milling capacity. At East Boulder Mine, the 2E cut-off grade for the dominant mechanised ramp and fill stopes is 0.05opt and this aligns the head grade and tonnage of material milled and the Mineral Reserves; the 2E cut-off grade for the few sub-level extraction stopes is 0.20opt. At Stillwater Mine, reconciliation data indicates that the low-grade material has an average 2E grade of 0.12opt constitutes approximately 9% of the milled tonnage. However, the low-grade material was excluded from the LoM plan underlying the Mineral Reserves for Stillwater Mine due to the use of a higher 2E cut-off grade of 0.2opt in the Dow Upper and Dow Lower block models and 0.3opt in the rest of the mine. In future following the commissioning of the additional mill capacity at Stillwater Mine, the Qualified Person will reassess the necessity for lowering the 2E cut-off grade for Mineral Reserve reporting to improve alignment between the head grade and tonnage of material milled and the Mineral Reserves. 13.7.3.5 Tonnage Shortfall Factor A 4% tonnage shortfall factor was accounted for in the Proved and Probable Reserve tonnages for Stillwater Mine. The shortfall factor represents ore left behind in the sill that is not cleaned out and ore that was identified in the ribs, but not mined. The shortfall factor reduces tons and ounces in the Mineral Reserves, but the grade is unaffected by the application of this factor. 13.7.3.6 Mine Call Factor At this stage, no Mine Call Factors were applied to the Mineral Reserves as the loss in ounces between the stopes and the surface RoM stockpile is ascribed to deletion. Future mine to mill reconciliations at Stillwater and East Boulder Mines will establish Mine Call Factors at each of the sites which will be utilised for mine planning. Indicated Mineral Resources to Probable Mineral Reserves Conversion Factors The mineability block factor (MBF), which is calculated in the definition drilled areas, is integral to the estimation of Probable Mineral Reserves. MBFs for the various reef domains are derived from a comprehensive mine reconciliation process at Stillwater and East Boulder Mines. A MBF is calculated as the percentage of the fully diluted ore grade tonnage within a mineable area compared with the total fully diluted ore grade tonnage within the boundary area of a block or percent of material historically extracted from the block. The mineable area within a block is the area that has been mined out, is within the active stopes or has sufficient grade and continuity that it should have been or will be mined. An adjustment is made to the percentage determined to compensate for negative or positive tonnage 142 and metal ounce balances determined from historical stope reconciliation. The MBFs are used to perform adjustments of estimates when converting Indicated Mineral Resources to Probable Mineral Reserves. The final MBFs for each block shown in Table 36 reduced the final Probable Mineral Reserve yield in ore tons per foot of footwall lateral. Table 36: Mineability Block Factors for Stillwater and East Boulder Mines Mine Block MBF Stillwater Dow UG Upper 63% Dow UG Lower 58% Block-1 Upper 71% Block-1 Lower East 32% Block-1 Lower West 70% Block-2 27% Block-3 45% Block-6 53% Block-7 46% Block-8 40% Blitz West 25% Blitz 64% East Boulder Frog Pond East 70% Frog Pond West 70% Once the development and stope designs and layouts have been established in the Indicated Mineral Resource areas, Proved Mineral Reserve model statistics are applied for the derivation of production scheduled for Probable Mineral Reserve areas per block and domain. The following Proved Mineral Reserve model statistics are used: Yield in ore tons per foot of footwall lateral driven; Yield in ounces per foot of footwall lateral driven; and Grade in ounces per ton. The block and domain specific statistics are applied to respective Probable Mineral Reserve blocks for which there are development designs and high-level stope outlines to estimate the Probable Mineral Reserve tonnages and grades. Life of Mine Production Scheduling and Budgeting Process Overview A formalised LoM production scheduling and budgeting process is followed for the Sibanye-Stillwater US PGM Operations, paying attention to the integrated nature of the operations. The LoM production schedules for Stillwater and Easter Boulder Mines are tested for economic viability before being aggregated for Mineral Reserve reporting. The LoM production scheduling focuses on primary access (lateral) development design and scheduling and stope design and scheduling. Each stope is evaluated in terms of a proposal, which also contains reef access and stope designs, production schedules and results of the economic

143 assessments completed. Only the stopes that are associated with positive economic outcomes are included in the aggregate LoM production schedule for each mine. The key elements accounted for in the development, stope and loM production scheduling and budgeting processes include the following: Milling days; RoM ore tonnage and contained 2E metal content; RoM ore 2E grade; Low-grade ore (reef sand) tonnage milled; Backfill placed; Mining method splits with tonnages and grade; Primary development required; Secondary development required; Development tonnage broken; Total tonnage broken (ore and waste); and Tonnage to be milled (feed). The data (tonnage, grade and development) generated by the scheduling process feeds into the Xeras system for the development of cost budgets. The budgets account for all costs associated with mining, processing, engineering maintenance, site overheads and all capital costs associated with primary development and mine-based projects. These budgets are then accounted for in the LoM Financial Model employed for the economic viability testing of the LoM plans. LoM Production Schedule for Stillwater Mine Table 37 and Figure 56 present the LoM production schedule for Stillwater Mine to FY2054. Figure 56 shows the production ramp up associated with increased output from mainly the Stillwater East Section from FY2026 to FY2029. Production is maintained at the steady state level until FY2052 after which there is reduction in tonnage in FY2053 and FY2054. The reduction is due to depletion of the currently scheduled Measured and Indicated Mineral Resources included in the LoM production schedule for Stillwater Mine. As shown in Table 22, there is a significant proportion of Indicated and Measured Mineral Resources not scheduled for mining in the current LoM plan available for LoM extension, when required. Sustained additional definition drilling will be required to upgrade parts of the Indicated Mineral Resources to Measured Mineral Resources included in the production schedule while the unscheduled remnant Measured Mineral Resources left in the historically mined areas can potentially be brought into the production schedule at insignificant capital expenditure, when required and subject. A 10% 2E grade improvement from the average of 0.39opt to a new average of 0.45opt is also noticeable from FY2027 onwards as the mine approaches the steady state production level and high- grade ore production matches concentrator capacity. The grades reflected in Table 37 and Figure 56 incorporate the impact of the conservative approach of using a 100% ore percentage and the grade reduction factor discussed in Section 13.7.2 adopted in the conversion of Mineral Resources to Mineral Reserves. 144 Table 37: LoM Production Schedule for Stillwater Mine Figure 56: LoM RoM ore production schedule for Stillwater Mine Based on the historical performance at Stillwater Mine and considering the available mining equipment fleet for the Stillwater Mine, the Qualified Person is of the opinion that the LoM production plan is achievable. The LoM production schedule includes the scheduled Measured and Indicated Mineral Resources and excludes Inferred Mineral Resources. Life of Mine Production Schedule for East Boulder Mine Table 38 and Figure 57 present the LoM production schedule for East Boulder Mine to FY2069. Figure 57 also shows production targets from FY2024 to FY2068 planned at levels achieved in FY2021 after completion of the Fill The Mill Project. Production ceases after a reduction in FY2069. With some modest capital expenditure, there are unscheduled Measured and Indicated Mineral Resources reflected in Table 22 which can be brought into the LoM production schedule to main production at the steady FY2021 FY2022 FY2023 FY2024 FY2025 FY2026 FY2027 FY2028 FY2029 FY2030 FY2031 FY2032 Mill Feed Tons 898 229 746 956 728 560 782 359 777 832 930 205 982 715 1 109 772 1 179 270 1 200 093 1 199 806 1 200 489 Feed 2E Content (oz) 381 327 285 838 279 207 303 261 303 599 377 459 437 352 498 787 536 322 547 856 562 478 555 299 Returnable 2E Content (oz) 346 557 260 206 239 393 276 549 276 733 344 027 397 921 454 202 489 309 499 275 515 085 509 492 Feed 2E Grade (opt) 0.42 0.39 0.38 0.39 0.39 0.41 0.45 0.45 0.45 0.46 0.47 0.46 FY2033 FY2034 FY2035 FY2036 FY2037 FY2038 FY2039 FY2040 FY2041 FY2042 FY2043 FY2044 Mill Feed Tons 1 199 978 1 199 360 1 200 990 1 200 231 1 198 986 1 200 637 1 199 549 1 198 752 1 200 051 1 199 820 1 200 820 1 199 872 Feed 2E Content (oz) 548 078 541 060 545 671 542 305 538 897 533 829 538 272 540 822 520 645 518 209 537 194 542 267 Returnable 2E Content (oz) 502 245 495 265 499 585 497 625 494 227 488 557 492 074 494 497 475 578 473 200 491 188 496 765 Feed 2E Grade (opt) 0.46 0.45 0.45 0.45 0.45 0.44 0.45 0.45 0.43 0.43 0.45 0.45 FY2045 FY2046 FY2047 FY2048 FY2049 FY2050 FY2051 FY2052 FY2053 FY2054 Mill Feed Tons 1 203 718 1 199 573 1 201 232 1 199 847 1 199 641 1 199 983 1 200 282 1 199 816 1 131 245 475 596 Feed 2E Content (oz) 535 329 523 484 527 887 522 492 536 474 531 111 579 876 556 019 588 909 252 021 Returnable 2E Content (oz) 490 641 478 375 482 421 478 053 491 071 485 967 531 009 508 824 541 383 231 682 Feed 2E Grade (opt) 0.44 0.44 0.44 0.44 0.45 0.44 0.48 0.46 0.52 0.53 Parameter Actual Parameter Parameter Budget Budget Bdget 0.00 0.05 0.10 0.15 0.20 0.25 0.30 0.35 0.40 0.45 0.50 0.55 0 200 000 400 000 600 000 800 000 1 000 000 1 200 000 1 400 000 FY 2 0 2 1 FY 2 0 2 2 FY 2 0 2 3 FY 2 0 2 4 FY 2 0 2 5 FY 2 0 2 6 FY 2 0 2 7 FY 2 0 2 8 FY 2 0 2 9 FY 2 0 3 0 FY 2 0 3 1 FY 2 0 3 2 FY 2 0 3 3 FY 2 0 3 4 FY 2 0 3 5 FY 2 0 3 6 FY 2 0 3 7 FY 2 0 3 8 FY 2 0 3 9 FY 2 0 4 0 FY 2 0 4 1 FY 2 0 4 2 FY 2 0 4 3 FY 2 0 4 4 FY 2 0 4 5 FY 2 0 4 6 FY 2 0 4 7 FY 2 0 4 8 FY 2 0 4 9 FY 2 0 5 0 FY 2 0 5 1 FY 2 0 5 2 FY 2 0 5 3 FY 2 0 5 4 Fe e d 2 E G ra d e ( o p t) M ill F e e d ( To n s) Mill Feed Tons Feed 2E Grade (opt) 145 state level or to extend the LoM. In addition, sustained additional underground definition drilling will permit the upgrade of Inferred Mineral Resources and allow sustained production at the steady state level beyond FY2049. Table 38: LoM Production Schedule for East Boulder Mine Figure 57: LoM Production Schedule for East Boulder Mine Given the quantity of unscheduled Inferred Mineral Resources at East Boulder Mine, it is reasonable to expect that the definition drilling will permit the upgrading of significant Inferred Mineral Resources and subsequent conversion to Mineral Reserves. Another key attribute of the production profile is the FY2021 FY2022 FY2023 FY2024 FY2025 FY2026 FY2027 FY2028 FY2029 FY2030 FY2031 FY2032 FY2033 FY2034 FY2035 FY2036 FY2037 Mill Feed Tons 720 953 545 873 565 820 631 438 647 381 638 411 686 999 686 999 686 999 686 999 686 999 686 999 686 999 671 059 714 577 678 052 687 946 Feed 2E Content (oz) 248 473 178 471 190 623 204 535 204 480 216 877 239 399 239 399 239 399 239 399 239 399 239 399 239 399 243 043 243 334 236 887 237 420 Returnable 2E Content (oz) 223 842 160 925 164 349 184 766 184 717 195 915 216 260 216 260 216 260 216 260 216 260 216 260 216 260 219 552 219 815 213 991 214 473 Feed 2E Grade (opt) 0.34 0.33 0.33 0.32 0.32 0.34 0.35 0.35 0.35 0.35 0.35 0.35 0.35 0.36 0.34 0.35 0.35 FY2038 FY2039 FY2040 FY2041 FY2042 FY2043 FY2044 FY2045 FY2046 FY2047 FY2048 FY2049 FY2050 FY2051 FY2052 FY2053 FY2054 Mill Feed Tons 683 703 717 100 717 897 723 526 739 637 760 135 747 742 745 203 744 689 730 002 721 627 708 004 639 872 702 868 714 501 688 929 694 608 Feed 2E Content (oz) 236 277 234 410 230 246 236 669 239 466 240 638 238 341 241 038 238 597 233 056 232 147 235 460 213 543 232 196 232 869 232 062 229 963 Returnable 2E Content (oz) 213 440 211 753 207 992 213 795 216 321 217 380 215 304 217 741 215 536 210 530 209 709 212 702 192 903 209 754 210 362 209 633 207 736 Feed 2E Grade (opt) 0.35 0.33 0.32 0.33 0.32 0.32 0.32 0.32 0.32 0.32 0.32 0.33 0.33 0.33 0.33 0.34 0.33 FY2055 FY2056 FY2057 FY2058 FY2059 FY2060 FY2061 FY2062 FY2063 FY2064 FY2065 FY2066 FY2067 FY2068 FY2069 Mill Feed Tons 643 795 675 016 719 184 681 280 698 783 671 549 677 236 674 942 655 452 699 749 721 315 739 214 728 286 747 472 405 497 Feed 2E Content (oz) 211 934 223 655 238 262 225 976 237 230 235 707 237 206 233 969 232 513 237 949 236 569 237 672 233 959 236 433 134 656 Returnable 2E Content (oz) 191 450 202 039 215 233 204 135 214 302 212 925 214 280 211 355 210 040 214 951 213 704 214 700 211 346 213 581 121 641 Feed 2E Grade (opt) 0.33 0.33 0.33 0.33 0.34 0.35 0.35 0.35 0.36 0.34 0.33 0.32 0.32 0.32 0.33 Parameter Parameter Parameter Actual Budget Budget Budget 0.00 0.05 0.10 0.15 0.20 0.25 0.30 0.35 0.40 0.45 0.50 0.55 0 100 000 200 000 300 000 400 000 500 000 600 000 700 000 800 000 FY 2 0 2 1 FY 2 0 2 3 FY 2 0 2 5 FY 2 0 2 7 FY 2 0 2 9 FY 2 0 3 1 FY 2 0 3 3 FY 2 0 3 5 FY 2 0 3 7 FY 2 0 3 9 FY 2 0 4 1 FY 2 0 4 3 FY 2 0 4 5 FY 2 0 4 7 FY 2 0 4 9 FY 2 0 5 1 FY 2 0 5 3 FY 2 0 5 5 FY 2 0 5 7 FY 2 0 5 9 FY 2 0 6 1 FY 2 0 6 3 FY 2 0 6 5 FY 2 0 6 7 FY 2 0 6 9 FY 2 0 7 1 Fe e d P d + P t G ra d e ( o p t) M ill F e e d ( To n s) Mill Feed Tons Feed 2E Grade (opt) 146 consistency in 2E grades (LoM average 2E grade of approximately 0.33opt), which reflects less grade variability compared to Stillwater Mine. The forecast 2E head grades are also aligned to the three-year actual average of 0.33opt. The Qualified Person considers the forecast production levels achievable as mining equipment and manpower required to meet the increased development and stoping requirements is available at the mine and the forecast production levels have been achieved in FY2021. Mining Equipment Stillwater Mine Operations at Stillwater Mine are mechanised, employing various pieces of equipment which is listed in Table 39. For both the Stillwater West and East Sections, the mine makes use of 4.0 cubic yard and 6.0 cubic yard LHDs for infrastructure development and 2.0 cubic yard LHDs for operations on the reef including reef development and stope ore removal. Other key elements of the current fleet are face drill rigs, bolters and dump trucks. These are further supported by numerous utility and transport units. The Qualified Person is satisfied that, accounting for the geographical separation of the stoping and development areas and the daily production called for, the Stillwater East Section has sufficient equipment to meet current production targets. The Stillwater East Section is currently under development and the mining equipment included in Table 39 is currently being employed for development and ore production. The planned development and production build-up and the resulting mechanised equipment requirements are supported by a detailed capital expenditure and equipment procurement schedule, providing for mining equipment procurement of approximately US$156 million over the FY2022 to FY2026 period. The Qualified Person is of the opinion that sufficient equipment has been scheduled for procurement over the next five years to meet the expanding production levels planned for the Stillwater East Section. Table 39: Stillwater West Section Current Mechanised Mining Equipment Quantities Equipment Description Number of Existing Units Mechanised Bolters 11 CMAC Bolters 36 Face Drill Rigs 33 LHDs 75 Dump Trucks 24 Utility Vehicles 221 Tractors 6 Locomotives 13 Total 419 A combination of vertical hoisting (via the shaft) and tramming (via trains and locomotives) is employed for the transport of ore and waste from the underground workings to the processing facility on surface. Currently, 60% of ore generated underground at the Stillwater Mine is hoisted via the shaft with the remainder being transported via train. The quantity of ore transported by rail will increase as the production levels at the Stillwater East Section increase.

147 East Boulder Mine Operations at East Boulder Mine are also mechanised, employing the equipment as listed in Table 40. The mine makes use of 4.0 cubic yard and 6.0 cubic yard LHDs for infrastructure development and 2.0 cubic yard LHDs for production mining operations on the reef, including development and stope ore removal. Table 40: East Boulder Mine Mechanised Mining Equipment Quantities Equipment Description Number of Existing Units Mechanised Bolter 5 CMAC Bolter 8 Face Drill Rigs 16 LHDs 34 Dump Trucks 7 Utility Supply Flatbeds 13 Tractor 13 Forklifts 8 Skidsteer 5 Locomotives 9 Mine Transportation 62 Road Maintenance 4 Total 176 The Qualified Person is of the opinion that, accounting for the geographical separation of the stoping and development areas and the daily production called for in the LoM production plan, the mine currently has sufficient equipment to meet production targets. Logistics Stillwater Mine A total of eleven adits have been driven and access underground workings at the Stillwater Mine; six are main accesses and intakes, four are dedicated exhausts, and one is an auxiliary drift. The main rail haulage adits are the 5000W and 5000E Levels. Ore is dropped down from the upper levels via a series of ore and waste passes to transfer boxes on 5000W Level from where the rock is railed to the mine portal by diesel locomotives. The rail cars discharge ore or waste into a purpose-built tip that dumps into a haul truck. The haul truck dumps the ore onto a RoM stockpile ahead of the concentrator. The waste rock is transported to the East Side Waste Rock Dump. For the Stillwater East Mine, ore and waste is dropped down from the upper levels via a series of AlimakTM ore and waste passes to transfer boxes on the 5000E Level from where the rock is railed to the mine portal by diesel locomotives. The rail cars discharge ore or waste into two dumps that drop the material into a “box” from where surface loaders pick up the material and load haul trucks that transport and dump the ore onto a RoM stockpile ahead of the concentrator or haul the waste to the East Side Waste Rock Dump. Ore and waste rock from the levels below the portal adit of the 5000 Level is hoisted to surface via the Vertical Shaft. Ore and waste rock is transferred from all the levels above 3500W and below 5000 Level via a series of raise-bored ore and waste rock passes to the main transfer boxes on the 3500W Rail Level. 148 Rock material (ore or waste) is hauled by tandem 20-ton diesel locomotives with on average twelve ore cars per train and discharged into the mine tip on 3500 Level which reports to the shaft. All broken rock from the rock passes reports to the main jaw crusher which in turn feeds, via an apron feeder, onto the main conveyor belt on 3100W Level. The conveyor belt feeds into the main surge box prior to loading into measuring flasks at the skip boxes. The ore and waste rock is hoisted separately to surface using two 10-ton skips and deposited on separate stockpiles. There is sufficient available hoisting time to meet the LoM production requirements. A double deck 50-person capacity service cage is also available in the shaft that can move men and material from surface to service all levels between 4400 Level and 3100 Level. A fully equipped ramp has been developed down to the 1600 Level, which is currently the lowest level on the mine. The ramp is used to haul production from the 2900, 2600, and 2300 Levels by bringing rock to the loading level of the shaft on 3500 Level. All ore and waste rock generated between 1600 Level and 2900 Level gravitates via rock passes down to lower levels where it is loaded via hydraulic chutes into articulated 30-ton haul trucks. Thereafter, the rock material is hauled to 2600 Level and discharged into the appropriate tips, which feed the 2500 Level chutes. The ore and waste rock is then loaded from the 2500 Level ore and waste chutes and hauled up the ramp to the 3500 Level by 42-ton diesel powered haul trucks. The various adits and the Vertical Shaft are used for the supply of all services to the underground operations, including compressed air, water supply, power, sandfill, and the transport of men, materials, equipment, diesel, explosives and rock. The Qualified Person is of the view that logistics employed at the Stillwater West Section for the transport of men, material and rock have sufficient capacity to meet the planned production levels. Considering the current and future design logistics capacities for the Stillwater East Section, there will be sufficient logistical support to meet the planned increases in production in this section. East Boulder Mine East Boulder Mine is accessed by two parallel tunnels from the surface portal, with the 6500 Level main access level equipped with 90lb rail for the transport of personnel, materials and rock to and from the mine. All levels above and below this access level are operated as trackless mining sections. Broken rock material (ore and waste) from the upper levels above the 9100 Level is transported to internal tips within each of the independent ramp systems. Ore and waste rock from the upper levels is gravitated to the main 6500 Level rail haulage via drop raises and Alimaks to near vertical ore and waste rock passes to transfer boxes on the 6500 Level from where the rock is railed to the surface by diesel locomotives. There are some internal transfers on the 7500, 7900 and 8500 Levels to place ore and waste into the Life of Mine (LoM) pass systems. All rock material on the upper levels passes through a grizzly to prevent blockage of the rock passes. Once on surface, the rail cars discharge the ore or waste material 149 into dedicated tips from where ore is conveyed to the concentrator stockpile and waste is loaded out for tailings dam wall construction. The twin 6500 Level access tunnels (Tunnel 1 and 2) are used for the supply of all services underground, water, power, sandfill, and the transport of personnel, materials, equipment, diesel, explosives and rock. Compressed air is supplied by underground compressors near the main shop complex and all compressed air passes through a dryer to remove excess water from the air stream. During FY2019 and FY2020, Tunnel 2 was subjected to a rail upgrade to improve train cycle times required to meet the increasing levels of production (ore and waste) associated with the Fill the Mill Project. This work was completed after an 18-months period in June 2020. The Qualified Person is of the opinion that, with the completion of the Tunnel 2 rail upgrade, the logistics employed at East Boulder Mine for the transport of personnel, material and rock are adequate to meet the planned production levels. Underground Mine Services Stillwater Mine 13.11.1.1 Overview Stillwater Mine continues to develop its infrastructure in FY2024 and beyond to accommodate the increased mining footprint resulting from the Stillwater East Section expansion. The infrastructure in place has been expanded to allow the mine to execute its LoM plan. 13.11.1.2 Ventilation Access and service adits and shafts are utilised for the ventilation of underground operations. In the Stillwater West Section (Figure 58), the openings are split between: Intakes: Stillwater Shaft,50W Portal (x2), 50E Portal (x2), 5500W Portal, Benbow Portal, and 5900 Portal; Exhaust openings: 5400E Portal, 5400E Raisebore breakouts (x2), 5150W Portal, 5300W Portal, 6600W Alimak to Surface breakout, and the 6600W breakout adit, 5300W West Fork Alimak to Surface Breakout, 56E13800 Alimak to surface breakout (x2). 150 Figure 58: Graphic of Ventsim Model for the Stillwater West Section In the Stillwater East Section, there are two main intakes (5000E Rail Portal and 5000E Portal) and two 56E13800 Alimaks to Surface Breakouts for exhaust as well as the E21900 Alimak needed in FY2031as shown in Figure 59. Figure 59: Graphic of Ventsim Model for the Stillwater East Section Ventilation temperature is planned to be conducive to optimum machine and personnel productivity and this will be achieved by using propane bulk air heaters installed at the main intake airways to be operated in winter to limit water freezing. The maximum temperature for operations underground is targeted to be less than 85°F wet bulb. Stillwater Mine draws approximately 2 100 000 cubic feet per minute (cfm) of ventilation air through the exhaust system via sixteen main exhaust fans, ranging from 400hp to 850hp, situated at various ventilation raises and adits. Ventilation flow is supplemented by booster fans ranging from 30hp to 150hp to create a mine-wide negative pressure system. Stope ventilation is achieved with 30hp to 100hp axial

151 fans in conjunction with rigid and lay-flat ducting. Total primary fan power installed in the system is 8 450hp. Stillwater Mine has implemented two main ventilation system upgrades scheduled to be completed in 2024: Stillwater East Section: The four 400HP primary fans at the 56E13800 Alimak Raises to surface were upgraded to four 700HP mixed flow primary fans. The increase in horsepower was to support future production and with the mixed flow fans, the main exhaust flow can be adjusted dynamically. Portal heaters are being installed at the Benbow Portal to allow for it to be used as an intake and provide ventilation to the eastern portion of the Stillwater East Section; Stillwater West: Two 850HP primary mixed flow fans were installed at the bottom of the 5300W West Fork Alimak to Surface Breakout (WFVR) in FY2023. In FY2024, two additional 850HP units will be installed for a total of four primary fans at this location. In FY2024, the 5150W and 5300W Portals will be swapped to intake airways as the ventilation system is converted to use the WFVR as the main exhaust; and Overall strategy of the WFVR is to have the exhaust raises on the far western extent of mining with the main power at the exhaust fans, reducing the requirements for booster fans. The ventilation plan over time will convert more levels to exhausting through the WFVR and will result in the decommissioning of primary vent fans on the 4800W and 6600W Levels. The 850HP fans are mixed flow units and the main exhaust flow can be adjusted dynamically. Air entering the mine on the 5000W, 5000E, Benbow Decline, 5500W, and 5900W portals and the shaft is heated via propane bulk air heaters in the winter to prevent freezing of pipes and to ensure productive working temperatures. 13.11.1.3 Mine Dewatering The lowest level at Stillwater Mine is the 1400W Level Decline and the lowest operational level is the 1600 W Level. Stillwater Mine has installed a series of “leapfrog” interim dams and pumps for the removal of waste and fissure water from these low points. Water is pumped from one pump station/sump up to the next in consecutive lifts to bring the water out of the mine via the 1900W Level Pump Station. Drain water is collected in sumps in the various haulages and pumped to the main pumps station or a drain hole on that level to ensure haulages and declines are kept dry. The 1900W Level Pump Station comprises six main pumps which pump water to an intermediate pump station on the 2500W Level, which pumps to a series of sumps on the 3100W Level, and water is then pumped from this intermediate pump station to the 4400W Level Pump Station. This water is then pumped up to the 5300W Level Surge Reservoir from where it is gravity fed to the West Clarifier on surface. Water from areas above the 5000E Level at the Stillwater East Section reports to the East Clarifier on surface while the remainder of the water reports to the West Clarifier through the 5300W level surge reservoir. A disk filtration system installed on surface in FY2020 was commissioned in Q1 FY2021 which was designed to treat all water disposed of via percolation and the Land Application and Disposal facility adjacent to the Hertzler Tailings Storage Facility to comply with recently issued water disposal regulations. 152 The current pumping capacity at Stillwater Mine is approximately 2 500gal per minute and is adequate for handling the expected amount of mine inflow water. In addition, clarifier upgrades were completed in FY2021 to increase capacity to 2 500gal per minute for each of the two clarifiers resulting in a total clarifier capacity of 5 000gal per minute. The Qualified Person is of the opinion that Stillwater Mine has an appropriate mine dewatering system, and that the dewatering system can handle all water inflows into the mine. 13.11.1.4 Compressed Air The installed compressed air system at Stillwater Mine consists of eleven stationary compressors for 19 600cfm of capacity. There are six compressors on the east side and five on the west side. These compressors are all located on surface and are tied into the total mine system by underground piping and a 12-inch diameter on-surface trunk line between the east side compressor house and the west side Loci Barn compressor house. Compressed air volumes are being increased as production ramps up in the Stillwater East Section. In FY2021, an engineering study was launched with the inhouse projects team and executed by Nordmin Engineering to further delineate future needs. The compressed air service map for Stillwater Mine is shown in Figure 60. Figure 60: Stillwater Mine Compressed Air Service Map 153 13.11.1.5 Service Water The present service water system provides the Stillwater East Section with approximately 550gal per minute of service water, which is sufficient for the projected production from this section. The 550gal per minute was calculated by taking historical Stillwater Mine service water quantities and correlating with the total tons of rock broken during the same period. This calculation took into consideration all sandfill, diamond drilling, mining and miscellaneous water uses required for the production at Stillwater Mine. The present surface pump house delivers service water to the Stillwater East Section and, as the production in this section continues to ramp up, the service water demand will increase. To meet the increased demand, the service water piping was upgraded to 8-inch diameter Schedule 40 steel pipe. The 8-inch steel pipe was installed from the 5000E Portal through the 5000E Drive (TBM tunnel) to the bottom of the 5600E15-200 Utilities boreholes in Q1 FY2021. An upgrade of the three vertical turbine pumps motors to 100hp in the surface pump house was required to meet the ultimate steady-state water demand. These upgrades, along with the 8-inch piping upgrade, allow the surface pumps to deliver 550gal per minute of water to the 5600E15-200 Drill Water Reservoir (DWR), which was commissioned in May 2020. The 4700W service water system that feeds the FWL was commissioned in FY2022 and the 6000E reservoir was commissioned in FY2023. A schematic diagram showing the Stillwater East Section service water reticulation is shown in Figure 61. Figure 61: Stillwater East Section Service Water Reticulation 154 East Boulder Mine 13.11.2.1 Overview East Boulder Mine continues to increase its mining footprint and development continues upwards to generate more Mineral Reserves. This development is supported by the necessary mine services and infrastructure, which includes the following: 6500, 7200 and 8200 Level sand plants; An additional sand plant on the 8800 Level is planned for commissioning in FY2025; A fully optimised ventilation system is planned for completion in FY2024; Infrastructure for the 72740-ramp system; and Infrastructure required for the development of the 7500 and 7200 Footwall Levels and the Frog Pond incline. 13.11.2.2 Ventilation At East Boulder Mine, ventilation openings are split between the following: Intake ways: 6500W Portals (x2) and BVR Alimak Intake Raise (Figure 62); and Exhaust ways: Simpson Creek Raise, BVR Alimak Exhaust Raise, Graham Creek Raise, 79W FWL (surface breakout in FY2027) and 75E Alimak to surface in FY2029. East Boulder Mine draws 550 000cfm of air to ventilate the underground operations via four main mains fans, 400hp exhaust fans located at the Brownlee Ventilation Raises (two) and Simpson Creek Raise and one 600hp fan located at the Graham Creek Raise. The air is exhausted via two vertical raises to the Frog Pond adit, a raise to Simpsons Creek adit and the Graham Creek Raise. Additional forcing fans are utilised in primary development sections. Stope ventilation is achieved with 40hp to 100hp axial fans in conjunction with rigid and lay-flat ducting. Whenever possible, through ventilation is achieved by establishing a raise from the sill level of the stope to the level above. This allows separate and unique air from the primary circuit to flow through the stopes. Figure 62: Graphic of Ventsim Model for the East Boulder Mine East Boulder Mine has implemented a main ventilations system upgrade which is scheduled to be completed in FY2024 and this upgrade entails the following:

155 An 850HP mixed flow fan has been installed at the Graham Creek Raise to provide the primary exhaust for the Western extent of the East Boulder. The main exhaust flow can be adjusted dynamically; The Frog Pond Alimak Raises (BVR) have had a major upgrade with a passive heat exchanger installed on surface at the top of the raises. One raise has been commissioned as an intake airway which allows for intake air to be delivered to the 7500W FWL; The two existing 400HP fans will be replaced by a singular 600HP mixed flow fan installed at the bottom of the exhaust raise. The main exhaust flow can be adjusted dynamically; and Overall strategy is to get another intake in at East Boulder Mine to increase air quality and reduce main fan pressure. The system is split into two vent zones with it generally described as the 6500 Portals feeding the western side of the mine and exhausting through the Graham Creek Raise and the BVR intake raise feeding the eastern side and being exhausted through the Simpon Creek and BVR exhaust raise. Air entering the mine on the 6500 Level is heated via two propane bulk air heaters in the winter to prevent freezing of pipes and to ensure productive working temperatures. Air entering the mine through the BVR intake raise is passively heated using mine air from the BVR exhaust raise at the top of the BVR raises. Air temperature is monitored and air flow is regulated through the BVR intake to keep intake temperatures above freezing in the wintertime. The Qualified Person is satisfied with the current ventilation system which provides air flow that is adequate for the mine’s needs. 13.11.2.3 Mine Dewatering Mining operations are primarily situated above the main adit level allowing for water drainage from the active sites and, therefore, water pumping is not a major challenge. Furthermore, water inflow from fissures and underground aquifers is minimal. Ramp development below the 6500 Level is equipped with normal mobile pumps and cascade sump/pumps to bring the water to the 6500 Level. Water management focus is primarily to ensure that there is adequate infrastructure to manage service water and wastewater from the underground fill. The pumping capacity of the mine is approximately 396gal per minute from the main pump station on the 6500 Level, which exceeds the historical and current water flow rates of less than 250gal per minute. The Qualified Person is satisfied with the pumping capacity at the mine, which meets the current and future needs of the mine. 13.11.2.4 Compressed Air The present compressed air system at East Boulder Mine consists of five stationary compressors and a mine wide distribution system. These compressors are all located underground and are tied into the mine compressed air system by underground piping and a controller, and deliver compressed air based on demand. Air is piped via an 8-inch diameter main trunk on the 6500 Level, 6-inch diameter pipes up each ramp, and 6-inch or 8-inch lines on each level. There is also a dedicated 10-inch trunk that runs from the compressors near the central shop to the 7500 Level. All the pipes are interconnected. Each compressor is rated at 500hp and can deliver 1 750cfm at 125psig at the 6500 Level elevation. Collectively, all compressors can deliver over 8 700cfm but only four compressors are required to run at 156 peak demand, with normal duty requiring three compressors run online and with the fifth providing the required redundancy. A compressed air dryer was commissioned on 6500 Level in early FY2020 to reduce water in the air lines. A 10-inch diameter pipeline loop from the 7500 Level up to the 8200 Level was installed in FY2020 to increase storage capacity above the 7500 Level. A 200 HP satellite compressor was added in FY2021 to service a long hole drilling machine, with three more satellite compressors to be added and installed at long hole drilling locations. In addition, studies on long-term engineering and option planning started in FY2021 and scheduled for completion in FY2022 will which more closely define the long-term compressed air requirements and strategy. As a result, the Qualified Person is satisfied with the compressed air system in place at East Boulder Mine. The compressed air service map for East Boulder Mine is shown in Figure 63. Figure 63: East Boulder Mine Compressed Air Distribution System 13.11.2.5 Service Water The current service water system consists of multiple DWRs situated on each level underground (Figure 64). The DWR system is fed from the riser pump located at the surface clarifier, which receives the return water from the mining activities underground. The clarified water is pumped underground via 157 a pipeline from the clarifier to the 6500 Level DWR from where it is pumped vertically to the DWRs at the higher levels in the mine in a cascading fashion – DWRs are located at the 6500, 6700, 6900, 7200, 7500, 7900, 8200, 8500 and 8800 Levels. Clean Portal Water is also distributed to the 6500 DWR via a pipeline in Tunnel 1 from a sump inside Portal 1. The future water distribution plan provides for one more DWR at the 9100 Level. The DWRs are equipped with pump skids that have two pumps per skid, each pump delivering 300gal per minute at 350ft of head. The 7900, 8200, 8500 and 8800 DWRs are controlled via variable frequency drives (VFDs) and 40hp pumps, whereas the rest of the DWRs have 125hp direct feed pumps. Each system is sufficient and the DWR planned will be constructed with 40hp pumps and VFDs. The Qualified Person is satisfied with the current service water system, which provides sufficient service water to the mining operations, and no major additions are required. The planned upgrades will ensure the mine has sufficient service water for to the expanded operations. Figure 64: East Boulder Mine Drill Water Reservoir Layout Manpower Table 41 and Table 42 show the LoM manpower plans for Stillwater and East Boulder Mines, respectively. The revision of the LoM plan for Stillwater Mine has resulted in a progressive reduction in the headcount for the mining, technical services and administration, concentrator, surface operations and engineering and maintenance complements, from a total headcount of 1 236 in FY2021 to 1 102 in FY2023. The reduction trend is planned to continue across all disciplines except for concentrator and surface 158 operations resulting in a total headcount of 995 in FY2024 followed by a progressive increase from FY2025 (total headcount of 1 126) to FY2031 (total headcount of 1 288) in line with the planned production ramp up. As per the current LoM plan, total headcount is planned to remain stable at the FY2031 level for the remainder of the LoM to sustain the planned steady state production levels. Total headcount for East Boulder Mine has been stable over the period FY2021 to FY2023 (457-461) but this is planned to increase by 9% during FY2024 and FY2025 to 503. Total headcount will remain stable at 501 from FY2026 onwards until FY2046 and thereafter decrease progressively until the end of the LoM. Table 41: LoM Manpower Plan for Stillwater Mine FY2021 FY2022 FY2023 FY2024 FY2025 FY2026 FY2027 FY2028 FY2029 FY2030 FY2031 FY2032 Mining 870 790 708 597 598 666 686 725 753 757 789 773 Engineering Maintenance 148 140 205 199 199 227 230 240 250 250 250 250 Technical Services & Admin 147 141 140 96 97 115 115 117 117 117 117 117 Concentrator 43 43 33 42 42 58 58 61 66 71 71 71 Surface 28 22 16 61 62 60 59 60 62 62 62 62 Total Mine Site 1 236 1 136 1 102 995 998 1 125 1 147 1 202 1 247 1 256 1 288 1 271 FY2033 FY2034 FY2035 FY2036 FY2037 FY2038 FY2039 FY2040 FY2041 FY2042 FY2043 FY2044 Mining 767 768 764 762 765 758 750 750 740 733 728 688 Engineering Maintenance 250 250 250 250 250 250 250 250 250 250 250 250 Technical Services & Admin 117 117 117 117 117 117 117 117 117 117 117 117 Concentrator 71 71 71 71 71 71 71 71 71 71 71 71 Surface 62 62 62 62 62 62 62 62 62 62 62 62 Total Mine Site 1 266 1 267 1 263 1 261 1 263 1 257 1 249 1 249 1 239 1 232 1 227 1 187 FY2045 FY2046 FY2047 FY2048 FY2049 FY2050 FY2051 FY2052 FY2053 FY2054 Mining 678 666 645 654 551 533 544 507 465 295 Engineering Maintenance 250 250 250 250 238 238 238 214 194 141 Technical Services & Admin 117 117 117 117 117 117 115 115 104 104 Concentrator 71 71 71 71 71 71 71 46 46 46 Surface 62 58 58 58 58 58 58 46 46 46 Total Mine Site 1 177 1 161 1 140 1 149 1 034 1 016 1 025 927 855 632 Actual Description Budget Description Description Budget Budget

159 Table 42: LoM Manpower Plan for East Boulder Mine The Qualified Persons noted that lower mining productivities when viewed in terms of tonnage generated per number of mining employees are forecast at East Boulder Mine from FY2024 until FY2040 (average 1 362 tons per employee) than achieved since FY2021 (1 440 tons per employee) after which productivity is forecast to increase to the FY2021-2023 level. Using this metric, productivity levels at Stillwater Mine declined from 727 tons per employee in FY2021 to 661 tons per employee in FY2023. A reversal of this downward trend is anticipated in FY2024 followed by a progressive improvement to approximately 955 tons per employee in FY2030 from where it is kept at the level of 932-1323 tons per employee for the remainder of the LoM. The Qualified Persons are satisfied with the current manpower plans for Stillwater and East Boulder Mines which are aligned to the actual levels of productivity achieved previously. FY2021 FY2022 FY2023 FY2024 FY2025 FY2026 FY2027 FY2028 FY2029 FY2030 FY2031 FY2032 FY2033 FY2034 FY2035 FY2036 FY2037 Mining 294 293 311 308 318 315 315 315 315 315 315 315 315 315 315 315 315 Engineering Maintenance 71 74 64 91 91 91 91 91 91 91 91 91 91 91 91 91 91 Technical Services & Admin 46 51 47 50 50 51 51 51 51 51 51 51 51 51 51 51 51 Concentrator 30 27 28 33 33 33 33 33 33 33 33 33 33 33 33 33 33 Surface 16 11 11 11 11 11 11 11 11 11 11 11 11 11 11 11 11 Total Mine Site 457 456 461 493 503 501 501 501 501 501 501 501 501 501 501 501 501 FY2038 FY2039 FY2040 FY2041 FY2042 FY2043 FY2044 FY2045 FY2046 FY2047 FY2048 FY2049 FY2050 FY2051 FY2052 FY2053 FY2054 Mining 315 315 315 315 315 315 315 315 315 307 307 307 307 306 306 306 299 Engineering Maintenance 91 91 91 91 91 91 91 91 91 91 91 91 91 91 91 91 92 Technical Services & Admin 51 51 51 51 51 51 51 51 51 51 51 51 51 51 51 51 51 Concentrator 33 33 33 33 33 33 33 33 33 33 33 33 33 33 33 33 33 Surface 11 11 11 11 11 11 11 11 11 11 11 11 11 11 11 11 11 Total Mine Site 501 501 501 501 501 501 501 501 501 493 493 493 493 492 492 492 486 FY2055 FY2056 FY2057 FY2058 FY2059 FY2060 FY2061 FY2062 FY2063 FY2064 FY2065 FY2066 FY2067 FY2068 FY2069 Mining 299 291 291 291 291 236 236 221 216 204 204 204 160 108 60 Engineering Maintenance 92 92 92 92 92 78 78 78 78 78 78 78 56 56 56 Technical Services & Admin 51 51 51 51 51 47 47 47 47 47 47 47 29 29 29 Concentrator 33 33 33 33 33 33 33 33 33 33 33 16 9 9 9 Surface 11 11 11 11 11 11 11 11 11 11 11 11 8 8 8 Total Mine Site 486 478 478 478 478 405 405 390 385 373 373 356 262 210 162 Description Description Budget Budget Budget Description Actual 160 PROCESSING AND RECOVERY Mineral Processing Methods Background Ore processing plants at Stillwater and East Boulder Mines and the smelter and base metal refinery at the Columbus Metallurgical Complex have been in continuous operation for decades. All metallurgical processes and technology in place at the ore processing, smelting and refining facilities are appropriate, well-proven and aligned to norms and practices in the PGM sectors. The processing methods were selected based on metallurgical testwork carried out as part of feasibility studies at the time of development. However, results of the testwork have been superseded by actual operational data and experience accumulated over several years of continuous successful operation of these facilities. Accordingly, there are no plans to introduce new processing technology at the processing facilities. The recently completed plant capacity upgrades at Stillwater Concentrator and the metallurgical complex were based on existing technology and process flowsheets. There are no expansion plans anticipated at the East Boulder Concentrator which has historically been operated below nameplate capacity. Higher utilisation of the installed capacity at the East Boulder Concentrator continues based on existing and proven technology and process flowsheet. Ore Processing Stillwater Concentrator 14.2.1.1 Plant Design and Equipment Specifications The Stillwater Concentrator was commissioned in 1986 and since been upgraded to 3 400-ton per operating day conventional crushing, milling, flotation, and filtration plant producing a PGM-base metal sulphide concentrate suitable for downstream smelting and refining. Primary crushing equipment consists of Metso (Nordberg) feeder and jaw crusher with a capacity of 300 tons per operating hour. Primary grinding equipment consists of: A Metso 3 000HP semi-autogenous grinding (SAG) mill charged with 4-inch hardened steel balls and with a capacity of 179 tons per operating hour; and A Metso 3 000HP ball mill charged with 3-inch hardened steel balls and with a capacity of 179 tons per operating hour. The flotation circuit consists of: Flash flotation circuit containing a Metso flash cell and Metso cleaner cells; Rougher flotation circuit consisting of twelve Metso 300cft convention flotation cells; Rougher-cleaner flotation circuit consisting of two 3ft Metso column flotation cells, two 1.5ft Metso column flotation cells, and three Metso 350cft conventional cleaner flotation cells; Middling flotation circuit consisting of six Metso 300cft conventional flotation cells; Middling cleaner flotation circuit consisting of eight Metso 300cft conventional cleaner flotation cells; Scavenger flotation circuit consisting of ten Metso 300cft conventional flotation cells; and 161 Scavenger cleaner flotation circuit consisting of eight Metso 300cft conventional cleaner flotation cells and a 5ft column flotation cell; Filtration equipment consists of a Metso 10 plate pressure filter with a capacity of 100 tons concentrate per day (4 300 tons per day ore feed). 14.2.1.2 Plant Capacity The PGM concentrator at Stillwater Mine was commissioned in 1986 as a 500-ton per operating day conventional crushing, milling and flotation plant. Following several process modifications and expansions, the concentrator capacity increased to approximately 3 100 tons per operating day by FY2020. The concentrator has historically operated on a ten-day or eleven-day fortnight basis and has been switched off every second weekend resulting in approximately 75% utilisation. This was required to maintain the balance with mining volumes of 750 000 tons per year at the time, but the concentrator currently operates on a continuous basis with a target utilisation of 92% due to the increased tonnage delivered from the mine in recent years. At the 92% utilisation, the plant capacity before expansion is equivalent to approximately 1.04 million tons per year. A significant capital expansion project at the Stillwater Concentrator was finalised and commissioned in late (Q3) FY2023. This expansion has resulted in an operational capacity increasing to 3 400 tons per operating day (i.e., 1.1 million tons per year) at full utilisation. This capacity will accommodate additional ore from the Stillwater East Section until FY2028 and additional capacity is required for the steady state steady production targets exceeding 1.1 million tons per annum. A bottleneck in the flotation circuits needs to be resolved to upgrade capacity further to 4100 tons per day (i.e. approximately 1.4 million tons per annum at 92% utilisation) as per the Blitz Project plans. Mechanical equipment needed for the flotation circuit upgrades has already been procured as part of the Blitz Project Sibanye-Stillwater has undertaken to complete this work at an additional cost of approximately $1.8 million (labour cost) a year before the capacity of 1.4 million tons is required. The following areas of the concentrator have already been upgraded to increase tonnage throughput capacity as part of the Blitz Project: Milling Section: A new SAG mill, a new ball mill and new pebble crushing facility were installed to replace an existing comminution facility which was decommissioned. The new milling building was commissioned in late (Q3) FY2023 and there is no additional project capital provision for this section beyond FY2023; Flotation Section: Associated with the milling circuit replacement, the flash flotation cells were also be replaced with new cells. The remainder of the flotation circuit required minimal expansion, with the addition of a few cleaner cells, and the increase in capacity of some of the float column cells. The old float plant building had sufficient capacity and infrastructure to accommodate the minor expansions required. This upgraded circuit was commissioned in parallel with the new milling circuit in Q3 FY2023. Further upgrades to the remaining flotations circuits required to increase plant capacity from 3 400 tons to 4 110 ton per day (i.e. 1.1 million tons to 1.4 million tons per year at 92% utilisation) have been considered but deferred to a time when the additional capacity is needed (i.e. from FY2029 onwards); Tailings Section: Upgrades were completed in FY2023 on the tailings distribution system between the mill and final tailings discharge pump to the TSF. These also included upgrades to slurry pumps, 162 distribution lines, and system controls to handle the increased throughput. Minor upgrades are planned to be completed in FY2024 to the tailings lines going to the TSF to improve system reliability at the maximum planned throughput; and Concentrate Handling: Upgrade of the concentrate handling facility was commissioned at the end of FY2020. The concentrate thickener has been replaced and a new stock tank and filter press have been installed. The dry concentrate bin has also been replaced to allow delivery into the new side-tipping trucks, which have been implemented for the transportation of the concentrate from the mine to the Columbus Metallurgical Complex. These same trucks return with slag and reverts for reprocessing. 14.2.1.3 Manpower Requirements The plant staffing comprises four crews operating on two 12-hour shifts of one Supervisor, four Operators and a Tailings Storage Facility Operator. Current budget staff is twelve Maintenance (Mechanical) Technicians to support Concentrator, Surface Operations, Paste Plant, Water Treatment, and Building Maintenance and these technicians follow the 24-hour per 7-day week shift rotation system. There are four Electrical Technicians with the same area of responsibility as Concentrator Maintenance Technicians but working on a seven-day per week basis. Major and routine planned maintenance is scheduled on a regular basis to ensure the plant mechanical availability of 92% is maintained. 14.2.1.4 Process Description The concentrator currently receives ore from the Off-shaft and Upper West areas of the Stillwater West Section and Blitz West area of the Stillwater East Section as well as slag and brick recycle materials from the smelter. Smelter slag and brick recycle materials are delivered to the primary crushing area and are campaign-treated through the concentrator. A typical slag campaign would last 24 hours and would entail process changes such as different reagent dosages, lower throughput and shutting down the flash float circuit. Approximately 75% to 80% recovery of contained 2E is the sustainable target for these campaigns. The concentrator has previously processed approximately 1.1 million tons per year of RoM ore feed at a 92% total 2E recovery from this material (FY2020). The concentrator capacity expansion was based on the existing process flow diagram which is presented in Figure 65. The process comprises open circuit crushing followed by two stages of milling, with the sized product being delivered to the flotation circuit. Various stages of flotation including roughing, cleaning and scavenging in addition to a regrind circuit ensure that recovery is optimised and concentrate grades suitable for smelting are realised.

163 Figure 65: Block Flow Diagram of the Stillwater Concentrator 14.2.1.5 Production Plan The recent history and budget operational parameters for the concentrator are presented together with the LoM production plan in Table 43, Figure 66 and Figure 67. The FY2021, FY2022 and FY2023 data presented reflects the actual annual performance whilst the FY2024 to FY2054 data represents current budget targets. The current operational methods and capacities are adequate until FY2028 after which flotation circuit upgrades will be required to increase overall concentrator capacity to 1.4 million tons per annum. The metallurgical efficiencies projected have not been obtained historically, but as a result of the process upgrades completed in FY2023 and the minor increases projected, these are deemed reasonable budget targets. However, the flotation circuit debottlenecking project should be completed to increase concentrator capacity to 1.1 million tons before FY2029. Table 43: Stillwater Concentrator Actual and Forecast LoM Operational Throughput and Outputs FY2021 FY2022 FY2023 FY2024 FY2025 FY2026 FY2027 FY2028 FY2029 FY2030 FY2031 FY2032 Total Feed tons 936 439 779 288 792 082 782 359 777 832 930 205 982 715 1 109 772 1 179 270 1 200 093 1 199 806 1 200 489 Concentrate Produced tons 22 703 19 415 21 293 21 132 21 000 25 112 26 483 29 932 31 867 32 394 32 543 32 624 2E Recovery % 91.62 91.70 91.20 91.80 91.80 91.79 91.63 91.70 91.88 91.77 92.22 92.40 2E Metal Produced oz 346 556 260 206 262 923 276 549 278 684 344 027 397 921 454 202 489 309 499 275 515 085 509 492 FY2033 FY2034 FY2035 FY2036 FY2037 FY2038 FY2039 FY2040 FY2041 FY2042 FY2043 FY2044 Total Feed tons 1 199 978 1 199 360 1 200 991 1 200 231 1 198 986 1 200 637 1 199 549 1 198 752 1 200 051 1 199 820 1 200 820 1 199 872 Concentrate Produced tons 32 570 32 517 32 568 32 621 32 569 32 546 32 480 32 465 32 468 32 451 32 521 32 557 2E Recovery % 92.28 92.18 92.20 92.41 92.36 92.16 92.06 92.08 91.99 91.96 92.08 92.25 2E Metal Produced oz 502 245 495 265 499 585 497 625 494 227 488 557 492 074 494 497 475 578 473 200 491 188 496 765 FY2045 FY2046 FY2047 FY2048 FY2049 FY2050 FY2051 FY2052 FY2053 FY2054 Total Feed tons 1 203 718 1 199 573 1 201 232 1 199 847 1 199 641 1 199 983 1 200 282 1 199 816 1 131 245 475 596 Concentrate Produced tons 32 677 32 469 32 515 32 516 32 525 32 521 32 555 32 521 30 802 12 950 2E Recovery % 92.30 92.03 92.03 92.14 92.18 92.15 92.22 92.16 92.58 92.58 2E Metal Produced oz 490 641 478 375 482 421 478 053 491 071 485 967 531 009 508 824 541 383 231 682 Parameter Unit Unit Unit Actual Parameter Parameter Budget Budget Budget 164 Figure 66: Stillwater Concentrator Actual and Forecast LoM Operational Throughput and Outputs Figure 67: Stillwater Concentrator Actual and Forecast LoM Operational Data 14.2.1.6 Energy Requirements The energy requirement for the Stillwater Concentrator is 6.5MW and is fed by a feed rated for 15MW and a 21.8MW substation. Power to the concentrator is fed from the West Substation as detailed in Section 15.1.4 and is delivered to the plant via incoming Line #2. The substation has sufficient capacity for the concentrator and the planned expansions. - 5 10 15 20 25 30 35 40 0 200 400 600 800 1 000 1 200 1 400 1 600 FY 2 0 2 1 FY 2 0 2 2 FY 2 0 2 3 FY 2 0 2 4 FY 2 0 2 5 FY 2 0 2 6 FY 2 0 2 7 FY 2 0 2 8 FY 2 0 2 9 FY 2 0 3 0 FY 2 0 3 1 FY 2 0 3 2 FY 2 0 3 3 FY 2 0 3 4 FY 2 0 3 5 FY 2 0 3 6 FY 2 0 3 7 FY 2 0 3 8 FY 2 0 3 9 FY 2 0 4 0 FY 2 0 4 1 FY 2 0 4 2 FY 2 0 4 3 FY 2 0 4 4 FY 2 0 4 5 FY 2 0 4 6 FY 2 0 4 7 FY 2 0 4 8 FY 2 0 4 9 FY 2 0 5 0 FY 2 0 5 1 FY 2 0 5 2 FY 2 0 5 3 FY 2 0 5 4 FY 2 0 5 5 C o n c e n tr a te ( th o u sa n d t o n s) Fe e d ( th o u sa n d t o n s) RoM Ore Feed Recycle Feed Concentrator Capacity Concentrate Produced 0 100 200 300 400 500 600 80 81 82 83 84 85 86 87 88 89 90 91 92 93 94 FY 2 0 2 1 FY 2 0 2 2 FY 2 0 2 3 FY 2 0 2 4 FY 2 0 2 5 FY 2 0 2 6 FY 2 0 2 7 FY 2 0 2 8 FY 2 0 2 9 FY 2 0 3 0 FY 2 0 3 1 FY 2 0 3 2 FY 2 0 3 3 FY 2 0 3 4 FY 2 0 3 5 FY 2 0 3 6 FY 2 0 3 7 FY 2 0 3 8 FY 2 0 3 9 FY 2 0 4 0 FY 2 0 4 1 FY 2 0 4 2 FY 2 0 4 3 FY 2 0 4 4 FY 2 0 4 5 FY 2 0 4 6 FY 2 0 4 7 FY 2 0 4 8 FY 2 0 4 9 FY 2 0 5 0 FY 2 0 5 1 FY 2 0 5 2 FY 2 0 5 3 FY 2 0 5 4 FY 2 0 5 5 2 E M e ta l P ro d u c e d ( k o z) 2 E R e c o v e ry ( % ) 2E Metal Produced 2E Recovery 165 14.2.1.7 Water Requirements The maximum water requirement for the Stillwater Concentrator when operating is 2 000gal per minute and demand ranges from 1 300gal to 2 000gal per minute. The Stillwater Concentrator water balance is water-positive, and the concentrator receives return water from the Hertzler TSF, as well as treated water from underground. The Nye TSF is used as the excess water storage facility. 14.2.1.8 Reagent Requirements -The process materials (reagents and steel balls) used in the Stillwater Concentrator are readily available and mostly sourced from credible suppliers located in the USA or North America. Reagents commonly used are potassium amyl xanthate, di-thiophosphate, carboxymethyl cellulose, methyl Isobutyl carbinol, and flocculant/coagulant. Hardened steel balls in 3-inch and 4-inch size are used in the primary grinding mills and are consumed at approximately 1lb/ton total. The Qualified Persons are satisfied that the measures in place in respect of the supply of process materials which should ensure security of supplies over the life of the operations East Boulder Concentrator 14.2.2.1 Plant Design and Equipment Specifications The East Boulder Concentrator was commissioned in 2001 as a 2 000-ton per operating day conventional crushing, milling, flotation, and filtration plant producing a PGM-base metal sulphide concentrate suitable for downstream smelting and refining. Primary crushing equipment consists of Metso (Nordberg) feeder and jaw crusher with a capacity 300 tons per operating hour. Primary grinding equipment consists of: A Metso 2 000HP SAG mill charged with 4-inch hardened steel balls and with a capacity of 150 tons per operating hour; A Metso 2 000HP ball mill charged with 3-inch hardened steel balls and with a capacity of 105 tons per operating hour. The flotation circuit consists of: Flash flotation circuit containing a Metso unit cell and Metso unit cell cleaner; Rougher flotation consisting of ten Metso 5cft convention flotation cells; Rougher-cleaner flotation circuit consisting of a 3ft Metso column flotation cell, four Metso 100cft conventional cleaner flotation cells, and four Metso 50cft conventional cleaner flotation cells; Middling flotation circuit consisting of ten Metso 500cft conventional flotation cells; Middling cleaner flotation circuit consisting of four Metso 100cft conventional cleaner flotation cells, and four Metso 50cft conventional cleaner flotation cells; Scavenger flotation consisting of twelve Metso 500cft conventional flotation cells. Scavenger cleaner flotation consisting of eight Metso 100cft conventional cleaner flotation cells and a 3ft column flotation cell. 166 Filtration equipment consists of a Metso-Outotec 8-plate pressure filter with a capacity of 100 tons concentrate per day (4 000 tons per day ore feed). 14.2.2.2 Plant Capacity The concentrator at East Boulder Mine was commissioned in 2001 as a 2 000-ton per operating day conventional crushing, milling and flotation plant producing. The design capacity of the concentrator is approximately 2 500 tons per operating day following several process modifications and expansions. This capacity is equivalent to an estimated 838 000 tons per year at 92% operational utilisation and sufficient for the LoM annual production targets. However, at the current 75% utilisation and 99% availability and operating on a four-crew schedule, the current capacity of the concentrator is approximately 2 400 tons per operating day. This capacity is equivalent to an estimated 650 000 tons per year, which is sufficient capacity for the planned production targets until FY2026. The concentrator will be operated at higher utilisation than currently to accommodate higher throughputs (up to 760 000 tons per annum) planned from FY2027 onwards. Prior to FY2017, the concentrator processed approximately 650 000 tons per year of RoM ore feed from the Frog Pond East and West Sections of East Boulder Mine and achieved total 2E recoveries of approximately 91%. Operating the plant below capacity necessitated a ten-day or eleven-day fortnight operating basis, with plant switch-off every second weekend resulting in approximately 75% utilisation. Due to a higher utilisation of the concentrator following the implementation of the Fill The Mill Project, the concentrator achieved peak production of 722 000 tons milled in FY2020. The Qualified Person notes the plan to sustain the budgeted recovery to an average 91% for the LoM should be achievable through metallurgical input and optimisation as before. Furthermore, the planned tonnage throughput peaking at approximately 760 000 tons per annum for the LoM is achievable considering that the annual targets are significantly below the 838 000 tons per year plant capacity at full operational utilisation. The upgraded concentrate handling facility which includes larger filter press and concentrate storage bin than were previously used and cater to side-tipping bulk trucks can handle the anticipated concentrate volumes. The side-tip trucks have the added advantage of also being usable for transporting slag or bricks from the Columbus Metallurgical Complex to the concentrators. 14.2.2.3 Manpower Requirements The plant staffing comprises three crews operating two 12-hour shifts of one Supervisor and three Concentrator Operators and one Heavy Equipment Operator per rotating crew as well as one Water Systems Operator. Maintenance is currently staffed with six Mechanical Technicians, two Electrical Technicians, one Maintenance General Foreman, one Maintenance Planner and one Supervisor, all of whom currently work on a five-day per week basis. Major and routine planned maintenance is scheduled for shut-down intervals lasting 12 to 36 hours twice per month, which has resulted in plant mechanical availability of more than 99%. These staffing levels

167 are adequate for the current levels of operation. The increase in throughput necessitated the appointment of a fourth shift and the transition to continuous operations. Therefore, planned maintenance shut-downs have been initiated to ensure plant availability is maintained. 14.2.2.4 Process Description The simplified block flow for the East Boulder Concentrator is presented in Figure 68. The process comprises open circuit crushing followed by two stages of milling, with the sized product being delivered to the flotation circuit. Various stages of flotation including roughing, cleaning and scavenging in addition to a regrind circuit ensure that recovery is optimised and concentrate grades suitable for smelting are realised. Figure 68: East Boulder Concentrator Simplified Block Flow Diagram 14.2.2.5 Production Plan The recent history and budget operational parameters for the East Boulder Concentrator are presented together with the LoM budget data for the East Boulder Concentrator in Table 44, Figure 70. The FY2021, FY2022 and FY2023 data presented reflects the actual annual performance whilst the FY2024 to FY2069 data represents current budget targets. The current operational methods and capacities are adequate. Metallurgical efficiencies projected have also been sustainably obtained historically and are thus reasonable budget targets. 168 Table 44: East Boulder Concentrator Actual and Forecast LoM Operational Throughput and Outputs The key variables reviewed for the LoM are presented in Figure 69 and Figure 70. Figure 69: East Boulder Concentrator Actual and Forecast LoM Operational Throughput and Outputs FY2021 FY2022 FY2023 FY2024 FY2025 FY2026 FY2027 FY2028 FY2029 FY2030 FY2031 FY2032 FY2033 FY2034 FY2035 FY2036 FY2037 Total Feed tons 720 033 545 873 565 820 631 438 647 381 638 411 686 999 686 999 686 999 686 999 686 999 686 999 686 999 671 059 714 577 678 052 687 946 Concentrate Produced tons 17 859 17 134 17 514 15 525 15 917 15 696 16 891 16 891 16 891 16 891 16 891 16 891 16 891 16 499 17 569 16 671 16 914 2E Recovery % 90.60 91.33 90.86 90.97 90.97 90.97 90.97 90.97 90.97 90.97 90.97 90.97 90.97 90.97 90.97 90.97 90.97 2E Metal Produced oz 223 842 160 925 164 349 184 766 184 717 195 915 216 260 216 260 216 260 216 260 216 260 216 260 216 260 219 552 219 815 213 991 214 473 FY2038 FY2039 FY2040 FY2041 FY2042 FY2043 FY2044 FY2045 FY2046 FY2047 FY2048 FY2049 FY2050 FY2051 FY2052 FY2053 FY2054 Total Feed tons 683 703 717 100 717 897 723 526 739 637 760 135 747 742 745 203 744 689 730 002 721 627 708 004 639 872 702 868 714 501 688 929 694 608 Concentrate Produced tons 16 810 17 631 17 651 17 789 18 185 18 689 18 384 18 322 18 309 17 948 17 742 17 407 15 732 17 281 17 567 16 938 17 078 2E Recovery % 90.97 90.97 90.97 90.97 90.97 90.97 90.97 90.97 90.97 90.97 90.97 90.97 90.97 90.97 90.97 90.97 90.97 2E Metal Produced oz 213 440 211 753 207 992 213 795 216 321 217 380 215 304 217 741 215 536 210 530 209 709 212 702 192 903 209 754 210 362 209 633 207 736 FY2055 FY2056 FY2057 FY2058 FY2059 FY2060 FY2061 FY2062 FY2063 FY2064 FY2065 FY2066 FY2067 FY2068 FY2069 Total Feed tons 643 795 675 016 719 184 681 280 698 783 671 549 677 236 674 942 655 452 699 749 721 315 739 214 728 286 747 472 405 497 Concentrate Produced tons 15 829 16 596 17 682 16 750 17 181 16 511 16 651 16 595 16 115 17 204 17 735 18 175 17 906 18 378 9 970 2E Recovery % 90.97 90.97 90.97 90.97 90.97 90.97 90.97 90.97 90.97 90.97 90.97 90.97 90.97 90.97 90.97 2E Metal Produced oz 191 450 202 039 215 233 204 135 214 302 212 925 214 280 211 355 210 040 214 951 213 704 214 700 211 346 213 581 121 641 Budget Budget Budget Parameter Unit Parameter Unit Actual Parameter Unit - 2 4 6 8 10 12 14 16 18 20 - 50 100 150 200 250 300 350 400 450 500 550 600 650 700 750 800 850 900 FY 2 0 2 1 FY 2 0 2 2 FY 2 0 2 3 FY 2 0 2 4 FY 2 0 2 5 FY 2 0 2 6 FY 2 0 2 7 FY 2 0 2 8 FY 2 0 2 9 FY 2 0 3 0 FY 2 0 3 1 FY 2 0 3 2 FY 2 0 3 3 FY 2 0 3 4 FY 2 0 3 5 FY 2 0 3 6 FY 2 0 3 7 FY 2 0 3 8 FY 2 0 3 9 FY 2 0 4 0 FY 2 0 4 1 FY 2 0 4 2 FY 2 0 4 3 FY 2 0 4 4 FY 2 0 4 5 FY 2 0 4 6 FY 2 0 4 7 FY 2 0 4 8 FY 2 0 4 9 FY 2 0 5 0 FY 2 0 5 1 FY 2 0 5 2 FY 2 0 5 3 FY 2 0 5 4 FY 2 0 5 5 FY 2 0 5 6 FY 2 0 5 7 FY 2 0 5 8 FY 2 0 5 9 FY 2 0 6 0 FY 2 0 6 1 FY 2 0 6 2 FY 2 0 6 3 FY 2 0 6 4 FY 2 0 6 5 FY 2 0 6 6 FY 2 0 6 7 FY 2 0 6 8 FY 2 0 6 9 FY 2 0 7 0 C o n c e n tr a te P ro d u c e d ( th o u sa n d t o n s) Fe e d ( th o u sa n d t o n s) Total Feed Concentrator Nameplate Capacity Concentrate Produced 169 Figure 70: East Boulder Concentrator Actual and Forecast LoM Operational Data 14.2.2.6 Energy Requirements The energy requirement for the East Boulder Concentrator is 4.5MW and is fed by a 20MW substation. The concentrator at East Boulder Mine is fed with power from a dedicated substation which comprises a 15/20MVA transformer. Sufficient power is available for the mill operations. 14.2.2.7 Water Requirements The water requirement for the East Boulder Concentrator when operating is 1200gal per minute. The overall mine water balance is water positive, requiring disposal of treated water. The concentrator utilises a combination of TSF return water and treated underground water for processing purposes. 14.2.2.8 Process Materials Requirements As is the case for the Stillwater Concentrator, the process materials (reagents and steel balls) used in the East Boulder Concentrator are readily available and mostly sourced from credible suppliers located in the USA or North America. Reagents commonly used are potassium amyl xanthate, di-thiophosphate, carboxymethyl cellulose, methyl Isobutyl carbinol, and flocculant/coagulant. Hardened steel balls in 3- inch and 4-inch size are used in the primary grinding mills and are consumed at approximately 1lb/ton total. The Qualified Persons are satisfied that the measures in place in respect of the supply of process materials which should ensure security of supplies over the life of the operations. 0 25 50 75 100 125 150 175 200 225 250 73 74 75 76 77 78 79 80 81 82 83 84 85 86 87 88 89 90 91 92 FY 2 0 2 1 FY 2 0 2 2 FY 2 0 2 3 FY 2 0 2 4 FY 2 0 2 5 FY 2 0 2 6 FY 2 0 2 7 FY 2 0 2 8 FY 2 0 2 9 FY 2 0 3 0 FY 2 0 3 1 FY 2 0 3 2 FY 2 0 3 3 FY 2 0 3 4 FY 2 0 3 5 FY 2 0 3 6 FY 2 0 3 7 FY 2 0 3 8 FY 2 0 3 9 FY 2 0 4 0 FY 2 0 4 1 FY 2 0 4 2 FY 2 0 4 3 FY 2 0 4 4 FY 2 0 4 5 FY 2 0 4 6 FY 2 0 4 7 FY 2 0 4 8 FY 2 0 4 9 FY 2 0 5 0 FY 2 0 5 1 FY 2 0 5 2 FY 2 0 5 3 FY 2 0 5 4 FY 2 0 5 5 FY 2 0 5 6 FY 2 0 5 7 FY 2 0 5 8 FY 2 0 5 9 FY 2 0 6 0 FY 2 0 6 1 FY 2 0 6 2 FY 2 0 6 3 FY 2 0 6 4 FY 2 0 6 5 FY 2 0 6 6 FY 2 0 6 7 FY 2 0 6 8 FY 2 0 6 9 FY 2 0 7 0 2 E M e ta l P ro d u c e d ( k o z) 2 E R e c o v e ry ( % ) 2E Metal Produced 2E Recovery 170 Concentrator Process Control Sampling The concentrators at Stillwater and East Boulder Mines carry out routine sampling at various stages of the process to produce the data required for the management of the processes and accounting for the metals processed. The samples are analysed at the Sibanye-Stillwater-owned and operated laboratory located at the Columbus Metallurgical Complex. Concentrator feed samples for Stillwater and East Boulder Mines are not taken at either concentrator due to the inclusion of flash flotation and gravity recovery processes within the milling circuit. This precludes representative sampling of the concentrator head feed stream and, as a result, concentrator metallurgical recoveries and plant head feed grades (which are the basis for Mineral Reserve grades reported) are back-calculated from feed mass, concentrate mass and grade, and tailings grade. The concentrate and tailings samples are taken at both concentrators using automated linear falling stream sample cutters. The samples are produced in duplicate using two stage rotary samplers on the concentrate thickener feed pipeline, resulting in a 24-hour composite sample, which is representative of the concentrator final product. This composite sample is not used for accounting purposes as the concentrate sample from the smelter is used for this purpose. Linear falling stream sample cutters also produce the primary tailings samples, which are reduced using two stage rotary tailings samplers at both plants to produce duplicate samples from the final float tails streams. This tailings material sampling process results in the production of a duplicate daily composite sample for analysis. The final tails material is then pumped to the sand plant in the case of the concentrator at East Boulder Mine, and the tailings dewatering section for the concentrator at Stillwater Mine. The laboratory analytical process followed for the concentrator samples resembles that employed for the geological samples described in Section 8 although the concentrate samples are processed in a separate line dedicated for the receiving, preparation and analysis of these high-grade samples. The sampling equipment and the sampling regimes in place are adequate and suitable for the operations. Sampling equipment for feed sampling at both the Stillwater and East Boulder Concentrators consists of vezin rotary hammer and rotary splitter supplied by FLSmidth which is capable of up to 250 samples per hour. Equipment for float feed, tailings sampling and metal accounting consists of rotary vezin cross- stream cutters supplied by FLSmidth which are capable of up 360 samples per hour. Equipment for smelter feed accounting consists of two-stage rotary vezin cross-stream cutters supplied by FLSmidth and these are capable of up to 250 samples per hour. The concentrate sample analyses are subsequently verified via the automated sampling process of the concentrate at the smelter and analysis at the laboratory. Smelting and Refining Background The Columbus Metallurgical Complex was commissioned in 1990 and focused on smelting concentrate from Stillwater Mine. Initially, a 30-ton concentrate per day smelting facility was installed, which was

171 subsequently replaced with a 100-ton per day unit in 1999. Prior to 1990, concentrate from the concentrator at Stillwater Mine (the only concentrator at the time) was exported to Belgium for toll treatment and refining. The smelting operations have been expanded over the years, with the diversity of the operations at the complex also expanded to include base metal refining and PGM autocatalytic converter recycling operations. Currently, the smelter beneficiates the primary PGM concentrate from Stillwater and East Boulder Mines as well as PGM autocatalytic material sourced from third parties. There have been modest capacity upgrades of various units of the smelter and refinery as part of the Blitz Project. Smelter 14.3.2.1 Design and Equipment Specifications The Smelter at the Columbus Metallurgical Complex was commissioned in 1990 as a 30-ton of concentrate per operating day plant producing a copper and nickel matte containing PGMs. The Smelter has been through several upgrades to its current capacity to 185-ton of concentrate and used automotive catalysts per operating day. The current configuration consists of a concentrate dryer supplier by Carrier Vibrating Equipment Inc, two electric submerged arc furnaces supplied by Hatch Ltd, two top blown rotary converters supplied by Metso-Outotech, and an off-gas treatment facility consisting of Dynawave scrubbers supplied by Monsanto Enviro-Chem. The process flow and description is presented in Section 14.3.2.3. 14.3.2.2 Capacity The smelter comprises of two 150-ton per day primary smelting electric furnaces (Electric Furnace #1 and Electric Furnace #2), both of which can be configured to operate in a primary role or alternatively with Furnace #2 in a primary role and Furnace #1 in a slag cleaning role. PGM concentrate averaging 11% to 13% moisture is received from the concentrators in 30-ton side-tipping trucks. The process flow and description is presented in Section 14.3.2.3. The following areas of the smelter have recently been upgraded with a view to increasing tonnage throughput capacity in response to production increases at Stillwater and East Boulder Mines: Concentrate Receiving and Drying: A completely new concentrate receiving facility was designed and constructed. This allows delivery via side-tip trucks with the concentrate offloaded and rehandled into the feeding system via a dedicated front-end loader. A new fluid bed dryer has also been installed with a nominal capacity of approximately 320 tons per day. Both concentrate handling and drying facilities were commissioned in early FY2021; Smelter and Gas Cleaning: Both Electric Furnace 1 and Electric Furnace 2 now operate in primary smelting duty at an installed power of 7.5MW each, with a combined feed capacity of 185 tons per day of dried concentrate. The gas handling facility did not require any upgrades to accommodate the increased furnace capacity and has demonstrated adequate capacity. Both Electrical Furnaces were supplied by Hatch and have been rebuilt since original install. Electric Furnace 1 was rebuilt in FY2021, and Electric Furnace 2 was rebuilt in FY2023; Granulation: The slag handling methodology is such that top blown rotary converter slag and furnace slag materials are treated separately. While the furnace slag is cooled and returned to the Stillwater or East Boulder Mine Concentrators for re-milling, the converter slag is granulated at the smelter. This granulation facility has been redesigned for upgrade. The top blown rotary 172 converter matte dryer was installed during FY2021 and the electric furnace matte/top blown rotary converter slag dryer was installed in early FY2022. Both dryers were supplied by Carrier Vibrating Equipment, Inc; Top Blown Rotary Converters: The existing two top blown rotary converters were supplied by Metso-Outotech and have been upgraded to larger drums, which has resulted in larger charge capacity and longer blowing time. This has also increased overall converting capacity by reducing converter downtimes. The converter upgrades were completed during FY2022; and Regeneration: Sulphur dioxide off gas is captured by way of 2 primary Dynawave scrubbers and a secondary Dynawave scrubber supplied by Monsanto Enviro-Chem. Additionally, to maintain the Columbus Metallurgical Complex’s permitted sulphur dioxide discharge level in the final atmospheric discharge gas, an additional sodium hydroxide regeneration train was installed. This unit modifies the scrubber liquor with the addition of further NaOH and subsequent addition of hydrated lime, which precipitates a gypsum product (CaSO4.2H2O), which is sold as an agricultural soil modifier and regenerates the NaOH for reuse in the scrubber circuits. The additional caustic regeneration train is a duplicate of the existing trains and is fully operational. 14.3.2.3 Process Description The simplified process flow block diagram for the smelter processes is presented in Figure 71. The concentrate bins delivered to the smelter are sampled, where after the concentrate is discharged via an elevator system into a fluidised bed dryer. Natural gas is available at the Columbus Metallurgical Complex site as a piped utility and, as such, is used wherever possible as a heating source. The dryer is thus natural gas fired and reduces the concentrate moisture to below 1%. Used automotive catalysts, which average 70oz 2E per ton, are combined with the new concentrate feed after the dryer. The treatment and processing of recycle materials is addressed in Section 21.1. High-temperature furnace fume and process gases from the electric furnace roof extraction system enter a primary bag house, whilst the lower temperature gas and particulates from the tapping, converting and granulation processes enter a secondary baghouse. The baghouses use high- performance Gore-Tex coated membrane bags to capture the particulates, which are recycled back to the furnace feed hoppers via a pneumatic conveying system. Matte produced from the arc furnaces is granulated and then charged into the top-blown rotary converter (TBRC), where the sulphur and iron components are oxidised. The slag from this process is recycled to the furnaces. The matte typically contains 350oz 2E per ton to 700oz 2E per ton, 28% to 30% Cu, 40% to 42% Ni, 20% to 22% S, 2% iron (Fe) and the balance comprising cobalt (Co), gold (Au), silver (Ag), Rh, tellurium (Te) and selenium (Se). 173 Figure 71: A Simplified Block Flow Diagram of the Smelter 14.3.2.4 Process Control Sampling All concentrate transfers to the smelter from the two concentrators are sampled using a pipe sampler on a grid pattern prior to offloading. A final composite sample per shipment with an ultimate sample mass of approximately 10lbs is then transported to the in-house laboratory. This sample provides the definitive analysis for the concentrate from the concentrators, which is used in the metallurgical accounting process. All catalyst material received at the smelter is sampled and prepared separately from the concentrate. The material is either sampled using a pipe sampler or TEMA sampler. These samples are then transported to the in-house laboratory. The sample provides definitive analysis for the catalyst from recycled material, which is used in the metallurgical accounting process. Converter matte, once granulated, is the smelter final product and is sampled at the smelter by a falling stream sampler (supplied by Salina Vortex Corp.) at the granulator. A primary sample is taken, which is reduced to approximately 2lb via a twelve-point rotary splitter (supplied by Eriez Manufacturing Co.) before being manually delivered as a duplicate sample to the in-house laboratory. This sample provides the definitive analysis for the convertor matte from the smelter, which is used in the metallurgical accounting process. The laboratory analysis process flow for smelter samples resembles that for the geological samples described in Section 8, although the converter matte and concentrate samples are processed in a separate line dedicated for the receiving, preparation and analysis of high-grade samples. Other samples produced by the smelter for analysis at the analytical laboratory, which are utilised for internal accounting purposes, are as follows: Furnace slag: spoon samples are taken during the tapping process and composited daily; 174 Converter slag: converter slag is grab sampled from each bin produced for recycle back to the furnaces, and composited on a daily and weekly basis; Furnace matte: furnace matte is grab sampled from each bin produced and composited on a daily and weekly basis; and Gypsum product: gypsum product is pipe-sampled from each weekly composite sample container bin resulting in a bulk sample, which is dried and incrementally split for analysis of the final aliquot. The sampling equipment and the sampling regimes in place at the smelter are adequate and suitable for the operations. 14.3.2.5 Production Plan The recent history and budget operational parameters for the smelter plant have been reviewed and the key variables are presented in Table 45, Figure 72 and Figure 73. The FY2021, FY2022 and FY2023 data presented reflects the actual annual performance whilst the FY2024 to FY2069 data represents the current budget targets. Metallurgical efficiencies projected have also been sustainably obtained historically and are thus reasonable budget targets. The increases in smelter operational duty planned are visible whilst the other key variables such as smelter first pass recovery and recycle tons treated remain at levels previously achieved. The increases in concentrate feed will be achieved with both electric furnaces operating in primary duty, whilst the implemented upgrades to concentrate receiving and drying and the larger converter drums will match this capacity. Table 45: Smelter Historical and Budget Operational Data FY2021 FY2022 FY2023 FY2024 FY2025 FY2026 FY2027 FY2028 FY2029 FY2030 FY2031 FY2032 FY2033 FY2034 FY2035 FY2036 FY2037 Smelter Concentrate Feed tons 40 393 34 075 35 483 38 384 38 328 41 895 44 543 48 087 50 059 50 615 50 735 50 812 50 759 50 284 51 429 50 538 50 732 Smelter Recycle Feed tons 9 561 7 579 4 245 4 392 7 300 9 904 11 193 12 166 11 968 12 793 11 297 11 010 11 113 10 157 10 171 8 853 8 767 Converter Matte Produced tons 2 031 1 469 1 445 1 744 1 723 1 985 2 243 2 431 2 398 2 564 2 264 2 200 2 227 2 035 2 038 1 769 1 757 Smelter 1st Pass Recovery % 97.37 97.85 97.97 97.60 97.20 97.02 96.92 96.91 96.94 96.90 96.96 96.99 96.99 97.04 97.06 97.13 97.15 Total 2E Recovered oz 1 257 205 971 139 725 236 769 015 949 220 1 210 113 1 371 232 1 493 225 1 514 986 1 580 647 1 495 409 1 470 477 1 470 217 1 401 984 1 407 667 1 310 835 1 302 144 FY2038 FY2039 FY2040 FY2041 FY2042 FY2043 FY2044 FY2045 FY2046 FY2047 FY2048 FY2049 FY2050 FY2051 FY2052 FY2053 FY2054 Smelter Concentrate Feed tons 50 625 51 402 51 405 51 552 51 943 52 526 52 244 52 301 52 046 51 723 51 516 51 215 49 492 51 119 51 379 48 957 30 808 Smelter Recycle Feed tons 9 872 10 134 10 049 10 190 10 341 10 204 9 839 9 762 8 416 8 346 8 452 9 911 9 541 10 024 10 146 9 014 6 382 Converter Matte Produced tons 1 978 2 031 2 008 2 042 2 072 2 045 1 966 1 956 1 686 1 672 1 689 1 986 1 912 2 009 2 028 1 806 1 279 Smelter 1st Pass Recovery % 97.08 97.09 97.10 97.11 97.11 97.11 97.12 97.14 97.25 97.24 97.24 97.10 97.10 97.03 97.06 97.01 97.02 Total 2E Recovered oz 1 370 043 1 389 648 1 382 631 1 379 113 1 389 496 1 399 239 1 378 052 1 369 177 1 263 947 1 258 208 1 260 214 1 374 558 1 324 595 1 418 894 1 405 731 1 360 666 871 144 FY2055 FY2056 FY2057 FY2058 FY2059 FY2060 FY2061 FY2062 FY2063 FY2064 FY2065 FY2066 FY2067 FY2068 FY2069 Smelter Concentrate Feed tons 16 256 17 045 18 160 17 203 17 648 16 963 17 106 17 047 16 557 17 672 18 213 18 663 18 387 18 870 10 239 Smelter Recycle Feed tons 4 115 4 355 4 626 4 388 4 606 4 589 4 606 4 543 4 515 4 633 4 593 4 615 4 543 4 603 2 615 Converter Matte Produced tons 825 870 927 879 923 917 923 910 905 926 920 925 910 920 524 Smelter 1st Pass Recovery % 97.05 97.03 97.04 97.03 97.00 96.95 96.95 96.97 96.93 96.99 97.05 97.08 97.08 97.11 97.03 Total 2E Recovered oz 469 982 496 764 528 352 501 105 526 010 523 405 525 887 518 733 515 457 528 453 524 621 527 112 518 880 525 252 298 600 Budget Budget Budget Parameter Unit Parameter Unit Actual Parameter Unit

175 Figure 72: Smelter Actual and Forecast LoM Operational Throughput Figure 73: Smelter LoM Operational Performance, Actual and Forecast 0 250 500 750 1 000 1 250 1 500 1 750 2 000 2 250 2 500 2 750 0 5 000 10 000 15 000 20 000 25 000 30 000 35 000 40 000 45 000 50 000 55 000 60 000 65 000 70 000 FY 2 0 2 1 FY 2 0 2 2 FY 2 0 2 3 FY 2 0 2 4 FY 2 0 2 5 FY 2 0 2 6 FY 2 0 2 7 FY 2 0 2 8 FY 2 0 2 9 FY 2 0 3 0 FY 2 0 3 1 FY 2 0 3 2 FY 2 0 3 3 FY 2 0 3 4 FY 2 0 3 5 FY 2 0 3 6 FY 2 0 3 7 FY 2 0 3 8 FY 2 0 3 9 FY 2 0 4 0 FY 2 0 4 1 FY 2 0 4 2 FY 2 0 4 3 FY 2 0 4 4 FY 2 0 4 5 FY 2 0 4 6 FY 2 0 4 7 FY 2 0 4 8 FY 2 0 4 9 FY 2 0 5 0 FY 2 0 5 1 FY 2 0 5 2 FY 2 0 5 3 FY 2 0 5 4 FY 2 0 5 5 FY 2 0 5 6 FY 2 0 5 7 FY 2 0 5 8 FY 2 0 5 9 FY 2 0 6 0 FY 2 0 6 1 FY 2 0 6 2 FY 2 0 6 3 FY 2 0 6 4 FY 2 0 6 5 FY 2 0 6 6 FY 2 0 6 7 FY 2 0 6 8 FY 2 0 6 9 FY 2 0 7 0 M a tt e P ro d u c e d ( to n s) Fe e d ( to n s) Smelter Concentrate Feed Smelter Recycle Feed Converter Matte Produced 0 200 400 600 800 1 000 1 200 1 400 1 600 1 800 82 83 84 85 86 87 88 89 90 91 92 93 94 95 96 97 98 99 100 FY 2 0 2 1 FY 2 0 2 3 FY 2 0 2 5 FY 2 0 2 7 FY 2 0 2 9 FY 2 0 3 1 FY 2 0 3 3 FY 2 0 3 5 FY 2 0 3 7 FY 2 0 3 9 FY 2 0 4 1 FY 2 0 4 3 FY 2 0 4 5 FY 2 0 4 7 FY 2 0 4 9 FY 2 0 5 1 FY 2 0 5 3 FY 2 0 5 5 FY 2 0 5 7 FY 2 0 5 9 FY 2 0 6 1 FY 2 0 6 3 FY 2 0 6 5 FY 2 0 6 7 FY 2 0 6 9 2 E R e c o v e re d ( k o z) 2 E R e c o v e ry ( % ) New Feed 2E Recovered Recycle Feed 2E Recovered Smelter 1st Pass Recovery 176 14.3.2.6 Manpower Requirements The budgeted total smelter manpower complement is 96 consisting of 43 hourly and 14 salaried employees in operations and 28 hourly and 11 salaried employees in maintenance. 14.3.2.7 Energy Requirements The energy requirement for the smelter is approximately 11MW. Power is supplied to the Columbus Metallurgical Complex via a dedicated switching station containing two transformers. The power supply is adequate for both the smelting and base metal refining operations. 14.3.2.8 Water Requirements The water requirement for the smelter is 21Mgals/yr. The entire Columbus Metallurgical Complex is water neutral, with sufficient recycle and storage facilities included. The water supply is adequate for both the smelting and base metal refining operations. 14.3.2.9 Flux and Other Requirements The process materials (e.g., flux) used in the smelting operations are readily available. Typical smelter process materials are catalyst (recycle material), limestone, taconite, quick lime, oxygen, hydrated lime, caustic, and flocculant. Most sources are domestic in nature and the overseas sources have been studied intensely to evaluate secondary and tertiary sources in case of supply chain interruption from the primary source. The Qualified Persons are satisfied with security of supplies in respect of process materials for the smelting operations over the life of operations. Base Metal Refinery 14.3.3.1 Design and Equipment Specifications The Base Metals Refinery (BMR) at the Columbus Metallurgical Complex was commissioned in 1996 as a 660 pounds of smelter matte per hour plant producing PGM filter cake. Since commissioning, the BMR has been upgraded to increase capacity the current level of 1 300 pounds of smelter matte per hour. The current configuration consists of the nickel atmospheric leach circuit, a copper dissolve autoclave designed by Hatch Ltd, a nickel sulfate crystallizer supplied by Swenson Technology Inc, a copper electrowinning plant, and two polish leach autoclaves designed by Bateman Engineering. The detailed process flow and description is presented in Section 14.3.3.3. 14.3.3.2 Capacity The BMR facility was installed in 1996 at a nameplate capacity of 660lbs per hour but has a current capacity of more than 1 200lb per hour of granulated matte due to some process expansions – primarily a result of process optimisation and improvement. The BMR currently operates on two 12-hour shifts continuously from Monday morning to Thursday afternoon (equivalent to 80 hours per week or a utilisation of 47.6%). The copper electrowinning circuit at the facility, which operates continuously, was 177 expanded in FY2021 by adding six cells to eliminate a bottleneck that occurred historically in the BMR process. The expanded processing capacity can produce 750 tons per year of copper, with spare capacity remaining. The BMR process flow and description is presented in Section 14.3.3.3. The Qualified Person Is also of the view that, with the current matte capacity exceeding 1 200lb per hour and the expanded copper electrowinning circuit, the forecast matte volumes and nickel processing capacity can be accommodated through the existing operational schedule, with occasional overtime to cover any variance. 14.3.3.3 Process Description The granulated converter matte product is weighed upon receipt at the BMR facility. The matte is milled and leached with sulphuric acid and oxygen at atmospheric conditions to remove nickel as a sulphate crystal product. The remaining solids from the nickel leach are then leached with sulphuric acid and oxygen under pressurized conditions to dissolve copper with some selenium (Se) and tellurium (Te) dissolved in the process. The latter two metals are cemented out of solution, leaving the copper solution for electrowinning. The solids remaining after copper dissolution forms the PGM filter cake, which is washed, filtered and dried. The simplified process flow block diagram for the BMR processes is presented in Figure 74. The final product (filter cake) is despatched to Johnson Matthey Company (Johnson Matthey) for further separation and refining. 178 Figure 74: A Simplified Block Flow Diagram of the Base Metal Refinery 14.3.3.4 Process Control Sampling The converter matte bins received from the smelter at the BMR are weighed and the mass becomes the final value used in the metal accounting system. The analysis used in the accounting system originates from the final smelter sample. BMR products are all sampled within the production process and the products are analysed for quality control purposes only as follows: NiSO4 crystals: A primary sample is taken from the bagging process via a rotary splitter, which is reduced further for final analysis; Copper cathode: This is sampled by drilling of the cathode plate, digested and analysed by ICP spectrometry for the copper turnings produced, and the analysis is used as the dispatch analysis for the cathode product; and PGM filter cake: This is the final BMR product shipped to Johnson Matthey for further refining. This material is sampled at the final product dryer by a rotary splitter and is then sub-sampled. Duplicate samples are produced, and the analytical results of these samples become the invoice analyses for the shipments.

179 The invoiced analysis is checked by Johnson Matthey on receipt, in addition to which there is an umpire process, which is followed for variances greater than those allowed in the contract. The in-house laboratory reports quarterly on the correlations achieved between analyses from Johnson Matthey, in- house and umpire laboratories (where required) on a per element basis. The BMR sample analysis process also resembles that for the geological samples described in Section 8 although the filter cake, converter matte and concentrate samples are processed in a separate line dedicated for the receiving, preparation and analysis of high-grade samples. The main sampling point in the BMR is for the PGM filtercake. This process utilizes a rotary splitter supplied by Verder Scientific, and the sampling equipment and the sampling regimes in place at the BMR are adequate and suitable for the operations 14.3.3.5 Manpower Requirements The total BMR manpower complement is 34 consisting of 16 hourly and 6 salaried employees in operations and 9 hourly and 3 salaried employees in maintenance. 14.3.3.6 Energy Requirements The energy requirement for the BMR is approximately 1MW. Power is supplied to the Columbus Metallurgical Complex via a dedicated switching station containing two transformers. The power supply is adequate for all base metal refining operations. 14.3.3.7 Water Requirements The water requirement for the BMR is approximately 9Mgals/yr. The entire Columbus Metallurgical Complex is water neutral, with sufficient recycle and storage facilities included. The water supply is adequate for all base metal refining operations 14.3.3.8 Process Materials Requirements The process materials (reagents) used in the BMR are also readily available and sourced from credible domestic suppliers. Typical reagents used are sulfuric acid, oxygen, chopped recycled copper wire, EW smoothing agent (polyacrylic acid), and flocculant. The Qualified Persons are satisfied that the measures in place in respect of the supply of process materials which should ensure security of supplies over the life of the operations. 14.3.3.9 Production Plan The recent history and budget operational parameters for the BMR have been reviewed and the key variables are presented in Table 46, Figure 75 and Figure 76. The FY2021, FY2022, and FY2023 data presented reflects the actual annual performance whilst the FY2024 to FY2069 data presents the current LoM budget targets. The Qualified Person is of the view that the current operational methods and 180 capacities are adequate. Furthermore, the metallurgical recoveries projected have also been sustainably obtained historically and are reasonable budget targets. Table 46: Base Metal Refinery Historical and Forecast LoM Operational Data Figure 75: Base Metal Refinery Actual and Forecast LoM Operational Throughput and Base Metals Recovered FY2021 FY2022 FY2023 FY2024 FY2025 FY2026 FY2027 FY2028 FY2029 FY2030 FY2031 FY2032 FY2033 FY2034 FY2035 FY2036 FY2037 BMR Matte Feed tons 2 043 1 469 1 435 1 744 1 723 1 985 2 243 2 431 2 398 2 564 2 264 2 200 2 227 2 035 2 038 1 769 1 757 Cu Produced tons 551 419 390 479 472 546 624 680 663 720 621 602 608 569 570 479 474 Ni Produced tons 900 669 630 755 749 859 963 1 040 1 034 1 094 982 956 968 872 873 773 770 Total 2E Recovered oz 1 255 404 983 922 729 683 768 253 950 661 1 207 693 1 368 490 1 490 238 1 511 956 1 577 486 1 492 418 1 467 536 1 467 277 1 399 180 1 404 851 1 308 213 1 299 540 PGM Recovery % 99.80 99.80 99.80 99.80 99.80 99.80 99.80 99.80 99.80 99.80 99.80 99.80 99.80 99.80 99.80 99.80 99.80 FY2038 FY2039 FY2040 FY2041 FY2042 FY2043 FY2044 FY2045 FY2046 FY2047 FY2048 FY2049 FY2050 FY2051 FY2052 FY2053 FY2054 BMR Matte Feed tons 1 978 2 031 2 008 2 042 2 072 2 045 1 966 1 956 1 686 1 672 1 689 1 986 1 912 2 009 2 028 1 806 1 279 Cu Produced tons 550 567 560 569 578 571 547 543 440 436 444 553 530 562 568 505 372 Ni Produced tons 850 871 861 876 888 876 845 841 755 749 752 853 823 859 867 773 533 Total 2E Recovered oz 1 367 303 1 386 869 1 379 865 1 376 355 1 386 717 1 396 441 1 375 295 1 366 438 1 261 419 1 255 691 1 257 693 1 371 808 1 321 946 1 416 056 1 402 920 1 357 945 869 402 PGM Recovery % 99.80 99.80 99.80 99.80 99.80 99.80 99.80 99.80 99.80 99.80 99.80 99.80 99.80 99.80 99.80 99.80 99.80 FY2055 FY2056 FY2057 FY2058 FY2059 FY2060 FY2061 FY2062 FY2063 FY2064 FY2065 FY2066 FY2067 FY2068 FY2069 BMR Matte Feed tons 825 870 927 879 923 917 923 910 905 926 920 925 910 920 524 Cu Produced tons 252 266 284 269 283 281 283 279 277 283 282 283 279 282 160 Ni Produced tons 330 348 371 352 370 367 370 365 362 371 369 370 365 368 210 Total 2E Recovered oz 469 042 495 771 527 295 500 103 524 958 522 358 524 835 517 696 514 426 527 396 523 572 526 058 517 842 524 202 298 003 PGM Recovery % 99.80 99.80 99.80 99.80 99.80 99.80 99.80 99.80 99.80 99.80 99.80 99.80 99.80 99.80 99.80 Parameter Unit Parameter Unit Actual Parameter Unit Budget Budget Budget 0 100 200 300 400 500 600 700 800 900 1 000 1 100 1 200 0 200 400 600 800 1 000 1 200 1 400 1 600 1 800 2 000 2 200 2 400 2 600 2 800 FY 2 0 2 1 FY 2 0 2 2 FY 2 0 2 3 FY 2 0 2 4 FY 2 0 2 5 FY 2 0 2 6 FY 2 0 2 7 FY 2 0 2 8 FY 2 0 2 9 FY 2 0 3 0 FY 2 0 3 1 FY 2 0 3 2 FY 2 0 3 3 FY 2 0 3 4 FY 2 0 3 5 FY 2 0 3 6 FY 2 0 3 7 FY 2 0 3 8 FY 2 0 3 9 FY 2 0 4 0 FY 2 0 4 1 FY 2 0 4 2 FY 2 0 4 3 FY 2 0 4 4 FY 2 0 4 5 FY 2 0 4 6 FY 2 0 4 7 FY 2 0 4 8 FY 2 0 4 9 FY 2 0 5 0 FY 2 0 5 1 FY 2 0 5 2 FY 2 0 5 3 FY 2 0 5 4 FY 2 0 5 5 FY 2 0 5 6 FY 2 0 5 7 FY 2 0 5 8 FY 2 0 5 9 FY 2 0 6 0 FY 2 0 6 1 FY 2 0 6 2 FY 2 0 6 3 FY 2 0 6 4 FY 2 0 6 5 FY 2 0 6 6 FY 2 0 6 7 FY 2 0 6 8 FY 2 0 6 9 FY 2 0 7 0 M e ta l P ro d u c e d ( to n s) B M R M a tt e F e e d ( to n s) BMR Matte Feed Cu Produced Ni Produced 181 Figure 76: Base Metal Refinery Actual and Forecast LoM Operational Performance PGM Prill Splits Sibanye-Stillwater measures and reports metal prill splits as a ratio of palladium to platinum in the various intermediate products from the individual operations. The current ratios based on data for the FY2023 period have been reviewed by the Qualified Person. The Pd and Pt prill split percentages, based on the Pd:Pt ratio in concentrate resulting from the processing of ore from Stillwater and Easter Boulder Mines, are presented in Table 47. These have also been utilised for business and LoM planning. Table 47: Summary of Pt and Pd Prill Split Data Mine Pd: Pt Ratio Prill Split FY2023 Pt Pd Stillwater Mine 3.51:1 22.17% 77.83% East Boulder Mine 3.60:1 21.73% 78.27% Processing Logistics Concentrate from both the Stillwater and East Boulder Concentrators, with moisture content of 11% to 13%, is trucked via side-tipper bulk trucks to the smelter. Travel time for the concentrate truck from East Boulder Mine to the smelter by road is approximately two to three hours but the travel time for the concentrate truck from Stillwater Mine to the smelter is approximately one and a half hours. Following tube sampling for moisture and initial assays, the material is introduced into a fluidised bed, natural gas dryer that reduces moisture to less than 1%. The dried concentrate is conveyed to a feed storage bin and sampled in duplicate. 0 100 200 300 400 500 600 700 800 900 1 000 1 100 1 200 1 300 1 400 1 500 1 600 94.0 94.5 95.0 95.5 96.0 96.5 97.0 97.5 98.0 98.5 99.0 99.5 100.0 FY 2 0 2 1 FY 2 0 2 2 FY 2 0 2 3 FY 2 0 2 4 FY 2 0 2 5 FY 2 0 2 6 FY 2 0 2 7 FY 2 0 2 8 FY 2 0 2 9 FY 2 0 3 0 FY 2 0 3 1 FY 2 0 3 2 FY 2 0 3 3 FY 2 0 3 4 FY 2 0 3 5 FY 2 0 3 6 FY 2 0 3 7 FY 2 0 3 8 FY 2 0 3 9 FY 2 0 4 0 FY 2 0 4 1 FY 2 0 4 2 FY 2 0 4 3 FY 2 0 4 4 FY 2 0 4 5 FY 2 0 4 6 FY 2 0 4 7 FY 2 0 4 8 FY 2 0 4 9 FY 2 0 5 0 FY 2 0 5 1 FY 2 0 5 2 FY 2 0 5 3 FY 2 0 5 4 FY 2 0 5 5 FY 2 0 5 6 FY 2 0 5 7 FY 2 0 5 8 FY 2 0 5 9 FY 2 0 6 0 FY 2 0 6 1 FY 2 0 6 2 FY 2 0 6 3 FY 2 0 6 4 FY 2 0 6 5 FY 2 0 6 6 FY 2 0 6 7 FY 2 0 6 8 FY 2 0 6 9 FY 2 0 7 0 2 E R e c o v e re d ( k o z) 2 E R e c o v e ry ( % ) Total 2E Recovered PGM Recovery 182 Recycled automotive catalysts and other PGM-bearing materials, averaging 70oz 2E per ton, constitute a separate source of smelter feed. This is delivered to the smelter by clients in 3ft cube bags and boxes. This material is pulverised, sorted and sampled in the same manner prior to smelting to ensure client custom metal is accounted separately. All slag from the smelter as well as from the furnace and Top Blown Rotary Converter used lining bricks is sampled to quantify residual precious metals and returned to both the Stillwater and East Boulder Concentrators. The slag is transported via the return haul for the side-tipper trucks for re-milling to ensure residual metals are returned to the value stream. The residual metals are also accounted for in terms of the concentrator recovery performance measurement.

183 INFRASTRUCTURE Stillwater Mine Complex Concentrator Infrastructure The processing plant infrastructure at Stillwater Mine was built in 1987 and is in a good operational condition. Historical budgets have provided for adequate sustaining and project capital for maintenance and upgrades of plant infrastructure to ensure sustained performance at the required capacities. The planned maintenance of the Stillwater Concentrator follows the JD Edwards Maintenance Control system. Power supply to the concentrator plant is described in Section 15.1.4. As the Stillwater Concentrator is being upgraded to accommodate the increased capacity resulting from the Blitz expansion (Stillwater East Section), the power supply has also been upgraded accordingly. The concentrate handling thickener building and concentrate handling loadout building were completed and commissioned in FY2021. Several additional buildings are planned as part of the Concentrator Expansion to be completed in F2022 and these include the following: Hertzler Overflow (O/F) tank and pump building; Hertzler Motor Control Centre (MCC) expansion building; 5150 process water expansion building; Ore handling building; and Grinding building. Tailings Storage Facilities The TSFs for Stillwater Mine are at the mature stage. Stillwater Mine has moved the production deposition from the original Nye TSF to the Hertzler TSF. The Hertzler TSF is permitted to Stage 3 (equivalent to a height of 5 030ftmamsl), after which additional permitting will be required following a revised design. The current plan is to increase the capacity of the Hertzler TSF with new, additional tailings storage (Cells 4 and 5), to accommodate the increased production rate arising following additional material from the Stillwater East Section. The TSF is inspected by independent consultants on an annual basis, with Knight- Piésold being the defined Engineer-of-Record. The TSFs at the Stillwater Mine comprises two slimes impoundments, namely the Nye TSF (no longer in full- time use) and the Hertzler TSF (current primary storage). The Nye TSF was used from the start of the mine until 2002 when the Hertzler TSF was commissioned, and it is currently undergoing capping for closure by the end of FY2024. The Hertzler TSF is currently permitted to an elevation of 5 030ft including freeboard and supernatant pond, which is the maximum extent of the current Stage 3 embankment raise. Concentrator tailings are sampled and pumped to a paste plant alongside the Nye TSF located to the southwest of the concentrator. The paste plant, which is used on a limited basis, operates as a staging point for whole tailings slurry. The tailings may be routed from the paste plant either to the 5150 Level underground sand plant or to the Hertzler Pump House, from where it can be routed to either of the 184 other sand plants or the Hertzler TSF. Tailings can also be routed to the Nye TSF from the concentrator, the paste plant or the pump house, if required. Whole tailings material is classified at the underground sand plants into coarse sand and slimes fractions, the sand remains underground and is pumped into stopes for backfilling purposes, whilst the slimes fraction is pumped back to the pump house. The slime is then pumped via two eight-inch pipelines to the Hertzler TSF for deposition. Deposition on the Hertzler TSF is via periodic rotational discharge of tailings slurry around the perimeter of the facility using a group of spigots. Once a localised tailings beach has formed, deposition is transferred to another group of spigots at a different location. Water reclamation is achieved via two inclined reclaim pumps located at the south end of the TSF, which return process water to the concentrator. The adjacent Land Application and Disposal (LAD) pond to the west of the Hertzler Tailings Storage Facility is used to manage treated mine water volumes. The TSF is geomembrane lined, and the liner is routinely inspected by the Engineer of Record and an Independent Tailings Review Board, where possible. Basin underdrain and seepage measurement is performed and monitored via vibrating wire piezometers, whilst embankment crest-mounted survey monuments are used to measure slope slippage or movement. Additional inclinometers are installed around the base of the impoundment to monitor deeper ground movement and displacement. The basin underdrain pore pressures are monitored on a weekly basis via the piezometers, and these respond quickly to changes in the basin underdrain pumping rate. This results in changes in the tailings mass consolidation and hence maximises storage availability and assists in long-term closure planning. The concentrator performs weekly, monthly and quarterly TSF inspections and monitoring per its standard procedures, which are reviewed as part of the annual independent Engineer of Record inspection of the TSF performed by Knight-Piésold of Canada. The inspections and monitoring are required by the 2015 Montana Metal Mine Reclamation Act (MCA). The most recent inspection was performed in September 2023, with a review period from October 2022 to September 2023. No material issues were identified, but a corrective action plan for the issues which were identified was developed and submitted to the Montana Department of Environmental Quality (MDEQ) as required and in compliance with the MCA. The Nye TSF, located immediately to the south of the mining and processing complex, was decommissioned as the primary storage facility in 2001 but is used for emergency tailings storage and water management purposes. Supernatant water is recycled to the concentrator as process water via an inclined retractable pump at the north end of the facility. Survey beacons are in place and are routinely measured for slope stability and slippage. The most recent inspection of the TSF by Knight- Piésold raised no material findings. Knight-Piésold has been retained to develop a closure and rehabilitation plan for the Nye TSF. Capping of the Nye TSF commenced in late FY2018 and is expected to be completed by FY2024. 185 Stage 3 of the Hertzler TSF was completed in 2015 and filling of Stage 3 is currently underway. As part of the annual inspection of the Hertzler TSF, Knight-Piésold calculates a projected fill rate of the current and planned TSF capacity as an elevation above mean sea level by year. Knight-Piésold’s latest TSF filling calculations contained in the 2023 Annual Inspection Report estimates the Stage 3 limit of 5 030ftmsl to be reached (based on pond elevation) by April 2031(Figure 77) at the envisaged RoM ore production rates. The Qualified Person is satisfied with Knight-Piésold’s estimate of the Stage 3 capacity of Stage 3. Figure 77: Hertzler TSF Knight-Piésold Calculated Elevation Profile Stage 3 is currently the maximum permitted height of the Hertzler TSF and, as a result, operation of the TSF beyond this stage will require the design and approval of a Stage 4. A Plan of Operations Amendment for the Stage 4 and Stage 5 TSF expansions has been prepared and was submitted for agency approval in April 2023. Hertzler TSF expansion involves an initial capital expenditure amount of $6.5 million for studies over the FY2024 to FY2026 period and follow up expenditure of $135.4 million for detailed design and construction between FY2029 and FY2031, which have been budgeted for as discussed in Section 18.2.2.4. The Qualified Person deems the quantum of the capital budget to be sufficient for the implementation of the Hertzler TSF expansion. Sibanye-Stillwater has indicated to the Qualified Person that there are no 186 apparent impediments anticipated that will prevent the approval of the Hertzler TSF expansion. However, if the approval is declined and a new TSF is required, a timeframe of approximately three to five years for environmental permitting processes and two years for construction would be required. In addition, a higher capital budget provision than the current provision may be required. East Waste Rock Storage Facility The current East Waste Rock Storage Facility at Stillwater Mine is projected to reach capacity in Q4 FY2030 in conjunction with waste rock capping and closure of the Nye TSF. As a result, an expansion of the East Waste Rock Storage Facility has been designed, proposed, and included in the Amendment 14 Operating Permit application for Stillwater Mine. The Amendment 14 application was submitted in November 2023 and will be subject to an Environmental Impact Statement review and associated State and Federal permitting. It is expected that the Record of Decision and Permit will be issued no later than FY2028. Construction of the expansion area is currently targeted to begin in FY2029 with completion and ability to accept waste rock storage starting in FY2031. The project involves approximately $20 million of capital expenditure. The East Side Waste Rock Storage Facility expansion includes a 56-acre extension to the northeast along with a 200ft increase in the height of the overall facility. Based on current LoM plan, the facility is designed to contain 35 years of waste rock storage. Power Stillwater Mine receives power from North West Energy from a substation located adjacent to the mine site. It receives power from the grid via two sources as follows: 100kV line via the Columbus-Rapelje Auto-substation; and 100kV line via Chrome Junction Substation. The powerline from Chrome Junction to Stillwater Mine is a radial feed at 100kV and feeds three small substations belonging to Beartooth Electric. The Nye REA Tap substation feeds the Hertzler TSF. The mine site has two main substations, namely the West Substation and East Substation, both connected to North West Energy’s substation adjacent to the mine via a 100KV line. The West Substation is owned and maintained by North West Energy and feeds most of the existing mine site including the concentrator. The East Substation is owned and maintained by Stillwater Mine and was installed as part of the Blitz Project to power the Stillwater East Section. The actual power demand loads for Stillwater Mine are as follows: West Substation: 20MW at 0.92 Power Factor, with current load capacity of approximately 109% without fans and 82% with fans; East Substation: 12.5MW at 0.88 Power Factor; and Monthly maximum peak for the site: 32.5MW.

187 Power into Stillwater Mine is reticulated from the West Substation through three incoming lines. Incoming line #1 distributes to the following: Upper West Feeder; 5000 West Portal Feeder; West Compressor/Surface Feeder; Vertical Mill; and Skip Hoist and Shaft feeder. Incoming Line #2 feeds to the following: Main Shaft Feeder A for mining operations; Main Shaft Feeder B for mining operations; Man hoist; Concentrator 480V loads; WFVR fans; and Auxiliary services including workshops and hoist room. Incoming line #3 feeds the following: Ball and Sag mill; 480v transformer #1; and 480v Transformer #2. Stillwater Mine has a 750kVA emergency generator to power the cage hoist and provide emergency power for the phones and other small critical loads. All underground transformers are dry-cooled, eliminating the risk of oil leakage and/or fire. In addition, these transformers are skid mounted, installed in concreted cubbies, well- demarcated and supplied with lighting. Stillwater Mine has a detailed inventory of all underground switchgear, controller and transformers managed through the JD Edwards Management System. Bulk Water 15.1.5.1 Water Supply The bulk water supply for the Stillwater Mine is a mix of fresh make-up water from supply wells and recycled mine water. The overall water balance is positive meaning that water disposal is required. Treatment and disposal of surplus water are discussed in Section 15.1.5.2. The onsite water supply wells provide potable water for the mine, make-up water for reagent mixing, and cooling water to some systems (e.g., lube system cooling). Onsite, the water is reticulated to various sites through a network of pipelines (distribution system). The two existing wells and associated distribution system is adequate for the Stillwater Mine ramp up production requirements. Water consumption from the wells is approximately 110gal per minute. The Qualified Person recognises that the net positive water balance at the site is adequate for ongoing operations. 188 15.1.5.2 Water Treatment The water treatment system at Stillwater Mine treats and disposes impacted water from the underground mining operations. Impacted mine water is first clarified before a portion is reused as mine service water while the remaining water continues to the biological treatment process to remove nitrates and is then disposed of by land application or infiltration. The current system is designed to treat and disposal of 2 500gal per minute. Current actual water treatment flowrates are approximately 600 gal per minute from the Stillwater West Section and 900 gal per minute from the Stillwater East Section (total of 1 500 gal per minute) which is approximately 60% of design flow. The Stillwater West Section is expected to remain near 600gal per minute for the foreseeable future. Results of groundwater studies in FY2021 suggested water inflows into the Stillwater East Section exceeding 3 000gal per minute, an estimate that has since been derated to 1 600gal per minute informed by results of subsequent review work completed in FY2021. Therefore, water treatment projections could increase to 2 200gal per minute, which remains below the current treatment plant and disposal capacity of 2 500 gal per minute. Nonetheless, efforts are underway to complete evaluation, engineering, and permitting in the future an expansion is needed in the future. In addition, clarifier upgrades were completed in FY2021 to increase capacity to 2 500gal per minute for each clarifier resulting in a total clarifier capacity of 5 000gal per minute. 15.1.5.3 Septic System The sanitary utilities at the Stillwater Mine consist of a septic system that includes a solids tank, an Advantex treatment system and a leach field. The system is operated primarily as a treatment and disposal system with the leach field providing secondary or back-up disposal. The treated effluent is sent to the Hertzler Land Application Disposal system for disposal. The capacity of the septic system of 18 000gal per day is adequate for the steady-state requirements for Stillwater Mine. Roads Stillwater Mine is located approximately 30 miles southwest of Absarokee and 4 miles south-southwest of Nye. It is accessed from Absarokee by the mainly unpaved County Road 420, which passes the Hertzler Ranch TSF or via the paved State Highway 78 and State Highway 419 and Nye Road. The road network on the Stillwater Mine site consists of unpaved roads, which are primarily used for the transport of logistics and stores for the functioning of the mine and for transport of personnel for access to the infrastructure positioned around the mine site. Equipment Maintenance Stillwater Mine has three workshops on surface, which are the following: Surface Locomotive Workshop: This has a single bay service and mechanical repair facility for all rolling stock (locomotives and ore cars) operating on the 5000 Level West. This workshop is primarily for work on wheels and engines; 189 East Side Workshop: This has multiple bay service and mechanical repairs facilities serving surface equipment as well as major repairs and rebuilds of primary equipment from the East Side. Stillwater West Workshop: This has multiple bay service and mechanical repair facilities for light and medium duty underground equipment as well as major repair/rebuild services for primary underground gear equipment that can be moved to the surface. It has full machining, welding, and Diesel Particulate Matter testing capabilities. In addition, Stillwater Mine has the following underground workshops: 6100W Level Workshop: This has multiple bay services and mechanical repair shop; 5600E Level Workshop: This has multiple bay services and mechanical repair shop for all rubber- tired equipment in the Stillwater East Section of the mine; 5000W Level Workshop: This is dedicated to the trackless equipment, which is serviced in the mine. It has a single bay service facility and is available for light mechanical repairs, servicing and electrical repairs on mobile equipment. All the rail equipment on this level is serviced and repaired on surface; 3500W Level Kiruna Workshop: This is a single bay service and mechanical repair workshop facility, which was designed specifically for the maintenance of the three Kiruna trucks and for maintenance of the AD30 Cat Trucks. The Kiruna trucks have been decommissioned; 3500W Level Locomotive Workshop: The 3 500 Level is primarily an ore and waste rock tramming level. Therefore, the workshop is a two-bay service and repair facility for rolling stock; 3800W Level Workshop: This is a two-bay service and mechanical repairs shop for all production equipment in the FWL; 3800E Level Workshop. This is a multiple bay service and mechanical repair shop subject to the same requirements at the 3800W Level Workshop; 2000W Level Workshop: This is the workshop on the lowest level, which caters for mechanical, electrical and general repair and services in multiple bays. All the underground workshops are well-equipped with good lighting, clean concrete floor areas for maintenance and wash bays to ensure quality inspections and are stocked with the appropriate tools and lifting equipment. Some of the workshops also provide for an administrative office underground to ensure that the planned maintenance system is updated timeously. A well-developed maintenance programme based on the JD Edwards Planned Maintenance system is in place and this includes daily, weekly and monthly scheduled maintenance. Major rebuilds of equipment take place on site or are sent to offsite Original Equipment Manufacturer (OEM) repair shops. In addition, the Sibanye-Stillwater US PGM Operations are developing a robust Asset Management Plan. Pre-use checks for all equipment are carried out and logged by the machine operator. Each piece of equipment has a unit number, which is entered into the management system. Equipment performance is logged daily by the operator onto the log sheet, which is uploaded into the system. The maintenance schedule flags equipment for weekly or monthly maintenance. The planned maintenance system records all equipment on the system for availability, utilisation, unit cost, age and planned replacement per the policy for that classification. Job cards are uploaded into the system to ensure each unit has a history of replacements done. The mine keeps over 500 maintenance items on the system. Shop Availability Maps are used by the mine to assist in planning and updating the status of work in the underground workshops. The overall physical map, including all workshops, is updated by the Workshop 190 Foreman daily to ensure that production teams know the status of repairs/maintenance on the equipment. The Maintenance Department has a target of 80% availability for its major mobile equipment. This percentage is an acceptable standard in industry for underground production and development fleets, although higher availabilities have been achieved at other mines. The unit utilisation is generally lower than industry norms due to the geographical spread of the mining operations. In addition, Stillwater Mine has found it more cost effective to provide more equipment than available at other mines (particularly the equipment that is not readily mobile such as bolters and drill rigs) to save on transport between the geographically spread underground production workings. Buildings Several new or modified buildings are required to support the production ramp up at Stillwater Mine. The following buildings were included in the expansion or modification plan: Expansions: warehouse, core shed and offices to support additional personnel; and Modifications: dry-house. Significant expansion of the warehouse at Stillwater Mine (7 500 square feet), implemented in 2019, was needed to accommodate the additional mine and concentrator consumables. The dry-house, relocated ambulance/rescue facility and expanded foreman offices are included in the North Multi-Service Wing. This Multi-Service Wing expansion was completed in FY2021, and includes: Seven new beat rooms; Renovated dispatch area with a “high-tech” control room; Two-bay ambulance garage; Medical area; Mine rescue area; and Five offices for foremen. The core shed handles all drillcore from the drilling and ore control related to the mine development and mine operations. The production ramp up approximately doubled the volume of core requiring handling and logging. The core handling area was consequently expanded within the existing structure to add 1 400 square feet, which displaced the ambulance, paramedic and rescue area. The core shed expansion was also completed in late FY2021. A geology and engineering office expansion was also completed, and this supports the additional Engineers and Geologists needed for the expanded operations. Figure 78 shows the overall site layout for Stillwater Mine.

191 Figure 78: Stillwater Mine Site Layout Transportation Personnel transportation to the Stillwater Mine is a combination of company supplied bussing and light vehicles, and personal vehicles. Transportation of salaried personnel is primarily by company owned light vehicles. Based on the current light vehicle to salaried personnel ratio, no additional light vehicles will be required for future mine plans. Hourly personnel travel to and from site either by company bussing or personal carpools. With employment growth and traffic commitments, additional busing is anticipated for the future mine plans. 192 East Boulder Mine Complex Concentrator Infrastructure The processing plant infrastructure at East Boulder Mine was built in 1999. The plant infrastructure is in a good condition, with the plant having been operated below nameplate capacity since establishment. Appropriate sustaining capital budget provisions have allowed for the undertaking of routine planned maintenance according to the JD Edwards Maintenance Control system. The power supply to the concentrator plants is described in Section 15.2.3. Tailings Storage Facilities The TSF at the East Boulder Mine comprises two cells of a single slimes impoundment as the current primary storage. Stage 1, comprising Cell 1, was operated from 2001 to 2007 after which Cell 2 became the primary deposition facility (Stage 2). Stage 3 is an embankment lift of Stages 1 and 2 and was operated from 2014 through 2020. Stage 4 is currently being filled and has been operated from FY2020. Stage 5 is an additional embankment lift and become active in FY2024. Beyond Stage 5, the East Boulder TSF has one additional embankment lift permitted and approved – i.e. Stage 6. Concentrator tailings are sampled and pumped to the underground sand plant where it is classified into coarse sand and slimes fractions. The sand remains underground and is pumped into stopes for backfilling purposes, whilst the slimes fraction is pumped back to surface. The slime is then pumped via one ten-inch pipeline to the TSF for deposition. Deposition on the TSF is via periodic rotational discharge of tailings slurry around the perimeter of the facility using a group of spigots. Once a localised tailings beach has formed, deposition is transferred to another group of spigots at a different location. Water reclamation is achieved via three inclined reclaim pumps and pipelines located on the south- western embankment of the TSF, closest to the concentrator, which discharges into the reclaim water tanks at the concentrator. All stages of the TSF are geomembrane lined. Basin underdrain and seepage measurement is performed and monitored via vibrating wire piezometers whereas embankment crest-mounted survey monuments are used to measure slope slippage or movement. Additional inclinometers are installed around the base of the impoundment to monitor deeper ground movement and displacement. The basin underdrain pore pressures are monitored on a weekly basis via the piezometers, and these respond quickly to changes in the basin underdrain pumping rate. Water drainage results in changes in the tailings mass consolidation and hence maximises storage availability and assists in long-term closure planning. The concentrator performs weekly, monthly and quarterly TSF inspections and monitoring per its standard procedures which are reviewed as part of the annual Engineer of Record inspection of the TSF performed by Knight-Piésold. The most recent inspection was performed in September 2023, with a review period from October 2022 to September 2023. No material issues were identified, but a corrective action plan for the issues which were identified has been developed and planned to be submitted to the MDEQ by 9 January 2024 as required and in compliance with the MCA. 193 Filling of Stage 4 is currently underway and projected to continue into FY2024 with the freeboard allowance provided with completion of lining for Stage 5. As part of the annual inspection of the East Boulder TSF, Knight-Piésold calculated a projected fill rate of the current and planned TSF capacity as an elevation above mean sea level by year. Stage 5 and Stage 6 lifts are already permitted with Stage 5 construction completed and Stage 6 under construction. The embankment crest maximum elevation of Stage 5 has been designed by Knight-Piésold as 6 330ftmamsl, and the Stage 6 crest has been designed at 6 344ftmamsl. Water treatment facilities were upgraded to increase the water treatment capacity and the Guard Shack was also relocated to allow for the Stage 6 build. Based on Knight-Piésold’s current filling calculations, the Stage 4 limit is estimated to be reached in Q3 2024. As part of the planning to meet the Inflow Design Flood management procedures, an interim overflow channel will be installed, which will extend the capacity as indicated in Figure 79, while the Stage 5 construction is scheduled to be complete in January 2024, well ahead of the required first discharge. The Qualified Person considers the design and capacity filling calculations for the TSF to be appropriate and to take cognisance of the planned production. Figure 79: East Boulder TSF Calculated Elevation Profile 194 The Stage 5 and Stage 6 lifts are currently under construction, with Stage 5 scheduled for completion and lining in Q FY2024 and Stage 6 scheduled for completion in FY2025. The Stage 5 and Stage 6 foundation preparation and infrastructure relocation were completed in late FY2023. This work included relocation of soil piles, fencing, underdrain collection basin, nitrogen collection pond, recycle pond and Pumphouse 1, main overhead powerline, mill overhead powerline, guard shack and gate, transformers, fiber, Boe Ranch pipeline and vaults, underdrain pipeline, nitrogen pond pipeline, groundwater well pumpback system, inclinometers, warehouse septic system, surface electrical building, fire hydrants, wash bay, burn pit, laydown yard, equipment ready line, mill fuel storage, and mine access road. The Qualified Person notes Knight-Piésold’s current filling calculations discussed above and that the TSF basin filling schedule depends on the incremental addition of settled tailings solids and on changes in the supernatant pond volume. The TSF filling curve has been updated with the estimated tailings disposal projections provided by Sibanye-Stillwater and an assumed constant supernatant pond volume. An updated short-term filling curve as of September 2023 is shown on Figure 80 and briefly summarised as follows: The water level was at approximate elevation 6 311.4ft; The supernatant pond volume was approximately 199Mgal; The Stage 4 TSF (maximum filling level elevation 6 315 ft) and Stage 5 TSF (maximum filling level elevation 6 324ft) will be reached in September of 2024 and December of 2027, respectively, assuming 55% of the tailings are deposited to the TSF, the existing water pond volume is maintained and the settled dry tailings density is 70lb/ft3; and Stage 6 is currently projected to reach capacity in December 2032. Basin underdrain water is transferred to the mine water recycle pond. As illustrated in Figure 80, the rate and timing of impoundment filling depends on changes to the supernatant pond volume as well as the proportion of the total tailings that are ‘stored’ as underground backfill. Sibanye-Stillwater’s tailings deposition records indicate that approximately 54% of the tailings solids were deposited into the TSF from January through September 2023, with the remainder of the tailings solids stored as underground backfill. Assuming that the plant production remains approximately consistent with previous years, then about 50% to 55% of the total tailings solids will continue to be deposited into the TSF. Furthermore, if the 200Mgal supernatant pond volume is also maintained, then the Stage 4 TSF would reach capacity in September 2024 (with 6ft. freeboard allowance maintained). Detailed pond level and volume monitoring must continue on an ongoing basis. Figure 79

195 Figure 80: East Boulder TSF Calculated Elevation Profile The capital budget for East Boulder Mine includes capital expenditure for the Lewis Gulch TSF comprising $5.5 million for infrastructure and topsoil relation in FY2026 and $53.4 million for construction between FY2027 and FY2028, and $7.5 million for closure between FY2043 and FY2045. The budget includes costs for a future TSF amounting to $100 million between FY2039 and FY2042. The Qualified Person is satisfied with the capital allowance for new TSFs (e.g., Lewis Gulch TSF and another future TSF) that will be required in future. Dry Fork Waste Rock Storage Area In conjunction with the construction of new and expanded tailings facilities, a new waste rock storage area has been designed. The proposed Dry Fork Waste Rock Storage Area (West Storage Area) was included in the permitting of the Lewis Gulch TSF within Amendment 004. Approval of Amendment 004 is expected in July 2024. The Dry Fork Waste Rock Storage Area (West Storage Area) will be 102 acres in size and is designed to contain 5.4 million cubic yards of material. Based on current mine plans, this will provide waste rock storage up to FY2047. A second, separate waste dump (East Waste Rock Storage Area) has been envisioned in the Dry Fork Waste Rock Storage Area with some preliminary design work 196 completed. The East Waste Storage Area in the Dry Fork Waste Rock Storage Area will provide an additional 28 years of storage beyond FY2047 (up to FY2075). Permitting of the East Waste Storage Area is anticipated in the 2040s. Construction of the Stage 6 TSF lift is scheduled for completion in January 2026. Upon completion of the Stage 6 TSF embankment lift and lining, waste rock will need to be placed in the Dry Fork Waste Rock Storage Area or within the existing Stage 6 TSF. Construction of Phase 1 of the Dry Fork Waste Rock Storage Area is scheduled for to begin in late FY2024 and continues to FY2025 based on anticipated regulatory approval which will be permitted as part of the Lewis Gulch TSF. A bridge and access road will be constructed at the start of Phase 1 in FY2025. The capital budget for the Phase 1 of Dry Fork Waste Rock Storage Area (construction and lining) amounts to $28.5 million over the period FY2024 and FY2026. Phase 2 to Phase 4 also have capital provisions in the capital budget for East Boulder Mine in FY2030 ($2.9 million), FY2035 ($7.5 million) and FY2046 ($6.3 million), respectively, as well as for closure between FY2055 and FY2056 ($5.5 million). The Qualified Person is satisfied with the capital provisions for construction and closure of the waste rock storage facilities. Power Power to East Boulder Mine is fed from the North West Energy’s 161kV powerline via a tap located north of Springdale and then via the Duck Creek Substation. Park Electric, a power co-operative, supplies power to the mine site and owns the distribution facilities. The power feed from Duck Creek to McLeod and from McLeod to the mine is via a 69kV powerline. Sibanye-Stillwater owns two main substations situated at East Boulder Mine. The mill transformer is a 15/20MVA 69kV to 4 160V and the mine operations transformer is a 10/14MVA 69kV to 13.8kV. There are no spares for either transformer, but there is a cross feed between the two substations which is rated for 8MW. Dedicated capacity for East Boulder Mine is 23MW at a unity power factor contracted from Park Electric, which is adequate for the increased production levels associated with the Fill the Mill Project. East Boulder power loads are currently as follows: Mine and surface: 7MW at a 0.91 power factor (approximately 77% of maximum capacity); Concentrator: 5.5MW at a 0.93 power factor (approximately 40% of maximum capacity); and Monthly Maximum Peak: 12.5MW at a 0.91 power factor. There are two main feeders that feed the underground switchgear from the surface switchgear. Normal operation is to use one feeder and have the other feeder available as a backup. One feeder is installed in Tunnel #1 and the second feeder installed in Tunnel #2. Current underground load is approximately 5MW at a 0.80 power factor. Each of these feeder cables have a loading capacity of approximately 7MW (assuming a 5% maximum voltage drop). East Boulder Mine has two 2MVA Caterpillar 3516B diesel generators which were installed in 2001 at the portal on surface. These generators are currently permitted only as emergency generators, which should be operated for at most 500 hours per year. The generators are designed to operate at the same time 197 in parallel and share the load. When running in parallel, the continuous load on these generators is limited to 3.5MW to allow for peak demands of less than 4MW. Bulk Water 15.2.5.1 Water Supply The water supply for the East Boulder Mine is a mix of fresh make-up water from groundwater supply wells, recycled water from the water treatment facilities and ground water encountered during mining operations. The overall water balance is positive, and disposal of surplus water is required. The groundwater supply wells include the potable water system which provides potable water to the surface operations only and the freshwater system which provides fire water for surface operations and reagent make-up water for the mill. Onsite, the water is reticulated to various sites through a network of pipelines (distribution system). Water consumption from the wells is approximately 50gal per minute and is not expected to increase significantly in future. Water Right Permits allow for beneficial use of up to 262gal per minute from mine water and up to 200gal per minute from potable wells. Treatment and discharge to percolation is not considered a beneficial use and discharge through the Montana Pollutant Discharge Elimination System permit is not included in the water right quota. Current water rights, therefore, are sufficient to support the mine plan. 15.2.5.2 Water Treatment The water treatment system at East Boulder Mine treats and discharges mine water from the underground mining operations. The current system was designed to treat approximately 750gal per minute of water from the underground mining operations. Mine water is first clarified, with a portion recycled to the underground drill water reservoir while the remaining water continues to the biological water treatment process to remove nitrates and ammonia. Treated water is split between recycling for mine use and disposal by percolation to groundwater, based on operational demands. In late FY2015, East Boulder Mine received a new Montana Pollutant Discharge Elimination System (Water Discharge) permit, which stipulated stringent metals discharge limits. The permit allows for a five- year interim period for treatment system evaluation and improvements before the new discharge limits apply. A new discharge permit was issued in September 2023 which included a revision to the discharge limits. For compliance, the drilling of a deep injection test well was undertaken and successfully tested. The testing of an existing 45 000ft pipeline from East Boulder Mine site to the injection well system was also completed and commissioned in FY2020. This pipeline was designed to carry treated mine water effluent to an injection well at the Yates Gravel Pit for compliance with the discharge limits. 15.2.5.3 Septic System The East Boulder Mine wastewater treatment facility was originally designed and permitted in 1998. The system serves the upper bench office buildings and the concentrator. The design basis for the original system was 600 employees with a peak per capita flow rate of 15gal per day (i.e., 9 000gal per day for the whole mine). The system consisted of approximately 700ft of 8-inch diameter PVC gravity sewer, 198 combined septic dose tank, and two zone conventional drain field with each zone having thirteen 100ft long laterals. In 2006, the collection system was expanded to include a Mobile Dry Building which was included in the original design of 600 employees. The 2006 improvements also made modifications to the existing drainfield to correct ongoing maintenance issues. The 2006 drainfield modifications consisted of replacing the existing conventional drain field with trench infiltrator chambers, adding one lateral to each zone of the drainfield for a total of twenty-eight 100ft long laterals, updating dose pumps and controls, and reducing the drainfield application rate from 1.2gal per day/ft2 to 0.8gal per day/ft2 (due to updated regulations). In FY2015, measured flow tests resulted in an approximate daily flow rate of 9 000gal per day with peak daily flows of 11 000gal per day. Permitting to accommodate the increase is complete as well as the upgrade of the existing wastewater treatment system to 11 000gal per day. The improvements have increased the septic and dose tank capacity and controls. Roads East Boulder Mine is located approximately 25 miles south of Big Timber. The mine is accessed from Big Timber via the paved State Highway 298 and the unpaved East Boulder Road maintained by Sibanye- Stillwater. The road network on the East Boulder Mine site consists of unpaved roads which are primarily used for the transport of logistics and stores for the functioning of the mine and for transport of personnel for access to the infrastructure positioned around the mine site. Buildings East Boulder Mine has adequate modern, fit for purpose offices for administration, technical and personnel services. The mine also has a change house in proximity for the use of mine staff as well as drill core processing and storage facilities. The processing plant has an additional separate small control office facility for operational staff. Likewise, the surface engineering workshops have small operational offices within the workshops. The mine provides adequate secure parking in a gravel parking area adjacent to the main office entry. The mine complex is fenced, with the complex accessed from a security guard manned main gate. Figure 81 shows the overall site layout for East Boulder Mine.

199 Figure 81: East Boulder Mine Site Layout Equipment Maintenance East Boulder Mine also makes use of the JD Edwards Planned Maintenance system, with the robust Asset Management Plan. The mine has two workshops on surface, which are the following: Surface Locomotive Workshop: This has a single bay service and mechanical repairs facility for all rolling stock, and includes facilities for work on wheels and engines on the locomotives and ore cars; and 200 Surface Engineering Workshop: This has multiple bay service and mechanical repair facilities for surface trucks with full machining, welding and electrical maintenance facilities. The mine has the following workshops underground: 6500 Level Workshop: This has multiple-bay facilities and carries out repairs for both mechanical and electrical faults and maintenance. It also provides a service facility for the rail bound equipment and the adjacent sandfill plant. The workshop is equipped with separate wash bay, office area, warehouse and fuel store. Major overhauls are carried out in the surface workshops; A small service bay at 68 780 Level. 7900 Level Mobile Workshop: This is primarily for the mobile equipment in the upper mine. It has an ambulance and medical support centre and adjacent refuge bay. This is expected to be a permanent workshop for the life of the mine. All the underground workshops are well-equipped with good lighting, clean concrete floor areas for maintenance, wash bays to ensure quality inspections, and are stocked with the appropriate tools and lifting equipment. Transportation Personnel transportation to East Boulder Mine is a combination of company supplied bussing and company supplied light vehicles. Current company policy mandates the use of company supplied bussing for hourly personnel. Transportation of salaried personnel is primarily by company owned light vehicles. Based on the current light vehicle to salaried personnel ratio, no additional light vehicles will be required for future mine plans. Columbus Metallurgical Facility The Columbus Metallurgical Complex, which houses the smelter, base metal refinery, laboratory and recycling plant, was built on freehold owned by Sibanye-Stillwater. The building and stack heights are limited due to the proximity of the light aircraft field. The facilities are secured by fencing and access is limited to card holding employees. The Columbus Metallurgical Complex includes well-established automated sampling and sample processing facilities with a robotic operated sample laboratory. Office facilities are adequate for the required staff to operate the base metal refinery and smelter. Infrastructure at the Columbus Metallurgical Complex is maintained in a good operational condition through adequate capital provisions for maintenance and upgrades as required. Power supply to these facilities is from North West Energy at the standard 100kV at the main switch station and two-step down transformers. Sibanye-Stillwater keeps a spare transformer onsite and, therefore, power supply is reliable. 201 MARKET STUDIES Introduction PGMs (also referred to as Platinum Group Elements or PGEs) comprise platinum, palladium, rhodium, ruthenium, iridium and osmium. The Bushveld Complex in South Africa contains approximately 80% of the known global PGM mineralisation and produces approximately 80% of the world’s annual PGM supply from the UG2 and Merensky Reefs. The J-M Reef mined at Stillwater and East Boulder Mines is the sole source of primary palladium and platinum production in the USA, accounting for approximately 5% of the world annual primary PGM supply. PGM mineralisation in the J-M Reef is dominated by palladium and platinum, with other PGMs occurring in negligible quantities. Sibanye-Stillwater commissioned an independent PGM market study by its research company, SFA Analytics (SFA Oxford), which was completed in October 2023. Information from this source along with negotiated contracts inform Sibanye-Stillwater’s price and sales predictions. Given that palladium and platinum account for almost 100% of the revenue generated at Stillwater and East Boulder Mines, this market review focuses on these two metals. PGM Market Overview According to SFA Oxford, both platinum and palladium markets were in supply deficit during 2023 because of continued light vehicle demand recovery from both pandemic lows and the semiconductor chip shortage, as well as periods of supply disruption in South Africa and Russia. However, palladium prices declined 38% from $1 725/oz at the beginning of 2023 while the platinum price was rangebound, averaging $904/oz over the year. In palladium’s case, this is interpreted to be because of increasing sales of Russian palladium to China through 2023, eroding price support for palladium. The relatively stable platinum price belied the decline in PGM basket prices for South African producers through 2023. Global light vehicle production amounted to 82 million units in 2023, with production forecasts for 2024 anticipated to exceed the 2019 (pre-COVID-19 pandemic) level of approximately 86.5 million units. The main regions driving this production outlook are China, Japan, India and Korea. Through 2023, the US automotive sector faced disruptive strikes with concurrent inflation and high interest rates tempering light vehicle sales. The Battery Electric Vehicle (BEV) share of global light duty vehicles grew from 9% in 2022 to 12% in 2023. However, cautious BEV uptake in the West and aggressive price cuts have seen a number of European and US automakers scaling back prior BEV sales targets and timelines. The forthcoming elections in Europe and the US in 2024 may also contribute to a slower pace of electrification growth in these jurisdictions. 202 Platinum and Palladium Demand and Supply Demand Drivers According to SFA Oxford, the main uses of platinum are as a catalyst for automotive emissions control, in a wide range of jewellery pieces and in industrial catalytic and fabrication applications. Palladium is primarily used as a catalyst in the automotive sector, mainly in gasoline-powered on-road vehicles, but alongside platinum in parts of the light-duty diesel engine after-treatment too. The second main use of palladium is in electrical components, specifically in multi-layer ceramic capacitors (MLCCs), as conductive pastes and in electrical plating. Platinum Through 2023, the platinum price oscillated in a narrow range between $1 080/oz and $904/oz, settling at $970/oz at the beginning of 2024. In 2023, global primary platinum supply is estimated to have grown by 1.4% year-on-year (y-o-y) to 5.56Moz, with production increases in South Africa, Zimbabwe and the North Americas offsetting a 1.2% (-8koz) y-o-y reduction in Russian production because of smelter maintenance at Nornickel. Through 2023, prolonged Eskom load curtailment in South Africa slowed the processing of an estimated 90koz of platinum contained in excess Work-in-Progress (WIP) stocks. Global primary platinum supply remains 8.8% (-538koz) lower than 2019’s pre-COVID 19 pandemic production levels. Autocatalyst recycling provides the bulk of secondary PGM supply and contributed 1.4Moz of platinum in 2023, in line with 2022 recycling levels. According to SFA Oxford, platinum demand for all applications is projected to rise by 1% in 2024 to 7.7Moz, supported by growth in light vehicle production, which is recovering from the semiconductor chip shortage, and expanding use of platinum loaded gasoline autocatalysts. This autocatalyst demand accounted for some 3.5Moz or 44% of platinum demand in 2023 and is expected to continue at this level in 2024. Chemical, electrical, glass and medical demand for platinum is forecast to continue to rise steadily from 2023 demand levels of 1.7Moz. Through 2024, jewellery demand for platinum is expected to remain stable at or near 2023 levels (1.47Moz). Platinum is required across the entire hydrogen value chain, including the upstream, mid-stream and downstream segments, and demand is predicted to rise from current levels of approximately 190koz per annum to some 365koz per annum by 2030. The hydrogen economy and industrial applications are therefore the long-term growth areas for platinum demand. The platinum market’s supply deficit of 450koz at the end of 2023 is forecast to continue through 2024 to a level of approximately 445koz by the end of the year. Palladium Palladium prices declined from $1 725/oz at the beginning of 2023 to $1 075/oz at the beginning of 2024. Global primary palladium supply reduced by 1.7% y-o-y in 2023 to 6.34Moz, with production increases in South Africa, Zimbabwe and the North Americas being eclipsed by reduced Russian production because of lower efficiencies related to alternative equipment sourcing (a consequence of the Russia- Ukraine conflict) and a period of smelter maintenance.

203 Global primary palladium supply in 2023 was 11.6% lower (-836koz) than pre-COVID 19 pandemic production levels in 2019, with Zimbabwe being the only jurisdiction to display growth since 2019 following the completion of the third concentrator at Ngezi Mine. Primary palladium supply is forecast to increase 2.2% y-o-y in 2024, to approximately 6.42Moz, with higher palladium yields anticipated from mines in South Africa and the North Americas. Over the next decade, secondary palladium supply from autocatalyst recycling is anticipated to grow from the 2023 level of 2.4Moz as the stock of aging light vehicles to be scrapped will progressively yield higher PGM loaded autocatalyst. 2023 is interpreted by SFA Oxford to have been a peak of all-application global palladium demand at 10.2Moz. Price-driven substitution for platinum in autocatalyst applications is anticipated to dampen 2024 demand to below 8.0Moz from the 2023 palladium-for-autocatalyst peak of 8.2Moz. Anticipated demand for palladium in all other applications, except for dental uses, is forecast to remain steady through 2024 at current levels of approximately 1.95Moz per annum. Dental use demand for palladium is forecast to continue to gradually decline from present levels of approximately 170koz per annum because of price driven substitution into alternative materials. Palladium demand related to the hydrogen economy is restricted to the mid-stream and downstream segments including catalysts for methanol synthesis, and for sustainable aviation fuel and diesel manufacture. Some additional demand for palladium over the next decade will depend on the pace of development of these hydrogen economy segments. SFA Oxford anticipate that the 2023 palladium supply deficit of 1.49Moz will be reduced to a supply deficit of approximately 855koz in 2024. Palladium and Platinum Pricing Outlook For business planning and Mineral Reserve estimation, Sibanye-Stillwater uses forward looking prices that it considers will stay stable for at least three to five years, and will significantly change if there is a fundamental, perceived long-term shift in the market, as opposed to basing it only on short term analyst consensus forecasts. Sibanye-Stillwater also considers its general view of the market, the relative position of its operations on the costs curve, as well as its operational and company strategy in its forecasting of forward-looking prices. On a monthly basis, Sibanye-Stillwater also receives an independent report from UBS Bank (Commodity Consensus Forecasts Report) which contains consensus outlooks from the various banks on a broad range of commodities. It benchmarks its forward-looking prices to the market consensus forecast. Table 48 summarises the forward-looking prices of palladium and platinum applied by Sibanye-Stillwater for business planning and Mineral Reserve declaration as at December 31, 2023. This also shows comparison between Sibanye-Stillwater and Market Consensus forward-looking prices. The Qualified 204 Persons note that the comparison shows overall agreement between the price forecasts and, therefore, Sibanye-Stillwater forward-looking prices are reasonable. Table 48: Comparison of Sibanye-Stillwater and Market Consensus Prices Metal Unit Market Consensus Forward Price – 2024 Mineral Reserve Price – 2024 Platinum USD/oz 1 135 1 250 Palladium USD/oz 1 213 1 250 Material Metals Marketing Agreements The Columbus Metallurgical Complex and Precious Metal Refining Sibanye-Stillwater’s wholly owned Columbus Metallurgical Complex is a state-of-the-art operation that provides smelting and refining processes for PGM concentrates from the Stillwater and East Boulder mines. In addition, the complex facilitates recycling operations for various materials containing PGMs, principally automotive catalytic converters that are provided by third-party suppliers under arms-length commercial offtake or toll treating contract terms. The complex produces a PGM-rich concentrate after base metal refining that is shipped to a third-party precious metal refinery under a toll processing agreement that provides Sibanye-Stillwater returns of finished metal. Sibanye-Stillwater utilises a single third-party company for all of its precious metals refining services for Sibanye-Stillwater’s US PGM Operations. All of Sibanye-Stillwater’s current mined palladium and platinum in the United States is committed for sale to such company. The refining and sales agreements are multiple year contracts entered into with the third-party company. Sibanye-Stillwater pays its refiner a per-ounce refining charge for toll processing of the refined PGM-rich concentrate, and the refiner also retains a small percentage of contained metals. Refined PGMs of minimum 99.5% purity in sponge form are transferred upon sale from Sibanye-Stillwater’s account to the account of the third-party refiner. The refiner will purchase all of the mined palladium and platinum at competitive prices based on a pricing mechanism linked to various agreed to industry benchmarks. Wheaton International Streaming Agreement In 2018, Wheaton Precious Metals International Limited (Wheaton International) and the Group entered into a Streaming Agreement. As per the Streaming Agreement, 100% of refined mined gold and 4.5% of refined mined palladium from the Stillwater Mining Company operations (Sibanye-Stillwater US PGM Operations) will be delivered to Wheaton International over the life of mine of the operations. Each ounce is identified as a separate performance obligation. In exchange for this, Wheaton International paid the Sibanye-Stillwater US$500 million on 25 July 2018 (the Advance Amount). Under the Streaming Agreement, in addition to the Advance Amount, Wheaton International will pay Sibanye-Stillwater 18% of the US dollar spot palladium and gold prices for each ounce delivered under the Streaming Agreement until the Advance Amount has been reduced to nil through metal deliveries. Thereafter, Sibanye-Stillwater will receive 22% of the spot US dollar palladium and gold prices for each ounce of palladium and gold delivered under the Streaming 205 Agreement. The contract will be settled by the Sibanye-Stillwater delivering metal credits to Wheaton International representing underlying refined, mined gold and palladium. As per the Streaming Agreement, the following entitlements apply: Palladium entitlement percentage: o The palladium entitlement percentage will be either 4.5%, 2.25% or 1% over the life of mine, depending on whether or not the Advance Amount has been fully reduced, and a certain number of contractual ounces have been delivered (375 000oz for the first trigger drop down to 2.25% and 550 000oz for the second trigger drop down rate to 1%). Gold entitlement percentage: o The gold entitlement percentage will be 100% over the life of the mine; Monthly cash percentage: o The monthly cash payment to be received is 18%, 16%, 14% or 10% of the market price of the metal credit delivery to Wheaton International while the Advance Amount is not fully reduced. After the Advance Amount has been fully reduced, the cash percentage is 22%, 20%, 18% or 14%. In both cases, the payments by Wheaton International may be reduced if debt covenants exceed three and half multiples of the net debt to adjusted Earnings Before Interest, Taxes, Depreciation and Amortisation (EBITDA) ratio. The balance of the ounces in the monthly delivery (i.e. 100%-18%= 82%) is then used to determine the utilisation of the deferred revenue balance. Sibanye-Stillwater agreed to use commercially reasonable efforts to facilitate the development of the Blitz Project. The Streaming Agreement includes a completion test on the development of the Blitz Project, including completion of underground development, critical surface infrastructure and expansion of the concentrator production output. If Sibanye-Stillwater fails to meet certain completion targets in relation to the Blitz Project, it is required to pay Wheaton International certain cash amounts. The Qualified Person notes that, with the achievement of the agreed to project milestones, the completion test on the development of the Blitz Project has been scheduled for completion during the first half of 2024. The Streaming Agreement, with an effective date of 1 July 2018, continues for an initial period of 40 years and can be extended for successive 10-year periods until termination notice is given or there are no active mining operations at the Sibanye-Stillwater US PGM Operations. The Qualified Persons note that the Streaming Agreement is material to the Sibanye-Stillwater US PGM Operations but sets out conditions that are not excessively onerous and can easily be achieved by Sibanye-Stillwater if the current LoM plans for Stillwater and East Boulder Mines are executed as planned. 206 ENVIRONMENTAL STUDIES, PERMITTING, PLANS, NEGOTIATIONS/AGREEMENTS Social and Community Agreements In order to assist in managing Sibanye-Stillwater’s Social Licence to Operate, a progressive and effective Good Neighbor Agreement was signed in 2000 and this agreement was amended in 2005, 2009, 2015 and 2023. The Good Neighbor Agreement is a legally binding contract between Sibanye-Stillwater, the Northern Plains Resource Council, Cottonwood Resource Council and Stillwater Protective Association, which is binding on current and future owners and managers of the Stillwater and East Boulder Mines. It provides an avenue for the citizen groups to access information on the Stillwater and East Boulder Mines and to participate in decisions on the operations that may impact the local communities, economies, or environment. In essence, it provides for citizen oversight of Stillwater and East Boulder Mines to guarantee protection of the area’s quality of life and productive agricultural land and allows for local communities to have access to critical information about mining operations and the opportunity to address potential problems before they occur. Furthermore, it requires the information to be sufficiently detailed to permit assessment of potential environmental and social impacts. There are no commitments to local procurement and hiring in the Good Neighbor Agreement. While not contractually obliged to commit to local procurement and hiring, Sibanye-Stillwater gives preference to local skilled personnel as deliberate local economic empowerment. Both Stillwater and East Boulder Mines have a Good Neighbor Oversight Committee that meets three times per year. In addition to these formal, transcribed meetings, a Technology Committee and other committees meet as needed but communicate weekly to address ongoing projects. This constant stakeholder engagement enables citizens to meaningfully engage in the permitting and mine planning processes and provide feedback in advance of formal comment periods. This approach allows Sibanye-Stillwater to adjust its permitting strategy to address stakeholder concerns, where necessary, and effectively reduce the potential permitting delays and negative comments during public comment periods. A primary focus of the Good Neighbor Agreement is water quality, and under the agreement, the Stillwater and East Boulder Rivers are closely monitored for changes in water quality. The agreement sets water quality triggers that meet or exceed the state and federal requirements. If a Good Neighbor Agreement water quality trigger is exceeded, Sibanye-Stillwater will take the appropriate remedial actions as defined in the agreement. As part of the monitoring, citizens may attend all mine-related water quality inspections and sampling events but are also provided with quarterly water quality reports. A provision is also made for the citizens to conduct independent water quality sampling, if necessary. The Good Neighbor Agreement is also aimed at ensuring public safety and security by restricting mine traffic and monitoring Sibanye-Stillwater’s adherence to the permitted traffic volumes and speed limits. In order to meet traffic requirements, the agreement provides for carpooling and bussing as a preferable means of transport for mine employees. These arrangements also afford mine workers additional rest time and keep tired drivers off the road.
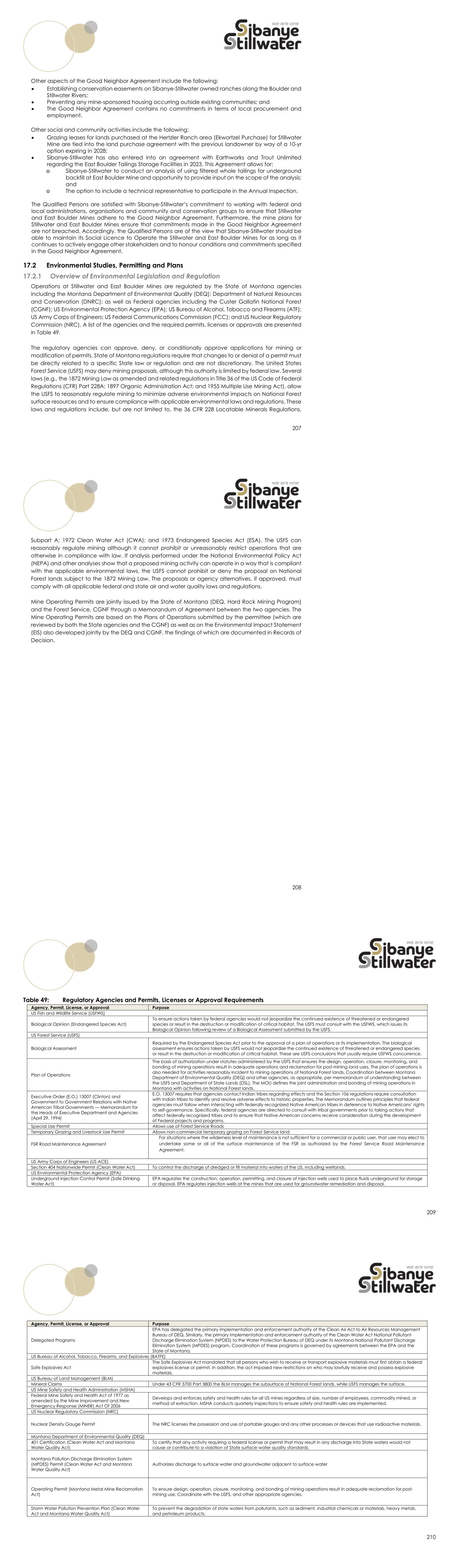
207 Other aspects of the Good Neighbor Agreement include the following: Establishing conservation easements on Sibanye-Stillwater owned ranches along the Boulder and Stillwater Rivers; Preventing any mine-sponsored housing occurring outside existing communities; and The Good Neighbor Agreement contains no commitments in terms of local procurement and employment. Other social and community activities include the following: Grazing leases for lands purchased at the Hertzler Ranch area (Ekwortzel Purchase) for Stillwater Mine are tied into the land purchase agreement with the previous landowner by way of a 10-yr option expiring in 2028; Sibanye-Stillwater has also entered into an agreement with Earthworks and Trout Unlimited regarding the East Boulder Tailings Storage Facilities in 2023. This Agreement allows for: o Sibanye-Stillwater to conduct an analysis of using filtered whole tailings for underground backfill at East Boulder Mine and opportunity to provide input on the scope of the analysis; and o The option to include a technical representative to participate in the Annual Inspection. The Qualified Persons are satisfied with Sibanye-Stillwater’s commitment to working with federal and local administrations, organisations and community and conservation groups to ensure that Stillwater and East Boulder Mines adhere to the Good Neighbor Agreement. Furthermore, the mine plans for Stillwater and East Boulder Mines ensure that commitments made in the Good Neighbor Agreement are not breached. Accordingly, the Qualified Persons are of the view that Sibanye-Stillwater should be able to maintain its Social Licence to Operate the Stillwater and East Boulder Mines for as long as it continues to actively engage other stakeholders and to honour conditions and commitments specified in the Good Neighbor Agreement. Environmental Studies, Permitting and Plans Overview of Environmental Legislation and Regulation Operations at Stillwater and East Boulder Mines are regulated by the State of Montana agencies including the Montana Department of Environmental Quality (DEQ); Department of Natural Resources and Conservation (DNRC); as well as Federal agencies including the Custer Gallatin National Forest (CGNF); US Environmental Protection Agency (EPA); US Bureau of Alcohol, Tobacco and Firearms (ATF); US Army Corps of Engineers; US Federal Communications Commission (FCC); and US Nuclear Regulatory Commission (NRC). A list of the agencies and the required permits, licenses or approvals are presented in Table 49. The regulatory agencies can approve, deny, or conditionally approve applications for mining or modification of permits. State of Montana regulations require that changes to or denial of a permit must be directly related to a specific State law or regulation and are not discretionary. The United States Forest Service (USFS) may deny mining proposals, although this authority is limited by federal law. Several laws (e.g., the 1872 Mining Law as amended and related regulations in Title 36 of the US Code of Federal Regulations (CFR) Part 228A; 1897 Organic Administration Act; and 1955 Multiple Use Mining Act), allow the USFS to reasonably regulate mining to minimize adverse environmental impacts on National Forest surface resources and to ensure compliance with applicable environmental laws and regulations. These laws and regulations include, but are not limited to, the 36 CFR 228 Locatable Minerals Regulations, 208 Subpart A; 1972 Clean Water Act (CWA); and 1973 Endangered Species Act (ESA). The USFS can reasonably regulate mining although it cannot prohibit or unreasonably restrict operations that are otherwise in compliance with law. If analysis performed under the National Environmental Policy Act (NEPA) and other analyses show that a proposed mining activity can operate in a way that is compliant with the applicable environmental laws, the USFS cannot prohibit or deny the proposal on National Forest lands subject to the 1872 Mining Law. The proposals or agency alternatives, if approved, must comply with all applicable federal and state air and water quality laws and regulations. Mine Operating Permits are jointly issued by the State of Montana (DEQ, Hard Rock Mining Program) and the Forest Service, CGNF through a Memorandum of Agreement between the two agencies. The Mine Operating Permits are based on the Plans of Operations submitted by the permittee (which are reviewed by both the State agencies and the CGNF) as well as on the Environmental Impact Statement (EIS) also developed jointly by the DEQ and CGNF, the findings of which are documented in Records of Decision. 209 Table 49: Regulatory Agencies and Permits, Licenses or Approval Requirements Agency, Permit, License, or Approval Purpose US Fish and Wildlife Service (USFWS) Biological Opinion (Endangered Species Act) To ensure actions taken by federal agencies would not jeopardize the continued existence of threatened or endangered species or result in the destruction or modification of critical habitat. The USFS must consult with the USFWS, which issues its Biological Opinion following review of a Biological Assessment submitted by the USFS. US Forest Service (USFS) Biological Assessment Required by the Endangered Species Act prior to the approval of a plan of operations or its implementation. The biological assessment ensures actions taken by USFS would not jeopardize the continued existence of threatened or endangered species or result in the destruction or modification of critical habitat. These are USFS conclusions that usually require USFWS concurrence. Plan of Operations The basis of authorization under statutes administered by the USFS that ensures the design, operation, closure, monitoring, and bonding of mining operations result in adequate operations and reclamation for post-mining land uses. The plan of operations is also needed for activities reasonably incident to mining operations of National Forest lands. Coordination between Montana Department of Environmental Quality (DEQ) and other agencies, as appropriate, per memorandum of understanding between the USFS and Department of State Lands (DSL). The MOU defines the joint administration and bonding of mining operations in Montana with activities on National Forest lands. Executive Order (E.O.) 13007 (Clinton) and Government to Government Relations with Native American Tribal Governments — Memorandum for the Heads of Executive Department and Agencies (April 29, 1994) E.O. 13007 requires that agencies contact Indian tribes regarding effects and the Section 106 regulations require consultation with Indian tribes to identify and resolve adverse effects to historic properties. The Memorandum outlines principles that federal agencies must follow when interacting with federally recognized Native American tribes in deference to Native Americans’ rights to self-governance. Specifically, federal agencies are directed to consult with tribal governments prior to taking actions that affect federally recognized tribes and to ensure that Native American concerns receive consideration during the development of Federal projects and programs. Special Use Permit Allows use of Forest Service Roads Temporary Grazing and Livestock Use Permit Allows non-commercial temporary grazing on Forest Service land FSR Road Maintenance Agreement For situations where the wilderness level of maintenance is not sufficient for a commercial or public user, that user may elect to undertake some or all of the surface maintenance of the FSR as authorized by the Forest Service Road Maintenance Agreement. US Army Corps of Engineers (US ACE) Section 404 Nationwide Permit (Clean Water Act) To control the discharge of dredged or fill material into waters of the US, including wetlands. US Environmental Protection Agency (EPA) Underground Injection Control Permit (Safe Drinking Water Act) EPA regulates the construction, operation, permitting, and closure of injection wells used to place fluids underground for storage or disposal. EPA regulates injection wells at the mines that are used for groundwater remediation and disposal. 210 Agency, Permit, License, or Approval Purpose Delegated Programs EPA has delegated the primary implementation and enforcement authority of the Clean Air Act to Air Resources Management Bureau of DEQ. Similarly, the primary implementation and enforcement authority of the Clean Water Act National Pollutant Discharge Elimination System (NPDES) to the Water Protection Bureau of DEQ under its Montana National Pollutant Discharge Elimination System (MPDES) program. Coordination of these programs is governed by agreements between the EPA and the State of Montana. US Bureau of Alcohol, Tobacco, Firearms, and Explosives (BATFE) Safe Explosives Act The Safe Explosives Act mandated that all persons who wish to receive or transport explosive materials must first obtain a federal explosives license or permit. In addition, the act imposed new restrictions on who may lawfully receive and possess explosive materials. US Bureau of Land Management (BLM) Mineral Claims Under 43 CFR 3700 Part 3800 the BLM manages the subsurface of National Forest lands, while USFS manages the surface. US Mine Safety and Health Administration (MSHA) Federal Mine Safety and Health Act of 1977 as amended by the Mine Improvement and New Emergency Response (MINER) Act Of 2006 Develops and enforces safety and health rules for all US mines regardless of size, number of employees, commodity mined, or method of extraction. MSHA conducts quarterly inspections to ensure safety and health rules are implemented. US Nuclear Regulatory Commission (NRC) Nuclear Density Gauge Permit The NRC licenses the possession and use of portable gauges and any other processes or devices that use radioactive materials. Montana Department of Environmental Quality (DEQ) 401 Certification (Clean Water Act and Montana Water Quality Act) To certify that any activity requiring a federal license or permit that may result in any discharge into State waters would not cause or contribute to a violation of State surface water quality standards. Montana Pollution Discharge Elimination System (MPDES) Permit (Clean Water Act and Montana Water Quality Act) Authorizes discharge to surface water and groundwater adjacent to surface water Operating Permit (Montana Metal Mine Reclamation Act) To ensure design, operation, closure, monitoring, and bonding of mining operations result in adequate reclamation for post- mining use. Coordinate with the USFS, and other appropriate agencies. Storm Water Pollution Prevention Plan (Clean Water Act and Montana Water Quality Act) To prevent the degradation of state waters from pollutants, such as sediment, industrial chemicals or materials, heavy metals, and petroleum products.
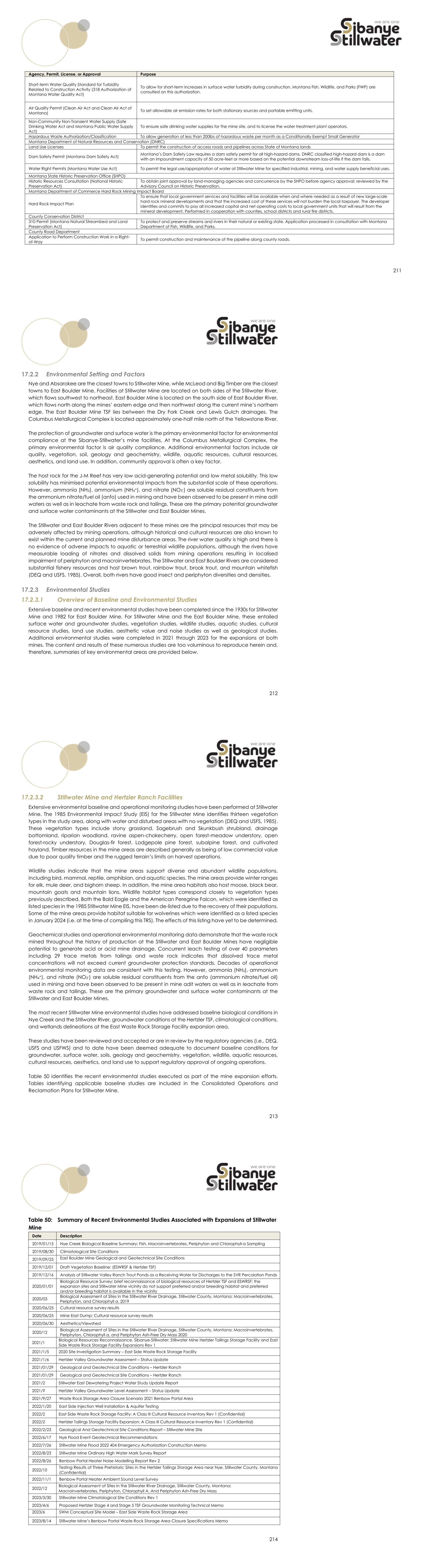
211 Agency, Permit, License, or Approval Purpose Short-term Water Quality Standard for Turbidity Related to Construction Activity (318 Authorization of Montana Water Quality Act) To allow for short-term increases in surface water turbidity during construction. Montana Fish, Wildlife, and Parks (FWP) are consulted on this authorization. Air Quality Permit (Clean Air Act and Clean Air Act of Montana) To set allowable air emission rates for both stationary sources and portable emitting units. Non-Community Non-Transient Water Supply (Safe Drinking Water Act and Montana Public Water Supply Act) To ensure safe drinking water supplies for the mine site, and to license the water treatment plant operators. Hazardous Waste Authorization/Classification To allow generation of less than 200lbs of hazardous waste per month as a Conditionally Exempt Small Generator Montana Department of Natural Resources and Conservation (DNRC) Land Use Licenses To permit the construction of access roads and pipelines across State of Montana lands Dam Safety Permit (Montana Dam Safety Act) Montana’s Dam Safety Law requires a dam safety permit for all high-hazard dams. DNRC classified high-hazard dam is a dam with an impoundment capacity of 50 acre-feet or more based on the potential downstream loss-of-life if the dam fails. Water Right Permits (Montana Water Use Act) To permit the legal use/appropriation of water at Stillwater Mine for specified industrial, mining, and water supply beneficial uses. Montana State Historic Preservation Office (SHPO) Historic Resources Consultation (National Historic Preservation Act) To obtain joint approval by land-managing agencies and concurrence by the SHPO before agency approval; reviewed by the Advisory Council on Historic Preservation. Montana Department of Commerce Hard Rock Mining Impact Board Hard Rock Impact Plan To ensure that local government services and facilities will be available when and where needed as a result of new large-scale hard rock mineral developments and that the increased cost of these services will not burden the local taxpayer. The developer identifies and commits to pay all increased capital and net operating costs to local government units that will result from the mineral development. Performed in cooperation with counties, school districts and rural fire districts. County Conservation District 310 Permit (Montana Natural Streambed and Land Preservation Act) To protect and preserve streams and rivers in their natural or existing state. Application processed in consultation with Montana Department of Fish, Wildlife, and Parks. County Road Department Application to Perform Construction Work in a Right- of-Way To permit construction and maintenance of the pipeline along county roads. 212 Environmental Setting and Factors Nye and Absarokee are the closest towns to Stillwater Mine, while McLeod and Big Timber are the closest towns to East Boulder Mine. Facilities at Stillwater Mine are located on both sides of the Stillwater River, which flows southwest to northeast. East Boulder Mine is located on the south side of East Boulder River, which flows north along the mines’ eastern edge and then northwest along the current mine’s northern edge. The East Boulder Mine TSF lies between the Dry Fork Creek and Lewis Gulch drainages. The Columbus Metallurgical Complex is located approximately one-half mile north of the Yellowstone River. The protection of groundwater and surface water is the primary environmental factor for environmental compliance at the Sibanye-Stillwater’s mine facilities. At the Columbus Metallurgical Complex, the primary environmental factor is air quality compliance. Additional environmental factors include air quality, vegetation, soil, geology and geochemistry, wildlife, aquatic resources, cultural resources, aesthetics, and land use. In addition, community approval is often a key factor. The host rock for the J-M Reef has very low acid-generating potential and low metal solubility. This low solubility has minimised potential environmental impacts from the substantial scale of these operations. However, ammonia (NH3), ammonium (NH4+), and nitrate (NO3-) are soluble residual constituents from the ammonium nitrate/fuel oil (anfo) used in mining and have been observed to be present in mine adit waters as well as in leachate from waste rock and tailings. These are the primary potential groundwater and surface water contaminants at the Stillwater and East Boulder Mines. The Stillwater and East Boulder Rivers adjacent to these mines are the principal resources that may be adversely affected by mining operations, although historical and cultural resources are also known to exist within the current and planned mine disturbance areas. The river water quality is high and there is no evidence of adverse impacts to aquatic or terrestrial wildlife populations, although the rivers have measurable loading of nitrates and dissolved solids from mining operations resulting in localised impairment of periphyton and macroinvertebrates. The Stillwater and East Boulder Rivers are considered substantial fishery resources and host brown trout, rainbow trout, brook trout, and mountain whitefish (DEQ and USFS, 1985). Overall, both rivers have good insect and periphyton diversities and densities. Environmental Studies 17.2.3.1 Overview of Baseline and Environmental Studies Extensive baseline and recent environmental studies have been completed since the 1930s for Stillwater Mine and 1982 for East Boulder Mine. For Stillwater Mine and the East Boulder Mine, these entailed surface water and groundwater studies, vegetation studies, wildlife studies, aquatic studies, cultural resource studies, land use studies, aesthetic value and noise studies as well as geological studies. Additional environmental studies were completed in 2021 through 2023 for the expansions at both mines. The content and results of these numerous studies are too voluminous to reproduce herein and, therefore, summaries of key environmental areas are provided below. 213 17.2.3.2 Stillwater Mine and Hertzler Ranch Facilities Extensive environmental baseline and operational monitoring studies have been performed at Stillwater Mine. The 1985 Environmental Impact Study (EIS) for the Stillwater Mine identifies thirteen vegetation types in the study area, along with water and disturbed areas with no vegetation (DEQ and USFS, 1985). These vegetation types include stony grassland, Sagebrush and Skunkbush shrubland, drainage bottomland, riparian woodland, ravine aspen-chokecherry, open forest-meadow understory, open forest-rocky understory, Douglas-fir forest, Lodgepole pine forest, subalpine forest, and cultivated hayland. Timber resources in the mine areas are described generally as being of low commercial value due to poor quality timber and the rugged terrain’s limits on harvest operations. Wildlife studies indicate that the mine areas support diverse and abundant wildlife populations, including bird, mammal, reptile, amphibian, and aquatic species. The mine areas provide winter ranges for elk, mule deer, and bighorn sheep. In addition, the mine area habitats also host moose, black bear, mountain goats and mountain lions. Wildlife habitat types correspond closely to vegetation types previously described. Both the Bald Eagle and the American Peregrine Falcon, which were identified as listed species in the 1985 Stillwater Mine EIS, have been de-listed due to the recovery of their populations. Some of the mine areas provide habitat suitable for wolverines which were identified as a listed species in January 2024 (i.e. at the time of compiling this TRS). The effects of this listing have yet to be determined. Geochemical studies and operational environmental monitoring data demonstrate that the waste rock mined throughout the history of production at the Stillwater and East Boulder Mines have negligible potential to generate acid or acid mine drainage. Concurrent leach testing of over 40 parameters including 29 trace metals from tailings and waste rock indicates that dissolved trace metal concentrations will not exceed current groundwater protection standards. Decades of operational environmental monitoring data are consistent with this testing. However, ammonia (NH3), ammonium (NH4+), and nitrate (NO3-) are soluble residual constituents from the anfo (ammonium nitrate/fuel oil) used in mining and have been observed to be present in mine adit waters as well as in leachate from waste rock and tailings. These are the primary groundwater and surface water contaminants at the Stillwater and East Boulder Mines. The most recent Stillwater Mine environmental studies have addressed baseline biological conditions in Nye Creek and the Stillwater River, groundwater conditions at the Hertzler TSF, climatological conditions, and wetlands delineations at the East Waste Rock Storage Facility expansion area. These studies have been reviewed and accepted or are in review by the regulatory agencies (i.e., DEQ, USFS and USFWS) and to date have been deemed adequate to document baseline conditions for groundwater, surface water, soils, geology and geochemistry, vegetation, wildlife, aquatic resources, cultural resources, aesthetics, and land use to support regulatory approval of ongoing operations. Table 50 identifies the recent environmental studies executed as part of the mine expansion efforts. Tables identifying applicable baseline studies are included in the Consolidated Operations and Reclamation Plans for Stillwater Mine. 214 Table 50: Summary of Recent Environmental Studies Associated with Expansions at Stillwater Mine Date Description 2019/01/15 Nye Creek Biological Baseline Summary: Fish, Macroinvertebrates, Periphyton and Chlorophyll-a Sampling 2019/08/30 Climatological Site Conditions 2019/09/25 East Boulder Mine Geological and Geotechnical Site Conditions 2019/12/01 Draft Vegetation Baseline: (ESWRSF & Hertzler TSF) 2019/12/16 Analysis of Stillwater Valley Ranch Trout Ponds as a Receiving Water for Discharges to the SVR Percolation Ponds 2020/01/01 Biological Resource Survey; brief reconnaissance of biological resources of Hertzler TSF and ESWRSF; the expansion sites and Stillwater Mine vicinity do not support preferred and/or breeding habitat and preferred and/or breeding habitat is available in the vicinity 2020/03 Biological Assessment of Sites in the Stillwater River Drainage, Stillwater County, Montana: Macroinvertebrates, Periphyton, and Chlorophyll a, 2019 2020/06/25 Cultural resource survey results 2020/06/25 Mine East Dump; Cultural resource survey results 2020/06/30 Aesthetics/Viewshed 2020/12 Biological Assessment of Sites in the Stillwater River Drainage, Stillwater County, Montana: Macroinvertebrates, Periphyton, Chlorophyll a, and Periphyton Ash-Free Dry Mass 2020 2021/1 Biological Resources Reconnaissance, Sibanye-Stillwater: Stillwater Mine Hertzler Tailings Storage Facility and East Side Waste Rock Storage Facility Expansions Rev 1 2021/1/5 2020 Site Investigation Summary – East Side Waste Rock Storage Facility 2021/1/6 Hertzler Valley Groundwater Assessment – Status Update 2021/01/29 Geological and Geotechnical Site Conditions – Hertzler Ranch 2021/01/29 Geological and Geotechnical Site Conditions – Hertzler Ranch 2021/2 Stillwater East Dewatering Project Water Study Update Report 2021/? Hertzler Valley Groundwater Level Assessment – Status Update 2021/9/27 Waste Rock Storage Area Closure Scenario 2021 Benbow Portal Area 2022/1/20 East Side Injection Well Installation & Aquifer Testing 2022/2 East Side Waste Rock Storage Facility: A Class III Cultural Resource Inventory Rev 1 (Confidential) 2022/2 Hertzler Tailings Storage Facility Expansion: A Class III Cultural Resource Inventory Rev 1 (Confidential) 2022/2/23 Geological And Geotechnical Site Conditions Report – Stillwater Mine Site 2022/6/17 Nye Flood Event Geotechnical Recommendations 2022/7/26 Stillwater Mine Flood 2022 404 Emergency Authorization Construction Memo 2022/8/23 Stillwater Mine Ordinary High Water Mark Survey Report 2022/8/26 Benbow Portal Heater Noise Modelling Report Rev 2 2022/10 Testing Results of Three Prehistoric Sites in the Hertzler Tailings Storage Area near Nye, Stillwater County, Montana (Confidential) 2022/11/1 Benbow Portal Heater Ambient Sound Level Survey 2022/12 Biological Assessment of Sites in the Stillwater River Drainage, Stillwater County, Montana: Macroinvertebrates, Periphyton, Chlorophyll A, And Periphyton Ash-Free Dry Mass 2023/3/30 Stillwater Mine Climatological Site Conditions Rev 1 2023/4/6 Proposed Hertzler Stage 4 and Stage 5 TSF Groundwater Monitoring Technical Memo 2023/6 SWM Conceptual Site Model – East Side Waste Rock Storage Area 2023/8/14 Stillwater Mine’s Benbow Portal Waste Rock Storage Area Closure Specifications Memo

215 Date Description 2023/8 Nye Creek Morphology Assessment Final Report 2023/9/21 Nye Creek Biological Baseline Summary: Fish, Macroinvertebrates, Periphyton and Chlorophyll-a Sampling Rev 2 2023/10/6 East Side Waste Rock Storage Facility Storm Water Mixing Analysis 2023/10/30 East Side Waste Rock Storage Facility Proposed Expansion Closure Analysis Rev 2 2023/10 East Side Waste Rock Storage Facility and Hertzler Tailings Storage Facility Expansion Vegetation Baseline Rev 1 2023/11 Visual Assessment of the East Side Waste Rock Storage Facility and Hertzler Ranch Tailings Storage Facility Expansion – Stillwater Mine Baseline Technical Memorandum 2023/11 Stillwater Mine MA 014 Soil Baseline Characterization Rev 1 2023/12/21 Final 2023 OHWM Delineation Report 2024/2/7 Analyses of June 2022 Flood Flows at Stillwater and East Boulder Mines 2024/3/1 Sibanye-Stillwater 2023 Groundwater Dependent Ecosystem (GDE) Inventory Nye Mine – East Blitz Project 2023/12 SWM Biological Monitoring Report 2024/2/7 Analyses of June 2022 Flood Flows at Stillwater and East Boulder Mines 2024/3/1 Sibanye-Stillwater 2023 Groundwater Dependent Ecosystem (GDE) Inventory Nye Mine – East Blitz Project 17.2.3.3 East Boulder Mine Baseline data for East Boulder Mine was collected between 1982 and 1992 to support the 1992 Environmental Impact Statement. Additional baseline data was collected between 1997 and 2023 to support water management and additional expansions at the mine. The geology of East Boulder Mine comprises unconsolidated alluvium and glacial deposits overlying Palaeozoic sedimentary bedrock and igneous bedrock of the Stillwater Complex (DEQ and USFS, 2020). Groundwater in the Stillwater Complex occurs primarily in an extensive network of joints, fractures and fault zones resulting in slow groundwater flow. The glacial deposits vary in grain size and are a mixture of boulder, gravel, sand and silt sized particles, which result in variable groundwater flow rates. The majority of recharge to the underlying glacial deposits and bedrock is understood to occur through the alluvial deposits (DEQ and USFS, 2020). Groundwater occurs beneath the East Boulder Mine at depths from 120ft to 150ft below the ground surface but follows the ground surface and becomes shallower near the East Boulder River (DEQ and USFS, 2020). Groundwater flows from southeast to northwest parallel to the axis of the valley that contains the East Boulder Mine. The groundwater quality in the East Boulder Mine footprint has low total dissolved solids concentrations and low concentrations of sulphate, chloride and heavy metals. The East Boulder River adjacent to the East Boulder Mine is characterized by riffles and pools. Peak flows in the East Boulder River result from snowmelt and precipitation. The river loses water to the groundwater system northeast of the permit area and gains water from the groundwater system farther downstream along the East Boulder Mine. The water quality of the East Boulder River is good, with low total dissolved solids concentrations. Total dissolved solids concentrations vary with river flow; higher total dissolved solids concentrations are measured during times of lower flow in the winter and early spring. Sampling of the aquatic environment of the East Boulder River for thirteen years identified that the river had 216 excellent biotic integrity and no impairment of water quality of biological integrity resulting from East Boulder Mine operations has been identified. The Lewis Gulch drainage has surface water flow along portions of the drainage in response to snowmelt. Three springs along the Dry Fork drainage flow for distances before infiltrating into the ground. Flowing surface water did not intercept the East Boulder River during baseline studies. The surface water in the Lewis Gulch and Dry Fork drainages is high quality with low total dissolved solids and metals concentrations. Four distinct plant communities are located within the East Boulder Mine boundary. These include Mature Douglas Fir Forest, Early Seral Douglas Fir Forest, Reclaimed Grassland, and Meadow Grassland. No threatened or endangered plant species were identified as occurring at the East Boulder Mine. One sensitive species (Whitebark pine) was identified in the area of the proposed future disturbance at East Boulder Mine. The most recent East Boulder Mine environmental studies have addressed baseline environmental conditions, cultural resources surveys, wetland surveys, mine groundwater inflow, climatological conditions, and biological assessment of the East Boulder River. The Class III cultural resource inventory study completed in 2021 identified from records seven previously identified cultural sites within the study area but did not identify evidence of those sites in the recent field survey of over 315 acres and no further survey work was recommended. The survey did not identify any sites that would preclude the planned expansions. Wildlife studies indicate that the area around East Boulder Mine supports diverse and abundant wildlife populations. The mine areas provide winter ranges for elk and mule deer. In addition, the mine area habitats host moose, black bear, grizzly bear, and wild trout. Brown trout and rainbow trout are the most abundant species in the East Boulder River (DEQ and USFS, 2012a). The recent baseline study Construction and operation of the TSF and Dry Fork waste rock storage facilities would result in short- term and long-term impacts on wildlife use patterns, wildlife habitat quantities, and vegetative composition. The project may decrease wildlife forage production and availability in the short term due to the removal of vegetation. Possible adverse effects to aquatic resources in the East Boulder River or the perennial or ephemeral streams could result from soil erosion / storm water discharges occurring during construction. However, wildlife carrying capacity may increase in the long-term after the project is complete and the project area is revegetated. Effective January 2024, the USF&W Service listed the wolverine as a threatened species. Some of the East Boulder Mine site areas have been identified as having the potential for wolverine habitat. Impacts have yet to be determined. All ecological, geological, hydrological, geotechnical, archaeological, and climatological studies appear to be completed for the Lewis Gulch TSF Stage 4 and 5 expansions, the Dry Fork Waste Rock Storage Area and associated haul road and bridge. 217 The baseline studies have been reviewed and accepted by the regulatory agencies after having been deemed adequate to document baseline conditions for groundwater, surface water, soil, geology and geochemistry, vegetation, wildlife, aquatic resources, cultural resources, aesthetics, and land use to support regulatory approval of operations. Table 51 identifies the recent environmental studies executed at East Boulder Mine. Tables identifying applicable baseline studies are included in the Consolidated Operations and Reclamation Plans for East Boulder Mine. Table 51: Summary of Recent Environmental Studies Associated with Expansions at East Boulder Mine Date Description 2019/09/25 Geological and Geotechnical Site Conditions 2020/12 Biological Assessment of Sites on the East Boulder River: Sweet Grass County Montana, 2020 2021/10/14 Climatological Site Conditions 2021/05 Lower Lewis Gulch and Dry Fork Sites Wetland Survey 2021/05 Lewis Gulch and Dry Fork Creek Updated Baseline Hydrogeologic Monitoring Report 2021/06/21 East Boulder Mine Groundwater Inflow Analysis 2021/08 East Boulder Expansion: A Class III Cultural Resource Inventory in Sweet Grass County, Montana 2021/08 Baseline Environmental Survey at the East Boulder Mine 2021/10/14 East Boulder Mine Climatological Site Conditions 2021/11 Monitoring of Chlorophyll-a and Periphyton Ash-Free Dry Mass on the East Boulder River, Sweet Grass County Montana, 2021 2022/1/12 Closure Analysis of the East Boulder Mine Stage 6 Embankment Underdrain Collection System 2022/1/20 2022 CGNF Site Wide Biological Opinion 2022/1/28 GNA Water Treatment Optimization Memo 2022/2/11 EBM Future TSF and WRSA Options Assessment 2022/3/9 Updated Closure Analysis of the East Boulder Mine Waste Rock Storage Area Underdrain Collection System with Passive Water Treatment 2022/3 East Boulder Mine 2020 Water Management Plan Revision 1 2022/8 Energy Use Assessment for Sibanye-Stillwater Mine Sites 2022/9/9 East Boulder Amendment 4 Wetlands Delineation Report 2022/10/24 East Boulder Tailings Materials Testing Report Final 2022/11/7 East Boulder Mine Subsidence Adherence Memo 2022/12/9 East Boulder Mine Major Amendment 004 Supplemental Delineation Report 2022/12 Biological Assessment of Sites on the East Boulder River: Sweet Grass County, Montana, 2022 2022/12 East Boulder Mine 2022 Groundwater Dependent Ecosystem Survey Phase 1 2023/1/6 East Boulder Mine Filtered Tailings Summary Report 2023/1/11 East Boulder Mine Filtered Tailings Options Study 2023/2 Biodiversity Impact Assessment for 2021, US PGM Operations 2023/3/27 East Boulder Mine Whole Mill Tailings as Back Fill Memo 2023/11 East Boulder Mine 2023 Nitrogen Loading Analysis Memorandum 2023/11/27 East Boulder Mine Amendment 004 EIS – Tech Memorandum 1 – Review of Dry Fork Waste Rock Storage Area Nitrate Attenuation and Potential Duration of Active Water Treatment 2023/11/27 East Boulder Mine Amendment 004 EIS – Technical Memorandum No. 2 – Review of Dry Fork Waste Rock Storage Area Reclamation and Capping Alternatives 2023/11/27 East Boulder Mine Amendment 004 EIS – Technical Memorandum No. 3 – Tailings Management Alternatives to Slurried Impoundment Deposition 2024/2/7 Analyses of June 2022 Flood Flows at Stillwater and East Boulder Mines 218 17.2.3.4 Metallurgical Complex No baseline studies, environmental studies nor impact assessments specific to the Columbus Metallurgical Complex (smelter and base metal refinery) were completed for permitting purposes as these were not required by the regulatory authorities. As there was no public land interaction and associated permitting, an EIS or similar studies were not required for construction and operation of the smelter and base metal refinery. Permitting Status and Compliance 17.2.4.1 Overview of Permitting Status Permits from the Federal, State and local agencies for the Sibanye-Stillwater US PGM Operations include permits from the State of Montana (e.g., mine permit, air quality permit, stormwater discharge permits, water discharge permits, exploration permit, and potable water supply permit, dam safety and water rights), and permits from the US Environmental Protection Agency (EPA) and US Forest Service (USFS). The county conservation districts provide permits to protect and preserve streams and rivers, whereas the road departments provide permits for access to conduct activities in road rights of way. Table 52 summaries the existing permits and their status for the Sibanye-Stillwater US PGM Operations. Mining occurs on Federal lands managed by the USFS and on private land. Most of the private land is historic patented mining claims which are now private. Those private lands not currently owned by Sibanye-Stillwater are leased. Federal lands and permission to access the surface for mining purposes is applied for and granted by the USFS in conjunction with the NEPA process and technical application to the USFS and DEQ. The Qualified Persons conclude that most of the key approvals have been granted and are reasonably anticipated to continue to be granted for mining and processing operations for the foreseeable future. 17.2.4.2 Stillwater Mine and Hertzler Ranch Facilities Specific permitting requirements vary widely by agency and regulated media and these are described in USFS and DEQ regulations and associated guidance. All necessary permits and approvals are in place and adequate for existing operations. Permits and licenses requiring renewal in FY2023 have been developed in a timely manner and submitted to the regulatory agencies for approval and efforts initiated for permits and licenses needing renewal in FY2024. Permits and approvals are tracked and renewal dates, schedules, timeframes and requirements for continued compliance are addressed in a timely manner with few exceptions. Reclamation bonding is required under the Operating Permit (No. 00118). Bonding is addressed in the Section 0 (Reclamation Plans and Costs). Permitting for planned expansions have been initiated in a timely manner and appear to be on track for schedule changes in operations. There are three current violations of the Operating Permit No. 00118 and two of the Exploration License No. 00046 relating to nitrate concentrations in groundwater and surface water, and submittal of Water Resource Management Reports (WRMR) and Biological Monitoring Reports beyond their prescribed

219 deadlines. These violations were issued between December 2019 and February 2020. The December 2019 and February 2020 DEQ letters identified violations related to the following: Stillwater (Operating Permit No. 00118): o 12/13/19 -Stillwater Mine: 00039- Exceedances of nitrate+nitrite levels in East Side Waste Rock Storage Facility groundwater monitoring well MW-18A (>10mg/l), which are located downgradient of the East Side Waste Rock Storage Facility and up-gradient of the Stillwater River. Elevated concentrations relate to seepage of meteoric waters through the East Side Waste Rock Storage Facility materials that accumulate nitrogen from traces of residual anfo. Resolved through AOC; 00039 – Failing to submit a plan (or third-party review/report) for agency review and approval and falling to take prompt and appropriate remedial corrective measures to address the exceedance in HMW-10 at the Hertzler TSF. Resolved through AOC; 00039- Failure to submit required 2018 Water Resource Monitoring Report and Biological Monitoring Reports by the June deadlines. Resolved through corrective action and required biological monitoring took place in 2020. o 1/30/2020 – Benbow; Exploration Permit 0046; o 00040- Exceedances of nitrate+nitrite levels in BMW-3. Elevated concentrations relate to seepage of meteoric waters through the Benbow Waste Rock Storage Area materials that accumulate nitrogen from traces of residual anfo. Resolved through AOC; o 00040- Exceedance of Numeric Nutrient Standard in Benbow Mill Site Creek (BMSCR). Resolved through corrective action and installation of Permeable Reactive Barrier and initiation of BMW-3 as a pump back well; o 00040- 2018 Annual Water Resources Monitoring Report was submitted on December 31, 2019, six months after due date. Resolved through corrective action; Water Resources Monitoring Plan Submitted to DEQ; o 02/04/2020 Stillwater Mine: 00041 – Exceedances of nitrate+nitrite levels in East Side Waste Rock Storage Facility groundwater monitoring well MW-14A. Dismissed based on CORP Stipulation 21; 00041- Failing to notify Agency of any corrective actions taken to address the change in groundwater Quality in MW-14A. Resolved through AOC; 00041-The 2018 Annual Water Resources Monitoring Report was submitted on December 31, 2019, six months after due date. Resolved through corrective action. Water Resources Monitoring Plan submitted to DEQ; 00041- The 2018 Annual Biological Monitoring Report was submitted on December 31, 2019, six months after due date. Resolved through corrective action Biological Monitoring Plan submitted to DEQ; o 03/25/2022 – Hertzler: Exceedance of Water Quality Standard (HMW-16). Resolved through AOC; Departure from approved Plan: Water Resource Monitoring Plan. Resolved through AOC; o 06/07/2022 Stillwater Valley Ranch (SVR): 00073- Exceedance of Water Quality Standard SVR Well Nitrate +Nitrite 10mg/l and Non-degradation Standard of 7.5mg/l. Resolved through AOC; o 09/06/2023 Stillwater Mine: 220 MPDES Permit MT0024716 – Montana DEQ Water Protection Bureau issued a violation letter regarding self-reporting noncompliance reports on June 20, 2023, due to a tear in Pond 3 liner, August 1, 2023, when pond 2 overflowed into pond 3 and finally on August 8, 2023, when the water treatment plant cell overtopped and treated water went into Mountain View Creek. Stillwater Mine initiated implementation of corrective actions at the East Side Waste Rock Storage Facility in 2016 with agency knowledge, although approved plans were not formally submitted or approved. Although water quality standards have been exceeded due to seepage from the East Side Waste Rock Storage Facility, no beneficial uses in the Stillwater River have been impacted or compromised with respect to surface water quality or residential groundwater supplies. DEQ has stated that the resolution of these violations will be dependent on the timely initiation of the meeting with DEQ and USFS, the timely implementation of remedial corrective actions, and the submittal of documentation of the corrective actions specified in the Consolidated Operations and Reclamation Plan. Corrective actions at the East Side Waste Rock Storage Facility have been initiated since 2016 and include synoptic monitoring, phased East Side Waste Rock Storage Facility lining and Nitrogen Collection Pond installation, consultant evaluation of water quality changes (2018 and 2019) and initiation of in situ treatment of nitrogen with methanol injection. Corrective actions at the Hertzler TSF include repair of the liner tear (during 2015), installation of groundwater capture French drains and pump back system, installation of in-situ remediation, synoptic and biological monitoring on Stillwater River at Hertzler Ranch, and additional well installations. Corrective actions have been implemented at the Benbow Waste Rock Storage Facility and Benbow Mill Spring Creek. Corrective actions include synoptic monitoring of Benbow Mill Site Creek and Little Rocky Creek, installation of groundwater collection vaults for foundation drains (beneath waste rock storage area and WTP2 feed pond) and pump back of collected groundwater for treatment, as well as installation of a permeable reactive barrier (PRB) treatment system using methanol injection. Monitoring data indicates water quality concentrations in the creeks have returned to below regulatory levels, indicating successful implementation of the PRB, although groundwater concentrations remain above regulatory standards. The Qualified Persons conclude that the corrective actions implemented appear to have reasonable effectiveness and, where water quality has not yet been restored to below levels of regulatory concern, water quality concentration trends show stable to downward progression. Most of the violations have been resolved and closed while a few remain open at the time of the report. Closeout of the remaining violations is pending further monitoring and regulatory acceptance of corrective action completion. 17.2.4.3 East Boulder Mine Permits required for current operations at East Boulder Mine include permits from the State of Montana (e.g., mine permit, air quality permit, stormwater discharge permits, water discharge permits, exploration permit, and potable water supply permit), and permits from the Federal government including the EPA and USFS. There are two open regulatory violations at the time of compiling this TRS and these are described as follows: 221 09/12/2023: o Notice of Non-Compliance – USFS issued a Notice of Noncompliance for Unauthorized activities on NFS lands associated with the BVR Heat Exchanger Project. Project site access road encroached onto the USFS Swan 2 unpatented claim; 09/14/2023: o 00102-Montana DEQ Hard Rock Mining Bureau issued a violation for ‘'Departure from Conditions of Approved Operating and Reclamation Pla'. In MR23‐002, SMC had committed to overland transportation of construction equipment to the vent raises using an access path solely on SMC patented claims. Furthermore, no reclamation of the path was included in the revision or accounted for in the reclamation bond, since it was intended to be an overland access path without removal of timber. Due to winter conditions, access to the BVR Heat exchanger locations referenced above is not available until after spring snow melt. Therefore, final reclamation of the location to conform to the two violations listed above cannot be completed until spring 2024. Plans are in place to execute reclamation in spring of 2024. Federal permits from the EPA are for Class V groundwater injection wells. These Class V injection well permits address the following: Recycling of water back into the mine (MT5000-05150); Disposal of septic system water (MT50000-06439); Disposal of treated adit water from the underground workings (MT50000-11713); and Injection of methanol into shallow alluvial groundwater for in situ biological reduction of nitrates (MT50000-008511). An amendment to Operating Permit No. 00149 for the development of the Lewis Gulch TSF and the Dry Fork WRSF has been submitted to the Agencies. This amendment includes a 404 Permit with the US Army Corps of Engineers (ACOE) for the waste rock haulage crossing. The DEQ and USFS have prepared an Environmental Impact Statement for the Lewis Gulch TSF and the Dry Fork WRSF Expansion Project, and the public comment period has ended and a ROD is expected to be issued second quarter 2024. East Boulder Mine is approved to discharge from three outfalls into the East Boulder River and groundwater in an alluvial aquifer under MPDES Permit MR-0026808. A permitted injection well for treated mine water at the Yates Gravel Pit is permitted and infrastructure is in place but as of this review, the system has not yet been operated. Groundwater monitoring between 2005 and 2010 detected concentrations of nitrate as nitrogen greater than the non-degradation level established in the MPDES permit in three monitoring wells downgradient of the tailings storage facility and the infiltration pond. The DEQ found the mine out of compliance with the MPDES permit (MT0026808), triggering SMC (the owner at the time) and the DEQ to enter into an Administrative Order on Consent (Docket No., WQA-10-04). A compliance plan was submitted to DEQ and approved to establish a series of corrective actions to address the exceedance of the MPDES nitrate as nitrogen limits. In addition, a groundwater capture and pump back system was constructed and became operational in 2011. In situ treatment wells were installed and reagent was injected into injection wells to reduce nitrates as nitrogen concentrations. A TSF embankment underdrain system was also installed to collect meteoric water through the embankment rock fill and 222 route the water back to the supernatant pond. An outer embankment liner was installed along the outer TSF Stage 3 slope to reduce infiltration of meteoric water through the embankment rock. As a result of the corrective actions, nitrate as nitrogen concentrations in downgradient monitoring wells were reduced to 35% of the non-degradation standard for groundwater in 2017. In 2017, the DEQ approved a mixing zone which resulted in a zone across which cumulative contributions from operational sources within the permit boundary are addressed. In January 2018, DEQ found that the Sibanye-Stillwater (SMC) is in compliance with the MPDES Permit and that the terms of the Consent Order were satisfied. The Qualified Persons conclude that long-term groundwater and surface water restoration and protection from operational impacts are ongoing and well managed, and compliance is likely to be achieved and maintained. 17.2.4.4 Columbus Metallurgical Complex The smelter at the Columbus Metallurgical Complex has only two permits, namely a Montana Air Quality Permit (#2635-17) from the DEQ Air Resources Bureau, and a MPDES Permit (-000469) with the DEQ Water Protection Bureau, both which are current and in good standing. The Qualified Persons understand that these permits are current and not due for renewal for several years. The Air Quality Permit (MAQP No. 2635-19) limits air emissions based on measured opacity, particulate emissions (PM10) from baghouse filters, and Sulphur dioxide (SO2) emissions based on maximum allowed smelter concentrate throughput (≤59 500 tons/year), precious metals recyclable material through put (≤15 000 tons/year), gypsum production (≤25 000 tons/rolling 12-month period), smelter slag production (≤60 000 tons/rolling 12-month period), the amount of waste ore for lining the slag pits (≤40 000 tons/rolling 12-month period), and emergency back-up generator run time (≤500 hours/rolling 12-month period). Emissions testing requirements of the Air Permit include: Particulate and opacity performance source tests every two years on the smelting circuit main stack and concentrate drying circuit main stack; Particulate and opacity performance source tests every five years on the process baghouse for the nickel sulphate crystal dryer; and SO2 performance source testing on the smelting circuit stack every five years. In addition, Continuous Emissions Monitoring System (CEMS) to monitor stack volumetric flow rate and record SO2 emissions are operated and maintained as required. Reporting of testing and monitoring results as well as material inventories is provided annually. The MPDES permit for stormwater contains non-numeric technology-based effluent limits and numeric water quality-based effluent limits. Non-numeric technology-based effluent limits include best management practices for managing materials to minimize contact with site waters, control site materials from egress, maintenance and erosion control practices. Numeric water quality-based effluent limits are established as well as benchmark and outfall monitoring requirements. However, the smelter operates in a zero-discharge mode with all stormwater contained onsite, following the storm

223 water pollution prevention plan and best management practices with all storm water retained via use of berms, ditches and percolation ponds. All permits have been renewed or revised in a timely manner. There are no performance or reclamation bonds associated with this facility. 224 Table 52: Permits Status Summary for the Sibanye-Stillwater US PGM Operations Site Operating Permit and Type Status Permit Number Regulatory Agency Discharge Type Date Issued Renewal Date Description Stillwater Mine Operating Permit and Type Status Permit Number Regulatory Agency Discharge Type Date Issued Renewal Date Description Original Permits Plan of Operations (POO) Active 118 USFS Custer Gallatin National Forest (CGNF)/ DEQ Hard Rock Mining Program Feb-90 NA Plan of Operations Original (EIS) Record of Decision Active 118 USFS CGNF/ DEQ Hard Rock Mining Program Jan-86 NA Mine Permit Stillwater Mine Operating Permit Active 118 USFS CGNF/ DEQ Hard Rock Mining Program Jan-86 NA Operating Permit #00118 - Approved by ROD in December 1985 Amendments Operating Permit Amendment No. 1 Active 118 USFS CGNF/ DEQ Hard Rock Mining Program Jun-86 NA Plant site relocation Operating Permit Amendment No. 2 Active 118 USFS CGNF/ DEQ Hard Rock Mining Program Sep-86 NA Sand borrow area approved Operating Permit Amendment No. 3 Active 118 USFS CGNF/ DEQ Hard Rock Mining Program Jan-87 NA Second sand borrow area approved Operating Permit Amendment No. 4 Active 118 USFS CGNF/ DEQ Hard Rock Mining Program Feb-87 NA Nye Tailings Impoundment toe dike relocation Operating Permit Amendment No. 5 Active 118 USFS CGNF/ DEQ Hard Rock Mining Program Mar-89 NA East-side development approved (increase permit area) Operating Permit Amendment No. 6 Active 118 USFS CGNF/ DEQ Hard Rock Mining Program Jul-89 NA Temporary sand pipeline approved 225 Site Operating Permit and Type Status Permit Number Regulatory Agency Discharge Type Date Issued Renewal Date Description Operating Permit Amendment No. 7 Active 118 USFS CGNF/ DEQ Hard Rock Mining Program Nov-90 NA Adit relocated, 3 perc ponds added, 5 monitoring wells added Operating Permit Amendment No. 8 Active 118 USFS CGNF/ DEQ Hard Rock Mining Program Sep-92 NA Facilities expansion, production increase to 2000 ton/day Operating Permit Amendment No. 9 Active 118 USFS CGNF/ DEQ Hard Rock Mining Program Mar-96 NA East-West mining areas connected with haulage way (mining under Stillwater River) Operating Permit Amendment No. 10 Active 118 USFS CGNF/ DEQ Hard Rock Mining Program Nov-98 NA Hertzler expansion approved and production cap eliminated Operating Permit Amendment No. 11 Active 118 USFS CGNF/ DEQ Hard Rock Mining Program Aug-12 NA Revised Water Management Plan at Stillwater, Hertzler LAD (closure/post-closure), Boe Ranch LAD (operations/closure/post- closure) Stillwater Mine Operating Permit Amendment No. 12 Active 118 USFS CGNF/ DEQ Hard Rock Mining Program Jul-10 NA Addition of Hertzler LAD Pivot #7 226 Site Operating Permit and Type Status Permit Number Regulatory Agency Discharge Type Date Issued Renewal Date Description Operating Permit Amendment No. 13 Active 118 USFS CGNF/ DEQ Hard Rock Mining Program May-23 NA Incorporated the Benbow Exploration Project into Mine Permit 00118 Operating Permit Amendment No. 14 Pending 118 USFS CGNF/ DEQ Hard Rock Mining Program Pending Minor Revisions Operating Permit Minor Revision 89-001 Active 118 USFS CGNF/ DEQ Hard Rock Mining Program Dec-89 NA Waste rock haulage railroad spur at 5150W Adit Operating Permit Minor Revision 90-001 Active 118 USFS CGNF/ DEQ Hard Rock Mining Program Jul-90 NA 5200E Ventilation Adit with auxiliary facilities Operating Permit Minor Revision 90-002 Active 118 USFS CGNF/ DEQ Hard Rock Mining Program Sep-90 NA Sediment basin construction (no new permit area) Operating Permit Minor Revision 91-001 Active 118 USFS CGNF/ DEQ Hard Rock Mining Program Jun-91 NA 5200E Portal, spur road, laydown, and access road Operating Permit Minor Revision 91-002 Active 118 USFS CGNF/ DEQ Hard Rock Mining Program Oct-91 NA Compressor pipeline crossing at Stillwater River Bridge Operating Permit Minor Revision 92-001 Active 118 USFS CGNF/ DEQ Hard Rock Mining Program Mar-92 NA 5000E loci haul rail track extension Operating Permit Minor Revision 92-002 Active 118 USFS CGNF/ DEQ Hard Rock Mining Program 1992 Permanent 5400E waste rock pile, eliminate laydown
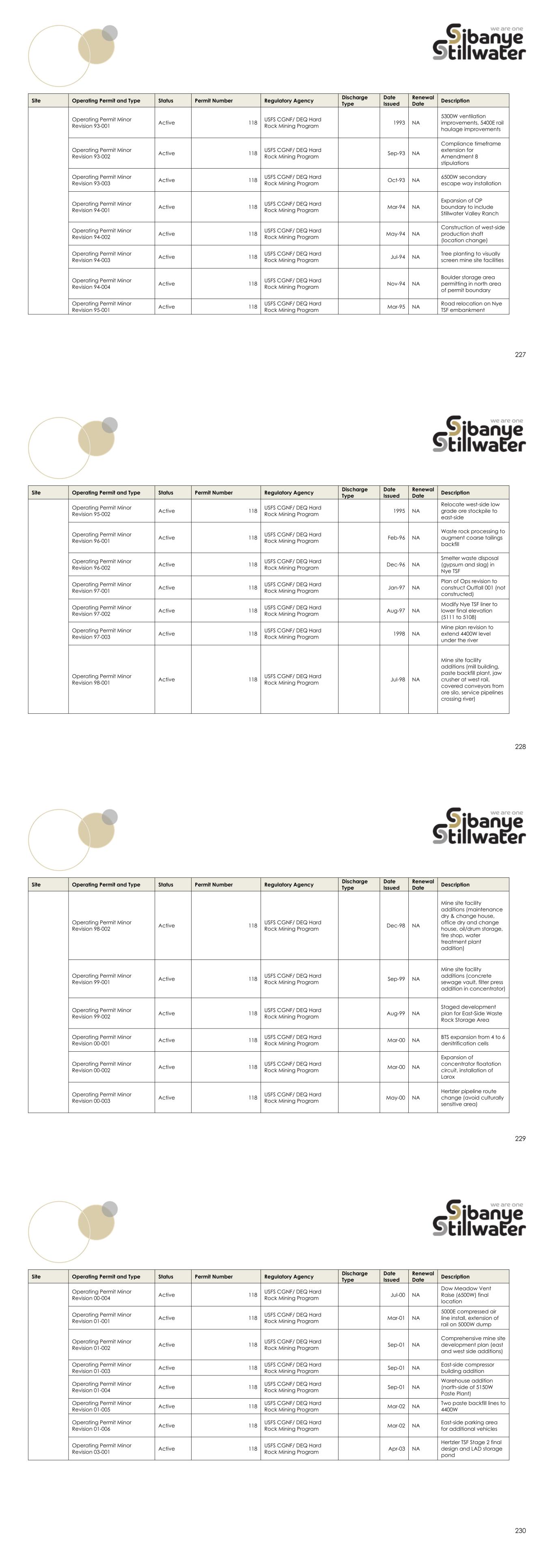
227 Site Operating Permit and Type Status Permit Number Regulatory Agency Discharge Type Date Issued Renewal Date Description Operating Permit Minor Revision 93-001 Active 118 USFS CGNF/ DEQ Hard Rock Mining Program 1993 NA 5300W ventilation improvements, 5400E rail haulage improvements Operating Permit Minor Revision 93-002 Active 118 USFS CGNF/ DEQ Hard Rock Mining Program Sep-93 NA Compliance timeframe extension for Amendment 8 stipulations Operating Permit Minor Revision 93-003 Active 118 USFS CGNF/ DEQ Hard Rock Mining Program Oct-93 NA 6500W secondary escape way installation Operating Permit Minor Revision 94-001 Active 118 USFS CGNF/ DEQ Hard Rock Mining Program Mar-94 NA Expansion of OP boundary to include Stillwater Valley Ranch Operating Permit Minor Revision 94-002 Active 118 USFS CGNF/ DEQ Hard Rock Mining Program May-94 NA Construction of west-side production shaft (location change) Operating Permit Minor Revision 94-003 Active 118 USFS CGNF/ DEQ Hard Rock Mining Program Jul-94 NA Tree planting to visually screen mine site facilities Operating Permit Minor Revision 94-004 Active 118 USFS CGNF/ DEQ Hard Rock Mining Program Nov-94 NA Boulder storage area permitting in north area of permit boundary Operating Permit Minor Revision 95-001 Active 118 USFS CGNF/ DEQ Hard Rock Mining Program Mar-95 NA Road relocation on Nye TSF embankment 228 Site Operating Permit and Type Status Permit Number Regulatory Agency Discharge Type Date Issued Renewal Date Description Operating Permit Minor Revision 95-002 Active 118 USFS CGNF/ DEQ Hard Rock Mining Program 1995 NA Relocate west-side low grade ore stockpile to east-side Operating Permit Minor Revision 96-001 Active 118 USFS CGNF/ DEQ Hard Rock Mining Program Feb-96 NA Waste rock processing to augment coarse tailings backfill Operating Permit Minor Revision 96-002 Active 118 USFS CGNF/ DEQ Hard Rock Mining Program Dec-96 NA Smelter waste disposal (gypsum and slag) in Nye TSF Operating Permit Minor Revision 97-001 Active 118 USFS CGNF/ DEQ Hard Rock Mining Program Jan-97 NA Plan of Ops revision to construct Outfall 001 (not constructed) Operating Permit Minor Revision 97-002 Active 118 USFS CGNF/ DEQ Hard Rock Mining Program Aug-97 NA Modify Nye TSF liner to lower final elevation (5111 to 5108) Operating Permit Minor Revision 97-003 Active 118 USFS CGNF/ DEQ Hard Rock Mining Program 1998 NA Mine plan revision to extend 4400W level under the river Operating Permit Minor Revision 98-001 Active 118 USFS CGNF/ DEQ Hard Rock Mining Program Jul-98 NA Mine site facility additions (mill building, paste backfill plant, jaw crusher at west rail, covered conveyors from ore silo, service pipelines crossing river) 229 Site Operating Permit and Type Status Permit Number Regulatory Agency Discharge Type Date Issued Renewal Date Description Operating Permit Minor Revision 98-002 Active 118 USFS CGNF/ DEQ Hard Rock Mining Program Dec-98 NA Mine site facility additions (maintenance dry & change house, office dry and change house, oil/drum storage, tire shop, water treatment plant addition) Operating Permit Minor Revision 99-001 Active 118 USFS CGNF/ DEQ Hard Rock Mining Program Sep-99 NA Mine site facility additions (concrete sewage vault, filter press addition in concentrator) Operating Permit Minor Revision 99-002 Active 118 USFS CGNF/ DEQ Hard Rock Mining Program Aug-99 NA Staged development plan for East-Side Waste Rock Storage Area Operating Permit Minor Revision 00-001 Active 118 USFS CGNF/ DEQ Hard Rock Mining Program Mar-00 NA BTS expansion from 4 to 6 denitrification cells Operating Permit Minor Revision 00-002 Active 118 USFS CGNF/ DEQ Hard Rock Mining Program Mar-00 NA Expansion of concentrator floatation circuit, installation of Larox Operating Permit Minor Revision 00-003 Active 118 USFS CGNF/ DEQ Hard Rock Mining Program May-00 NA Hertzler pipeline route change (avoid culturally sensitive area) 230 Site Operating Permit and Type Status Permit Number Regulatory Agency Discharge Type Date Issued Renewal Date Description Operating Permit Minor Revision 00-004 Active 118 USFS CGNF/ DEQ Hard Rock Mining Program Jul-00 NA Dow Meadow Vent Raise (6500W) final location Operating Permit Minor Revision 01-001 Active 118 USFS CGNF/ DEQ Hard Rock Mining Program Mar-01 NA 5000E compressed air line install, extension of rail on 5000W dump Operating Permit Minor Revision 01-002 Active 118 USFS CGNF/ DEQ Hard Rock Mining Program Sep-01 NA Comprehensive mine site development plan (east and west side additions) Operating Permit Minor Revision 01-003 Active 118 USFS CGNF/ DEQ Hard Rock Mining Program Sep-01 NA East-side compressor building addition Operating Permit Minor Revision 01-004 Active 118 USFS CGNF/ DEQ Hard Rock Mining Program Sep-01 NA Warehouse addition (north-side of 5150W Paste Plant) Operating Permit Minor Revision 01-005 Active 118 USFS CGNF/ DEQ Hard Rock Mining Program Mar-02 NA Two paste backfill lines to 4400W Operating Permit Minor Revision 01-006 Active 118 USFS CGNF/ DEQ Hard Rock Mining Program Mar-02 NA East-side parking area for additional vehicles Operating Permit Minor Revision 03-001 Active 118 USFS CGNF/ DEQ Hard Rock Mining Program Apr-03 NA Hertzler TSF Stage 2 final design and LAD storage pond
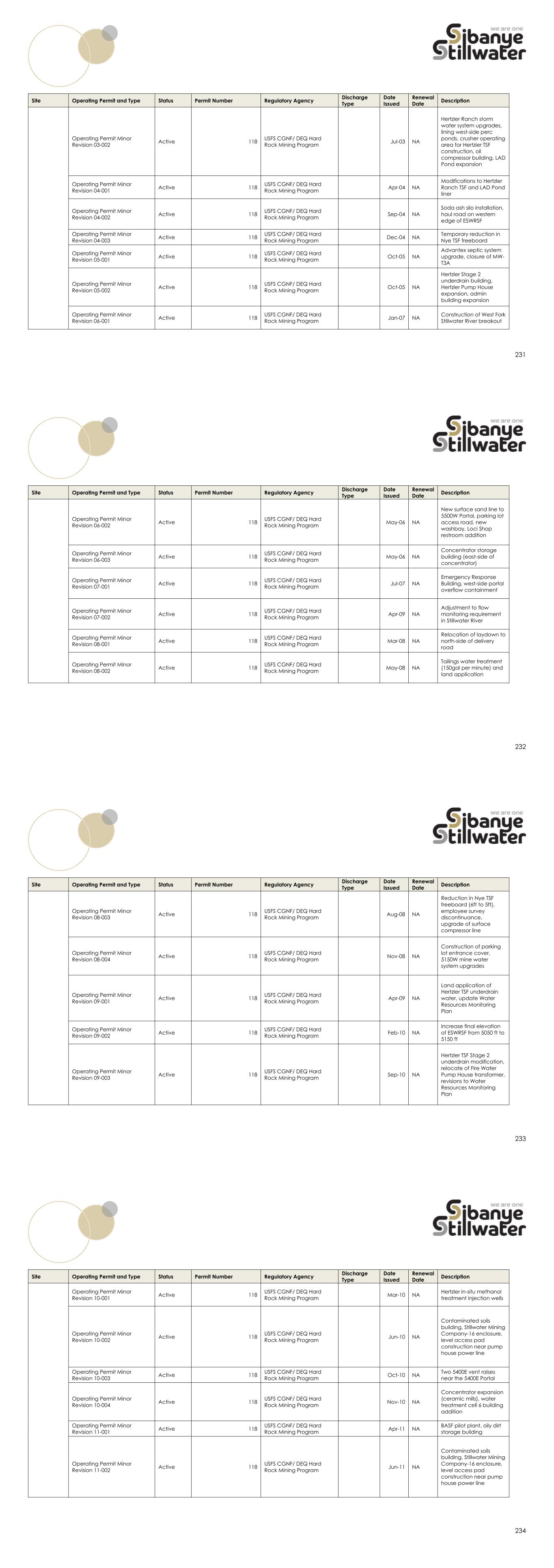
231 Site Operating Permit and Type Status Permit Number Regulatory Agency Discharge Type Date Issued Renewal Date Description Operating Permit Minor Revision 03-002 Active 118 USFS CGNF/ DEQ Hard Rock Mining Program Jul-03 NA Hertzler Ranch storm water system upgrades, lining west-side perc ponds, crusher operating area for Hertzler TSF construction, oil compressor building, LAD Pond expansion Operating Permit Minor Revision 04-001 Active 118 USFS CGNF/ DEQ Hard Rock Mining Program Apr-04 NA Modifications to Hertzler Ranch TSF and LAD Pond liner Operating Permit Minor Revision 04-002 Active 118 USFS CGNF/ DEQ Hard Rock Mining Program Sep-04 NA Soda ash silo installation, haul road on western edge of ESWRSF Operating Permit Minor Revision 04-003 Active 118 USFS CGNF/ DEQ Hard Rock Mining Program Dec-04 NA Temporary reduction in Nye TSF freeboard Operating Permit Minor Revision 05-001 Active 118 USFS CGNF/ DEQ Hard Rock Mining Program Oct-05 NA Advantex septic system upgrade, closure of MW- T3A Operating Permit Minor Revision 05-002 Active 118 USFS CGNF/ DEQ Hard Rock Mining Program Oct-05 NA Hertzler Stage 2 underdrain building, Hertzler Pump House expansion, admin building expansion Operating Permit Minor Revision 06-001 Active 118 USFS CGNF/ DEQ Hard Rock Mining Program Jan-07 NA Construction of West Fork Stillwater River breakout 232 Site Operating Permit and Type Status Permit Number Regulatory Agency Discharge Type Date Issued Renewal Date Description Operating Permit Minor Revision 06-002 Active 118 USFS CGNF/ DEQ Hard Rock Mining Program May-06 NA New surface sand line to 5500W Portal, parking lot access road, new washbay, Loci Shop restroom addition Operating Permit Minor Revision 06-003 Active 118 USFS CGNF/ DEQ Hard Rock Mining Program May-06 NA Concentrator storage building (east-side of concentrator) Operating Permit Minor Revision 07-001 Active 118 USFS CGNF/ DEQ Hard Rock Mining Program Jul-07 NA Emergency Response Building, west-side portal overflow containment Operating Permit Minor Revision 07-002 Active 118 USFS CGNF/ DEQ Hard Rock Mining Program Apr-09 NA Adjustment to flow monitoring requirement in Stillwater River Operating Permit Minor Revision 08-001 Active 118 USFS CGNF/ DEQ Hard Rock Mining Program Mar-08 NA Relocation of laydown to north-side of delivery road Operating Permit Minor Revision 08-002 Active 118 USFS CGNF/ DEQ Hard Rock Mining Program May-08 NA Tailings water treatment (150gal per minute) and land application 233 Site Operating Permit and Type Status Permit Number Regulatory Agency Discharge Type Date Issued Renewal Date Description Operating Permit Minor Revision 08-003 Active 118 USFS CGNF/ DEQ Hard Rock Mining Program Aug-08 NA Reduction in Nye TSF freeboard (6ft to 5ft), employee survey discontinuance, upgrade of surface compressor line Operating Permit Minor Revision 08-004 Active 118 USFS CGNF/ DEQ Hard Rock Mining Program Nov-08 NA Construction of parking lot entrance cover, 5150W mine water system upgrades Operating Permit Minor Revision 09-001 Active 118 USFS CGNF/ DEQ Hard Rock Mining Program Apr-09 NA Land application of Hertzler TSF underdrain water, update Water Resources Monitoring Plan Operating Permit Minor Revision 09-002 Active 118 USFS CGNF/ DEQ Hard Rock Mining Program Feb-10 NA Increase final elevation of ESWRSF from 5050 ft to 5150 ft Operating Permit Minor Revision 09-003 Active 118 USFS CGNF/ DEQ Hard Rock Mining Program Sep-10 NA Hertzler TSF Stage 2 underdrain modification, relocate of Fire Water Pump House transformer, revisions to Water Resources Monitoring Plan 234 Site Operating Permit and Type Status Permit Number Regulatory Agency Discharge Type Date Issued Renewal Date Description Operating Permit Minor Revision 10-001 Active 118 USFS CGNF/ DEQ Hard Rock Mining Program Mar-10 NA Hertzler in-situ methanol treatment injection wells Operating Permit Minor Revision 10-002 Active 118 USFS CGNF/ DEQ Hard Rock Mining Program Jun-10 NA Contaminated soils building, Stillwater Mining Company-16 enclosure, level access pad construction near pump house power line Operating Permit Minor Revision 10-003 Active 118 USFS CGNF/ DEQ Hard Rock Mining Program Oct-10 NA Two 5400E vent raises near the 5400E Portal Operating Permit Minor Revision 10-004 Active 118 USFS CGNF/ DEQ Hard Rock Mining Program Nov-10 NA Concentrator expansion (ceramic mills), water treatment cell 6 building addition Operating Permit Minor Revision 11-001 Active 118 USFS CGNF/ DEQ Hard Rock Mining Program Apr-11 NA BASF pilot plant, oily dirt storage building Operating Permit Minor Revision 11-002 Active 118 USFS CGNF/ DEQ Hard Rock Mining Program Jun-11 NA Contaminated soils building, Stillwater Mining Company-16 enclosure, level access pad construction near pump house power line

235 Site Operating Permit and Type Status Permit Number Regulatory Agency Discharge Type Date Issued Renewal Date Description Operating Permit Minor Revision 11-003 Active 118 USFS CGNF/ DEQ Hard Rock Mining Program Jun-11 NA Raise bore hole from 4400 level to 5000W Portal for road Operating Permit Minor Revision 11-004 Active 118 USFS CGNF/ DEQ Hard Rock Mining Program Nov-11 NA Final design surface facilities for Blitz Project Operating Permit Minor Revision 12-001 Active 118 USFS CGNF/ DEQ Hard Rock Mining Program Apr-12 NA Relocate power line, buried electrical line and transformer, office trailer installations, ESWRSF in- situ methanol treatment Operating Permit Minor Revision 12-002 Active 118 USFS CGNF/ DEQ Hard Rock Mining Program Jun-12 NA HDPE pipe welding shop addition at Batch Plant, concrete installations Operating Permit Minor Revision 12-003 Active 118 USFS CGNF/ DEQ Hard Rock Mining Program Sep-12 NA Overhead process water line install, east-side storm water collection system, concrete pad Operating Permit Minor Revision 13-001 Active 118 USFS CGNF/ DEQ Hard Rock Mining Program Apr-13 NA Inspection interval change to Hertzler HDPE line (5-yr to 10-year), expansion of Advantex waste water treatment pods by 3 236 Site Operating Permit and Type Status Permit Number Regulatory Agency Discharge Type Date Issued Renewal Date Description Operating Permit Minor Revision 13-002 Active 118 USFS CGNF/ DEQ Hard Rock Mining Program Jul-13 NA New buried sandline from Hertzler Pump House to 5500W Portal, concrete retaining wall near propane tanks Operating Permit Minor Revision 13-003 Active 118 USFS CGNF/ DEQ Hard Rock Mining Program Dec-13 NA Process water booster pump station, concrete pad for oxygen/acetylene, methanol storage tank and containment at Upper BTS, concrete pad for hazardous waste storage locker Operating Permit Minor Revision 14-001 Active 118 USFS CGNF/ DEQ Hard Rock Mining Program Mar-14 NA LAD Pond expansion, Hertzler TSF Stage 3 construction plan Operating Permit Minor Revision 14-002 Active 118 USFS CGNF/ DEQ Hard Rock Mining Program Jul-14 NA Hertzler TSF Stage 3 construction plan modifications 237 Site Operating Permit and Type Status Permit Number Regulatory Agency Discharge Type Date Issued Renewal Date Description Operating Permit Minor Revision 14-003 Active 118 USFS CGNF/ DEQ Hard Rock Mining Program Nov-14 NA Faulty mobile equipment building, concrete pads on 5000W rail, burial of overhead power lines, lower BTS building expansion for booster pump, concrete barrier walls at surface crusher, concrete storm water conveyance, additional east-side injection well Operating Permit Minor Revision 15-001 Active 118 USFS CGNF/ DEQ Hard Rock Mining Program Sep-15 NA Concrete containment pad for biodiesel fuel tote storage Operating Permit Minor Revision 16-001 Active 118 USFS CGNF/ DEQ Hard Rock Mining Program Jan-16 NA Closure/Post-Closure monitoring locations (sites) Operating Permit Minor Revision 16-002 Active 118 USFS CGNF/ DEQ Hard Rock Mining Program Jun-16 NA ESWRSF lining system and water transfer system Operating Permit Minor Revision 16-003 Active 118 USFS CGNF/ DEQ Hard Rock Mining Program May-15 NA Installation of inclinometers at the Nye and Hertzler TSFs Operating Permit Minor Revision 16-004 Active 118 USFS CGNF/ DEQ Hard Rock Mining Program Aug-16 NA Concrete sidewalk to new Blitz trailer 238 Site Operating Permit and Type Status Permit Number Regulatory Agency Discharge Type Date Issued Renewal Date Description Operating Permit Minor Revision 17-001 Active 118 USFS CGNF/ DEQ Hard Rock Mining Program Jun-17 5900W Portal Slope Stabilization and Ground Control, Concrete Pad and Containment; (East Side Rail Dump Expansion removed from MR 5/17/2017) Operating Permit Minor Revision 17-002 Active 118 USFS CGNF/ DEQ Hard Rock Mining Program Aug-17 Hertzler Ranch Perc Evaluation; Geotech work at West Fork (vent raise project); Geotech Evaluation upper Biological Treatment Cells; Add Admin Office Trailer Operating Permit Minor Revision 17-003 Active 118 USFS CGNF/ DEQ Hard Rock Mining Program Aug-17 Expansion of the existing east-side rail dump area with wind break for two new dump bays, a rail spur and concrete fuel containment area
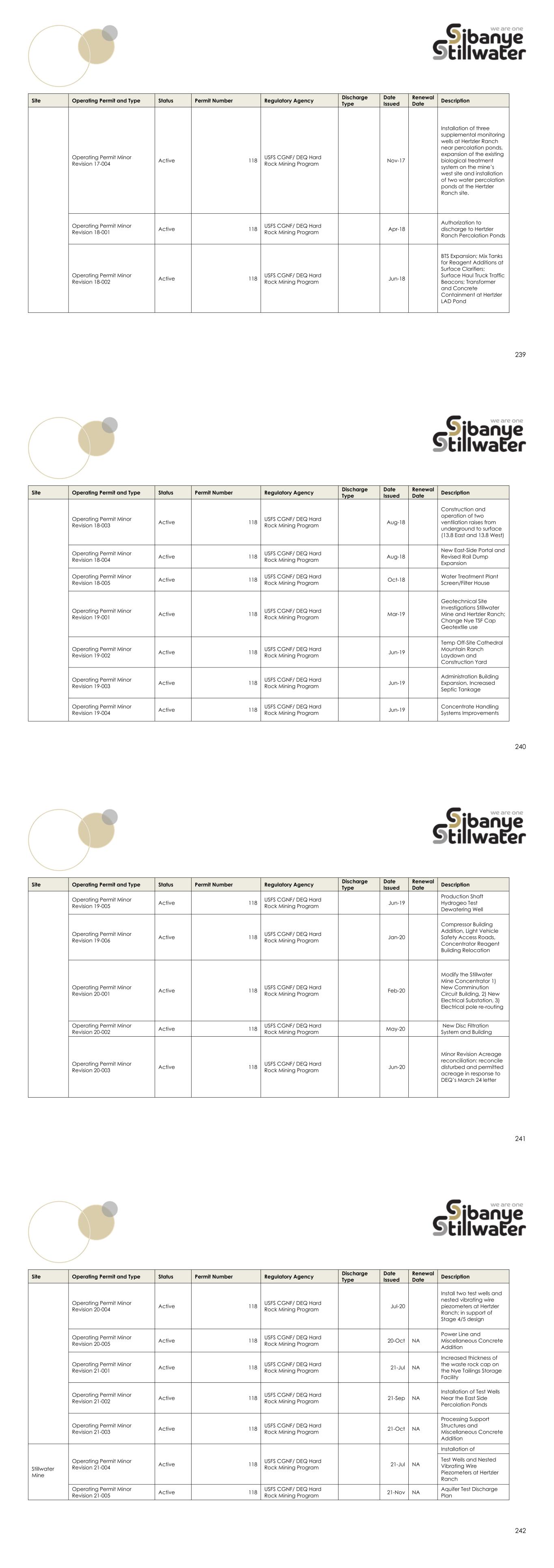
239 Site Operating Permit and Type Status Permit Number Regulatory Agency Discharge Type Date Issued Renewal Date Description Operating Permit Minor Revision 17-004 Active 118 USFS CGNF/ DEQ Hard Rock Mining Program Nov-17 Installation of three supplemental monitoring wells at Hertzler Ranch near percolation ponds, expansion of the existing biological treatment system on the mine’s west site and installation of two water percolation ponds at the Hertzler Ranch site. Operating Permit Minor Revision 18-001 Active 118 USFS CGNF/ DEQ Hard Rock Mining Program Apr-18 Authorization to discharge to Hertzler Ranch Percolation Ponds Operating Permit Minor Revision 18-002 Active 118 USFS CGNF/ DEQ Hard Rock Mining Program Jun-18 BTS Expansion; Mix Tanks for Reagent Additions at Surface Clarifiers; Surface Haul Truck Traffic Beacons; Transformer and Concrete Containment at Hertzler LAD Pond 240 Site Operating Permit and Type Status Permit Number Regulatory Agency Discharge Type Date Issued Renewal Date Description Operating Permit Minor Revision 18-003 Active 118 USFS CGNF/ DEQ Hard Rock Mining Program Aug-18 Construction and operation of two ventilation raises from underground to surface (13.8 East and 13.8 West) Operating Permit Minor Revision 18-004 Active 118 USFS CGNF/ DEQ Hard Rock Mining Program Aug-18 New East-Side Portal and Revised Rail Dump Expansion Operating Permit Minor Revision 18-005 Active 118 USFS CGNF/ DEQ Hard Rock Mining Program Oct-18 Water Treatment Plant Screen/Filter House Operating Permit Minor Revision 19-001 Active 118 USFS CGNF/ DEQ Hard Rock Mining Program Mar-19 Geotechnical Site Investigations Stillwater Mine and Hertzler Ranch; Change Nye TSF Cap Geotextile use Operating Permit Minor Revision 19-002 Active 118 USFS CGNF/ DEQ Hard Rock Mining Program Jun-19 Temp Off-Site Cathedral Mountain Ranch Laydown and Construction Yard Operating Permit Minor Revision 19-003 Active 118 USFS CGNF/ DEQ Hard Rock Mining Program Jun-19 Administration Building Expansion, Increased Septic Tankage Operating Permit Minor Revision 19-004 Active 118 USFS CGNF/ DEQ Hard Rock Mining Program Jun-19 Concentrate Handling Systems Improvements 241 Site Operating Permit and Type Status Permit Number Regulatory Agency Discharge Type Date Issued Renewal Date Description Operating Permit Minor Revision 19-005 Active 118 USFS CGNF/ DEQ Hard Rock Mining Program Jun-19 Production Shaft Hydrogeo Test Dewatering Well Operating Permit Minor Revision 19-006 Active 118 USFS CGNF/ DEQ Hard Rock Mining Program Jan-20 Compressor Building Addition, Light Vehicle Safety Access Roads, Concentrator Reagent Building Relocation Operating Permit Minor Revision 20-001 Active 118 USFS CGNF/ DEQ Hard Rock Mining Program Feb-20 Modify the Stillwater Mine Concentrator 1) New Comminution Circuit Building, 2) New Electrical Substation, 3) Electrical pole re-routing Operating Permit Minor Revision 20-002 Active 118 USFS CGNF/ DEQ Hard Rock Mining Program May-20 New Disc Filtration System and Building Operating Permit Minor Revision 20-003 Active 118 USFS CGNF/ DEQ Hard Rock Mining Program Jun-20 Minor Revision Acreage reconciliation: reconcile disturbed and permitted acreage in response to DEQ’s March 24 letter 242 Site Operating Permit and Type Status Permit Number Regulatory Agency Discharge Type Date Issued Renewal Date Description Operating Permit Minor Revision 20-004 Active 118 USFS CGNF/ DEQ Hard Rock Mining Program Jul-20 Install two test wells and nested vibrating wire piezometers at Hertzler Ranch; in support of Stage 4/5 design Operating Permit Minor Revision 20-005 Active 118 USFS CGNF/ DEQ Hard Rock Mining Program 20-Oct NA Power Line and Miscellaneous Concrete Addition Operating Permit Minor Revision 21-001 Active 118 USFS CGNF/ DEQ Hard Rock Mining Program 21-Jul NA Increased thickness of the waste rock cap on the Nye Tailings Storage Facility Operating Permit Minor Revision 21-002 Active 118 USFS CGNF/ DEQ Hard Rock Mining Program 21-Sep NA Installation of Test Wells Near the East Side Percolation Ponds Operating Permit Minor Revision 21-003 Active 118 USFS CGNF/ DEQ Hard Rock Mining Program 21-Oct NA Processing Support Structures and Miscellaneous Concrete Addition Stillwater Mine Operating Permit Minor Revision 21-004 Active 118 USFS CGNF/ DEQ Hard Rock Mining Program 21-Jul NA Installation of Test Wells and Nested Vibrating Wire Piezometers at Hertzler Ranch Operating Permit Minor Revision 21-005 Active 118 USFS CGNF/ DEQ Hard Rock Mining Program 21-Nov NA Aquifer Test Discharge Plan
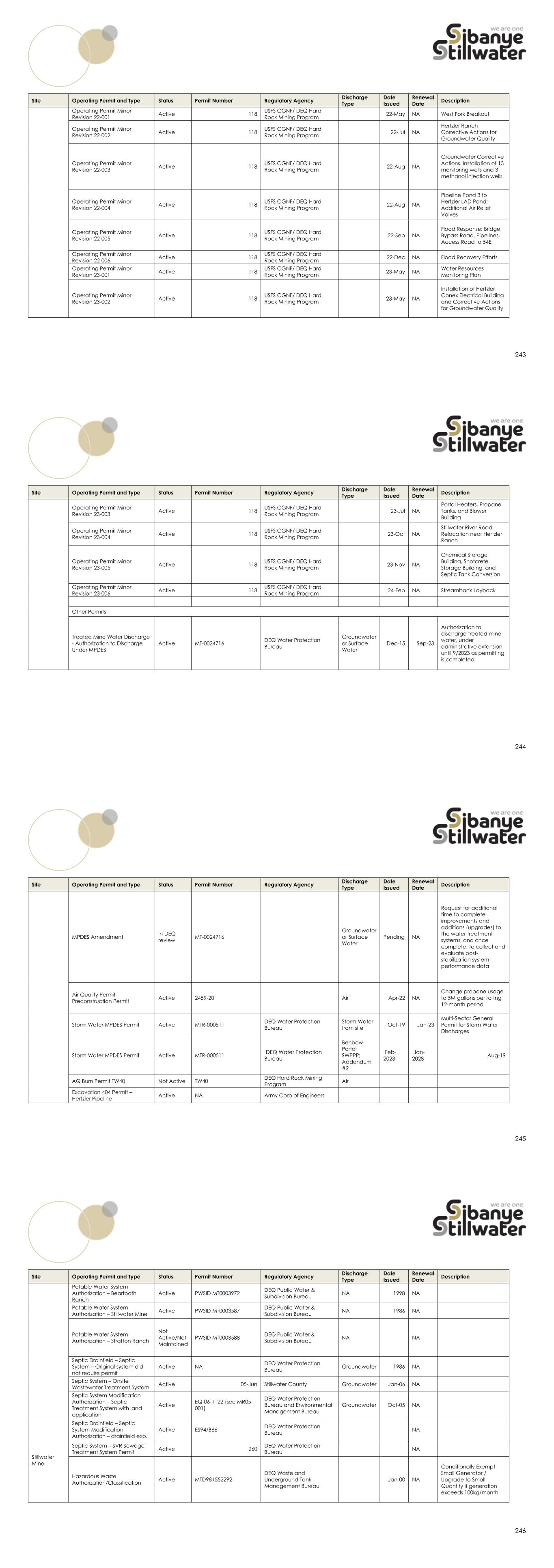
243 Site Operating Permit and Type Status Permit Number Regulatory Agency Discharge Type Date Issued Renewal Date Description Operating Permit Minor Revision 22-001 Active 118 USFS CGNF/ DEQ Hard Rock Mining Program 22-May NA West Fork Breakout Operating Permit Minor Revision 22-002 Active 118 USFS CGNF/ DEQ Hard Rock Mining Program 22-Jul NA Hertzler Ranch Corrective Actions for Groundwater Quality Operating Permit Minor Revision 22-003 Active 118 USFS CGNF/ DEQ Hard Rock Mining Program 22-Aug NA Groundwater Corrective Actions. Installation of 13 monitoring wells and 3 methanol injection wells. Operating Permit Minor Revision 22-004 Active 118 USFS CGNF/ DEQ Hard Rock Mining Program 22-Aug NA Pipeline Pond 3 to Hertzler LAD Pond: Additional Air Relief Valves Operating Permit Minor Revision 22-005 Active 118 USFS CGNF/ DEQ Hard Rock Mining Program 22-Sep NA Flood Response: Bridge, Bypass Road, Pipelines, Access Road to 54E Operating Permit Minor Revision 22-006 Active 118 USFS CGNF/ DEQ Hard Rock Mining Program 22-Dec NA Flood Recovery Efforts Operating Permit Minor Revision 23-001 Active 118 USFS CGNF/ DEQ Hard Rock Mining Program 23-May NA Water Resources Monitoring Plan Operating Permit Minor Revision 23-002 Active 118 USFS CGNF/ DEQ Hard Rock Mining Program 23-May NA Installation of Hertzler Conex Electrical Building and Corrective Actions for Groundwater Quality 244 Site Operating Permit and Type Status Permit Number Regulatory Agency Discharge Type Date Issued Renewal Date Description Operating Permit Minor Revision 23-003 Active 118 USFS CGNF/ DEQ Hard Rock Mining Program 23-Jul NA Portal Heaters, Propane Tanks, and Blower Building Operating Permit Minor Revision 23-004 Active 118 USFS CGNF/ DEQ Hard Rock Mining Program 23-Oct NA Stillwater River Road Relocation near Hertzler Ranch Operating Permit Minor Revision 23-005 Active 118 USFS CGNF/ DEQ Hard Rock Mining Program 23-Nov NA Chemical Storage Building, Shotcrete Storage Building, and Septic Tank Conversion Operating Permit Minor Revision 23-006 Active 118 USFS CGNF/ DEQ Hard Rock Mining Program 24-Feb NA Streambank Layback Other Permits Treated Mine Water Discharge - Authorization to Discharge Under MPDES Active MT-0024716 DEQ Water Protection Bureau Groundwater or Surface Water Dec-15 Sep-23 Authorization to discharge treated mine water, under administrative extension until 9/2023 as permitting is completed 245 Site Operating Permit and Type Status Permit Number Regulatory Agency Discharge Type Date Issued Renewal Date Description MPDES Amendment In DEQ review MT-0024716 Groundwater or Surface Water Pending NA Request for additional time to complete improvements and additions (upgrades) to the water treatment systems, and once complete, to collect and evaluate post- stabilization system performance data Air Quality Permit – Preconstruction Permit Active 2459-20 Air Apr-22 NA Change propane usage to 5M gallons per rolling 12-month period Storm Water MPDES Permit Active MTR-000511 DEQ Water Protection Bureau Storm Water from site Oct-19 Jan-23 Multi-Sector General Permit for Storm Water Discharges Storm Water MPDES Permit Active MTR-000511 DEQ Water Protection Bureau Benbow Portal SWPPP; Addendum #2 Feb- 2023 Jan- 2028 Aug-19 AQ Burn Permit TW40 Not Active TW40 DEQ Hard Rock Mining Program Air Excavation 404 Permit – Hertzler Pipeline Active NA Army Corp of Engineers 246 Site Operating Permit and Type Status Permit Number Regulatory Agency Discharge Type Date Issued Renewal Date Description Potable Water System Authorization – Beartooth Ranch Active PWSID MT0003972 DEQ Public Water & Subdivision Bureau NA 1998 NA Potable Water System Authorization – Stillwater Mine Active PWSID MT0003587 DEQ Public Water & Subdivision Bureau NA 1986 NA Potable Water System Authorization – Stratton Ranch Not Active/Not Maintained PWSID MT0003588 DEQ Public Water & Subdivision Bureau NA NA Septic Drainfield – Septic System – Original system did not require permit Active NA DEQ Water Protection Bureau Groundwater 1986 NA Septic System – Onsite Wastewater Treatment System Active 05-Jun Stillwater County Groundwater Jan-06 NA Septic System Modification Authorization – Septic Treatment System with land application Active EQ-06-1122 (see MR05- 001) DEQ Water Protection Bureau and Environmental Management Bureau Groundwater Oct-05 NA Stillwater Mine Septic Drainfield – Septic System Modification Authorization – drainfield exp. Active ES94/B66 DEQ Water Protection Bureau NA Septic System – SVR Sewage Treatment System Permit Active 260 DEQ Water Protection Bureau NA Hazardous Waste Authorization/Classification Active MTD981552292 DEQ Waste and Underground Tank Management Bureau Jan-00 NA Conditionally Exempt Small Generator / Upgrade to Small Quantity if generation exceeds 100kg/month
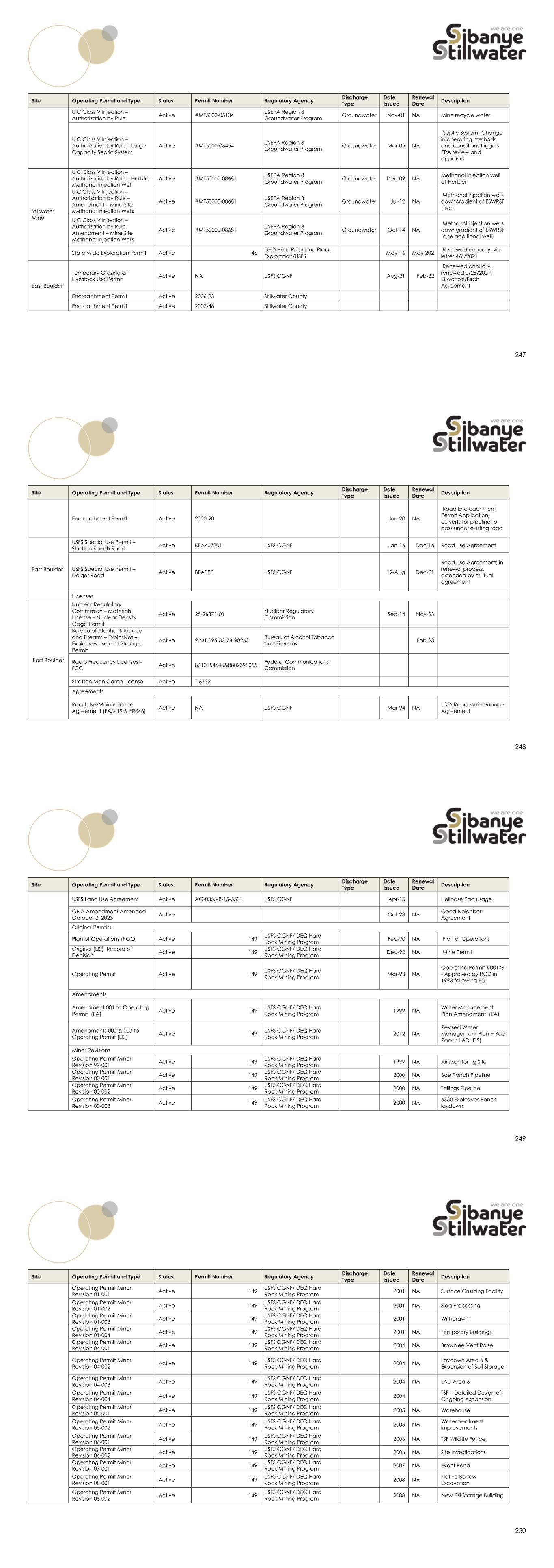
247 Site Operating Permit and Type Status Permit Number Regulatory Agency Discharge Type Date Issued Renewal Date Description UIC Class V Injection – Authorization by Rule Active #MT5000-05134 USEPA Region 8 Groundwater Program Groundwater Nov-01 NA Mine recycle water UIC Class V Injection – Authorization by Rule – Large Capacity Septic System Active #MT5000-06454 USEPA Region 8 Groundwater Program Groundwater Mar-05 NA (Septic System) Change in operating methods and conditions triggers EPA review and approval Stillwater Mine UIC Class V Injection – Authorization by Rule – Hertzler Methanol Injection Well Active #MT50000-08681 USEPA Region 8 Groundwater Program Groundwater Dec-09 NA Methanol injection well at Hertzler UIC Class V Injection – Authorization by Rule – Amendment – Mine Site Methanol Injection Wells Active #MT50000-08681 USEPA Region 8 Groundwater Program Groundwater Jul-12 NA Methanol injection wells downgradient of ESWRSF (five) UIC Class V Injection – Authorization by Rule – Amendment – Mine Site Methanol Injection Wells Active #MT50000-08681 USEPA Region 8 Groundwater Program Groundwater Oct-14 NA Methanol injection wells downgradient of ESWRSF (one additional well) State-wide Exploration Permit Active 46 DEQ Hard Rock and Placer Exploration/USFS May-16 May-202 Renewed annually, via letter 4/6/2021 East Boulder Temporary Grazing or Livestock Use Permit Active NA USFS CGNF Aug-21 Feb-22 Renewed annually, renewed 2/28/2021; Ekwortzel/Kirch Agreement Encroachment Permit Active 2006-23 Stillwater County Encroachment Permit Active 2007-48 Stillwater County 248 Site Operating Permit and Type Status Permit Number Regulatory Agency Discharge Type Date Issued Renewal Date Description Encroachment Permit Active 2020-20 Jun-20 NA Road Encroachment Permit Application, culverts for pipeline to pass under existing road East Boulder USFS Special Use Permit – Stratton Ranch Road Active BEA407301 USFS CGNF Jan-16 Dec-16 Road Use Agreement USFS Special Use Permit – Delger Road Active BEA388 USFS CGNF 12-Aug Dec-21 Road Use Agreement; in renewal process, extended by mutual agreement Licenses East Boulder Nuclear Regulatory Commission – Materials License – Nuclear Density Gage Permit Active 25-26871-01 Nuclear Regulatory Commission Sep-14 Nov-23 Bureau of Alcohol Tobacco and Firearm – Explosives – Explosives Use and Storage Permit Active 9-MT-095-33-7B-90263 Bureau of Alcohol Tobacco and Firearms Feb-23 Radio Frequency Licenses – FCC Active 8610054645&8802398055 Federal Communications Commission Stratton Man Camp License Active T-6732 Agreements Road Use/Maintenance Agreement (FAS419 & FR846) Active NA USFS CGNF Mar-94 NA USFS Road Maintenance Agreement 249 Site Operating Permit and Type Status Permit Number Regulatory Agency Discharge Type Date Issued Renewal Date Description USFS Land Use Agreement Active AG-0355-B-15-5501 USFS CGNF Apr-15 Helibase Pad usage GNA Amendment Amended October 3, 2023 Active Oct-23 NA Good Neighbor Agreement Original Permits Plan of Operations (POO) Active 149 USFS CGNF/ DEQ Hard Rock Mining Program Feb-90 NA Plan of Operations Original (EIS) Record of Decision Active 149 USFS CGNF/ DEQ Hard Rock Mining Program Dec-92 NA Mine Permit Operating Permit Active 149 USFS CGNF/ DEQ Hard Rock Mining Program Mar-93 NA Operating Permit #00149 - Approved by ROD in 1993 following EIS Amendments Amendment 001 to Operating Permit (EA) Active 149 USFS CGNF/ DEQ Hard Rock Mining Program 1999 NA Water Management Plan Amendment (EA) Amendments 002 & 003 to Operating Permit (EIS) Active 149 USFS CGNF/ DEQ Hard Rock Mining Program 2012 NA Revised Water Management Plan + Boe Ranch LAD (EIS) Minor Revisions Operating Permit Minor Revision 99-001 Active 149 USFS CGNF/ DEQ Hard Rock Mining Program 1999 NA Air Monitoring Site Operating Permit Minor Revision 00-001 Active 149 USFS CGNF/ DEQ Hard Rock Mining Program 2000 NA Boe Ranch Pipeline Operating Permit Minor Revision 00-002 Active 149 USFS CGNF/ DEQ Hard Rock Mining Program 2000 NA Tailings Pipeline Operating Permit Minor Revision 00-003 Active 149 USFS CGNF/ DEQ Hard Rock Mining Program 2000 NA 6350 Explosives Bench laydown 250 Site Operating Permit and Type Status Permit Number Regulatory Agency Discharge Type Date Issued Renewal Date Description Operating Permit Minor Revision 01-001 Active 149 USFS CGNF/ DEQ Hard Rock Mining Program 2001 NA Surface Crushing Facility Operating Permit Minor Revision 01-002 Active 149 USFS CGNF/ DEQ Hard Rock Mining Program 2001 NA Slag Processing Operating Permit Minor Revision 01-003 Active 149 USFS CGNF/ DEQ Hard Rock Mining Program 2001 Withdrawn Operating Permit Minor Revision 01-004 Active 149 USFS CGNF/ DEQ Hard Rock Mining Program 2001 NA Temporary Buildings Operating Permit Minor Revision 04-001 Active 149 USFS CGNF/ DEQ Hard Rock Mining Program 2004 NA Brownlee Vent Raise Operating Permit Minor Revision 04-002 Active 149 USFS CGNF/ DEQ Hard Rock Mining Program 2004 NA Laydown Area 6 & Expansion of Soil Storage Operating Permit Minor Revision 04-003 Active 149 USFS CGNF/ DEQ Hard Rock Mining Program 2004 NA LAD Area 6 Operating Permit Minor Revision 04-004 Active 149 USFS CGNF/ DEQ Hard Rock Mining Program 2004 TSF – Detailed Design of Ongoing expansion Operating Permit Minor Revision 05-001 Active 149 USFS CGNF/ DEQ Hard Rock Mining Program 2005 NA Warehouse Operating Permit Minor Revision 05-002 Active 149 USFS CGNF/ DEQ Hard Rock Mining Program 2005 NA Water treatment improvements Operating Permit Minor Revision 06-001 Active 149 USFS CGNF/ DEQ Hard Rock Mining Program 2006 NA TSF Wildlife Fence Operating Permit Minor Revision 06-002 Active 149 USFS CGNF/ DEQ Hard Rock Mining Program 2006 NA Site Investigations Operating Permit Minor Revision 07-001 Active 149 USFS CGNF/ DEQ Hard Rock Mining Program 2007 NA Event Pond Operating Permit Minor Revision 08-001 Active 149 USFS CGNF/ DEQ Hard Rock Mining Program 2008 NA Native Borrow Excavation Operating Permit Minor Revision 08-002 Active 149 USFS CGNF/ DEQ Hard Rock Mining Program 2008 NA New Oil Storage Building
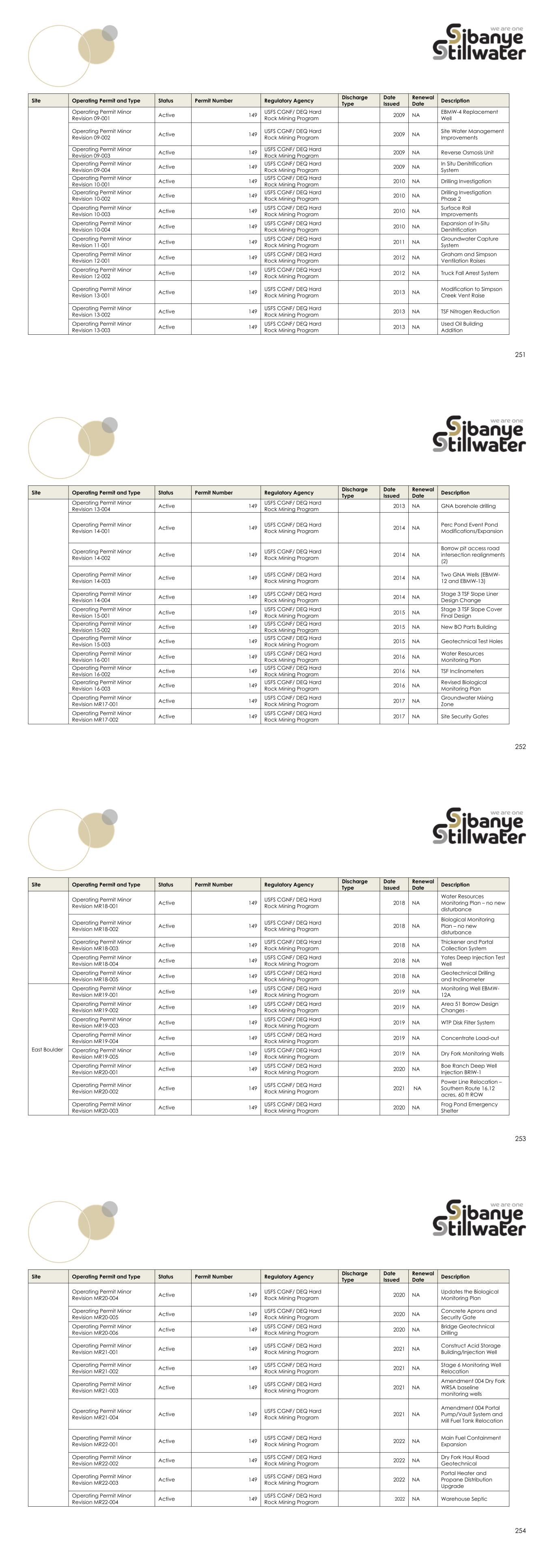
251 Site Operating Permit and Type Status Permit Number Regulatory Agency Discharge Type Date Issued Renewal Date Description Operating Permit Minor Revision 09-001 Active 149 USFS CGNF/ DEQ Hard Rock Mining Program 2009 NA EBMW-4 Replacement Well Operating Permit Minor Revision 09-002 Active 149 USFS CGNF/ DEQ Hard Rock Mining Program 2009 NA Site Water Management Improvements Operating Permit Minor Revision 09-003 Active 149 USFS CGNF/ DEQ Hard Rock Mining Program 2009 NA Reverse Osmosis Unit Operating Permit Minor Revision 09-004 Active 149 USFS CGNF/ DEQ Hard Rock Mining Program 2009 NA In Situ Denitrification System Operating Permit Minor Revision 10-001 Active 149 USFS CGNF/ DEQ Hard Rock Mining Program 2010 NA Drilling Investigation Operating Permit Minor Revision 10-002 Active 149 USFS CGNF/ DEQ Hard Rock Mining Program 2010 NA Drilling Investigation Phase 2 Operating Permit Minor Revision 10-003 Active 149 USFS CGNF/ DEQ Hard Rock Mining Program 2010 NA Surface Rail Improvements Operating Permit Minor Revision 10-004 Active 149 USFS CGNF/ DEQ Hard Rock Mining Program 2010 NA Expansion of In-Situ Denitrification Operating Permit Minor Revision 11-001 Active 149 USFS CGNF/ DEQ Hard Rock Mining Program 2011 NA Groundwater Capture System Operating Permit Minor Revision 12-001 Active 149 USFS CGNF/ DEQ Hard Rock Mining Program 2012 NA Graham and Simpson Ventilation Raises Operating Permit Minor Revision 12-002 Active 149 USFS CGNF/ DEQ Hard Rock Mining Program 2012 NA Truck Fall Arrest System Operating Permit Minor Revision 13-001 Active 149 USFS CGNF/ DEQ Hard Rock Mining Program 2013 NA Modification to Simpson Creek Vent Raise Operating Permit Minor Revision 13-002 Active 149 USFS CGNF/ DEQ Hard Rock Mining Program 2013 NA TSF Nitrogen Reduction Operating Permit Minor Revision 13-003 Active 149 USFS CGNF/ DEQ Hard Rock Mining Program 2013 NA Used Oil Building Addition 252 Site Operating Permit and Type Status Permit Number Regulatory Agency Discharge Type Date Issued Renewal Date Description Operating Permit Minor Revision 13-004 Active 149 USFS CGNF/ DEQ Hard Rock Mining Program 2013 NA GNA borehole drilling Operating Permit Minor Revision 14-001 Active 149 USFS CGNF/ DEQ Hard Rock Mining Program 2014 NA Perc Pond Event Pond Modifications/Expansion Operating Permit Minor Revision 14-002 Active 149 USFS CGNF/ DEQ Hard Rock Mining Program 2014 NA Borrow pit access road intersection realignments (2) Operating Permit Minor Revision 14-003 Active 149 USFS CGNF/ DEQ Hard Rock Mining Program 2014 NA Two GNA Wells (EBMW- 12 and EBMW-13) Operating Permit Minor Revision 14-004 Active 149 USFS CGNF/ DEQ Hard Rock Mining Program 2014 NA Stage 3 TSF Slope Liner Design Change Operating Permit Minor Revision 15-001 Active 149 USFS CGNF/ DEQ Hard Rock Mining Program 2015 NA Stage 3 TSF Slope Cover Final Design Operating Permit Minor Revision 15-002 Active 149 USFS CGNF/ DEQ Hard Rock Mining Program 2015 NA New BO Parts Building Operating Permit Minor Revision 15-003 Active 149 USFS CGNF/ DEQ Hard Rock Mining Program 2015 NA Geotechnical Test Holes Operating Permit Minor Revision 16-001 Active 149 USFS CGNF/ DEQ Hard Rock Mining Program 2016 NA Water Resources Monitoring Plan Operating Permit Minor Revision 16-002 Active 149 USFS CGNF/ DEQ Hard Rock Mining Program 2016 NA TSF Inclinometers Operating Permit Minor Revision 16-003 Active 149 USFS CGNF/ DEQ Hard Rock Mining Program 2016 NA Revised Biological Monitoring Plan Operating Permit Minor Revision MR17-001 Active 149 USFS CGNF/ DEQ Hard Rock Mining Program 2017 NA Groundwater Mixing Zone Operating Permit Minor Revision MR17-002 Active 149 USFS CGNF/ DEQ Hard Rock Mining Program 2017 NA Site Security Gates 253 Site Operating Permit and Type Status Permit Number Regulatory Agency Discharge Type Date Issued Renewal Date Description Operating Permit Minor Revision MR18-001 Active 149 USFS CGNF/ DEQ Hard Rock Mining Program 2018 NA Water Resources Monitoring Plan – no new disturbance Operating Permit Minor Revision MR18-002 Active 149 USFS CGNF/ DEQ Hard Rock Mining Program 2018 NA Biological Monitoring Plan – no new disturbance Operating Permit Minor Revision MR18-003 Active 149 USFS CGNF/ DEQ Hard Rock Mining Program 2018 NA Thickener and Portal Collection System Operating Permit Minor Revision MR18-004 Active 149 USFS CGNF/ DEQ Hard Rock Mining Program 2018 NA Yates Deep Injection Test Well Operating Permit Minor Revision MR18-005 Active 149 USFS CGNF/ DEQ Hard Rock Mining Program 2018 NA Geotechnical Drilling and Inclinometer East Boulder Operating Permit Minor Revision MR19-001 Active 149 USFS CGNF/ DEQ Hard Rock Mining Program 2019 NA Monitoring Well EBMW- 12A Operating Permit Minor Revision MR19-002 Active 149 USFS CGNF/ DEQ Hard Rock Mining Program 2019 NA Area 51 Borrow Design Changes - Operating Permit Minor Revision MR19-003 Active 149 USFS CGNF/ DEQ Hard Rock Mining Program 2019 NA WTP Disk Filter System Operating Permit Minor Revision MR19-004 Active 149 USFS CGNF/ DEQ Hard Rock Mining Program 2019 NA Concentrate Load-out Operating Permit Minor Revision MR19-005 Active 149 USFS CGNF/ DEQ Hard Rock Mining Program 2019 NA Dry Fork Monitoring Wells Operating Permit Minor Revision MR20-001 Active 149 USFS CGNF/ DEQ Hard Rock Mining Program 2020 NA Boe Ranch Deep Well Injection BRIW-1 Operating Permit Minor Revision MR20-002 Active 149 USFS CGNF/ DEQ Hard Rock Mining Program 2021 NA Power Line Relocation – Southern Route 16.12 acres, 60 ft ROW Operating Permit Minor Revision MR20-003 Active 149 USFS CGNF/ DEQ Hard Rock Mining Program 2020 NA Frog Pond Emergency Shelter 254 Site Operating Permit and Type Status Permit Number Regulatory Agency Discharge Type Date Issued Renewal Date Description Operating Permit Minor Revision MR20-004 Active 149 USFS CGNF/ DEQ Hard Rock Mining Program 2020 NA Updates the Biological Monitoring Plan Operating Permit Minor Revision MR20-005 Active 149 USFS CGNF/ DEQ Hard Rock Mining Program 2020 NA Concrete Aprons and Security Gate Operating Permit Minor Revision MR20-006 Active 149 USFS CGNF/ DEQ Hard Rock Mining Program 2020 NA Bridge Geotechnical Drilling Operating Permit Minor Revision MR21-001 Active 149 USFS CGNF/ DEQ Hard Rock Mining Program 2021 NA Construct Acid Storage Building/Injection Well Operating Permit Minor Revision MR21-002 Active 149 USFS CGNF/ DEQ Hard Rock Mining Program 2021 NA Stage 6 Monitoring Well Relocation Operating Permit Minor Revision MR21-003 Active 149 USFS CGNF/ DEQ Hard Rock Mining Program 2021 NA Amendment 004 Dry Fork WRSA baseline monitoring wells Operating Permit Minor Revision MR21-004 Active 149 USFS CGNF/ DEQ Hard Rock Mining Program 2021 NA Amendment 004 Portal Pump/Vault System and Mill Fuel Tank Relocation Operating Permit Minor Revision MR22-001 Active 149 USFS CGNF/ DEQ Hard Rock Mining Program 2022 NA Main Fuel Containment Expansion Operating Permit Minor Revision MR22-002 Active 149 USFS CGNF/ DEQ Hard Rock Mining Program 2022 NA Dry Fork Haul Road Geotechnical Operating Permit Minor Revision MR22-003 Active 149 USFS CGNF/ DEQ Hard Rock Mining Program 2022 NA Portal Heater and Propane Distribution Upgrade Operating Permit Minor Revision MR22-004 Active 149 USFS CGNF/ DEQ Hard Rock Mining Program 2022 NA Warehouse Septic
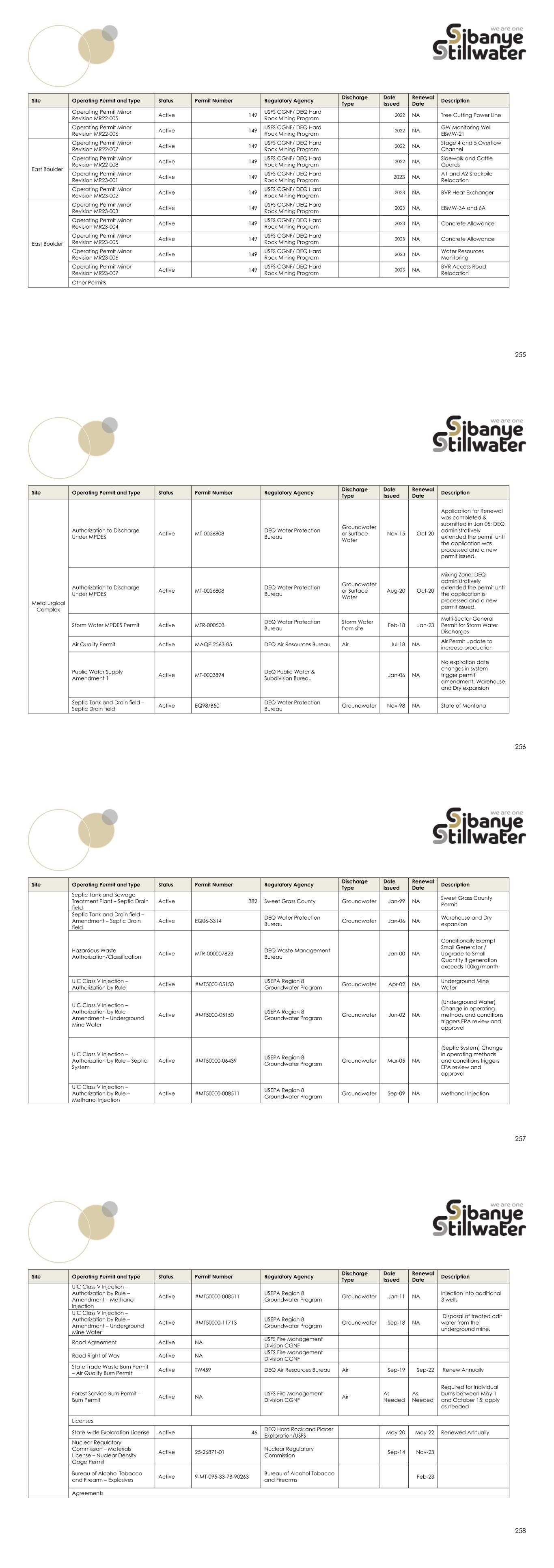
255 Site Operating Permit and Type Status Permit Number Regulatory Agency Discharge Type Date Issued Renewal Date Description Operating Permit Minor Revision MR22-005 Active 149 USFS CGNF/ DEQ Hard Rock Mining Program 2022 NA Tree Cutting Power Line Operating Permit Minor Revision MR22-006 Active 149 USFS CGNF/ DEQ Hard Rock Mining Program 2022 NA GW Monitoring Well EBMW-21 East Boulder Operating Permit Minor Revision MR22-007 Active 149 USFS CGNF/ DEQ Hard Rock Mining Program 2022 NA Stage 4 and 5 Overflow Channel Operating Permit Minor Revision MR22-008 Active 149 USFS CGNF/ DEQ Hard Rock Mining Program 2022 NA Sidewalk and Cattle Guards Operating Permit Minor Revision MR23-001 Active 149 USFS CGNF/ DEQ Hard Rock Mining Program 2023 NA A1 and A2 Stockpile Relocation Operating Permit Minor Revision MR23-002 Active 149 USFS CGNF/ DEQ Hard Rock Mining Program 2023 NA BVR Heat Exchanger East Boulder Operating Permit Minor Revision MR23-003 Active 149 USFS CGNF/ DEQ Hard Rock Mining Program 2023 NA EBMW-3A and 6A Operating Permit Minor Revision MR23-004 Active 149 USFS CGNF/ DEQ Hard Rock Mining Program 2023 NA Concrete Allowance Operating Permit Minor Revision MR23-005 Active 149 USFS CGNF/ DEQ Hard Rock Mining Program 2023 NA Concrete Allowance Operating Permit Minor Revision MR23-006 Active 149 USFS CGNF/ DEQ Hard Rock Mining Program 2023 NA Water Resources Monitoring Operating Permit Minor Revision MR23-007 Active 149 USFS CGNF/ DEQ Hard Rock Mining Program 2023 NA BVR Access Road Relocation Other Permits 256 Site Operating Permit and Type Status Permit Number Regulatory Agency Discharge Type Date Issued Renewal Date Description Metallurgical Complex Authorization to Discharge Under MPDES Active MT-0026808 DEQ Water Protection Bureau Groundwater or Surface Water Nov-15 Oct-20 Application for Renewal was completed & submitted in Jan 05; DEQ administratively extended the permit until the application was processed and a new permit issued. Authorization to Discharge Under MPDES Active MT-0026808 DEQ Water Protection Bureau Groundwater or Surface Water Aug-20 Oct-20 Mixing Zone; DEQ administratively extended the permit until the application is processed and a new permit issued. Storm Water MPDES Permit Active MTR-000503 DEQ Water Protection Bureau Storm Water from site Feb-18 Jan-23 Multi-Sector General Permit for Storm Water Discharges Air Quality Permit Active MAQP 2563-05 DEQ Air Resources Bureau Air Jul-18 NA Air Permit update to increase production Public Water Supply Amendment 1 Active MT-0003894 DEQ Public Water & Subdivision Bureau Jan-06 NA No expiration date changes in system trigger permit amendment. Warehouse and Dry expansion Septic Tank and Drain field – Septic Drain field Active EQ98/B50 DEQ Water Protection Bureau Groundwater Nov-98 NA State of Montana 257 Site Operating Permit and Type Status Permit Number Regulatory Agency Discharge Type Date Issued Renewal Date Description Septic Tank and Sewage Treatment Plant – Septic Drain field Active 382 Sweet Grass County Groundwater Jan-99 NA Sweet Grass County Permit Septic Tank and Drain field – Amendment – Septic Drain field Active EQ06-3314 DEQ Water Protection Bureau Groundwater Jan-06 NA Warehouse and Dry expansion Hazardous Waste Authorization/Classification Active MTR-000007823 DEQ Waste Management Bureau Jan-00 NA Conditionally Exempt Small Generator / Upgrade to Small Quantity if generation exceeds 100kg/month UIC Class V Injection – Authorization by Rule Active #MT5000-05150 USEPA Region 8 Groundwater Program Groundwater Apr-02 NA Underground Mine Water UIC Class V Injection – Authorization by Rule – Amendment – Underground Mine Water Active #MT5000-05150 USEPA Region 8 Groundwater Program Groundwater Jun-02 NA (Underground Water) Change in operating methods and conditions triggers EPA review and approval UIC Class V Injection – Authorization by Rule – Septic System Active #MT50000-06439 USEPA Region 8 Groundwater Program Groundwater Mar-05 NA (Septic System) Change in operating methods and conditions triggers EPA review and approval UIC Class V Injection – Authorization by Rule – Methanol Injection Active #MT50000-008511 USEPA Region 8 Groundwater Program Groundwater Sep-09 NA Methanol Injection 258 Site Operating Permit and Type Status Permit Number Regulatory Agency Discharge Type Date Issued Renewal Date Description UIC Class V Injection – Authorization by Rule – Amendment – Methanol Injection Active #MT50000-008511 USEPA Region 8 Groundwater Program Groundwater Jan-11 NA Injection into additional 3 wells UIC Class V Injection – Authorization by Rule – Amendment – Underground Mine Water Active #MT50000-11713 USEPA Region 8 Groundwater Program Groundwater Sep-18 NA Disposal of treated adit water from the underground mine. Road Agreement Active NA USFS Fire Management Division CGNF Road Right of Way Active NA USFS Fire Management Division CGNF State Trade Waste Burn Permit – Air Quality Burn Permit Active TW459 DEQ Air Resources Bureau Air Sep-19 Sep-22 Renew Annually Forest Service Burn Permit – Burn Permit Active NA USFS Fire Management Division CGNF Air As Needed As Needed Required for individual burns between May 1 and October 15; apply as needed Licenses State-wide Exploration License Active 46 DEQ Hard Rock and Placer Exploration/USFS May-20 May-22 Renewed Annually Nuclear Regulatory Commission – Materials License – Nuclear Density Gage Permit Active 25-26871-01 Nuclear Regulatory Commission Sep-14 Nov-23 Bureau of Alcohol Tobacco and Firearm – Explosives Active 9-MT-095-33-7B-90263 Bureau of Alcohol Tobacco and Firearms Feb-23 Agreements
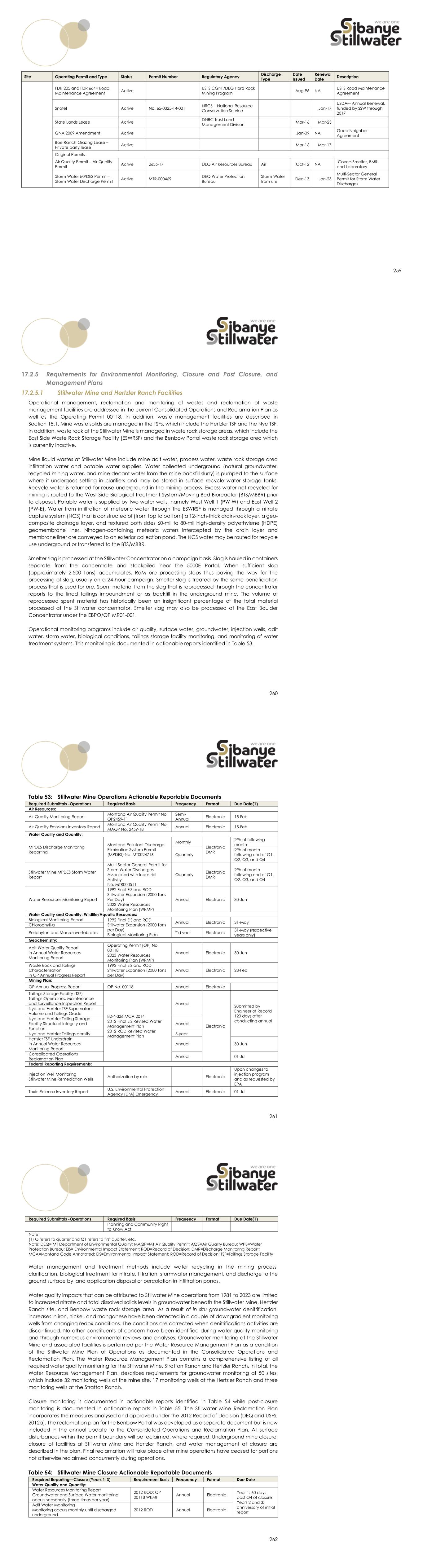
259 Site Operating Permit and Type Status Permit Number Regulatory Agency Discharge Type Date Issued Renewal Date Description FDR 205 and FDR 6644 Road Maintenance Agreement Active USFS CGNF/DEQ Hard Rock Mining Program Aug-96 NA USFS Road Maintenance Agreement Snotel Active No. 65-0325-14-001 NRCS–- National Resource Conservation Service Jan-17 USDA–- Annual Renewal, funded by SSW through 2017 State Lands Lease Active DNRC Trust Land Management Division Mar-16 Mar-23 GNA 2009 Amendment Active Jan-09 NA Good Neighbor Agreement Boe Ranch Grazing Lease – Private party lease Active Mar-16 Mar-17 Original Permits Air Quality Permit – Air Quality Permit Active 2635-17 DEQ Air Resources Bureau Air Oct-12 NA Covers Smelter, BMR, and Laboratory Storm Water MPDES Permit – Storm Water Discharge Permit Active MTR-000469 DEQ Water Protection Bureau Storm Water from site Dec-13 Jan-23 Multi-Sector General Permit for Storm Water Discharges 260 Requirements for Environmental Monitoring, Closure and Post Closure, and Management Plans 17.2.5.1 Stillwater Mine and Hertzler Ranch Facilities Operational management, reclamation and monitoring of wastes and reclamation of waste management facilities are addressed in the current Consolidated Operations and Reclamation Plan as well as the Operating Permit 00118. In addition, waste management facilities are described in Section 15.1. Mine waste solids are managed in the TSFs, which include the Hertzler TSF and the Nye TSF. In addition, waste rock at the Stillwater Mine is managed in waste rock storage areas, which include the East Side Waste Rock Storage Facility (ESWRSF) and the Benbow Portal waste rock storage area which is currently inactive. Mine liquid wastes at Stillwater Mine include mine adit water, process water, waste rock storage area infiltration water and potable water supplies. Water collected underground (natural groundwater, recycled mining water, and mine decant water from the mine backfill slurry) is pumped to the surface where it undergoes settling in clarifiers and may be stored in surface recycle water storage tanks. Recycle water is returned for reuse underground in the mining process. Excess water not recycled for mining is routed to the West-Side Biological Treatment System/Moving Bed Bioreactor (BTS/MBBR) prior to disposal. Potable water is supplied by two water wells, namely West Well 1 (PW-W) and East Well 2 (PW-E). Water from infiltration of meteoric water through the ESWRSF is managed through a nitrate capture system (NCS) that is constructed of (from top to bottom) a 12-inch-thick drain-rock layer, a geo- composite drainage layer, and textured both sides 60-mil to 80-mil high-density polyethylene (HDPE) geomembrane liner. Nitrogen-containing meteoric waters intercepted by the drain layer and membrane liner are conveyed to an exterior collection pond. The NCS water may be routed for recycle use underground or transferred to the BTS/MBBR. Smelter slag is processed at the Stillwater Concentrator on a campaign basis. Slag is hauled in containers separate from the concentrate and stockpiled near the 5000E Portal. When sufficient slag (approximately 2 500 tons) accumulates, RoM ore processing stops thus paving the way for the processing of slag, usually on a 24-hour campaign. Smelter slag is treated by the same beneficiation process that is used for ore. Spent material from the slag that is reprocessed through the concentrator reports to the lined tailings impoundment or as backfill in the underground mine. The volume of reprocessed spent material has historically been an insignificant percentage of the total material processed at the Stillwater concentrator. Smelter slag may also be processed at the East Boulder Concentrator under the EBPO/OP MR01-001. Operational monitoring programs include air quality, surface water, groundwater, injection wells, adit water, storm water, biological conditions, tailings storage facility monitoring, and monitoring of water treatment systems. This monitoring is documented in actionable reports identified in Table 53. 261 Table 53: Stillwater Mine Operations Actionable Reportable Documents Required Submittals -Operations Required Basis Frequency Format Due Date(1) Air Resources: Air Quality Monitoring Report Montana Air Quality Permit No. OP2459-11 Semi- Annual Electronic 15-Feb Air Quality Emissions Inventory Report Montana Air Quality Permit No. MAQP No. 2459-18 Annual Electronic 15-Feb Water Quality and Quantity: MPDES Discharge Monitoring Reporting Montana Pollutant Discharge Elimination System Permit (MPDES) No. MT0024716 Monthly Electronic DMR 28th of following month Quarterly 28th of month following end of Q1, Q2, Q3, and Q4 Stillwater Mine MPDES Storm Water Report Multi-Sector General Permit for Storm Water Discharges Associated with Industrial Activity No. MTR000511 Quarterly Electronic DMR 28th of month following end of Q1, Q2, Q3, and Q4 Water Resources Monitoring Report 1992 Final EIS and ROD Stillwater Expansion (2000 Tons Per Day) 2023 Water Resources Monitoring Plan (WRMP) Annual Electronic 30-Jun Water Quality and Quantity; Wildlife/Aquatic Resources: Biological Monitoring Report 1992 Final EIS and ROD Stillwater Expansion (2000 Tons per Day) Biological Monitoring Plan Annual Electronic 31-May Chlorophyll-a Periphyton and Macroinvertebrates 2nd year Electronic 31-May (respective years only) Geochemistry: Adit Water Quality Report in Annual Water Resources Monitoring Report Operating Permit (OP) No. 00118 2023 Water Resources Monitoring Plan (WRMP) Annual Electronic 30-Jun Waste Rock and Tailings Characterization in OP Annual Progress Report 1992 Final EIS and ROD Stillwater Expansion (2000 Tons per Day) Annual Electronic 28-Feb Mining Plan: OP Annual Progress Report OP No. 00118 Annual Electronic Electronic Submitted by Engineer of Record 120 days after conducting annual Tailings Storage Facility (TSF) Tailings Operations, Maintenance and Surveillance Inspection Report 82-4-336 MCA 2014 2012 Final EIS Revised Water Management Plan 2012 ROD Revised Water Management Plan Annual Nye and Hertzler TSF Supernatant Volume and Tailings Grade Nye and Hertzler Tailing Storage Facility Structural Integrity and Function Annual Nye and Hertzler Tailings density 5-year Hertzler TSF Underdrain in Annual Water Resources Monitoring Report Annual 30-Jun Consolidated Operations Reclamation Plan Annual 01-Jul Federal Reporting Requirements: Injection Well Monitoring Stillwater Mine Remediation Wells Authorization by rule Electronic Upon changes to injection program and as requested by EPA Toxic Release Inventory Report U.S. Environmental Protection Agency (EPA) Emergency Annual Electronic 01-Jul 262 Required Submittals -Operations Required Basis Frequency Format Due Date(1) Planning and Community Right to Know Act Note (1) Q refers to quarter and Q1 refers to first quarter, etc. Note: DEQ= MT Department of Environmental Quality; MAQP=MT Air Quality Permit; AQB=Air Quality Bureau; WPB=Water Protection Bureau; EIS= Environmental Impact Statement; ROD=Record of Decision; DMR=Discharge Monitoring Report; MCA=Montana Code Annotated; EIS=Environmental Impact Statement; ROD=Record of Decision; TSF=Tailings Storage Facility Water management and treatment methods include water recycling in the mining process, clarification, biological treatment for nitrate, filtration, stormwater management, and discharge to the ground surface by land application disposal or percolation in infiltration ponds. Water quality impacts that can be attributed to Stillwater Mine operations from 1981 to 2023 are limited to increased nitrate and total dissolved solids levels in groundwater beneath the Stillwater Mine, Hertzler Ranch site, and Benbow waste rock storage area. As a result of in situ groundwater denitrification, increases in iron, nickel, and manganese have been detected in a couple of downgradient monitoring wells from changing redox conditions. The conditions are corrected when denitrifications activities are discontinued. No other constituents of concern have been identified during water quality monitoring and through numerous environmental reviews and analyses. Groundwater monitoring at the Stillwater Mine and associated facilities is performed per the Water Resource Management Plan as a condition of the Stillwater Mine Plan of Operations as documented in the Consolidated Operations and Reclamation Plan. The Water Resource Management Plan contains a comprehensive listing of all required water quality monitoring for the Stillwater Mine, Stratton Ranch and Hertzler Ranch. In total, the Water Resource Management Plan, describes requirements for groundwater monitoring at 50 sites, which include 32 monitoring wells at the mine site, 17 monitoring wells at the Hertzler Ranch and three monitoring wells at the Stratton Ranch. Closure monitoring is documented in actionable reports identified in Table 54 while post-closure monitoring is documented in actionable reports in Table 55. The Stillwater Mine Reclamation Plan incorporates the measures analysed and approved under the 2012 Record of Decision (DEQ and USFS, 2012a). The reclamation plan for the Benbow Portal was developed as a separate document but is now included in the annual update to the Consolidated Operations and Reclamation Plan. All surface disturbances within the permit boundary will be reclaimed, where required. Underground mine closure, closure of facilities at Stillwater Mine and Hertzler Ranch, and water management at closure are described in the plan. Final reclamation will take place after mine operations have ceased for portions not otherwise reclaimed concurrently during operations. Table 54: Stillwater Mine Closure Actionable Reportable Documents Required Reporting—Closure (Years 1-3) Requirement Basis Frequency Format Due Date Water Quality and Quantity: Water Resources Monitoring Report Groundwater and Surface Water monitoring occurs seasonally (three times per year) 2012 ROD; OP 00118 WRMP Annual Electronic Year 1: 60 days past Q4 of closure Years 2 and 3: anniversary of initial report Adit Water Monitoring Monitoring occurs monthly until discharged underground 2012 ROD Annual Electronic

263 Required Reporting—Closure (Years 1-3) Requirement Basis Frequency Format Due Date Hertzler TSF Underdrain, Hertzler Ranch TSF Cover Seepage, and Stillwater TSF Cover Seepage Monitoring occurs seasonally until quality stabilizes 2012 ROD Annual Electronic Shaft Water Quality and Level/Elevation Monitoring Monitoring occurs seasonally for quality and level until stabilization, then annual frequency 2012 ROD Annual Electronic Hertzler Ranch Land Application Disposal System Annual monitoring for salts load from land application system during closure 2012 ROD Annual Electronic Reclamation Plan; Geotechnical and Stability: Tailings Storage Facility (TSF): Stillwater TSF Structural Integrity and Function Annual inspection by Engineer of Record, maintenance as needed 2012 ROD 2012 Final EIS Revised Water Management Plan Annual Electronic Year 1: 60 days past Q4 of closure Years 2 and 3: anniversary of initial report Stillwater TSF Seepage Outlet Structure and Shaft Trout Stream Channel Annual inspection, maintenance as needed Hertzler Ranch TSF Structural Integrity and Function Annual inspection, maintenance as needed Annual Electronic Reclamation Plan; Geotechnical and Stability: Hertzler Seepage Outlet Structure and Discharge Channel to LAD Pond Annual inspection, maintenance as needed 2012 Final EIS 2012 ROD Revised Water Management Plan Annual Electronic Year 1: 60 days past Q4 of closure Years 2 and 3: anniversary of initial report Stillwater Mine Storm Water Channels Annual inspection, maintenance as needed Annual Electronic Table 55: Stillwater Mine Post Closure Actionable Reportable Documents Required Reporting—Post Closure (Years 4-8) Requirement Basis Frequency Format Due Date Reclamation Plan; Water Quality and Quantity: Water Monitoring Report Groundwater and Surface Water monitoring occurs seasonally (three times per year) 2012 ROD Revised Water Management Plan; OP 00118 WRMP Annual Electronic Years 4 through 8: annual anniversary of initial closure report Shaft Water Quality and Level/Elevation Monitoring occurs seasonally for quality and level until stabilization, then annually until it discharges Annual Hard Copy Report Years 4 through 8: annual anniversary of initial closure report Reclamation Plan; Geotechnical and Stability: Hertzler and Stillwater TSF Structural Integrity and Function; Annual visual monitoring Years 4 and 5 2012 Final EIS and ROD Annual Hard Copy Report Years 4 through 8: annual anniversary of initial closure report Visual monitoring every 5 years from Year 5 until final bond release 5-Year Electronic Fifth-year anniversaries of Year 5 closure report Stillwater TSF Seepage Outlet Structure and Shaft Discharge Trout Stream, Hertzler TSF Cover Seepage Discharge Channel, Storm Water Channel Monitoring annually Years 4 – 8 Annual Electronic Years 4 through 8: annual anniversary of initial closure report Monitoring every 5 years from Year 5 until final bond release 5-Year Electronic Fifth-year anniversaries of Year 5 closure report Site Maintenance Monitoring: 264 Required Reporting—Post Closure (Years 4-8) Requirement Basis Frequency Format Due Date Function of facilities Ponds (percolation and Hertzler LAD storage) Storm water ditches and sediment basins TSF seepage and Shaft outlet channels TSF covers and underdrain outlet structures 2012 Final EIS Revised Water Management Plan 2012 FMEA Annual Electronic Years 4 through 8: annual anniversary of initial closure report Abandon/Close Monitoring Wells Abandonment anticipated to be in Year 9 Year 9: anniversary of initial closure report Vent raise replacement 2012 USFS 2012 FMEA Year 63 Note: FMEA=Failure Modes and Effects Analysis; ROD=Record of Decision; WRMP=Water Resources Monitoring Plan Concurrent reclamation has occurred since the start of operations in 1986. At the time of mine closure and facilities reclamation, all surface facilities will be decommissioned, all structures will be disassembled and removed from the site, and the land reclaimed consistent with the approved post-mine land use. Roads that will remain will include the main access road to the reclaimed portals, tailings storage facilities, water conveyance structures, and water monitoring sites to allow for long-term monitoring and maintenance. These roads will be reclaimed when long-term monitoring and maintenance activities cease. The Qualified Persons conclude that adequate volumes of soil materials are available for replacement of the required soil cover on all disturbances. Furthermore, reclamation should meet the State of Montana provisions and requirements under the Montana Metal Mine Reclamation Act (MCA 82-4-336). The Stillwater Mine Closure and Reclamation Plan is also intended to meet the USFS requirements governing mineral development (36 CFR 228.8), and reclamation requirements under the Federal Seed Act (7 U.S.C., Section 1551-1610) and current USFS seeding guidelines. 17.2.5.2 East Boulder Mine East Boulder Mine consists of the underground mine and surface processing, waste rock and tailings storage facilities. The Consolidated Operations and Reclamation Plan describes water management of both underground mine water, supernatant water from the tailings storage facility, and basin and embankment underdrain water. Operational management, reclamation and monitoring of wastes and reclamation of waste management facilities are addressed in the current Consolidated Operations and Reclamation Plan for East Boulder Mine. East Boulder Mine has several plans including those for water resource and biological monitoring and resource protection. Operational monitoring programs include air quality, surface water, groundwater, injection wells, adit water, storm water, biological conditions, TSF, and water treatment systems. This monitoring is documented in actionable reports identified in Table 56. Waste management facilities are described in Section 15.2. Mine waste solids are managed in the East Boulder TSF. Waste rock from the underground mine is currently used in construction of the TSF embankments. The finest fraction of the tailings is pumped to the lined tailings facility. Currently, Stages 5 and 6 are being constructed. Supernatant water from the TSF is recycled in a closed loop system with the mill. The TSF basin capture water is pumped to either the TSF supernatant pond or the water recycle pond. The embankment underdrain capture water is pumped to the TSF supernatant pond. 265 Water collected underground (natural groundwater, recycled mining water, and mine decant water from the slurry of mine backfill) is discharged from the mine adit, collected, treated in the treatment plant, and then returned for reuse underground in the mining process or discharged via the approved MPDES Permit. Water management and treatment methods include water recycling in the mining process, biological treatment for nitrate, stormwater management, and discharge to the groundwater by percolation in infiltration ponds. East Boulder Mine recently received approval to dispose of water in a deep injection well on Boe Ranch, although this system has not yet been placed into service. The Water Resources Monitoring Plan, updated in August 2021, is a reference document for all water quality monitoring for the Plan of Operations, the Operating Permit No. 00149 and the MPDES Permit MT0026808. The plan outlines the approved monitoring locations, schedule, list of parameters for analysis, and methods for sampling of surface water, mine water, and groundwater at East Boulder Mine. Monitoring requirements for the Boe Ranch LAD facility are included in the Water Resources Monitoring Plan and include sampling of springs and groundwater and surface water locations as required by the EIS and the Record of Decision but will only become active if the land application disposal facility is constructed. Table 56: East Boulder Mine Operations Actionable Reportable Documents Required Submittals - Operations Required Basis Frequency Format Due Date(1) Air Resources: Air Quality Monitoring Report Montana Air Quality Permit No. 2563-07 Annual Hard Copy 15-Feb Air Quality Emissions Inventory Report Montana Air Quality Permit No. 2563-07 Annual Electronic 15-Feb Water Quality and Quantity: MPDES Discharge Monitoring Reporting Montana Pollutant Discharge Elimination System Permit (MPDES) No. MT0026808 Monthly Electronic DMR 28th of following month Quarterly 28th of month following end of Q1, Q2, Q3, and Q4 Annual 28th of month following end of Q4 MPDES Storm Water Report Multi-Sector General Permit for Storm Water Discharges Associated with Industrial Activity No. MTR000503 Quarterly Electronic DMR 28th of month following end of Q1, Q2, Q3, and Q4 Water Monitoring Report 1992 Final EIS and ROD Water Resources Monitoring Plan (WRMP) Quarterly with Annual Summary Hard Copy 60 days past end of Q1, Q2, Q3, and Q4 and Annual Summary February Water Quality and Quantity; Wildlife/Aquatic Resources: Biological Monitoring Report Biological Monitoring Plan Annual Hard Copy 30-April Chlorophyll-a Periphyton and Macroinvertebrates 3rd-year Hard Copy 30-April (respective years only) Geochemistry: 266 Required Submittals - Operations Required Basis Frequency Format Due Date(1) Adit Water Quality Report Quarterly Monitoring Operating Permit No. 00149 Quarterly with Annual Summary Hard Copy 60 days past end of Q1, Q2, Q3, and Q4 Waste Rock and Tailings Characterization 1992 Final EIS and ROD Quarterly with Annual Summary Hard Copy 60 days past end of Q1, Q2, Q3, and Q4 and Annual Summary February Mining Plan: MMRA Operating Permit Annual Report Operating Permit No. 00149 Annual Hard Copy 26-May Tailings Storage Facility (TSF) Tailings Operations, Maintenance and Surveillance Inspection Report 82-4-336 MCA 2014 2012 Final EIS Revised Water Management Plan 2012 ROD Revised Water Management Plan Annual Tailings Supernatant Volume and Tailings Grade Impoundment Structural Integrity and Function Annual Tailings Density 5-year Tailings Impoundment Underdrain Monitoring occurs quarterly Annual 30-Jun Consolidated Operations Reclamation Plan Annual 01-Jul Federal Reporting Requirements: Toxic Release Inventory Report U.S. Environmental Protection Agency (EPA) Emergency Planning and Community Right to Know Act Annual Electronic 01-Jul Federal Reporting Requirements: UIC Permits water injection/disposal U.S. Environmental Protection Agency (EPA) Annual Electronic Upon changes to injection program and as requested by EPA Federal Reporting Requirements: Injection Well Monitoring Remediation Wells Authorization by Rule U.S. Environmental Protection Agency (EPA) Electronic Upon changes to injection program and as requested by EPA (1) Q refers to quarter, Q1 refers to first quarter, etc. Note: DEQ= MT Department of Environmental Quality; MAQP=MT Air Quality Permit; AQB=Air Quality Bureau; WPB=Water Protection Bureau; EIS= Environmental Impact Statement; ROD=Record of Decision; DMR=Discharge Monitoring Report; MCA=Montana Code Annotated; EIS=Environmental Impact Statement; ROD=Record of Decision; TSF=Tailings Storage Facility The Qualified Persons can confirm that closure monitoring is documented in actionable reports identified in Table 57 while post-closure monitoring is documented in actionable reports listed in Table 58. All surface disturbances within the permit boundary will be reclaimed, where required. Underground mine closure, closure of facilities, and water management at closure are described in the Consolidated Operations and Reclamation Plan, which addresses closure and post-closure monitoring. Final reclamation will take place after mine operations have ceased for portions not otherwise reclaimed concurrently during operations. Table 57: East Boulder Mine Closure Actionable Reportable Documents Required Reporting—Closure (Years 1-3) Requirement Basis Frequency Format Due Date Water Quality and Quantity: Water Resources Monitoring Report Monitoring occurs quarterly 2012 ROD; Revised Water Management Plan; Annual Hard Copy Year 1: 60 days past Q4 of closure

267 Required Reporting—Closure (Years 1-3) Requirement Basis Frequency Format Due Date Operating Permit 00149 Surface and Groundwater Monitoring Plan Years 2 and 3: annual anniversary of initial report Adit Water Monitoring Monitoring occurs tri-annually: spring, summer, fall 2012 ROD; Revised Water Management Plan Annual Hard Copy Reclamation Plan; Geotechnical and Stability: Tailings Storage Facility: Impoundment Underdrain Monitoring occurs quarterly 2012 ROD 2012 Final EIS Revised Water Management Plan Annual Hard Copy Year 1: 60 days past Q4 of closure Years 2 and 3: annual anniversary of initial report Tailings Impoundment Cover Seepage Monitoring occurs quarterly Tailings Density, Grade, Supernatant Volume Impoundment Structural Integrity and Function Visual monitoring occurs annually Annual Hard Copy Table 58: East Boulder Mine Post Closure Actionable Reportable Documents Required Reporting—Post Closure (Years 4-8) Requirement Basis Frequency Format Due Date Reclamation Plan; Water Quality and Quantity: Water Monitoring Report Monitoring occurs quarterly 2012 ROD; Revised Water Management Plan; Operating Permit 00149 Surface and Groundwater Monitoring Plan Annual Hard Copy Report Years 4 through 8: annual anniversary of initial closure report Adit Water Monitoring Monitoring occurs bi-annually 2012 ROD; Revised Water Management Plan Annual Hard Copy Report Years 4 through 8: annual anniversary of initial closure report Reclamation Plan; Geotechnical and Stability: Tailings Storage Facility Impoundment Structural Integrity and Function. Annual visual monitoring Years 4 and 5 2012 Final EIS and ROD; Revised Water Management Plan Annual Hard Copy Report Years 4 through 8: annual anniversary of initial closure report Tailings Storage Facility Visual monitoring until final bond release 5-Year Hard Copy Report Fifth-year anniversaries of Year 5 closure report Tailings Storage Facility Seepage Outlet Structure, Cover Seepage Discharge Channel, Storm Water Channel Monitoring annually Years 4 – 8 Annual Hard Copy Report Years 4 through 8: annual anniversary of initial closure report Tailings Storage Facility Monitoring every 5 years from Year 5 until final bond release 5-Year Hard Copy Report Fifth-year anniversaries of Year 8 closure report Site Maintenance Monitoring: Function of facilities Ponds Storm water ditches and basins Tailings Storage Facility seepage outlet channels 2012 Final EIS Revised Water Management Plan 2012 FMEA Annual Hard Copy Report Years 4 through 8: annual anniversary of initial closure report 268 Required Reporting—Post Closure (Years 4-8) Requirement Basis Frequency Format Due Date Tailings Storage Facility cover and underdrain outlet structure Vent raise replacement 2012 USFS Report Year 63 from closure Note: FMEA=Failure Modes and Effects Analysis; ROD=Record of Decision; WRMP=Water Resources Monitoring Plan 17.2.5.3 Columbus Metallurgical Complex Waste management facilities at the Columbus Metallurgical Complex include temporary gypsum and smelter slag storage and storm water management. Air emissions are managed and monitored per the 2019 air permit requirements and include bag house collection of particulates and SO2 scrubbing systems. Air monitoring includes measurement of opacity, particulate emissions (PM10 and PM2.5), CO, VOC and SO2 emissions, and effluent flow rates. The air permit was updated in 2019 to encompass planned increases in production and refining. SMC (Sibanye-Stillwater) was given approval for the processing of smelter slag at Stillwater and East Boulder Mines to recover additional precious metals. Slag from the smelter is trucked to the mines daily for batch processing. Slag is also crushed in campaigns and used as slag pit liner material. A quarterly sample is collected and analysed for leachability (TCLP); testing to date confirms the slag passes TCLP criteria as non-hazardous. The slag is temporarily stored on the East Property located southeast of the smelter and in the slag bunkers located north of the smelter pending transport to the mines. Excess gypsum is stored on site in lined bunkers and shipped offsite for either agricultural use as fertilizer or directly to approved sanitary landfills in Billings or Hardin, Montana. The smelter is considered by the EPA to be a large quantity generator of hazardous wastes that include the following sources: Laboratory nickel/copper/arsenic/chromium acidic solutions; Slag, crucibles, and cupels from fire assay contaminated with lead and other metals (e.g., barium, cobalt, chromium, copper, lead, manganese, mercury, nickel and zinc); Contaminated personal protective equipment; Waste potassium permanganate; Iron removal residue solids containing arsenic, cadmium, chromium and lead; Electrowinning filter cake material contains arsenic; Electrowinning filter cloth containing lead; Fluorescent bulbs; Methyl ethyl ketone contaminated rags; and Spent aerosol paint canisters. All hazardous wastes are shipped offsite for proper disposal at a permitted, out-of-state Treatment Storage Disposal Facility. The Qualified Persons are of the view that there are no closure or post closure monitoring requirements for this facility. 269 Reclamation Plans and Costs 17.2.6.1 Overview Reclamation plans and bond amounts are available for Stillwater and East Boulder Mines in their respective Consolidated Operations and Reclamation Plan. The Benbow Portal has an independent Plan of Operations, and Reclamation Plan, which has been incorporated into the Stillwater Mine Operating Permit and bonding. The current State bonding is the principal financial instrument covering reclamation and restoration obligations. Reclamation surety bond amounts have been developed using methods provided in the DEQ Bonding Procedures Manual (DEQ, 2001). Reclamation surety bonds run to the benefit of the State of Montana, which issues the Operating Permits, and not to the Federal Government. Direct reclamation costs include, but are not limited to, tailings impoundments; waste rock storage facilities; portals, roads, and diversions interim care and maintenance; closure water treatment; and long-term care and maintenance. Indirect reclamation costs are based on a fixed percentage of direct costs (excluding long-term care and maintenance). Reclamation costs have been developed for forward looking five- year periods with an assumed annual inflation rate of approximately 2%. 17.2.6.2 Stillwater Mine and Hertzler Ranch Facilities Mine closure plans and bond bases of estimate are provided for the Stillwater Mine facilities in the Consolidated Operations and Reclamation Plan and includes the Benbow Portal reclamation plan and bond. . Reclamation for these facilities includes closure and post-closure management of adit waters, tailings storage facility, waste rock storage area, storm water management, and post-closure monitoring and maintenance programs. Post-closure monitoring would address the following items until bond is released and all applicable water quality standards are met: Groundwater and surface water quality would be monitored three times per year according to the approved water quality monitoring plans and the MPDES permit in place during post- closure; Shaft water quality would be monitored three times per year and annually thereafter until water quality stabilizes and mine water discharges from the shaft; Shaft water levels would be monitored three times per year until mine water exits the shaft; Tailings impoundment function and structural integrity would be monitored annually for the first five years and then once every five years thereafter; Seepage outlet structures and discharge channel function would be monitored annually for the first five years and then once every five years thereafter; Hertzler Ranch surface and groundwater monitoring would occur three times per year for nutrients, salts, and biomonitoring; Water from the Hertzler Ranch tailings storage facility seepage outlet structure would be monitored for quality and flow rate three times per year until water quality stabilizes; The post-closure maintenance plan would include the following items to be conducted annually during the first five years of closure and once every five years thereafter until bond is released, the MPDES permit is no longer needed, and water quality standards in effect at that time are met: o Function of all ponds including percolation ponds, storm water sediment retention ponds, and Hertzler Ranch LAD storage pond; 270 o Function of storm water, west-side shaft, and seepage outlet structure discharge channels; and o Function of underdrains. Current bonding for reclamation under the Operating Permit 00118 is funded for the amount of $63 000 000. The latest approved minor revision to the Operating Permit (MR241-001) has resulted in $62 263 829 of the $63 000 000 bond being allocated to approved activities, leaving $736 171 unallocated to reclamation obligations. The Qualified Persons understand that the increased costs are being driven by incorporation of the Benbow Exploration Project into the Mine Permit, recent cost of living increases, State estimates of long-term monitoring costs and expanded water treatment associated with the East-side Waste Rock Storage Area. Table 59 presents the Stillwater Mine reclamation schedule and Table 60 presents the reclamation monitoring and maintenance schedule for the mine. Table 59: Stillwater Mine Reclamation Schedule Activity Interim Year 1 of Active Closure Year 2 of Active Closure Year 3 of Active Closure 1st Qtr 2nd Qtr 3rd Qtr 4th Qtr 1st Qtr 2nd Qtr 3rd Qtr 4th Qtr 1st Qtr 2nd Qtr 3rd Qtr 4th Qtr 1st Qtr 2nd Qtr 3rd Qtr 4th Qtr Water Treatment: Water Treatment – Underground water during demo Water Treatment – Tailings Imp Supernatant, Underdrain & O/F Water Treatment – Liberated tailings water during cap placement Site Care & Maintenance Reclamation Activity: Plant Site – Demolition & Removal of Plant Buildings Plant Site – Reclamation Mine – Underground Decommissioning Mine – Adit and Raise Closure Stillwater Impoundment Hertzler Impoundment Water Treatment & LAD Facilities – Demolition & Removal Power Line – Removal

271 Table 60: Stillwater Mine Closure Monitoring and Maintenance Schedule Based on the Qualified Person’s assessment of the reclamation bond calculation and discussions with in-house Environmental Specialists and taking into account the approved Reclamation Plans and understanding of the annual regulatory review of surety bases, the current reclamation costs and liabilities are reasonably managed and funded while existing sureties appear adequate to meet foreseeable commitments for the Stillwater Mine, contingent to final resolution of the Stillwater Mine bond negotiations. 17.2.6.3 East Boulder Mine Mine closure plans and bond bases of estimate are provided for the East Boulder Mine facilities in the Consolidated Operations and Reclamation Plan. Table 61 presents the East Boulder Mine reclamation schedule while Table 62 presents the reclamation monitoring and maintenance schedule for the mine. Concurrent reclamation has occurred since the start of operations. At the time of mine closure and reclamation, all surface facilities will be decommissioned, all structures will be disassembled and removed, and the land will be reclaimed consistent with the approved post-mine land use. Roads that will remain include the main access road to the reclaimed portals, TSF, water conveyance structures, and water monitoring locations to allow for long-term monitoring and maintenance. These roads will be reclaimed when long-term monitoring and maintenance activities cease. Adequate volumes of soil materials are available for replacement of the required soil cover on all disturbances. Reclamation will meet the State of Montana provisions and requirements under the Montana Metal Mine Reclamation 272 Act (MCA 82-4-336). The Closure and Reclamation Plan is also intended to meet the USFS requirements governing mineral development (36 CFR 228.8), and reclamation requirements under the Federal Seed Act (7 U.S.C., Section 1551-1610) and current USFS seeding guidelines. Table 61: East Boulder Mine Reclamation Schedule Activity Interim Year 1 of Active Closure Year 2 of Active Closure Year 3 of Active Closure 1st Qtr 2nd Qtr 3rd Qtr 4th Qtr 1st Qtr 2nd Qtr 3rd Qtr 4th Qtr 1st Qtr 2nd Qtr 3rd Qtr 4th Qtr 1st Qtr 2nd Qtr 3rd Qtr 4th Qtr Water Treatment: Water Treatment – Adit Water Water Treatment – Tailings Imp Supernatant, Underdrain & O/F Water Treatment – Liberated tailings water during cap placement Site Care & Maintenance Reclamation Activity: Plant Site – Demolition & Removal of Plant Buildings ` Plant Site – Reclamation Mine – Underground Demolition and Disposal; Adit & Raise Closure Tailings Impoundment Reclamation Water Treatment & LAD Facilities – Demolition & Removal Boe Ranch Pipeline Reclamation Power Line (within permit area) + 2 sub-stations – Removal Access Roads – Reclamation 273 Table 62: East Boulder Mine Closure Monitoring and Maintenance Schedule Reclamation of East Boulder Mine includes closure and post-closure management of adit waters, tailings storage facility, storm water management, and post-closure monitoring and maintenance programs. Closure and post-closure monitoring would address the following items until bond is released and all applicable water quality standards are met: Groundwater and surface water quality would be monitored quarterly during closure and then twice per year according to the approved water quality monitoring plans and the MPDES permit in place during post-closure; Adit water quality and quantity would be monitored three times per year until as long as the MPDES permit is in effect and/or until water quality standards are met; Tailings impoundment function and structural integrity would be monitored annually during Years four and five and then once every five years; Seepage outlet structures, seepage through cover discharge channel, adit discharge channel, storm water channel, and percolation pond function would be monitored annually for Years 4 to 8 and then once every five years; Boe Ranch land application disposal, if constructed, would have a post-closure monitoring plan completed that describes the details of surface and groundwater sampling three times a year for up to five years to document water quality. The embankment on the storage pond would be reduced eliminating the need for inspection of embankment stability. This system has not been constructed or operated; The post-closure maintenance plan would include the following items to be conducted annually during post-closure Years 4 to 8 and once every five years thereafter until bond is released, the MPDES permit is no longer needed, and water quality standards in effect at that time are met: o Function of all ponds including percolation ponds, storm water sediment retention ponds; o Function of stormwater, adit discharge, and seepage outlet structure discharge channels; o Function of seepage outlet structure and underdrain. Year 1 Year 2 Year 3 Year 4 Year 5 Year 6 Year 7 Year 8 Groundwater Monitoring Surface Water Monitoring Adit Water Monitoring TSF Underdrain TSF Seepage through the Cover Salt Load Monitoring Abandon/Close Monitoring Wells One Time Tailings Volume, Density, Grade Structural Integrity Seepage Outlet Structure, Seepage through the Cover, Discharge Channel, Storm Water Channels Function of all Ponds (including Percolation Pond and Sediment Ponds) Function of Storm Water Channels and Basins, Adit Discharge Channel, TSF Seepage Outlet Channel Function of TSF Cover and Underdrain Outlet Structures Quarterly Quarterly Annual Closure Year ACTIVITY (1) Annual Annual (1) Closure and post‐closure monitoring and maintenance requirements are based on the 2012 Final EIS and ROD. Costs for ensuring these measures are carried out are included in the reclamation bond estimate calculations in Appendix G1 of the CORP. Post‐Closure Year Quarterly As Needed As Needed As Needed Site Maintenance Water Quality Monitoring Semiannual Monthly Semiannual Annual TSF Facility Monitoring Quarterly 274 Current bonding for reclamation under the Operating Permit 00149 is funded for the amount of $30 000 000, with $29 910 748 obligated (through Minor Revision MR23-003) and $89 216 unobligated. The potential Lewis Gulch TSF and the Dry Creek waste rock storage facility, when approved and constructed, would add to surety requirements until the East Boulder Mine is reclaimed and the incremental surety bond amount released. No estimates for those future reclamation liabilities are available. Based on the Qualified Persons’ assessment of the reclamation bond calculation, discussions with Site Environmental Specialist and noting the approved Reclamation Plans and understanding of the annual regulatory review of surety bases, the current reclamation costs and liabilities are reasonably managed and funded, existing sureties appear adequate to meet foreseeable commitments for the East Boulder Mine. 17.2.6.4 Columbus Metallurgical Complex The Columbus Metallurgical Complex does not operate under a comparable Federal or State operating permit like the mines and, as such, no reclamation plan or bond is required. The Qualified Persons can confirm that there are no closure plans contemplated for the Columbus Metallurgical Complex.

275 CAPITAL AND OPERATING COSTS Overview Stillwater and East Boulder Mines and the Columbus Metallurgical Complex have been operated as integrated mature mining, ore processing and mineral beneficiation operations producing PGMs and base metals. Much of the long-term infrastructure and equipment required for the operations is in place, with upgrades implemented to accommodate production increases anticipated in the LoM plans for the operations and/or any technological improvements that bring in operational efficiencies. The capital and operating costs for the three sites were estimated through an integrated, comprehensive budgeting process. Estimates of sustaining capital and operating costs were benchmarked to historical costs, while accounting for changes in production levels, escalation and contingencies. Project capital estimates for productivity enhancement projects were based on quotations from original equipment manufacturers and contractors. The foregoing constitutes sufficient justification for capital and operating cost budgeting for the operations. In addition, the accuracy level in the capital and operating costs utilised for LoM budgeting is within ±15% at up to 10% contingency for Proved Mineral Reserves and ±15% at up to 10% contingency for Probable Mineral Reserves. The capital and operating costs were utilised for the economic viability of the LoM plans for the mines and for the overall Sibanye- Stillwater US PGM Operations. Capital and operating costs in this section are reported by site, namely Stillwater Mine, East Boulder Mine and the Columbus Metallurgical Complex. However, for the purposes of economic viability testing of the LoM plans, the capital and operating costs for the Columbus Metallurgical Complex are assigned to Stillwater and East Boulder Mines proportionately to production at the mines. All costs are presented in real terms and US$. Capital Costs Background Capital cost budgets present the costs into two categories, namely Category 1 and Category 2. Category 1 is essential capital for business continuity and sustaining production at the sites whereas Category 2 capital relates to projects intended for improved productivity, efficiency improvement and the management of environmental and social/administration matters. The Blitz Project, which started in 2011 and centred on expanding mining operations towards the Stillwater East Section and ore processing facilities, has been the most significant Category 2 contributor at Stillwater Mine and the Columbus Metallurgical Complex in recent years. TSF capacity expansion which is in advanced stages of permitting has become the main contributor to Category 2 capital at East Boulder Mine. The accuracy levels stated in Section 18.1 are applicable to both capital expenditure categories. Stillwater Mine 18.2.2.1 LoM Capital Expenditure Schedule The LoM capital cost schedule for the Stillwater Mine is presented in Table 63 where it is also compared with actual capital expenditure for the FY2021 to FY2023 period. 276 The capital costs for Stillwater Mine include capital expenditure for mine and surface equipment, infrastructure, capitalised development, ongoing projects and environmental management, which relate to the mining and ore processing operations. In addition, there has been significant capital expenditure on the Blitz Project (Stillwater East Growth and Project Capital) until FY2022. There was also capital expenditure in FY2023 but at a significantly reduced level. Key changes to the Blitz Project after FY2021 include the following: TBM Tunnel/Benbow/5600E-Benbow was completed and the 5600E FWL was connected in 2022. Spending on Benbow portal area remediation continued at a reduced rate in FY2023 and this will continue until FY2024; Much of the capital expenditure previously reported as Growth Capital has been reported under stay in business (SIB) capital costs following the achievement of the desired level of production at the Stillwater East Section in FY2022 which is in line with the Sibanye-Stillwater criteria for reporting capital and operating costs; Stillwater East Section equipment capital expenditure which was previously reported under Growth Capital has been reported under SIB capital expenditure from FY2022 and any new equipment is covered under the SIB capital expenditure budget; Stillwater East Section infrastructure which was also reported under Growth Capital has been reported as SIB capital since FY2022. Only infrastructure projects associated with the 5600E/5000E drive have been funded as Growth Capital until completion; Capital expenditure for the expansion of the Stillwater Concentrator capacity has continued and is expected to be finalised in FY2024. The total capital budget for Stillwater Mine for the FY2024 to FY2054 period is approximately $2.34 billion (i.e. equivalent to $75.32 million per annum on average) and this is dominated by capitalised development (55%). Stillwater Mine’s capital expenditure in the capital budget is detailed by month for the first two years of the LoM and is annualised thereafter until FY2054. Long-term capital expenditure related to a specific project and/or scheduled equipment replacement is forecast in detail based on quotations from original equipment manufacturers and contractors. Routine long-term capital expenditure is forecast based on benchmarking with historical capital expenditure for the capitalised items. 18.2.2.2 Mining Capital The mining capital consists of several elements including development capital and capital associated with certain underground infrastructure upgrades. The following commentary outlines the main highlights of the capital expenditure schedule: Mine and Surface Equipment Capital: An annual provision averaging approximately $12.42 million has been budgeted for the procurement of additional mining and surface equipment for the Stillwater East and Stillwater West Sections between FY2024 and FY2054, with a peak of $23.66 million in FY2025. The peak expenditure in FY2025 is required for the ongoing replacement of certain primary and secondary underground equipment fleets that are past their normal life cycle replacement schedules. The lifecycle replacements are required to achieve and sustain the planned productivity levels; Capitalised Development Capital: Capitalised development is defined as the part of primary development which extends or improves the LoM, such as footwall levels, access ramps, and infrastructure development. The capital allowance for development averages $76.01 million per 277 annum between FY2024 and FY2033, which is a lower expenditure level relative to expenditure in FY2022 and FY2023 of $115.55 million and $140.44 million, respectively. The quantum of capitalised development capital declines to an average of $47.35 million per annum from FY2034 to FY2041, and progressively thereafter to $16.43 million in FY2048; Project Capital: This capital relates to specific, scheduled projects which enhance productivity or extend the life of mine, such as new tip and chute installations and rail extensions. This varies from year to year as requirements dictate but is budgeted at $7.52 million per annum and $233.13 million over the LoM. Higher than average annual expenditure between FY2025 and FY2027 (total of $123.80 million for the three years) relate to the construction of a sand plant in the Stillwater East Section (5500W SWE Paste Plant) and underground water handling infrastructure upgrades. An increase in Project Capital expenditure over the period FY2021 to FY2023 is due to the West Fork Vent Raise Project (approximately $10.00 million); Infrastructure Capital: This capital also relates to specific scheduled projects but with a focus on items such as communication, information technology (IT), software licences, power supply upgrades and the extension of the centralised blasting system as the mine footprint expands. This is budgeted at an average expenditure of $3.78 million per annum over the LoM; Other Capital: Other capital was an allocation towards longer term strategic projects such as the development of LoM rock and ventilation passes and there has been no allocation under this category since FY2023 as this expenditure has been moved to Project Capital expenditure; Stillwater East Expansion (Growth) Capital: This was capital budgeted for the development of the Stillwater East Section in terms of expansion items such as capitalised infrastructure, development, exploration drilling, underground equipment, surface infrastructure expansion, concentrator capacity expansion and concentrate handling facilities. It also accounted for the capital required to establish a LoM rock pass system. As discussed above, most of this expenditure is accounted for in SIB capital; Stillwater East Project Capital: This was capital budgeted for the establishment of permanent underground infrastructure and access, such as declines and ventilation raises. Most of this is also covered under SIB capital. Stillwater East (Blitz) Growth and Project capital expenditure cease in FY2024 and, thereafter, all mining capital costs associated with the Stillwater East Section will be incorporated in the general Stillwater Mine mining SIB capital expenditure budget. Based on the historical capital expenditure and the detail associated with the various capital budgets, the Qualified Person is of the view that sufficient capital provisions have been allowed for the support of the operations at Stillwater Mine. 18.2.2.3 Concentrator Capital The budgeted concentrator capital comprises modest sustaining capital per annum of between $225 thousand to $300 thousand for process equipment, buildings and infrastructure over the LoM. However, there are also specific capital provisions amounting to $12.65 million for maintenance/replacement of the River Bridge and $3.10 million for compressed air building upgrades between FY2024 and FY2026. With the finalisation of the concentrator expansion, all concentrator capital falls under SIB capital costs. 278 18.2.2.4 Environmental Capital Environmental capital expenditure encompasses TSF expansions, designs and implementation and associated infrastructure maintenance in addition to water and waste rock management and groundwater expenditure. The environmental capital schedule shows expenditure ramp up over two periods. The first period (FY2025 to FY2027) involves modest expenditure of $40.50 million on the next stage of the East Waste Rock Storage Facility (capping and expansion totalling $19.94 million) and water handling infrastructure upgrades resulting from increasing production in the Stillwater East Section. Elevated capital expenditure of $152.80 million in the second period (FY2029 to FY2021) includes $135.40 million for Hertzler TSF Stage 4/5 design and construction. The Hertzler TSF expansion project has initial capital expenditure amount of $6.50 million budgeted for studies over the FY2024 to FY2026 period. Capital expenditure over the remainder of the years is on average $4.82 million per annum which is aligned to historical expenditure. In addition to the LoM total environmental capital expenditure of $314.24 million, there is an allowance totalling $57 million provided for environmental closure. The environmental capital costs include $4.60 million for the final closure and capping of the Nye TSF and TSF replacement.
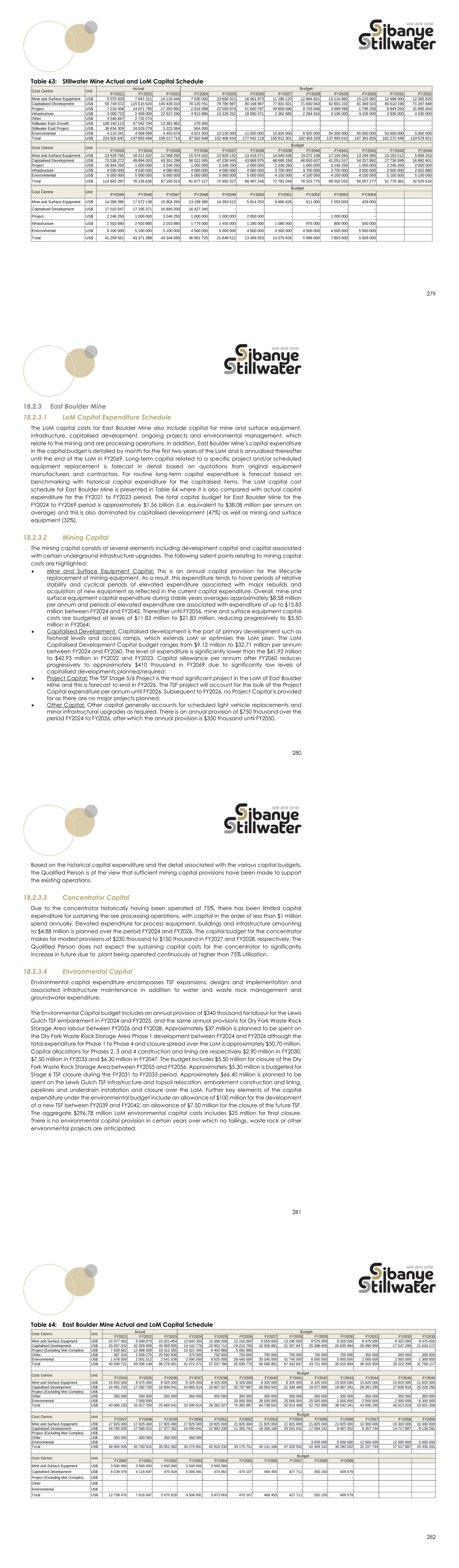
279 Table 63: Stillwater Mine Actual and LoM Capital Schedule FY2021 FY2022 FY2023 FY2024 FY2025 FY2026 FY2027 FY2028 FY2029 FY2030 FY2031 FY2032 Mine and Surface Equipment US$ 5 075 929 7 947 221 14 116 446 7 030 000 23 656 321 16 061 873 11 288 120 12 864 821 13 116 882 15 120 382 12 488 000 12 365 620 Capitalised Development US$ 55 749 072 115 515 620 140 439 310 78 120 761 79 790 987 80 168 987 77 831 821 71 640 043 62 801 232 81 369 023 83 510 198 71 287 848 Project US$ 7 234 408 14 671 790 17 293 992 2 816 998 22 500 874 51 680 787 49 609 696 8 743 648 3 669 496 1 796 250 8 844 250 31 895 454 Infrastructure US$ 3 009 723 2 458 000 22 917 290 4 913 886 13 328 252 18 080 471 2 362 665 2 284 816 4 106 000 4 106 000 3 930 000 4 030 000 Other US$ 4 546 847 2 732 274 - - - - - - - - - - Stillwater East Growth US$ 108 142 113 47 542 794 13 381 962 275 000 - - - - - - - - Stillwater East Project US$ 36 634 309 24 029 279 5 222 084 604 000 - - - - - - - - Environmental US$ 4 110 241 4 568 589 4 450 678 4 621 003 13 130 000 11 550 000 15 820 000 6 920 000 54 300 000 45 000 000 53 500 000 5 000 000 Total US$ 224 502 642 147 893 494 199 217 716 97 502 648 152 406 434 177 542 118 156 912 301 102 453 329 137 993 610 147 391 655 162 272 448 124 578 921 FY2033 FY2034 FY2035 FY2036 FY2037 FY2038 FY2039 FY2040 FY2041 FY2042 FY2043 FY2044 Mine and Surface Equipment US$ 13 429 765 18 211 632 11 568 265 15 574 632 13 929 132 13 418 271 14 045 638 19 072 138 17 104 265 13 199 385 13 193 512 5 889 253 Capitalised Development US$ 73 538 272 49 894 003 43 301 298 56 022 495 47 236 945 43 988 975 48 689 158 48 650 637 41 051 517 34 257 892 27 736 599 16 882 401 Project US$ 18 844 250 1 000 000 3 246 250 1 000 000 2 246 250 2 000 000 2 246 250 1 000 000 3 246 250 1 000 000 2 246 250 2 000 000 Infrastructure US$ 4 030 000 4 030 000 4 080 000 4 080 000 4 080 000 4 080 000 3 700 000 3 700 000 3 700 000 3 500 000 3 500 000 2 653 880 Environmental US$ 5 000 000 5 000 000 5 000 000 5 000 000 5 000 000 5 000 000 4 100 000 4 100 000 4 100 000 4 100 000 5 100 000 5 100 000 Total US$ 114 842 287 78 135 635 67 195 813 81 677 127 72 492 327 68 487 246 72 781 046 76 522 775 69 202 032 56 057 277 51 776 361 32 525 534 FY2045 FY2046 FY2047 FY2048 FY2049 FY2050 FY2051 FY2052 FY2053 FY2054 Mine and Surface Equipment US$ 14 399 385 17 572 138 15 904 265 13 199 385 14 393 512 5 814 253 8 690 626 511 000 1 553 000 428 000 Capitalised Development US$ 17 010 047 17 195 371 16 890 200 16 427 340 - - - - - - Project US$ 2 246 250 1 000 000 3 246 250 1 000 000 1 000 000 2 000 000 - - 1 000 000 - Infrastructure US$ 2 503 880 2 503 880 2 203 880 1 775 000 1 455 000 1 185 000 1 085 000 975 000 800 000 500 000 Environmental US$ 5 100 000 5 100 000 5 100 000 4 500 000 5 000 000 4 500 000 4 500 000 4 500 000 4 500 000 5 000 000 Total US$ 41 259 561 43 371 388 43 344 595 36 901 725 21 848 512 13 499 253 14 275 626 5 986 000 7 853 000 5 928 000 Cost Centre Unit Cost Centre Unit Actual Cost Centre Unit Budget Budget Budget 280 East Boulder Mine 18.2.3.1 LoM Capital Expenditure Schedule The LoM capital costs for East Boulder Mine also include capital for mine and surface equipment, infrastructure, capitalised development, ongoing projects and environmental management, which relate to the mining and ore processing operations. In addition, East Boulder Mine’s capital expenditure in the capital budget is detailed by month for the first two years of the LoM and is annualised thereafter until the end of the LoM in FY2069. Long-term capital related to a specific project and/or scheduled equipment replacement is forecast in detail based on quotations from original equipment manufacturers and contractors. For routine long-term capital expenditure is forecast based on benchmarking with historical capital expenditure for the capitalised items. The LoM capital cost schedule for East Boulder Mine is presented in Table 64 where it is also compared with actual capital expenditure for the FY2021 to FY2023 period. The total capital budget for East Boulder Mine for the FY2024 to FY2069 period is approximately $1.56 billion (i.e. equivalent to $38.08 million per annum on average) and this is also dominated by capitalised development (47%) as well as mining and surface equipment (32%). 18.2.3.2 Mining Capital The mining capital consists of several elements including development capital and capital associated with certain underground infrastructure upgrades. The following salient points relating to mining capital costs are highlighted: Mine and Surface Equipment Capital: This is an annual capital provision for the lifecycle replacement of mining equipment. As a result, this expenditure tends to have periods of relative stability and cyclical periods of elevated expenditure associated with major rebuilds and acquisition of new equipment as reflected in the current capital expenditure. Overall, mine and surface equipment capital expenditure during stable years averages approximately $8.58 million per annum and periods of elevated expenditure are associated with expenditure of up to $15.83 million between FY2024 and FY2042. Thereafter until FY2056, mine and surface equipment capital costs are budgeted at levels of $11.83 million to $21.83 million, reducing progressively to $3.50 million in FY2064; Capitalised Development: Capitalised development is the part of primary development such as footwall levels and access ramps, which extends LoM or optimises the LoM plan. The LoM Capitalised Development Capital budget ranges from $9.12 million to $32.71 million per annum between FY2024 and FY2060. The level of expenditure is significantly lower than the $41.92 million to $42.93 million in FY2022 and FY2023. Capital allowance per annum after FY2060 reduces progressively to approximately $410 thousand in FY2069 due to significantly low levels of capitalised developments planned/required; Project Capital: The TSF Stage 5/6 Project is the most significant project in the LoM of East Boulder Mine and this is forecast to end in FY2026. The TSF project will account for the bulk of the Project Capital expenditure per annum until FY2026. Subsequent to FY2026, no Project Capital is provided for as there are no major projects planned; Other Capital: Other capital generally accounts for scheduled light vehicle replacements and minor infrastructural upgrades as required. There is an annual provision of $750 thousand over the period FY2024 to FY2026, after which the annual provision is $350 thousand until FY2050. 281 Based on the historical capital expenditure and the detail associated with the various capital budgets, the Qualified Person is of the view that sufficient mining capital provisions have been made to support the existing operations. 18.2.3.3 Concentrator Capital Due to the concentrator historically having been operated at 75%, there has been limited capital expenditure for sustaining the ore processing operations, with capital in the order of less than $1 million spend annually. Elevated expenditure for process equipment, buildings and infrastructure amounting to $4.88 million is planned over the period FY2024 and FY2026. The capital budget for the concentrator makes for modest provisions of $230 thousand to $150 thousand in FY2027 and FY2028, respectively. The Qualified Person does not expect the sustaining capital costs for the concentrator to significantly increase in future due to plant being operated continuously at higher than 75% utilisation. 18.2.3.4 Environmental Capital Environmental capital expenditure encompasses TSF expansions, designs and implementation and associated infrastructure maintenance in addition to water and waste rock management and groundwater expenditure. The Environmental Capital budget includes an annual provision of $340 thousand for labour for the Lewis Gulch TSF embankment in FY2024 and FY2025, and the same annual provisions for Dry Fork Waste Rock Storage Area labour between FY2026 and FY2028. Approximately $37 million is planned to be spent on the Dry Fork Waste Rock Storage Area Phase 1 development between FY2024 and FY2026 although the total expenditure for Phase 1 to Phase 4 and closure spread over the LoM is approximately $50.70 million. Capital allocations for Phases 2, 3 and 4 construction and lining are respectively $2.90 million in FY2030, $7.50 million in FY2035 and $6.30 million in FY2047. The budget includes $5.50 million for closure of the Dry Fork Waste Rock Storage Area between FY2055 and FY2056. Approximately $5.30 million is budgeted for Stage 6 TSF closure during the FY2031 to FY2033 period. Approximately $66.40 million is planned to be spent on the Lewis Gulch TSF infrastructure and topsoil relocation, embarkment construction and lining, pipelines and underdrain installation and closure over the LoM. Further key elements of the capital expenditure under the environmental budget include an allowance of $100 million for the development of a new TSF between FY2039 and FY2042, an allowance of $7.50 million for the closure of the future TSF. The aggregate $296.78 million LoM environmental capital costs includes $25 million for final closure. There is no environmental capital provision in certain years over which no tailings, waste rock or other environmental projects are anticipated. 282 Table 64: East Boulder Mine Actual and LoM Capital Schedule FY2021 FY2022 FY2023 FY2024 FY2025 FY2026 FY2027 FY2028 FY2029 FY2030 FY2031 FY2032 FY2033 Mine and Surface Equipment US$ 10 077 403 9 560 073 15 921 454 13 643 350 14 308 208 12 150 000 8 555 000 13 295 000 8 575 000 8 325 000 8 475 000 8 325 000 8 475 000 Capitalised Development US$ 20 937 932 42 929 859 40 909 905 14 142 776 23 953 712 19 213 790 16 935 881 21 557 847 26 396 405 20 635 994 26 090 959 17 547 299 21 643 117 Project (Excluding Met Complex) US$ 7 629 862 12 888 929 18 312 355 10 321 345 8 400 866 5 082 980 - - - - - - - Other US$ 467 024 2 556 275 20 592 830 375 000 750 000 750 000 750 000 750 000 750 000 750 000 350 000 350 000 350 000 Environmental US$ 1 478 500 2 001 012 2 541 538 2 590 000 9 625 000 28 440 000 30 340 000 31 740 000 8 000 000 5 900 000 2 000 000 2 000 000 1 300 000 Total US$ 40 590 721 69 936 148 98 278 081 41 072 471 57 037 786 65 636 770 56 580 881 67 342 847 43 721 405 35 610 994 36 915 959 28 222 299 31 768 117 FY2034 FY2035 FY2036 FY2037 FY2038 FY2039 FY2040 FY2041 FY2042 FY2043 FY2044 FY2045 FY2046 Mine and Surface Equipment US$ 15 825 000 8 475 000 8 325 000 8 325 000 8 325 000 8 325 000 8 325 000 8 325 000 8 325 000 15 825 000 15 825 000 15 825 000 11 825 000 Capitalised Development US$ 24 491 233 17 592 750 16 994 541 24 665 514 19 607 027 32 707 987 28 063 542 21 339 468 19 077 896 19 867 341 26 261 295 27 838 919 25 026 256 Project (Excluding Met Complex) US$ - - - - - - - - - - - - - Other US$ 350 000 350 000 350 000 350 000 350 000 350 000 350 000 350 000 350 000 350 000 350 000 350 000 350 000 Environmental US$ - 7 500 000 - - - 33 000 000 28 000 000 25 000 000 25 000 000 2 500 000 2 500 000 2 500 000 6 300 000 Total US$ 40 666 233 33 917 750 25 669 541 33 340 514 28 282 027 74 382 987 64 738 542 55 014 468 52 752 896 38 542 341 44 936 295 46 513 919 43 501 256 FY2047 FY2048 FY2049 FY2050 FY2051 FY2052 FY2053 FY2054 FY2055 FY2056 FY2057 FY2058 FY2059 Mine and Surface Equipment US$ 17 825 000 17 825 000 17 825 000 17 825 000 19 825 000 21 825 000 21 825 000 21 825 000 21 825 000 21 825 000 10 300 000 10 300 000 10 300 000 Capitalised Development US$ 18 780 035 17 585 915 17 377 362 16 095 841 22 993 230 11 350 741 18 306 166 25 201 042 17 584 142 9 467 052 9 357 744 14 717 887 9 136 291 Project (Excluding Met Complex) US$ - - - - - - - - - - - - - Other US$ 350 000 350 000 350 000 350 000 - - - - - - - - - Environmental US$ - - - - - - - - 3 000 000 5 000 000 12 500 000 12 500 000 5 000 000 Total US$ 36 955 035 35 760 915 35 552 362 34 270 841 42 818 230 33 175 741 40 131 166 47 026 042 42 409 142 36 292 052 32 157 744 37 517 887 24 436 291 FY2060 FY2061 FY2062 FY2063 FY2064 FY2065 FY2066 FY2067 FY2068 FY2069 Mine and Surface Equipment US$ 3 500 000 3 500 000 3 500 000 3 500 000 3 500 000 - - - - - Capitalised Development US$ 9 239 476 4 116 697 470 918 5 006 691 473 063 470 107 469 455 427 711 355 150 409 579 Project (Excluding Met Complex) US$ - - - - - - - - - - Other US$ - - - - - - - - - - Environmental US$ - - - - - - - - - - Total US$ 12 739 476 7 616 697 3 970 918 8 506 691 3 973 063 470 107 469 455 427 711 355 150 409 579 Budget Budget Budget Budget Cost Centre Unit Cost Centre Unit Cost Centre Unit Actual Cost Centre Unit
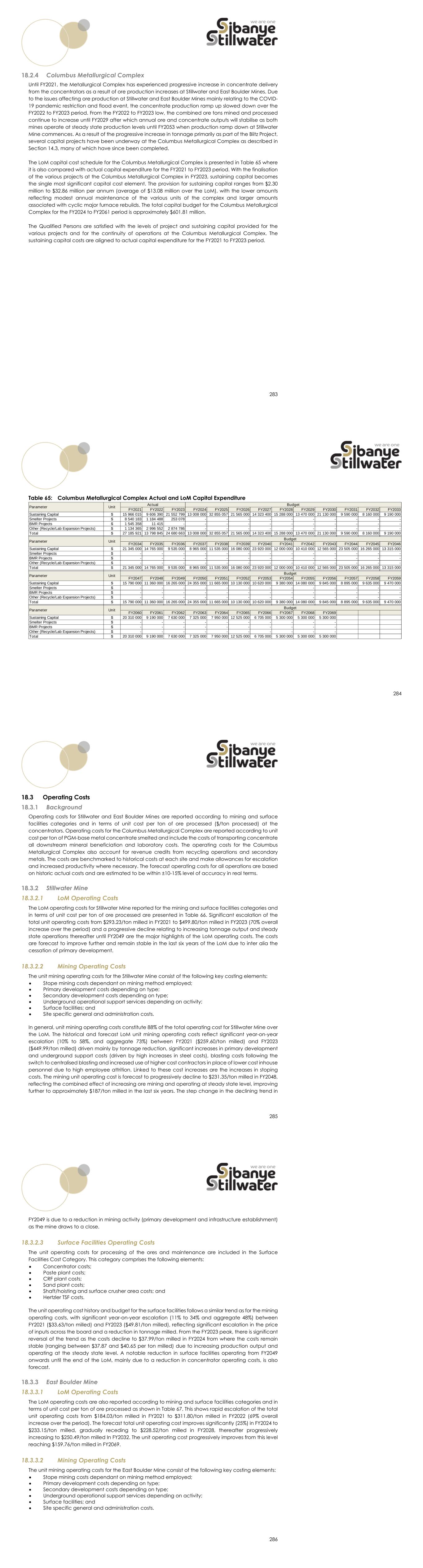
283 Columbus Metallurgical Complex Until FY2021, the Metallurgical Complex has experienced progressive increase in concentrate delivery from the concentrators as a result of ore production increases at Stillwater and East Boulder Mines. Due to the issues affecting ore production at Stillwater and East Boulder Mines mainly relating to the COVID- 19 pandemic restriction and flood event, the concentrate production ramp up slowed down over the FY2022 to FY2023 period. From the FY2022 to FY2023 low, the combined ore tons mined and processed continue to increase until FY2029 after which annual ore and concentrate outputs will stabilise as both mines operate at steady state production levels until FY2053 when production ramp down at Stillwater Mine commences. As a result of the progressive increase in tonnage primarily as part of the Blitz Project, several capital projects have been underway at the Columbus Metallurgical Complex as described in Section 14.3, many of which have since been completed. The LoM capital cost schedule for the Columbus Metallurgical Complex is presented in Table 65 where it is also compared with actual capital expenditure for the FY2021 to FY2023 period. With the finalisation of the various projects at the Columbus Metallurgical Complex in FY2023, sustaining capital becomes the single most significant capital cost element. The provision for sustaining capital ranges from $2.30 million to $32.86 million per annum (average of $13.08 million over the LoM), with the lower amounts reflecting modest annual maintenance of the various units of the complex and larger amounts associated with cyclic major furnace rebuilds. The total capital budget for the Columbus Metallurgical Complex for the FY2024 to FY2061 period is approximately $601.81 million. The Qualified Persons are satisfied with the levels of project and sustaining capital provided for the various projects and for the continuity of operations at the Columbus Metallurgical Complex. The sustaining capital costs are aligned to actual capital expenditure for the FY2021 to FY2023 period. 284 Table 65: Columbus Metallurgical Complex Actual and LoM Capital Expenditure FY2021 FY2022 FY2023 FY2024 FY2025 FY2026 FY2027 FY2028 FY2029 FY2030 FY2031 FY2032 FY2033 Sustaining Capital $ 15 966 015 9 606 390 21 552 799 13 008 000 32 855 057 21 565 000 14 323 400 15 288 000 13 470 000 21 130 000 9 590 000 8 160 000 9 190 000 Smelter Projects $ 8 540 183 1 184 488 253 078 - - - - - - - - - - BMR Projects $ 1 545 358 11 415 - - - - - - - - - - - Other (Recycle/Lab Expansion Projects) $ 1 134 365 2 996 552 2 874 786 - - - - - - - - - - Total $ 27 185 921 13 798 845 24 680 663 13 008 000 32 855 057 21 565 000 14 323 400 15 288 000 13 470 000 21 130 000 9 590 000 8 160 000 9 190 000 FY2034 FY2035 FY2036 FY2037 FY2038 FY2039 FY2040 FY2041 FY2042 FY2043 FY2044 FY2045 FY2046 Sustaining Capital $ 21 345 000 14 765 000 9 535 000 8 965 000 11 535 000 16 080 000 23 920 000 12 000 000 10 410 000 12 565 000 23 505 000 16 265 000 13 315 000 Smelter Projects $ - - - - - - - - - - - - - BMR Projects $ - - - - - - - - - - - - - Other (Recycle/Lab Expansion Projects) $ - - - - - - - - - - - - - Total $ 21 345 000 14 765 000 9 535 000 8 965 000 11 535 000 16 080 000 23 920 000 12 000 000 10 410 000 12 565 000 23 505 000 16 265 000 13 315 000 FY2047 FY2048 FY2049 FY2050 FY2051 FY2052 FY2053 FY2054 FY2055 FY2056 FY2057 FY2058 FY2059 Sustaining Capital $ 15 790 000 11 360 000 16 265 000 24 355 000 11 665 000 10 130 000 10 620 000 9 380 000 14 080 000 9 845 000 8 895 000 9 635 000 9 470 000 Smelter Projects $ - - - - - - - - - - - - - BMR Projects $ - - - - - - - - - - - - - Other (Recycle/Lab Expansion Projects) $ - - - - - - - - - - - - - Total $ 15 790 000 11 360 000 16 265 000 24 355 000 11 665 000 10 130 000 10 620 000 9 380 000 14 080 000 9 845 000 8 895 000 9 635 000 9 470 000 FY2060 FY2061 FY2062 FY2063 FY2064 FY2065 FY2066 FY2067 FY2068 FY2069 Sustaining Capital $ 20 310 000 9 190 000 7 630 000 7 325 000 7 950 000 12 525 000 6 705 000 5 300 000 5 300 000 5 300 000 Smelter Projects $ - - - - - - - - - - BMR Projects $ - - - - - - - - - - Other (Recycle/Lab Expansion Projects) $ - - - - - - - - - - Total $ 20 310 000 9 190 000 7 630 000 7 325 000 7 950 000 12 525 000 6 705 000 5 300 000 5 300 000 5 300 000 Parameter Unit Budget Budget Budget Budget Unit Parameter Actual Parameter Parameter Unit Unit 285 Operating Costs Background Operating costs for Stillwater and East Boulder Mines are reported according to mining and surface facilities categories and in terms of unit cost per ton of ore processed ($/ton processed) at the concentrators. Operating costs for the Columbus Metallurgical Complex are reported according to unit cost per ton of PGM-base metal concentrate smelted and include the costs of transporting concentrate all downstream mineral beneficiation and laboratory costs. The operating costs for the Columbus Metallurgical Complex also account for revenue credits from recycling operations and secondary metals. The costs are benchmarked to historical costs at each site and make allowances for escalation and increased productivity where necessary. The forecast operating costs for all operations are based on historic actual costs and are estimated to be within ±10-15% level of accuracy in real terms. Stillwater Mine 18.3.2.1 LoM Operating Costs The LoM operating costs for Stillwater Mine reported for the mining and surface facilities categories and in terms of unit cost per ton of ore processed are presented in Table 66. Significant escalation of the total unit operating costs from $293.23/ton milled in FY2021 to $499.80/ton milled in FY2023 (70% overall increase over the period) and a progressive decline relating to increasing tonnage output and steady state operations thereafter until FY2049 are the major highlights of the LoM operating costs. The costs are forecast to improve further and remain stable in the last six years of the LoM due to inter alia the cessation of primary development. 18.3.2.2 Mining Operating Costs The unit mining operating costs for the Stillwater Mine consist of the following key costing elements: Stope mining costs dependant on mining method employed; Primary development costs depending on type; Secondary development costs depending on type; Underground operational support services depending on activity; Surface facilities; and Site specific general and administration costs. In general, unit mining operating costs constitute 88% of the total operating cost for Stillwater Mine over the LoM. The historical and forecast LoM unit mining operating costs reflect significant year-on-year escalation (10% to 58%, and aggregate 73%) between FY2021 ($259.60/ton milled) and FY2023 ($449.99/ton milled) driven mainly by tonnage reduction, significant increases in primary development and underground support costs (driven by high increases in steel costs), blasting costs following the switch to centralised blasting and increased use of higher cost contractors in place of lower cost inhouse personnel due to high employee attrition. Linked to these cost increases are the increases in stoping costs. The mining unit operating cost is forecast to progressively decline to $231.35/ton milled in FY2048, reflecting the combined effect of increasing ore mining and operating at steady state level, improving further to approximately $187/ton milled in the last six years. The step change in the declining trend in 286 FY2049 is due to a reduction in mining activity (primary development and infrastructure establishment) as the mine draws to a close. 18.3.2.3 Surface Facilities Operating Costs The unit operating costs for processing of the ores and maintenance are included in the Surface Facilities Cost Category. This category comprises the following elements: Concentrator costs; Paste plant costs; CRF plant costs; Sand plant costs; Shaft/hoisting and surface crusher area costs; and Hertzler TSF costs. The unit operating cost history and budget for the surface facilities follows a similar trend as for the mining operating costs, with significant year-on-year escalation (11% to 34% and aggregate 48%) between FY2021 ($33.63/ton milled) and FY2023 ($49.81/ton milled), reflecting significant escalation in the price of inputs across the board and a reduction in tonnage milled. From the FY2023 peak, there is significant reversal of the trend as the costs decline to $37.99/ton milled in FY2024 from where the costs remain stable (ranging between $37.87 and $40.65 per ton milled) due to increasing production output and operating at the steady state level. A notable reduction in surface facilities operating from FY2049 onwards until the end of the LoM, mainly due to a reduction in concentrator operating costs, is also forecast. East Boulder Mine 18.3.3.1 LoM Operating Costs The LoM operating costs are also reported according to mining and surface facilities categories and in terms of unit cost per ton of ore processed as shown in Table 67. This shows rapid escalation of the total unit operating costs from $184.03/ton milled in FY2021 to $311.80/ton milled in FY2022 (69% overall increase over the period). The forecast total unit operating cost improves significantly (25%) in FY2024 to $233.15/ton milled, gradually receding to $228.52/ton milled in FY2028, thereafter progressively increasing to $250.49/ton milled In FY2032. The unit operating cost progressively improves from this level reaching $159.76/ton milled in FY2069. 18.3.3.2 Mining Operating Costs The unit mining operating costs for the East Boulder Mine consist of the following key costing elements: Stope mining costs dependant on mining method employed; Primary development costs depending on type; Secondary development costs depending on type; Underground operational support services depending on activity; Surface facilities; and Site specific general and administration costs.
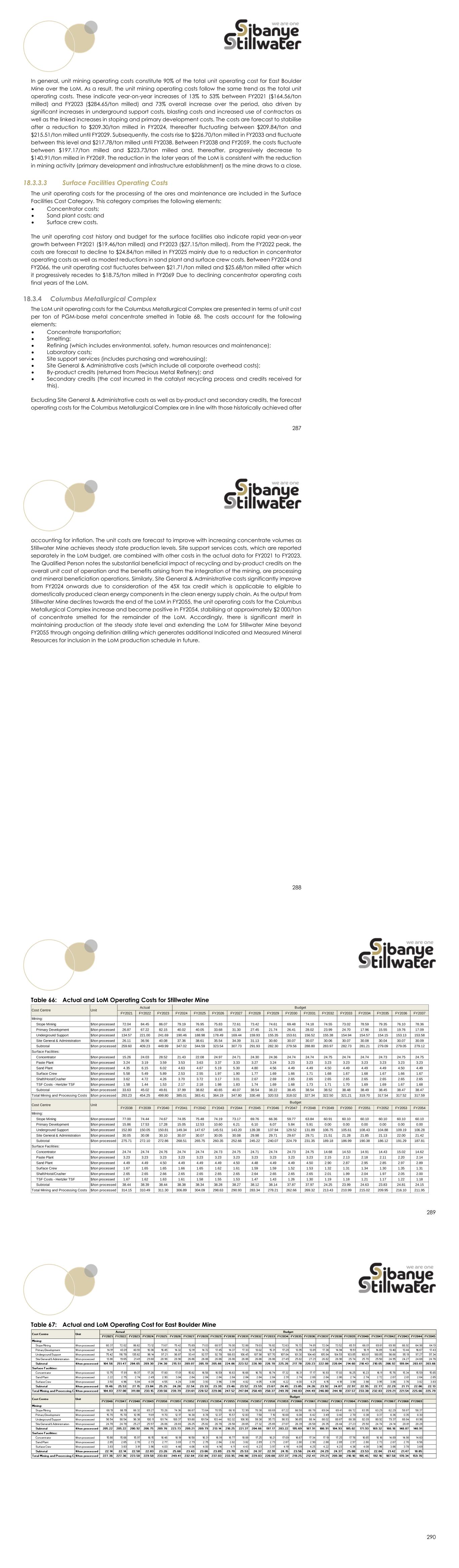
287 In general, unit mining operating costs constitute 90% of the total unit operating cost for East Boulder Mine over the LoM. As a result, the unit mining operating costs follow the same trend as the total unit operating costs. These indicate year-on-year increases of 13% to 53% between FY2021 ($164.56/ton milled) and FY2023 ($284.65/ton milled) and 73% overall increase over the period, also driven by significant increases in underground support costs, blasting costs and increased use of contractors as well as the linked increases in stoping and primary development costs. The costs are forecast to stabilise after a reduction to $209.30/ton milled in FY2024, thereafter fluctuating between $209.84/ton and $215.51/ton milled until FY2029. Subsequently, the costs rise to $226.70/ton milled in FY2033 and fluctuate between this level and $217.78/ton milled until FY2038. Between FY2038 and FY2059, the costs fluctuate between $197.17/ton milled and $223.73/ton milled and, thereafter, progressively decrease to $140.91/ton milled in FY2069. The reduction in the later years of the LoM is consistent with the reduction in mining activity (primary development and infrastructure establishment) as the mine draws to a close. 18.3.3.3 Surface Facilities Operating Costs The unit operating costs for the processing of the ores and maintenance are included in the Surface Facilities Cost Category. This category comprises the following elements: Concentrator costs; Sand plant costs; and Surface crew costs. The unit operating cost history and budget for the surface facilities also indicate rapid year-on-year growth between FY2021 ($19.46/ton milled) and FY2023 ($27.15/ton milled). From the FY2022 peak, the costs are forecast to decline to $24.84/ton milled in FY2025 mainly due to a reduction in concentrator operating costs as well as modest reductions in sand plant and surface crew costs. Between FY2024 and FY2066, the unit operating cost fluctuates between $21.71/ton milled and $25.68/ton milled after which it progressively recedes to $18.75/ton milled in FY2069 Due to declining concentrator operating costs final years of the LoM. Columbus Metallurgical Complex The LoM unit operating costs for the Columbus Metallurgical Complex are presented in terms of unit cost per ton of PGM-base metal concentrate smelted in Table 68. The costs account for the following elements: Concentrate transportation; Smelting; Refining (which includes environmental, safety, human resources and maintenance); Laboratory costs; Site support services (includes purchasing and warehousing); Site General & Administrative costs (which include all corporate overhead costs); By-product credits (returned from Precious Metal Refinery); and Secondary credits (the cost incurred in the catalyst recycling process and credits received for this). Excluding Site General & Administrative costs as well as by-product and secondary credits, the forecast operating costs for the Columbus Metallurgical Complex are in line with those historically achieved after 288 accounting for inflation. The unit costs are forecast to improve with increasing concentrate volumes as Stillwater Mine achieves steady state production levels. Site support services costs, which are reported separately in the LoM budget, are combined with other costs in the actual data for FY2021 to FY2023. The Qualified Person notes the substantial beneficial impact of recycling and by-product credits on the overall unit cost of operation and the benefits arising from the integration of the mining, ore processing and mineral beneficiation operations. Similarly, Site General & Administrative costs significantly improve from FY2024 onwards due to consideration of the 45X tax credit which is applicable to eligible to domestically produced clean energy components in the clean energy supply chain. As the output from Stillwater Mine declines towards the end of the LoM in FY2055, the unit operating costs for the Columbus Metallurgical Complex increase and become positive in FY2054, stabilising at approximately $2 000/ton of concentrate smelted for the remainder of the LoM. Accordingly, there is significant merit in maintaining production at the steady state level and extending the LoM for Stillwater Mine beyond FY2055 through ongoing definition drilling which generates additional Indicated and Measured Mineral Resources for inclusion in the LoM production schedule in future. 289 Table 66: Actual and LoM Operating Costs for Stillwater Mine FY2021 FY2022 FY2023 FY2024 FY2025 FY2026 FY2027 FY2028 FY2029 FY2030 FY2031 FY2032 FY2033 FY2034 FY2035 FY2036 FY2037 Mining: Stope Mining $/ton processed 72.04 84.45 86.07 79.19 76.95 75.83 72.61 73.42 74.61 69.48 74.18 74.55 73.02 78.59 79.35 76.10 78.36 Primary Development $/ton processed 26.87 67.22 82.15 40.02 40.05 33.68 31.30 27.45 21.74 26.41 28.02 23.99 24.70 17.96 15.55 19.76 17.09 Underground Support $/ton processed 134.57 221.00 241.69 190.46 188.98 178.49 169.44 159.93 155.35 153.61 156.52 155.38 154.94 154.57 154.15 153.13 153.58 Site General & Administration $/ton processed 26.11 36.56 40.08 37.36 38.61 35.54 34.39 31.13 30.60 30.07 30.07 30.06 30.07 30.08 30.04 30.07 30.09 Subtotal $/ton processed 259.60 409.23 449.99 347.02 344.59 323.54 307.73 291.93 282.30 279.56 288.80 283.97 282.73 281.21 279.09 279.05 279.12 Surface Facilities: Concentrator $/ton processed 15.26 24.03 28.52 21.43 22.08 24.97 24.71 24.30 24.36 24.74 24.74 24.75 24.74 24.74 24.73 24.75 24.75 Paste Plant $/ton processed 3.24 3.19 3.59 3.53 3.63 3.37 3.33 3.27 3.24 3.23 3.23 3.23 3.23 3.23 3.23 3.23 3.23 Sand Plant $/ton processed 4.35 6.15 6.02 4.63 4.67 5.19 5.30 4.80 4.56 4.49 4.49 4.50 4.49 4.49 4.49 4.50 4.49 Surface Crew $/ton processed 5.58 5.49 5.89 2.53 2.55 1.97 1.90 1.77 1.69 1.66 1.71 1.68 1.67 1.68 1.67 1.66 1.67 Shaft/Hoist/Crusher $/ton processed 3.62 4.72 4.26 3.70 3.72 3.17 3.01 2.67 2.69 2.65 2.65 2.65 2.65 2.65 2.65 2.65 2.65 TSF Costs - Hertzler TSF $/ton processed 1.58 1.44 1.53 2.17 2.18 1.98 1.83 1.74 1.69 1.68 1.73 1.71 1.70 1.69 1.69 1.67 1.68 Subtotal $/ton processed 33.63 45.02 49.81 37.99 38.82 40.65 40.07 38.54 38.22 38.45 38.54 38.52 38.48 38.49 38.45 38.47 38.47 Total Mining and Processing Costs $/ton processed 293.23 454.25 499.80 385.01 383.41 364.19 347.80 330.48 320.53 318.02 327.34 322.50 321.21 319.70 317.54 317.52 317.59 FY2038 FY2039 FY2040 FY2041 FY2042 FY2043 FY2044 FY2045 FY2046 FY2047 FY2048 FY2049 FY2050 FY2051 FY2052 FY2053 FY2054 Mining: Stope Mining $/ton processed 77.00 74.44 74.67 74.05 75.48 74.19 73.17 69.76 66.36 59.77 63.84 60.91 60.10 60.10 60.10 60.10 60.10 Primary Development $/ton processed 15.86 17.53 17.28 15.05 12.53 10.60 6.21 6.10 6.07 5.84 5.91 0.00 0.00 0.00 0.00 0.00 0.00 Underground Support $/ton processed 152.80 150.05 150.81 149.34 147.67 145.51 143.20 139.38 137.94 129.52 131.89 106.75 105.61 108.43 104.88 109.19 106.28 Site General & Administration $/ton processed 30.05 30.08 30.10 30.07 30.07 30.05 30.08 29.98 29.71 29.67 29.71 21.51 21.28 21.85 21.13 22.00 21.42 Subtotal $/ton processed 275.71 272.10 272.86 268.51 265.75 260.35 252.66 245.22 240.07 224.79 231.35 189.18 186.99 190.38 186.12 191.29 187.81 Surface Facilities: Concentrator $/ton processed 24.74 24.74 24.76 24.74 24.74 24.73 24.75 24.71 24.74 24.73 24.75 14.68 14.53 14.91 14.43 15.02 14.62 Paste Plant $/ton processed 3.23 3.23 3.23 3.23 3.23 3.23 3.23 3.23 3.23 3.23 3.23 2.15 2.13 2.18 2.11 2.20 2.14 Sand Plant $/ton processed 4.49 4.49 4.50 4.49 4.49 4.49 4.50 4.48 4.49 4.49 4.50 2.90 2.87 2.95 2.85 2.97 2.89 Surface Crew $/ton processed 1.67 1.65 1.65 1.66 1.65 1.62 1.61 1.59 1.59 1.52 1.53 1.32 1.31 1.34 1.30 1.35 1.31 Shaft/Hoist/Crusher $/ton processed 2.65 2.65 2.66 2.65 2.65 2.65 2.65 2.64 2.65 2.65 2.65 2.01 1.99 2.04 1.97 2.05 2.00 TSF Costs - Hertzler TSF $/ton processed 1.67 1.62 1.63 1.61 1.58 1.55 1.53 1.47 1.43 1.26 1.30 1.19 1.18 1.21 1.17 1.22 1.18 Subtotal $/ton processed 38.44 38.39 38.44 38.38 38.34 38.28 38.27 38.12 38.14 37.87 37.97 24.25 23.99 24.63 23.83 24.81 24.15 Total Mining and Processing Costs $/ton processed 314.15 310.49 311.30 306.89 304.09 298.63 290.93 283.34 278.21 262.66 269.32 213.43 210.99 215.02 209.95 216.10 211.95 Cost Centre Unit Actual Cost Centre Unit Budget Budget 290 Table 67: Actual and LoM Operating Cost for East Boulder Mine

291 Table 68: Actual and LoM Operating Costs for the Columbus Metallurgical Complex FY2021 FY2022 FY2023 FY2024 FY2025 FY2026 FY2027 FY2028 FY2029 FY2030 FY2031 FY2032 FY2033 FY2034 FY2035 FY2036 FY2037 Mineral Beneficiation Costs (Off-mine): Concentrate Transportation $/ton Smelted 113.76 353.79 235.67 132.53 134.65 141.28 150.90 152.35 152.56 154.10 153.94 152.10 151.22 149.78 147.27 146.13 144.95 Smelting $/ton Smelted 798.66 886.77 884.31 872.38 917.04 854.90 815.20 768.92 746.00 739.87 738.56 737.72 738.30 743.50 731.11 740.71 738.59 Refining $/ton Smelted 178.82 205.83 198.29 194.31 276.82 181.56 174.33 163.89 157.03 157.31 153.31 152.30 152.79 151.89 148.54 147.88 147.17 Laboratory $/ton Smelted 124.31 212.57 207.34 213.02 267.57 196.93 186.37 174.05 167.96 166.33 165.99 165.77 165.92 167.32 164.02 166.58 166.02 Columbus Support Services $/ton Smelted - - - 262.81 304.24 230.23 216.68 202.27 196.18 193.34 195.05 195.21 195.22 198.20 194.57 199.40 198.90 Site General & Administrative $/ton Smelted 1 268.20 1 516.69 1 629.87 327.78 342.60 318.71 299.76 277.66 266.73 263.80 263.17 262.77 263.05 265.53 259.62 264.20 263.19 By-product Credits $/ton Smelted -2 331.10 -2 206.89 -1 135.71 -871.30 -865.70 -925.01 -990.54 -1 003.83 -995.29 -1 018.20 -987.66 -969.41 -967.61 -959.62 -935.13 -908.88 -896.55 Secondary Credits (including Interest) $/ton Smelted -3 137.82 -2 716.68 -863.55 -513.63 -775.73 -990.35 -1 065.25 -1 074.07 -1 027.58 -1 073.29 -972.40 -937.53 -943.14 -884.63 -858.05 -779.57 -758.89 Total Costs $/ton Smelted -2 985.17 -1 747.92 1 156.21 617.90 601.49 8.24 -212.56 -338.76 -336.42 -416.74 -290.05 -241.06 -244.26 -168.03 -148.04 -23.55 3.39 FY2038 FY2039 FY2040 FY2041 FY2042 FY2043 FY2044 FY2045 FY2046 FY2047 FY2048 FY2049 FY2050 FY2051 FY2052 FY2053 FY2054 Mineral Beneficiation Costs (Off-mine): Concentrate Transportation $/ton Smelted 145.94 144.52 144.07 141.65 140.87 142.35 143.04 142.15 138.27 138.84 138.58 144.63 144.37 151.69 147.26 158.29 150.26 Smelting $/ton Smelted 739.76 731.40 731.38 729.82 725.74 719.75 722.63 722.05 724.66 728.02 730.20 733.39 752.40 734.41 731.65 758.58 1 095.18 Refining $/ton Smelted 150.17 148.53 148.25 148.23 147.47 145.51 145.38 145.10 142.62 143.34 144.12 148.53 152.78 149.08 148.56 153.13 232.80 Laboratory $/ton Smelted 166.32 164.10 164.09 163.68 162.59 161.00 161.77 161.62 162.32 163.22 163.79 164.63 169.69 164.90 164.17 171.33 260.85 Columbus Support Services $/ton Smelted 197.53 194.70 194.81 194.13 192.72 191.18 192.55 192.48 195.23 196.35 196.84 195.61 201.75 195.79 194.77 204.51 309.40 Site General & Administrative $/ton Smelted 263.75 259.76 259.75 259.00 257.05 254.20 255.57 255.29 256.54 258.14 259.18 260.71 269.78 261.20 259.88 272.73 433.40 By-product Credits $/ton Smelted -924.65 -917.55 -912.33 -905.24 -901.55 -900.39 -898.09 -893.17 -849.37 -847.64 -849.40 -910.47 -917.63 -946.33 -931.86 -970.53 -996.09 Secondary Credits (including Interest) $/ton Smelted -837.68 -853.04 -849.33 -855.91 -861.15 -843.66 -821.86 -812.49 -723.06 -710.92 -720.40 -827.30 -841.61 -845.90 -854.38 -813.97 -958.57 Total Costs $/ton Smelted -98.86 -127.59 -119.31 -124.64 -136.25 -130.05 -99.01 -86.96 47.22 69.36 62.90 -90.27 -68.45 -135.15 -139.95 -65.93 527.21 FY2055 FY2056 FY2057 FY2058 FY2059 FY2060 FY2061 FY2062 FY2063 FY2064 FY2065 FY2066 FY2067 FY2068 FY2069 Mineral Beneficiation Costs (Off-mine): Concentrate Transportation $/ton Smelted 131.15 132.02 131.99 132.15 135.27 139.88 139.58 138.14 141.37 135.51 130.66 128.08 127.97 126.00 132.31 Smelting $/ton Smelted 1 907.99 1 828.31 1 727.55 1 813.24 1 772.31 1 836.25 1 822.45 1 828.10 1 876.67 1 770.08 1 723.08 1 686.05 1 708.55 1 669.60 2 919.11 Refining $/ton Smelted 424.00 406.02 383.01 402.61 394.00 409.68 406.46 407.42 419.26 393.55 381.68 372.62 377.73 368.37 655.08 Laboratory $/ton Smelted 477.01 455.82 429.02 451.81 440.92 457.92 454.25 455.76 468.67 440.33 427.83 417.99 423.97 413.61 745.94 Columbus Support Services $/ton Smelted 567.11 541.22 509.28 536.50 522.35 540.83 536.71 539.03 553.23 521.43 508.32 497.40 504.62 492.74 892.46 Site General & Administrative $/ton Smelted 821.36 783.33 735.24 776.14 756.60 787.12 780.53 783.23 806.41 755.54 733.10 715.43 726.17 707.58 1 303.99 By-product Credits $/ton Smelted -962.16 -889.90 -889.25 -899.22 -918.21 -962.61 -959.84 -948.87 -976.20 -923.49 -883.53 -860.25 -860.40 -841.99 -951.18 Secondary Credits (including Interest) $/ton Smelted -1 219.96 -1 152.02 -1 141.01 -1 160.80 -1 168.86 -1 215.50 -1 208.20 -1 199.77 -1 225.68 -1 173.86 -1 136.23 -1 113.14 -1 116.05 -1 097.92 -1 320.20 Total Costs $/ton Smelted 2 146.51 2 104.80 1 885.83 2 052.43 1 934.39 1 993.57 1 971.95 2 003.03 2 063.75 1 919.08 1 884.92 1 844.18 1 892.56 1 837.99 4 377.50 Cost Centre Unit Budget Budget Budget Cost Centre Unit Actual Cost Centre Unit 292 ECONOMIC ANALYSIS Background The LoM production, capital and operating cost schedules for Stillwater and East Boulder Mines and the Columbus Metallurgical Complex were employed for the economic viability testing of the LoM plans for each mine and the consolidated LoM plan for the Sibanye-Stillwater US PGM Operations. The consolidated LoM plan forms the basis for the Mineral Reserve estimates for Stillwater and East Boulder Mines reported in this TRS. The LoM production schedules for Stillwater and East Boulder Mines are discussed in Section 13.8 while the associated LoM capital and operating costs are presented in Section 18. No exchange rates have been used for the economic analysis as all metal prices and costs are reported in the US currency. The Qualified Persons for Mineral Reserves have considered and applied the macroeconomic trends, data and assumptions, marketing information and commodity prices, taxation and royalties provided by Sibanye-Stillwater set out below. The outputs of the economic viability testing are reliant on these forward-looking economic parameters and assumptions which may be subject to revision as circumstances change. Economic Viability Testing Method The Discounted Cash Flow (DCF) methodology has been used for the economic testing of the individual LoM plans and consolidated LoM Plan for Sibanye-Stillwater US PGM Operations and the Mineral Reserves for Stillwater and East Boulder Mines. The DCF model is referred to as the Ore Reserve Economic Test (ORET) Model. With the DCF approach, a negative cash flow or NPV indicates sub-economic production whereas a positive cash flow or NPV indicates economic production and that the declaration of Mineral Reserves is justified. The method, therefore, allows for the identification of sub- economic production for exclusion through production schedule tail cutting if the sub-economic production occurs towards the final years of the LoM. A first-pass LoM plan for each mine that included the LoM production schedule and all operating and capital expenses, manpower requirements, equipment replacement and purchase, and primary and secondary development including ventilation and haulages that are needed to execute the plan was incorporated into the ORET Model. The first pass LoM plans for Stillwater and East Boulder Mines were consolidated to produce a single LoM plan for the Sibanye-Stillwater US PGM Operations. Cash flows have been forecast and discounted back to an NPV using a range of real discount rates from 2.5% to 7.5%. The LoMs for Stillwater and East Boulder Mines are 31 and 46 years, respectively. The 31-year LoM plan for Stillwater Mine contemplates driving footwall lateral declines and other infrastructure into areas currently classified as Inferred Mineral Resources, which are not scheduled for mining in the current LoM plan for the mine. Both mines have expanded in this manner over the years. Accordingly, the fact that Stillwater and East Boulder Mines have different LoMs is not a material issue. The ORET Model start date is 1 January 2024 and the LoM for the Sibanye-Stillwater US PGM Operations is 46 years. Financial years commencing 1 January have been used and each year’s cash flow is deemed to have occurred at the end of the period – i.e., on December 31. No assessed losses, 293 shareholder loan accounts or other balance sheet circumstances have been accounted for and, therefore, the cash flows are ungeared. Company tax and state royalty calculations have been incorporated into the computation of cash flows. Economic Assumptions and Forecasts Taxation With guidance from Sibanye-Stillwater, the Qualified Person for Mineral Reserves applied an aggregate tax rate of 24.37% for economic testing of the individual and consolidated LoM Plan for the Sibanye- Stillwater US PGM Operations in support of the declaration of Mineral Reserves for Stillwater and East Boulder Mines. This rate is made up of the cash tax rates for the State of Montana and Federal taxes. Taxation is calculated on real cash flows. Metal Price Forecast For the economic viability testing of the individual and the consolidated LoM Plan for Sibanye-Stillwater US PGM Operations, the forward-looking palladium and platinum metal prices as summarised in Table 48 have been used, and the rationale for the price determination is set out in Section 16.4. These prices have also been submitted by Sibanye-Stillwater to the SEC for review and noting. Discount Rate Sibanye-Stillwater’s internal benchmark real discount rate for the US PGM operations as at 31 December 2023 is 5%, based on corporate planning guidance. The Qualified Person for Mineral Reserves reviewed the base data utilised for the calculation of this internal benchmark discount rate as well as the calculation methodology for reasonableness. From the review, the Qualified Person concluded that the 5% internal benchmark real discount rate is reasonable for the discounting of cash flows for the Sibanye- Stillwater US PGM Operations. DCF Results and Sensitivity Analysis DCF Model An abridged cash-flow model showing expected annual cash flows for Stillwater and East Boulder Mines and the combined Sibanye-Stillwater US PGM Operations is presented in Table 69. 294 Table 69: Abridged Cash Flow Results (Cont’d on the Next Page) East Boulder Mine 2024 2025 2026 2027 2028 2029 2030 2031 2032 2033 2034 2035 2036 2037 2038 2039 2040 2041 2042 2043 2044 2045 2046 2047 2048 2049 2050 2051 2052 2053 2054 2055 2056 2057 2058 Palladium ounces produced 143,597 143,559 152,262 168,074 168,074 168,074 168,074 168,074 168,074 168,074 170,633 170,837 166,311 166,685 165,883 164,572 161,648 166,158 168,122 168,945 167,331 169,225 167,512 163,621 162,983 165,309 149,922 163,018 163,490 162,924 161,450 148,792 157,021 167,276 158,651 Platinum ounces produced 41,169 41,158 43,653 48,186 48,186 48,186 48,186 48,186 48,186 48,186 48,920 48,978 47,680 47,788 47,558 47,182 46,344 47,637 48,200 48,436 47,973 48,516 48,025 46,909 46,726 47,393 42,982 46,736 46,872 46,709 46,287 42,658 45,017 47,957 45,484 Com bined ounces produced 184,766 184,717 195,915 216,260 216,260 216,260 216,260 216,260 216,260 216,260 219,552 219,815 213,991 214,473 213,440 211,753 207,992 213,795 216,321 217,380 215,304 217,741 215,536 210,530 209,709 212,702 192,903 209,754 210,362 209,633 207,736 191,450 202,039 215,233 204,135 Palladium revenues $m 179.5 179.4 190.3 210.1 210.1 210.1 210.1 210.1 210.1 210.1 213.3 213.5 207.9 208.4 207.4 205.7 202.1 207.7 210.2 211.2 209.2 211.5 209.4 204.5 203.7 206.6 187.4 203.8 204.4 203.7 201.8 186.0 196.3 209.1 198.3 Platinum revenues $m 51.5 51.4 54.6 60.2 60.2 60.2 60.2 60.2 60.2 60.2 61.1 61.2 59.6 59.7 59.4 59.0 57.9 59.5 60.2 60.5 60.0 60.6 60.0 58.6 58.4 59.2 53.7 58.4 58.6 58.4 57.9 53.3 56.3 59.9 56.9 Gross Revenues $m 231.0 230.9 244.9 270.3 270.3 270.3 270.3 270.3 270.3 270.3 274.4 274.8 267.5 268.1 266.8 264.7 260.0 267.2 270.4 271.7 269.1 272.2 269.4 263.2 262.1 265.9 241.1 262.2 263.0 262.0 259.7 239.3 252.5 269.0 255.2 Less Smelting, refining & transportation $m (23.4) (25.3) (22.1) (22.7) (21.5) (20.9) (20.7) (20.7) (20.7) (20.7) (20.5) (21.3) (20.5) (20.8) (20.7) (21.2) (21.2) (21.5) (21.8) (22.1) (21.8) (21.8) (21.9) (21.5) (21.4) (21.1) (19.5) (20.8) (21.1) (20.9) (29.6) (47.2) (47.5) (48.0) (47.6) Net Smelting Returns $m 207.5 205.6 222.8 247.6 248.8 249.4 249.6 249.6 249.6 249.6 253.9 253.5 246.9 247.3 246.1 243.4 238.8 245.8 248.6 249.6 247.3 250.4 247.5 241.7 240.8 244.8 221.6 241.4 241.8 241.1 230.1 192.1 205.0 221.1 207.6 Less Mine operating costs $m (122.5) (120.9) (121.3) (127.6) (120.5) (115.9) (134.3) (128.3) (139.3) (135.2) (129.0) (140.7) (135.2) (131.1) (133.9) (124.6) (126.7) (134.0) (137.3) (135.3) (129.3) (127.1) (131.1) (131.6) (135.4) (134.5) (131.6) (127.5) (142.0) (131.7) (125.3) (134.9) (139.2) (142.0) (133.9) Recycling credit - including interest income $m 7.9 11.9 15.1 16.7 16.7 15.8 16.4 14.6 14.2 14.4 13.7 13.5 11.8 11.7 12.9 13.2 12.9 13.7 14.0 13.6 13.0 13.1 11.7 11.2 11.3 12.8 11.8 12.2 12.8 11.1 14.0 19.8 19.6 20.7 20.0 Less Royalties $m (11.1) (11.0) (11.9) (13.3) (13.3) (13.4) (13.4) (13.4) (13.4) (13.4) (13.5) (13.5) (13.2) (13.2) (13.1) (13.0) (12.7) (13.1) (13.2) (13.3) (13.2) (13.3) (13.2) (12.9) (12.8) (13.0) (11.8) (12.9) (12.9) (12.8) (12.3) (10.4) (11.0) (11.9) (11.2) Less Production taxes $m (8.1) (8.1) (8.6) (9.4) (9.5) (9.5) (9.5) (9.5) (9.5) (9.5) (9.6) (9.6) (9.4) (9.4) (9.3) (9.2) (9.1) (9.3) (9.4) (9.4) (9.4) (9.5) (9.4) (9.2) (9.2) (9.3) (8.5) (9.2) (9.2) (9.2) (8.9) (7.7) (8.0) (8.6) (8.1) Less Insurance $m (4.1) (4.3) (4.2) (4.2) (4.1) (4.1) (4.1) (4.1) (4.1) (4.1) (4.1) (4.1) (4.1) (4.1) (4.1) (4.1) (4.1) (4.1) (4.1) (4.1) (4.1) (4.1) (4.1) (4.1) (4.1) (4.1) (4.0) (4.0) (4.1) (4.0) (4.5) (5.8) (5.8) (5.8) (5.8) EBITDA $m 69.6 73.2 91.8 109.8 118.0 122.4 104.8 108.9 97.6 101.9 111.4 99.1 97.0 101.2 98.5 105.7 99.1 98.9 98.6 101.1 104.4 109.5 101.4 95.1 90.6 96.7 77.5 100.1 86.6 94.4 93.1 53.2 60.6 73.6 68.5 Less Closure Costs $m - - - - - - - - - - - - - - - - - - - - - - - - - - - - - - - - - - - Net Income (loss) before incom e taxes $m 69.6 73.2 91.8 109.8 118.0 122.4 104.8 108.9 97.6 101.9 111.4 99.1 97.0 101.2 98.5 105.7 99.1 98.9 98.6 101.1 104.4 109.5 101.4 95.1 90.6 96.7 77.5 100.1 86.6 94.4 93.1 53.2 60.6 73.6 68.5 Less 24.37% Income Tax $m (17.0) (17.8) (22.4) (26.8) (28.8) (29.8) (25.5) (26.5) (23.8) (24.8) (27.1) (24.1) (23.6) (24.7) (24.0) (25.8) (24.2) (24.1) (24.0) (24.6) (25.4) (26.7) (24.7) (23.2) (22.1) (23.6) (18.9) (24.4) (21.1) (23.0) (22.7) (13.0) (14.8) (17.9) (16.7) Net Income (loss) $m 52.6 55.3 69.4 83.0 89.2 92.5 79.3 82.4 73.8 77.0 84.2 74.9 73.3 76.5 74.5 80.0 75.0 74.8 74.6 76.5 78.9 82.8 76.7 71.9 68.6 73.1 58.6 75.7 65.5 71.4 70.4 40.2 45.9 55.6 51.8 Less Capital Expenditure $m (47.2) (70.2) (73.5) (61.6) (72.3) (47.8) (42.0) (39.8) (30.7) (34.5) (47.2) (38.4) (28.5) (36.1) (31.8) (79.2) (71.8) (58.7) (56.0) (42.4) (52.0) (51.5) (47.6) (41.8) (39.2) (40.5) (41.2) (46.1) (36.1) (43.1) (51.5) (56.5) (46.1) (41.1) (47.2) NeT Cash Flow $m 5.4 (14.8) (4.0) 21.4 17.0 44.7 37.3 42.6 43.1 42.5 37.0 36.5 44.8 40.5 42.7 0.7 3.1 16.1 18.6 34.1 26.9 31.3 29.1 30.1 29.3 32.6 17.4 29.6 29.3 28.3 18.9 (16.3) (0.3) 14.6 4.7 Cumulative Cash Flow $m 5.4 (14.8) (4.0) 21.4 17.0 44.7 37.3 42.6 43.1 42.5 37.0 36.5 44.8 40.5 42.7 0.7 3.1 16.1 18.6 34.1 26.9 31.3 29.1 30.1 29.3 32.6 17.4 29.6 29.3 28.3 18.9 (16.3) (0.3) 14.6 4.7 East Boulder After Tax NPV5% $m 448.1 Stillwater Mine 2024 2025 2026 2027 2028 2029 2030 2031 2032 2033 2034 2035 2036 2037 2038 2039 2040 2041 2042 2043 2044 2045 2046 2047 2048 2049 2050 2051 2052 2053 2054 2055 2056 2057 2058 Palladium ounces produced 214,003 214,146 266,220 307,925 351,477 378,644 386,356 398,591 394,262 388,655 383,253 386,596 385,079 382,450 378,062 380,784 382,659 368,019 366,179 380,098 384,414 379,675 370,183 373,314 369,934 380,008 376,058 410,913 393,746 418,941 179,284 - - - - Platinum ounces produced 62,550 62,591 77,812 90,001 102,731 110,672 112,926 116,502 115,236 113,597 112,019 112,996 112,552 111,784 110,501 111,297 111,845 107,566 107,028 111,097 112,358 110,973 108,199 109,114 108,126 111,070 109,916 120,103 115,086 122,450 52,402 - - - - Com bined ounces produced 276,553 276,737 344,032 397,926 454,208 489,316 499,282 515,092 509,499 502,252 495,272 499,592 497,632 494,234 488,564 492,081 494,504 475,585 473,207 491,195 496,772 490,648 478,382 482,427 478,060 491,078 485,974 531,017 508,832 541,390 231,686 - - - - Palladium revenues $m 267.5 267.7 332.8 384.9 439.3 473.3 482.9 498.2 492.8 485.8 479.1 483.2 481.3 478.1 472.6 476.0 478.3 460.0 457.7 475.1 480.5 474.6 462.7 466.6 462.4 475.0 470.1 513.6 492.2 523.7 224.1 - - - - Platinum revenues $m 78.2 78.2 97.3 112.5 128.4 138.3 141.2 145.6 144.0 142.0 140.0 141.2 140.7 139.7 138.1 139.1 139.8 134.5 133.8 138.9 140.4 138.7 135.2 136.4 135.2 138.8 137.4 150.1 143.9 153.1 65.5 - - - - Gross Revenues $m 345.7 345.9 430.0 497.4 567.8 611.6 624.1 643.9 636.9 627.8 619.1 624.5 622.0 617.8 610.7 615.1 618.1 594.5 591.5 614.0 621.0 613.3 598.0 603.0 597.6 613.8 607.5 663.8 636.0 676.7 289.6 - - - - Less Smelting, refining & transportation $m (32.6) (34.6) (36.1) (36.9) (39.7) (41.2) (41.6) (41.9) (41.9) (41.7) (41.8) (41.4) (41.8) (41.6) (41.6) (41.3) (41.3) (41.0) (40.7) (40.8) (41.0) (41.0) (40.8) (41.1) (41.1) (41.4) (42.2) (42.0) (41.5) (41.3) (24.4) - - - - Net Smelting Returns $m 313.1 311.4 394.0 460.5 528.1 570.4 582.5 602.0 595.0 586.1 577.3 583.1 580.2 576.2 569.1 573.8 576.8 553.5 550.8 573.2 579.9 572.3 557.2 562.0 556.5 572.5 565.3 621.8 594.5 635.5 265.2 - - - - Less Mine operating costs $m (212.2) (207.2) (242.1) (244.0) (271.5) (290.3) (273.7) (284.3) (291.7) (287.9) (309.4) (313.8) (302.8) (311.6) (309.7) (299.6) (300.4) (303.7) (307.0) (306.8) (308.5) (300.8) (295.6) (277.7) (285.8) (232.5) (229.7) (232.7) (227.1) (220.2) (91.7) - - - - Recycling credit - including interest income $m 11.8 17.8 26.4 30.7 35.0 35.7 37.9 34.7 33.4 33.5 30.8 30.6 27.6 26.8 29.5 30.7 30.7 30.4 30.7 30.7 30.0 29.4 25.9 25.6 25.8 29.6 29.8 31.0 31.1 28.7 15.6 - - - - Less Royalties $m (13.3) (13.3) (16.8) (19.6) (22.5) (24.2) (24.8) (25.5) (25.2) (24.8) (24.5) (24.7) (24.5) (24.4) (24.1) (24.3) (24.5) (23.5) (23.4) (24.3) (24.6) (24.2) (23.5) (23.7) (23.5) (24.3) (24.0) (26.3) (25.2) (26.8) (11.2) - - - - Less Production taxes $m (13.1) (13.1) (15.8) (18.0) (20.3) (21.6) (22.1) (22.6) (22.4) (22.1) (21.8) (22.0) (21.9) (21.7) (21.6) (21.7) (21.8) (21.1) (21.0) (21.7) (21.9) (21.7) (21.1) (21.3) (21.1) (21.7) (21.4) (23.3) (22.4) (23.7) (11.5) - - - - Less Insurance $m (7.8) (8.3) (8.4) (8.4) (8.5) (8.5) (8.5) (8.6) (8.6) (8.5) (8.5) (8.5) (8.5) (8.5) (8.5) (8.5) (8.6) (8.5) (8.5) (8.5) (8.5) (8.5) (8.5) (8.5) (8.5) (8.5) (8.6) (8.6) (8.6) (8.6) (8.1) - - - - EBITDA $m 78.3 87.4 137.3 201.2 240.4 261.4 291.3 295.7 280.6 276.2 243.9 244.7 250.0 236.8 234.7 250.2 252.3 227.2 221.6 242.5 246.4 246.5 234.3 256.4 243.3 315.1 311.4 361.9 342.3 384.9 158.3 - - - - Less Closure Costs $m - - - - - - - - - - - - - - - - - - - - - - - - - - - - - - - (22.8) (22.8) (11.4) - Net Income (loss) before incom e taxes $m 78.3 87.4 137.3 201.2 240.4 261.4 291.3 295.7 280.6 276.2 243.9 244.7 250.0 236.8 234.7 250.2 252.3 227.2 221.6 242.5 246.4 246.5 234.3 256.4 243.3 315.1 311.4 361.9 342.3 384.9 158.3 (22.8) (22.8) (11.4) (0.0) Less 24.37% Income Tax % $m (19.1) (21.3) (33.5) (49.0) (58.6) (63.7) (71.0) (72.1) (68.4) (67.3) (59.4) (59.6) (60.9) (57.7) (57.2) (61.0) (61.5) (55.4) (54.0) (59.1) (60.0) (60.1) (57.1) (62.5) (59.3) (76.8) (75.9) (88.2) (83.4) (93.8) (38.6) - - - - Net Income (loss) $m 59.2 66.1 103.9 152.1 181.8 197.7 220.3 223.6 212.2 208.9 184.5 185.1 189.1 179.1 177.5 189.3 190.8 171.8 167.6 183.4 186.3 186.5 177.2 193.9 184.0 238.3 235.5 273.7 258.9 291.1 119.7 (22.8) (22.8) (11.4) (0.0) Less Capital Expenditure $m (111.6) (172.1) (190.6) (166.2) (112.1) (147.3) (162.1) (169.0) (130.3) (121.3) (92.9) (77.4) (88.3) (78.7) (76.5) (84.0) (93.4) (77.5) (63.2) (60.5) (48.9) (52.5) (52.6) (54.3) (44.8) (33.2) (30.9) (22.6) (13.2) (15.5) (10.9) - - - - Net Cash Flow $m (52.3) (106.0) (86.8) (14.1) 69.7 50.4 58.2 54.6 81.9 87.6 91.6 107.6 100.8 100.3 101.0 105.2 97.5 94.3 104.4 122.9 137.4 133.9 124.7 139.5 139.2 205.1 204.6 251.0 245.7 275.6 108.8 (22.8) (22.8) (11.4) (0.0) Cumulative Cash Flow $m (52.3) (158.3) (245.1) (259.2) (189.4) (139.1) (80.9) (26.2) 55.6 143.3 234.8 342.5 443.2 543.6 644.5 749.7 847.2 941.6 1,045.9 1,168.9 1,306.3 1,440.2 1,564.9 1,704.4 1,843.7 2,048.7 2,253.3 2,504.3 2,750.1 3,025.6 3,134.5 3,111.7 3,088.9 3,077.5 3,077.5 Stillwater After Tax NPV5% $m 1,060.9 Combined Mines 2024 2025 2026 2027 2028 2029 2030 2031 2032 2033 2034 2035 2036 2037 2038 2039 2040 2041 2042 2043 2044 2045 2046 2047 2048 2049 2050 2051 2052 2053 2054 2055 2056 2057 2058 Palladium ounces produced 357,601 357,705 418,482 475,999 519,552 546,719 554,431 566,665 562,337 556,729 553,886 557,433 551,390 549,135 543,945 545,356 544,308 534,177 534,301 549,043 551,745 548,900 537,695 536,935 532,917 545,317 525,980 573,931 557,236 581,864 340,734 148,792 157,021 167,276 158,651 Platinum ounces produced 103,718 103,749 121,465 138,187 150,917 158,858 161,112 164,688 163,422 161,783 160,938 161,974 160,233 159,572 158,059 158,479 158,189 155,202 155,228 159,532 160,331 159,489 156,223 156,023 154,852 158,463 152,897 166,840 161,957 169,159 98,689 42,658 45,017 47,957 45,484 Com bined ounces produced 461,319 461,453 539,947 614,186 670,469 705,576 715,542 731,353 725,759 718,512 714,824 719,407 711,623 708,707 702,004 703,834 702,497 689,379 689,528 708,575 712,076 708,389 693,918 692,958 687,769 703,780 678,877 740,771 719,193 751,023 439,422 191,450 202,039 215,233 204,135 Palladium revenues $m 447.0 447.1 523.1 595.0 649.4 683.4 693.0 708.3 702.9 695.9 692.4 696.8 689.2 686.4 679.9 681.7 680.4 667.7 667.9 686.3 689.7 686.1 672.1 671.2 666.1 681.6 657.5 717.4 696.5 727.3 425.9 186.0 196.3 209.1 198.3 Platinum revenues $m 129.6 129.7 151.8 172.7 188.6 198.6 201.4 205.9 204.3 202.2 201.2 202.5 200.3 199.5 197.6 198.1 197.7 194.0 194.0 199.4 200.4 199.4 195.3 195.0 193.6 198.1 191.1 208.5 202.4 211.4 123.4 53.3 56.3 59.9 56.9 Gross Revenues $m 576.6 576.8 674.9 767.7 838.1 882.0 894.4 914.2 907.2 898.1 893.5 899.3 889.5 885.9 877.5 879.8 878.1 861.7 861.9 885.7 890.1 885.5 867.4 866.2 859.7 879.7 848.6 926.0 899.0 938.8 549.3 239.3 252.5 269.0 255.2 Less Smelting, refining & transportation $m (56.1) (59.9) (58.2) (59.6) (61.2) (62.1) (62.3) (62.6) (62.5) (62.5) (62.3) (62.7) (62.4) (62.4) (62.3) (62.5) (62.5) (62.4) (62.5) (62.9) (62.8) (62.8) (62.7) (62.6) (62.4) (62.5) (61.7) (62.8) (62.6) (62.2) (54.0) (47.2) (47.5) (48.0) (47.6) Net Smelting Returns $m 520.6 516.9 616.8 708.1 776.9 819.9 832.1 851.6 844.7 835.7 831.3 836.6 827.2 823.5 815.2 817.3 815.6 799.3 799.4 822.8 827.3 822.7 804.7 803.6 797.3 817.3 786.9 863.2 836.4 876.6 495.3 192.1 205.0 221.1 207.6 Less Mine operating costs $m (334.7) (328.1) (363.4) (371.7) (392.0) (406.1) (407.9) (412.6) (431.1) (423.1) (438.3) (454.5) (438.0) (442.7) (443.7) (424.3) (427.1) (437.7) (444.2) (442.1) (437.8) (427.8) (426.8) (409.3) (421.2) (367.0) (361.2) (360.2) (369.0) (351.9) (217.0) (134.9) (139.2) (142.0) (133.9) Recycling credit - including interest income $m 19.7 29.7 41.5 47.4 51.6 51.4 54.3 49.3 47.6 47.9 44.5 44.1 39.4 38.5 42.4 43.8 43.7 44.1 44.7 44.3 42.9 42.5 37.6 36.8 37.1 42.4 41.7 43.2 43.9 39.8 29.5 19.8 19.6 20.7 20.0 Less Royalties $m (24.5) (24.3) (28.7) (32.9) (35.8) (37.6) (38.2) (38.9) (38.6) (38.2) (38.0) (38.2) (37.7) (37.5) (37.2) (37.3) (37.2) (36.6) (36.6) (37.6) (37.7) (37.6) (36.7) (36.6) (36.3) (37.3) (35.8) (39.2) (38.1) (39.7) (23.6) (10.4) (11.0) (11.9) (11.2) Less Production taxes $m (21.3) (21.1) (24.4) (27.4) (29.7) (31.1) (31.6) (32.1) (31.9) (31.6) (31.4) (31.6) (31.2) (31.1) (30.9) (31.0) (30.9) (30.4) (30.4) (31.1) (31.3) (31.1) (30.5) (30.4) (30.2) (31.0) (30.0) (32.5) (31.6) (32.8) (20.4) (7.7) (8.0) (8.6) (8.1) Less Insurance $m (11.9) (12.6) (12.6) (12.6) (12.6) (12.6) (12.6) (12.6) (12.6) (12.6) (12.6) (12.6) (12.6) (12.6) (12.6) (12.6) (12.6) (12.6) (12.6) (12.6) (12.6) (12.6) (12.6) (12.6) (12.6) (12.6) (12.6) (12.6) (12.6) (12.6) (12.6) (5.8) (5.8) (5.8) (5.8) EBITDA $m 147.9 160.6 229.1 311.0 358.4 383.8 396.1 404.7 378.1 378.1 355.3 343.8 347.0 338.0 333.2 356.0 351.4 326.1 320.2 343.6 350.7 356.0 335.7 351.4 334.0 411.7 388.9 461.9 428.9 479.3 251.3 53.2 60.6 73.6 68.5 Less Closure Costs $m - - - - - - - - - - - - - - - - - - - - - - - - - - - - - - - (22.8) (22.8) (11.4) - Net Income (loss) before incom e taxes $m 147.9 160.6 229.1 311.0 358.4 383.8 396.1 404.7 378.1 378.1 355.3 343.8 347.0 338.0 333.2 356.0 351.4 326.1 320.2 343.6 350.7 356.0 335.7 351.4 334.0 411.7 388.9 461.9 428.9 479.3 251.3 30.4 37.8 62.2 68.5 Less 24.37% Income Tax % $m (36.0) (39.1) (55.8) (75.8) (87.3) (93.5) (96.5) (98.6) (92.2) (92.1) (86.6) (83.8) (84.6) (82.4) (81.2) (86.7) (85.6) (79.5) (78.0) (83.7) (85.5) (86.8) (81.8) (85.6) (81.4) (100.3) (94.8) (112.6) (104.5) (116.8) (61.3) (7.4) (9.2) (15.1) (16.7) Net Income (loss) $m 111.9 121.4 173.3 235.2 271.1 290.3 299.6 306.0 286.0 285.9 268.7 260.0 262.4 255.6 252.0 269.2 265.8 246.6 242.2 259.9 265.3 269.2 253.9 265.8 252.6 311.4 294.1 349.4 324.4 362.5 190.1 23.0 28.6 47.0 51.8 Less Capital Expenditure $m (158.8) (242.3) (264.1) (227.8) (184.3) (195.2) (204.1) (208.8) (161.0) (155.8) (140.1) (115.9) (116.9) (114.8) (108.3) (163.2) (165.2) (136.2) (119.2) (102.9) (101.0) (104.0) (100.2) (96.1) (84.0) (73.7) (72.1) (68.8) (49.3) (58.6) (62.3) (56.5) (46.1) (41.1) (47.2) Net Cash Flow $m (46.9) (120.9) (90.8) 7.4 86.7 95.1 95.4 97.3 125.0 130.1 128.6 144.1 145.6 140.8 143.7 106.0 100.6 110.4 123.0 157.0 164.3 165.2 153.7 169.7 168.6 237.7 222.0 280.6 275.1 303.9 127.8 (33.5) (17.5) 6.0 4.7 Cumulative Cash Flow $m (46.9) (167.7) (258.6) (251.2) (164.5) (69.4) 26.0 123.3 248.3 378.4 507.0 651.2 796.7 937.5 1,081.2 1,187.2 1,287.8 1,398.3 1,521.2 1,678.2 1,842.5 2,007.7 2,161.4 2,331.1 2,499.7 2,737.4 2,959.4 3,240.0 3,515.1 3,819.0 3,946.7 3,913.2 3,895.7 3,901.6 3,906.3 Com bined After Tax NPV5% $m 1,511.7
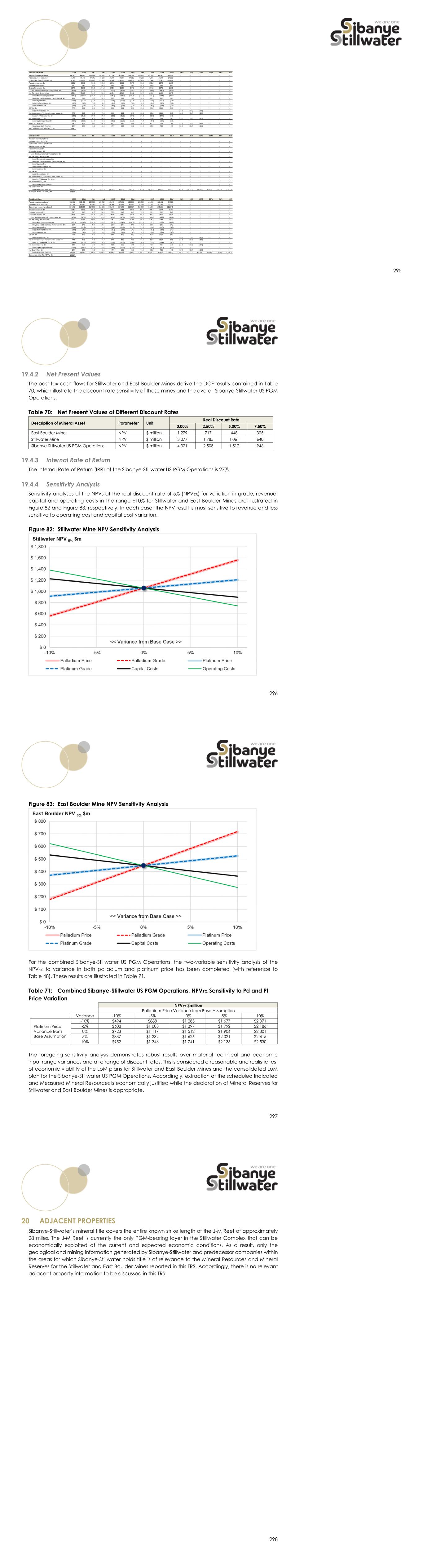
295 East Boulder Mine 2059 2060 2061 2062 2063 2064 2065 2066 2067 2068 2069 2070 2071 2072 2073 2074 2075 Palladium ounces produced 166,552 165,482 166,535 164,262 163,240 167,056 166,088 166,862 164,255 165,992 94,538 - - - - - - Platinum ounces produced 47,750 47,443 47,745 47,093 46,800 47,894 47,616 47,838 47,091 47,589 27,103 - - - - - - Combined ounces produced 214,302 212,925 214,280 211,355 210,040 214,951 213,704 214,700 211,346 213,581 121,641 - - - - - - Palladium revenues $m 208.2 206.9 208.2 205.3 204.1 208.8 207.6 208.6 205.3 207.5 118.2 - - - - - - Platinum revenues $m 59.7 59.3 59.7 58.9 58.5 59.9 59.5 59.8 58.9 59.5 33.9 - - - - - - Gross Revenues $m 267.9 266.2 267.8 264.2 262.6 268.7 267.1 268.4 264.2 267.0 152.1 - - - - - - Less Smelting, ref ining & transportation $m (47.8) (47.6) (47.7) (47.6) (47.4) (47.8) (48.0) (48.1) (48.0) (48.2) (44.9) - - - - - - Net Smelting Returns $m 220.1 218.6 220.2 216.6 215.1 220.9 219.1 220.2 216.2 218.8 107.2 - - - - - - Less Mine operating costs $m (137.1) (126.2) (131.7) (133.8) (125.7) (129.2) (131.3) (131.4) (117.1) (112.5) (83.7) - - - - - - Recycling credit - including interest income $m 20.6 20.6 20.7 20.5 20.3 20.7 20.7 20.8 20.5 20.7 13.5 - - - - - - Less Royalties $m (11.8) (11.7) (11.8) (11.6) (11.6) (11.9) (11.8) (11.8) (11.6) (11.7) (5.8) - - - - - - Less Production taxes $m (8.5) (8.5) (8.6) (8.4) (8.4) (8.6) (8.5) (8.5) (8.4) (8.5) (4.9) - - - - - - Less Insurance $m (5.8) (5.8) (5.8) (5.8) (5.8) (5.8) (5.8) (5.8) (5.8) (5.8) (5.8) - - - - - - EBITDA $m 77.5 86.9 83.0 77.4 84.0 86.2 82.5 83.5 93.8 101.0 20.5 - - - - - - Less Closure Costs $m - - - - - - - - - - - (13.8) (13.8) (6.9) - - - Net Income (loss) before income taxes $m 77.5 86.9 83.0 77.4 84.0 86.2 82.5 83.5 93.8 101.0 20.5 (13.8) (13.8) (6.9) - - - Less 24.37% Income Tax $m (18.9) (21.2) (20.2) (18.9) (20.5) (21.0) (20.1) (20.3) (22.9) (24.6) (5.0) - - - - - - Net Income (loss) $m 58.6 65.7 62.8 58.5 63.5 65.2 62.4 63.1 71.0 76.4 15.5 (13.8) (13.8) (6.9) - - - Less Capital Expenditure $m (33.9) (33.0) (16.8) (11.6) (15.8) (11.9) (16.5) (7.2) (5.7) (5.7) (5.7) - - - - - - NeT Cash Flow $m 24.7 32.7 46.0 46.9 47.7 53.3 45.9 56.0 65.2 70.8 9.8 (13.8) (13.8) (6.9) - - - Cumulative Cash Flow $m 24.7 32.7 46.0 46.9 47.7 53.3 45.9 56.0 65.2 70.8 9.8 (13.8) (13.8) (6.9) - - - East Boulder After Tax NPV5% $m 448.1 Stillwater Mine 2059 2060 2061 2062 2063 2064 2065 2066 2067 2068 2069 2070 2071 2072 2073 2074 2075 Palladium ounces produced - - - - - - - - - - - - - - - - - Platinum ounces produced - - - - - - - - - - - - - - - - - Combined ounces produced - - - - - - - - - - - - - - - - - Palladium revenues $m - - - - - - - - - - - - - - - - - Platinum revenues $m - - - - - - - - - - - - - - - - - Gross Revenues $m - - - - - - - - - - - - - - - - - Less Smelting, ref ining & transportation $m - - - - - - - - - - - - - - - - - Net Smelting Returns $m - - - - - - - - - - - - - - - - - Less Mine operating costs $m - - - - - - - - - - - - - - - - - Recycling credit - including interest income $m - - - - - - - - - - - - - - - - - Less Royalties $m - - - - - - - - - - - - - - - - - Less Production taxes $m - - - - - - - - - - - - - - - - - Less Insurance $m - - - - - - - - - - - - - - - - - EBITDA $m - - - - - - - - - - - - - - - - - Less Closure Costs $m - - - - - - - - - - - - - - - - - Net Income (loss) before income taxes $m - - - - - - - - - - - - - - - - - Less 24.37% Income Tax % $m - - - - - - - - - - - - - - - - - Net Income (loss) $m - - - - - - - - - - - - - - - - - Less Capital Expenditure $m - - - - - - - - - - - - - - - - - Net Cash Flow $m - - - - - - - - - - - - - - - - - Cumulative Cash Flow $m 3,077.5 3,077.5 3,077.5 3,077.5 3,077.5 3,077.5 3,077.5 3,077.5 3,077.5 3,077.5 3,077.5 3,077.5 3,077.5 3,077.5 3,077.5 3,077.5 3,077.5 Stillwater After Tax NPV5% $m 1,060.9 Combined Mines 2059 2060 2061 2062 2063 2064 2065 2066 2067 2068 2069 2070 2071 2072 2073 2074 2075 Palladium ounces produced 166,552 165,482 166,535 164,262 163,240 167,056 166,088 166,862 164,255 165,992 94,538 - - - - - - Platinum ounces produced 47,750 47,443 47,745 47,093 46,800 47,894 47,616 47,838 47,091 47,589 27,103 - - - - - - Combined ounces produced 214,302 212,925 214,280 211,355 210,040 214,951 213,704 214,700 211,346 213,581 121,641 - - - - - - Palladium revenues $m 208.2 206.9 208.2 205.3 204.1 208.8 207.6 208.6 205.3 207.5 118.2 - - - - - - Platinum revenues $m 59.7 59.3 59.7 58.9 58.5 59.9 59.5 59.8 58.9 59.5 33.9 - - - - - - Gross Revenues $m 267.9 266.2 267.8 264.2 262.6 268.7 267.1 268.4 264.2 267.0 152.1 - - - - - - Less Smelting, ref ining & transportation $m (47.8) (47.6) (47.7) (47.6) (47.4) (47.8) (48.0) (48.1) (48.0) (48.2) (44.9) - - - - - - Net Smelting Returns $m 220.1 218.6 220.2 216.6 215.1 220.9 219.1 220.2 216.2 218.8 107.2 - - - - - - Less Mine operating costs $m (137.1) (126.2) (131.7) (133.8) (125.7) (129.2) (131.3) (131.4) (117.1) (112.5) (83.7) - - - - - - Recycling credit - including interest income $m 20.6 20.6 20.7 20.5 20.3 20.7 20.7 20.8 20.5 20.7 13.5 - - - - - - Less Royalties $m (11.8) (11.7) (11.8) (11.6) (11.6) (11.9) (11.8) (11.8) (11.6) (11.7) (5.8) - - - - - - Less Production taxes $m (8.5) (8.5) (8.6) (8.4) (8.4) (8.6) (8.5) (8.5) (8.4) (8.5) (4.9) - - - - - - Less Insurance $m (5.8) (5.8) (5.8) (5.8) (5.8) (5.8) (5.8) (5.8) (5.8) (5.8) (5.8) - - - - - - EBITDA $m 77.5 86.9 83.0 77.4 84.0 86.2 82.5 83.5 93.8 101.0 20.5 - - - - - - Less Closure Costs $m - - - - - - - - - - - (13.8) (13.8) (6.9) - - - Net Income (loss) before income taxes $m 77.5 86.9 83.0 77.4 84.0 86.2 82.5 83.5 93.8 101.0 20.5 (13.8) (13.8) (6.9) - - - Less 24.37% Income Tax % $m (18.9) (21.2) (20.2) (18.9) (20.5) (21.0) (20.1) (20.3) (22.9) (24.6) (5.0) - - - - - - Net Income (loss) $m 58.6 65.7 62.8 58.5 63.5 65.2 62.4 63.1 71.0 76.4 15.5 (13.8) (13.8) (6.9) - - - Less Capital Expenditure $m (33.9) (33.0) (16.8) (11.6) (15.8) (11.9) (16.5) (7.2) (5.7) (5.7) (5.7) - - - - - - Net Cash Flow $m 24.7 32.7 46.0 46.9 47.7 53.3 45.9 56.0 65.2 70.8 9.8 (13.8) (13.8) (6.9) - - - Cumulative Cash Flow $m 3,931.0 3,963.7 4,009.7 4,056.6 4,104.3 4,157.6 4,203.5 4,259.5 4,324.7 4,395.4 4,405.3 4,391.5 4,377.7 4,370.8 4,370.8 4,370.8 4,370.8 Combined After Tax NPV5% $m 1,511.7 296 Net Present Values The post-tax cash flows for Stillwater and East Boulder Mines derive the DCF results contained in Table 70, which illustrate the discount rate sensitivity of these mines and the overall Sibanye-Stillwater US PGM Operations. Table 70: Net Present Values at Different Discount Rates Description of Mineral Asset Parameter Unit Real Discount Rate 0.00% 2.50% 5.00% 7.50% East Boulder Mine NPV $ million 1 279 717 448 305 Stillwater Mine NPV $ million 3 077 1 785 1 061 640 Sibanye-Stillwater US PGM Operations NPV $ million 4 371 2 508 1 512 946 Internal Rate of Return The Internal Rate of Return (IRR) of the Sibanye-Stillwater US PGM Operations is 27%. Sensitivity Analysis Sensitivity analyses of the NPVs at the real discount rate of 5% (NPV5%) for variation in grade, revenue, capital and operating costs in the range ±10% for Stillwater and East Boulder Mines are illustrated in Figure 82 and Figure 83, respectively. In each case, the NPV result is most sensitive to revenue and less sensitive to operating cost and capital cost variation. Figure 82: Stillwater Mine NPV Sensitivity Analysis 297 Figure 83: East Boulder Mine NPV Sensitivity Analysis For the combined Sibanye-Stillwater US PGM Operations, the two-variable sensitivity analysis of the NPV5% to variance in both palladium and platinum price has been completed (with reference to Table 48). These results are illustrated in Table 71. Table 71: Combined Sibanye-Stillwater US PGM Operations, NPV5% Sensitivity to Pd and Pt Price Variation NPV5% $million Palladium Price Variance from Base Assumption Variance -10% -5% 0% 5% 10% Platinum Price Variance from Base Assumption -10% $494 $888 $1 283 $1 677 $2 071 -5% $608 $1 003 $1 397 $1 792 $2 186 0% $723 $1 117 $1 512 $1 906 $2 301 5% $837 $1 232 $1 626 $2 021 $2 415 10% $952 $1 346 $1 741 $2 135 $2 530 The foregoing sensitivity analysis demonstrates robust results over material technical and economic input range variances and at a range of discount rates. This is considered a reasonable and realistic test of economic viability of the LoM plans for Stillwater and East Boulder Mines and the consolidated LoM plan for the Sibanye-Stillwater US PGM Operations. Accordingly, extraction of the scheduled Indicated and Measured Mineral Resources is economically justified while the declaration of Mineral Reserves for Stillwater and East Boulder Mines is appropriate. 298 ADJACENT PROPERTIES Sibanye-Stillwater’s mineral title covers the entire known strike length of the J-M Reef of approximately 28 miles. The J-M Reef is currently the only PGM-bearing layer in the Stillwater Complex that can be economically exploited at the current and expected economic conditions. As a result, only the geological and mining information generated by Sibanye-Stillwater and predecessor companies within the areas for which Sibanye-Stillwater holds title is of relevance to the Mineral Resources and Mineral Reserves for the Stillwater and East Boulder Mines reported in this TRS. Accordingly, there is no relevant adjacent property information to be discussed in this TRS.

299 OTHER RELEVANT DATA AND INFORMATION Catalytic Converter Recycling Business Background As part of the smelting and refining operations, the Sibanye-Stillwater US PGM Operations include a recycling facility for spent automotive catalytic converters at the Columbus Metallurgical Complex. The recycle business is operated on both toll and outright purchase bases dependant on prevailing market conditions. However, under these scenarios, accurate sampling and analysis is critical to the business. The recycled catalytic converters are added to the concentrate from the mines in the electric arc furnace and the contained PGMs are recovered using the copper and nickel in the mine concentrate as collectors. The format of the catalytic converters varies with the origin of the supply. The European market has mostly diesel vehicles which use a silicon carbide substrate and recycle material from this area tend to be higher in carbon content. However, the North American market tends to supply an exclusively palladium containing recycle material. Carbon and silicon carbide are problematic to the smelting process dependant on the levels contained and, therefore, are measured and managed accordingly. Recycle Processing The recycle materials are delivered in bulk bags with a mass and chemical analysis per bag from the supplier but the official mass and analytical measurements are performed by Sibanye-Stillwater US PGM Operations. The bags are stored until the furnace feed recipe allows for processing (based on the contained carbon) and then delivered into the process via the sampling plant. The bags are weighed, and the contents introduced into the sampling plant which produces a bulk sample equivalent to approximately 1.6% of the bulk mass which is then further reduced to produce the final samples for the laboratory analysis. Samples received are ground in a fully automated grinding and blending machine (HPM1500), analysed for carbon using a Leco™ analyser and pulverised. Carbon analysis is performed ahead of any other analysis to ensure that the process critical carbon levels are in line with the levels reported by the customer. This carbon analysis is used to inform the blending and processing of recycle materials to ensure excess carbon is not added into the smelting process. The pulverised material is subjected to preliminary XRF analysis then dual analysis through XRF (Panalytical Energy Dispersive XRF) and PbFA and ICP-OES. The sampled and crushed recycle materials are introduced into the smelting process via a dedicated hopper in the batching plant and are then blended into the primary furnace feed via the computer control system. The copper and nickel in the matte from the mine concentrates act as a collector for the Pd and Pt present in the smelter feed stream originating from both mine concentrates and recycle materials. As such, it is critical that the recycle materials are balanced with the mine concentrates to ensure sufficient collection capacity for the total PGM loading delivered. 300 Recycling Operations The catalyst recycling business forms an integral part of the Columbus Metallurgical Complex processing feedstock but is not relevant to the declaration of Mineral Reserves for Stillwater and East Boulder Mines. However, revenue credits from the recycling business and by-products often exceed the operating cost for the smelting and refining operations, which underscores the importance of these two additional revenue sources to the value of the Sibanye-Stillwater US PGM Operations. 301 INTERPRETATION AND CONCLUSIONS The Qualified Persons have extensively reviewed base geological, mining, ore processing, mineral beneficiation and environmental and permitting information and costs used to estimate the Mineral Resources and Mineral Reserves for the Sibanye-Stillwater US PGM Operations. From the review and participation in the Mineral Resource and Mineral Reserve estimation, the Qualified Persons are satisfied with the integrity of the base data, estimation processes and the final Mineral Resources and Mineral Reserves contained in this report. Below is a summary the Qualified Person’s interpretations and conclusions regarding the Mineral Resources and Mineral Reserves for the Sibanye-Stillwater US PGM Operations. The Sibanye-Stillwater US PGM Operations are well-established mining, ore processing and mineral beneficiation operations located in Montana and producing PGMs from the extraction of the J-M Reef, which is the highest-grade PGM deposit known to exist in the world. Sibanye-Stillwater has title (leased or held Mining Claims) in perpetuity over the entirety of the known outcrop of the J-M Reef along the Beartooth Mountains in Montana. It also holds surface rights (Tunnel and Mill Site Claims) over key land parcels on which mining infrastructure is built both at Stillwater and East Boulder Mines, with the mining complexes comprising underground mining and integrated ore processing infrastructure. The surface rights also provide servitude required to access the reef or to establish and connect surface infrastructure. A network comprising state roads and a Sibanye-Stillwater maintained road connects the mines, local towns and the Columbus Metallurgical Complex where the smelter, base metal refinery, laboratory and PGM catalyst recycling plant are situated. Regional power infrastructure is already installed providing adequate power supplies to the operations. In general, climatic conditions in this area do not significantly affect the operations at the three sites. However, a 500-year flood event in 2022 destroyed parts of State Highway 419 used to access Stillwater Mine and temporary suspension of the mining operations for seven weeks. A temporary road was built to reestablish access to and from the mine for essential shaft maintenance services and limited mining operations. Repairs were carried out on the damaged parts of the highway and access was restored in July 2023. Inclement weather in the form of heavy snow has temporarily restricted mine access, with no major impact on the operations, as snow removal and road maintenance have been adequate to quickly restore access. Whereas the regulatory framework for mining provides for a simplified system for obtaining and maintaining mining and surface title, the granting of permits and approvals for building a mine or expansions to existing mining operations is costly and can be a lengthy process. The 24-year-old Good Neighbor Agreement between Sibanye-Stillwater and the local authorities has facilitated seamless stakeholder participation in the scoping and review of applications for permits and approvals. Extensive exploration work spanning several decades and dominated by diamond drilling at Stillwater and East Boulder Mines produced data utilised for the evaluation of the J-M Reef. The J-M Reef is a world class magmatic reef-type PGM deposit in the geologically favourable Stillwater Complex. The extensive drillhole database accumulated from moderately spaced surface diamond drilling and closely spaced underground definition diamond drilling from footwall lateral drifts, complemented by 302 mining and ore processing information, has confirmed the presence and character of the Pd-Pt dominant mineralisation in the J-M Reef. The drilling strategy adopted is a consequence of the rugged terrain characterising the Beartooth Mountain area, the steep dips of the J-M Reef and high localised variability in the J-M Reef. The approaches employed for the collection, validation, processing and interpretation of drillhole data are in line with industry best practice. The extensive validated drillhole database forms the basis for the Mineral Resource estimates reported for Stillwater and East Boulder Mines. The combination of long-range continuity, occurrence at a consistent stratigraphic position and within a consistent stratigraphic sequence, localised thickness and grade variability and steep dips influences the drilling strategy and estimation approaches employed for the J-M Reef. Available data permitted the construction of 3D geological models and estimation of grades in areas supported by surface exploration and definition drillhole data classified as Measured and the remainder of the areas supported by surface drillhole data classified as Indicated or Inferred after consideration of geological confidence and knowledge. The estimation approaches are appropriate for the style and variability of the J-M Reef. The reporting of the Mineral Resources at the minimum mining width based on the dominant mechanised ramp and rill method used and 2E cut-off grade is well-reasoned. Detailed LoM plans for Stillwater and East Boulder Mines support the Mineral Reserve estimates reported by Sibanye-Stillwater for the Sibanye-Stillwater US PGM Operations. Modifying factors derived through reconciliation at the mines have been utilised for the conversion of Indicated and Measured Mineral Resources to Probable and Proven Mineral Reserves, respectively. The mechanised ramp and fill method, which is the dominant mining method, is well-understood at the mines and suited to the character and attitude of the J-M Reef. Mine designs for Stillwater and East Boulder Mines incorporate the hydrogeological and geotechnical models constructed from groundwater and geotechnical testwork, an extensive geotechnical database and historical experience at the mines. Ground support designs and procedures employed at the mines, which have been refined through ongoing continuous improvement initiatives, have minimised occurrences of major fall of ground occurrences. A higher- than-expected frequency of poor ground conditions at the Stillwater East Section has necessitated a revision of the mining plan, with fair and good ground types prioritised in the short to medium terms until a dedicated sand paste plant has been established in this area which would enable improved mining efficiencies when mining in areas of poor ground conditions. No significant groundwater inflows are experienced except when development extends into new areas, but these are addressed using existing procedures combining probe drilling, the use of drainholes and routine mine dewatering using cascading water pumps. The LoM production plans for Stillwater and East Boulder Mines were developed through a Mineral Resources to Mineral Reserve conversion process which utilised dilution factors and mining parameters informed by historical reconciliation results and performance. The use of factors aligned to historical performance enhances the achievability of the plans. The LoM plans envisage an important ore production tonnage ramp up at Stillwater Mine associated with the Stillwater East Section. The COVID- 19 pandemic restrictions, a 500-year flood event in FY2022 and a shaft incident in FY2023 interrupted the ramp up momentum. The LoM plan for East Boulder Mine envisages modest changes to production but the production levels are aligned with historical production levels after the implementation of the Fill The Mill Project. The COVID-19 pandemic restrictions as well technical staff turnover affected production

303 output in FY2022. The LoM plans for Stillwater and East Boulder Mines were subjected to economic viability testing to demonstrate that extraction of the scheduled Indicated and Measured Mineral Resources is economically justified. Furthermore, most of the key infrastructure for mining is already installed at the Stillwater and East Boulder Mines. Similarly, most of the mining equipment required for the execution of the plans is available at the mines. Bulk power and water supplies are secure, and the infrastructure upgrades required have been completed ahead of the achievement of steady state production levels. The concentrators employed for ore processing at Stillwater and East Boulder Mines have been operational for several decades and use proven technology and process routes. Furthermore, the forecast metallurgical recoveries and production profiles employed in the LoM plans are informed by historical experience. A recent concentrator capacity upgrade at Stillwater Mine accommodates increasing RoM ore production from the Stillwater East Section until FY2028. Further upgrades of the flotation cell capacity prior to FY2029 will eliminate the bottleneck in this area which is restricting plant capacity to below the planned steady state production levels. The LoM plan for East Boulder Mine benefits from surplus concentrator capacity. There is adequate storage capacity for the tailings resulting from ore processing at the concentrators at both Stillwater and East Boulder Mines in the short to medium terms. However, additional tailings storage capacity will be required for the remainder of the LoMs. Plans being considered for the upgrading the TSF capacities for the long-term disposal of the tailings include storage capacity upgrades at existing TSFs through elevation lifts and lateral expansions as well as the establishment of new TSFs. Sibanye-Stillwater is aware of the long timeframes for the granting of permits and related approvals of the upgrades and establishment of new TSFs. As a result, it will expedite the finalisation of the long-term tailings storage plans required to enable the undertaking of the requisite studies needed for permit and approval applications. The smelter and base metal refinery at the Columbus Metallurgical Complex utilise proven technology and process routes for the processing of concentrate and matte, respectively. There are no plans to introduce new processing technology at the processing facilities. Modest capacity upgrades and debottlenecking projects implemented to accommodate increased concentrate production from the Stillwater and East Boulder Mines have been concluded, with the bottleneck in the flotation circuits at the Stillwater Concentrator being the exception. The LoM plans for Stillwater and East Boulder Mines and the Columbus Metallurgical Complex provide for appropriate capital expenditure budgets for the sustainability of the operations and for the various capacity upgrades and production expansions envisaged. Sustaining capital costs are benchmarked to historical capital expenditure. Similarly, the forecast operating costs included in the LoM plans are based on actual costs at the operations, with adjustments made for escalation as required. The importance of the catalyst recycling business and by-products to the Sibanye-Stillwater US PGM Operations is manifested by revenue credits from these sources that often exceed the operating cost for the smelting and refining operations at the Columbus Metallurgical Complex. However, the recycling 304 business and the by-products are excluded from the Mineral Resources and Mineral Reserves for Stillwater and East Boulder Mines. Sibanye-Stillwater has all necessary rights and approvals to operate the mines, concentrators, TSFs, waste rock storage dumps, smelter and ancillary facilities associated with the Sibanye-Stillwater US PGM Operations. Appropriate additional studies, designs and permitting documents have been or are in the process of being completed to support the planned operational expansions. Current permit and license violations are being corrected and environmental impacts are being managed in close consultation with the appropriate agencies. There are reasonable prospects that the operator’s licence to operate on these premises is secure for the foreseeable future, unless terminated by regulatory authorities for other reasons. Bonding amounts are deemed reasonable and appropriate for the permitted activities and obligations at both Stillwater and East Boulder Mines. Furthermore, based on assessment of the current permits, technical submittals, regulatory requirements and project compliance history, continued acquisition of permit approvals should be possible and there is low risk of rejections of permit applications by the regulatory for the foreseeable future. The prevailing market fundamentals for palladium and platinum are forecast to remain in place in the foreseeable future and the price forecasts and other economic assumptions utilised for economic viability testing of the LoM plans are reasonable. Sibanye-Stillwater’s risk management process has identified various material risks to LoM plans and Mineral Reserves relating to geotechnical and geohydrological uncertainties, inability to execute LoM plans, metal price downturns, inadequate tailings storage capacity, unplanned production cost escalation, unplanned power outages and restricted access to the operations caused by extreme weather events. Sibanye-Stillwater has mitigated (and not eliminated) these risks as per its risk management protocols to reduce the likelihood of occurrence and/or impact when the risk occurs which resulted in a reclassification of the residual risks as low to medium risks. The Qualified Persons consider the risk management process robust and sufficient to identify material risks that should be mitigated to enhance the achievability of the LoM plans. From their appraisal of the residual risks after mitigation, the Qualified Persons could not identify any unmitigated material risks to the LoM plans and Mineral Reserves associated with the modifying factors or resulting from changes to any aspect of the modifying factors. The Qualified Persons could not identify any residual material risks that would affect the Mineral Resources and Mineral Reserves reported for Stillwater and East Boulder Mines or the projected economic outcomes. Sibanye-Stillwater is fully aware of the low to medium risks identified and have mitigation measures in place to minimise the impact of the risks on the mining, ore processing and mineral beneficiation operations in Montana. 305 RECOMMENDATIONS The Qualified Persons recommend further upgrades to the flotation circuits at the Stillwater Concentrator to increase plant capacity from 3 400 tons to 4 110 ton per day (i.e. 1.1 million tons to 1.4 million tons per year at 92% utilisation) prior to FY2029 when production targets set out in the LoM plan exceed the current 1.1-million-toncapacity. Mechanical equipment needed for the flotation circuit upgrades has already been procured as part of the Blitz Project. Sibanye-Stillwater has undertaken to complete this work at an additional cost of approximately $1.8 million (labour cost) a year before the capacity of 1.4 million tons is required. As a result, the Qualified Persons are satisfied with the quantum of the additional cost set out above and the timeframe for the upgrades. There are no specific recommendations for additional work at East Boulder Mine or the Columbus Metallurgical Complex. The geological models and LoM plans for the operations will be updated and refined as new information becomes available. Most of the costs associated with the generation of new data and updates of the geological models and LoM plans as well as Mineral Resource and Mineral Reserve estimates are accounted for in the capital and operating cost budgets. The Qualified Persons do not anticipate significant additional costs for the undertaking of this work. 306 RELIANCE ON INFORMATION PROVIDED BY REGISTRANT The Qualified Persons have relied on information provided by the Registrant in preparing the findings and conclusions regarding the following aspects of the modifying factors outside of the Qualified Persons’ expertise: Macroeconomic trends, data and assumptions – Section 19; Marketing information and plans within the control of the registrant – Section 16; Legal matters outside the expertise of the qualified person – Sections 3.3 and 3.4; Environmental matters outside the expertise of the Qualified Person – Section 17; and Governmental factors outside the expertise of the Qualified Person – Sections 3.2, 3.4, 17 and 20.

307 QUALIFIED PERSON’S CONSENT AND SIGN-OFF Based on the technical support and advice from the in-house Technical Experts/Specialists who have identified no fatal flaws in the data and information pertaining to their technical disciplines and the operations, the Qualified Persons consider it reasonable to rely upon the information on the Sibanye- Stillwater US PGM Operations provided by Sibanye-Stillwater (the registrant). 308 I, Jeff Hughs, am a Qualified Person pursuant to Subpart 1300 of Regulation S-K of the US Securities Act of 1933 (SK-1300) with the responsibility for the preparation and sign-off of the Mineral Resources for the Stillwater and East Boulder Mines. I hereby consent to the following: the public filing and use by Sibanye-Stillwater of the Technical Report Summary for the Sibanye- Stillwater US PGM Operations effective 31 December 2023; the use and reference to my name, including my status as an expert or “Qualified Person” (as defined by SK-1300) in connection with the Technical Report Summaries for which I am responsible; the use of any extracts from, information derived from or summary of the Technical Report Summaries for which I am responsible in the annual report of Sibanye-Stillwater on Form 20-F for the year ended 31 December 2023 (Form 20-F); and the incorporation by reference of the above items as included in the Form 20-F into any registration statement filed by Sibanye-Stillwater. I certify that I have read the Technical Report Summary of the Sibanye-Stillwater US PGM Operations effective 31 December 2023 being filed by Sibanye-Stillwater that supports the disclosure of the Mineral Resources and Mineral Reserves for the Stillwater and East Boulder Mines. I also certify that the Technical Report Summary of the Sibanye-Stillwater US PGM Operations fairly and accurately represents the information in the sections for which I am responsible. I certify that I have read the Form 20-F and that it fairly and accurately represents the information in the Technical Report Summaries for which I am responsible. Dated this: April 19, 2024 /s/ Jeffrey J. Hughs ________________________ Signature of Qualified Person Jeffrey J. Hughs _______________________ Full Name of Qualified Person AIPG CPG – 11792 ________________________ Professional Registration 309 I, Jennifer Evans, am a Qualified Person pursuant to Subpart 1300 of Regulation S-K of the US Securities Act of 1933 (SK-1300) with the responsibility for the preparation and sign-off of the Mineral Resources for the East Boulder Mine. I hereby consent to the following: the public filing and use by Sibanye-Stillwater of the Technical Report Summary for the Sibanye- Stillwater US PGM Operations effective 31 December 2023; the use and reference to my name, including my status as an expert or “Qualified Person” (as defined by SK-1300) in connection with the Technical Report Summaries for which I am responsible; the use of any extracts from, information derived from or summary of the Technical Report Summaries for which I am responsible in the annual report of Sibanye-Stillwater on Form 20-F for the year ended 31 December 2023 (Form 20-F); and the incorporation by reference of the above items as included in the Form 20-F into any registration statement filed by Sibanye-Stillwater. I certify that I have read the Technical Report Summary of the Sibanye-Stillwater US PGM Operations effective 31 December 2023 being filed by Sibanye-Stillwater that supports the disclosure of the Mineral Resources and Mineral Reserves for the Stillwater and East Boulder Mines. I also certify that the Technical Report Summary of the Sibanye-Stillwater US PGM Operations fairly and accurately represents the information in the sections for which I am responsible. I certify that I have read the Form 20-F and that it fairly and accurately represents the information in the Technical Report Summaries for which I am responsible. Dated this: April 19, 2024 /s/ Jennifer A. Evans ________________________ Signature of Qualified Person Jennifer A. Evans ________________________ Full Name of Qualified Person AIPG CPG – 11669 ________________________ Professional Registration 310 I, Annette McFarland, am a Qualified Person pursuant to Subpart 1300 of Regulation S-K of the US Securities Act of 1933 (SK-1300) with the responsibility for the preparation and sign-off of the Mineral Reserves for the Stillwater Mine. I hereby consent to the following: the public filing and use by Sibanye-Stillwater of the Technical Report Summary for the Sibanye- Stillwater US PGM Operations effective 31 December 2023; the use and reference to my name, including my status as an expert or “Qualified Person” (as defined by SK-1300) in connection with the Technical Report Summaries for which I am responsible; the use of any extracts from, information derived from or summary of the Technical Report Summaries for which I am responsible in the annual report of Sibanye-Stillwater on Form 20-F for the year ended 31 December 2023 (Form 20-F); and the incorporation by reference of the above items as included in the Form 20-F into any registration statement filed by Sibanye-Stillwater. I certify that I have read the Technical Report Summary of the Sibanye-Stillwater US PGM Operations effective 31 December 2023 being filed by Sibanye-Stillwater that supports the disclosure of the Mineral Resources and Mineral Reserves for the Stillwater and East Boulder Mines. I also certify that the Technical Report Summary of the Sibanye-Stillwater US PGM Operations fairly and accurately represents the information in the sections for which I am responsible. I certify that I have read the Form 20-F and that it fairly and accurately represents the information in the Technical Report Summaries for which I am responsible. Dated this: April 19, 2024 /s/ Annette McFarland ________________________ Signature of Qualified Person Annette McFarland ________________________ Full Name of Qualified Person Professional Engineer Mining – No. 23215 ________________________ Professional Registration

311 I, Pat Hansen, am a Qualified Person pursuant to Subpart 1300 of Regulation S-K of the US Securities Act of 1933 (SK-1300) with the responsibility for the preparation and sign-off of the Mineral Reserves for the East Boulder Mine. I hereby consent to the following: the public filing and use by Sibanye-Stillwater of the Technical Report Summary for the Sibanye- Stillwater US PGM Operations effective 31 December 2023; the use and reference to my name, including my status as an expert or “Qualified Person” (as defined by SK-1300) in connection with the Technical Report Summaries for which I am responsible; the use of any extracts from, information derived from or summary of the Technical Report Summaries for which I am responsible in the annual report of Sibanye-Stillwater on Form 20-F for the year ended 31 December 2023 (Form 20-F); and the incorporation by reference of the above items as included in the Form 20-F into any registration statement filed by Sibanye-Stillwater. I certify that I have read the Technical Report Summary of the Sibanye-Stillwater US PGM Operations effective 31 December 2023 being filed by Sibanye-Stillwater that supports the disclosure of the Mineral Resources and Mineral Reserves for the Stillwater and East Boulder Mines. I also certify that the Technical Report Summary of the Sibanye-Stillwater US PGM Operations fairly and accurately represents the information in the sections for which I am responsible. I certify that I have read the Form 20-F and that it fairly and accurately represents the information in the Technical Report Summaries for which I am responsible. Dated this: April 19, 2024 /s/ Patrick Hansen ________________________ Signature of Qualified Person Patrick Hansen ________________________ Full Name of Qualified Person MT PE 75419 ________________________ Professional Registration 312 I, Matt Ladvala, am a Qualified Person pursuant to Subpart 1300 of Regulation S-K of the US Securities Act of 1933 (SK-1300) with the responsibility for the preparation and sign-off of the Mineral Resources for the Stillwater Mine. I hereby consent to the following: the public filing and use by Sibanye-Stillwater of the Technical Report Summary for the Sibanye- Stillwater US PGM Operations effective 31 December 2023; the use and reference to my name, including my status as an expert or “Qualified Person” (as defined by SK-1300) in connection with the Technical Report Summaries for which I am responsible; the use of any extracts from, information derived from or summary of the Technical Report Summaries for which I am responsible in the annual report of Sibanye-Stillwater on Form 20-F for the year ended 31 December 2023 (Form 20-F); and the incorporation by reference of the above items as included in the Form 20-F into any registration statement filed by Sibanye-Stillwater. I certify that I have read the Technical Report Summary of the Sibanye-Stillwater US PGM Operations effective 31 December 2023 being filed by Sibanye-Stillwater that supports the disclosure of the Mineral Resources and Mineral Reserves for the Stillwater and East Boulder Mines. I also certify that the Technical Report Summary of the Sibanye-Stillwater US PGM Operations fairly and accurately represents the information in the sections for which I am responsible. I certify that I have read the Form 20-F and that it fairly and accurately represents the information in the Technical Report Summaries for which I am responsible. Dated this: April 19, 2024 /s/ Matthew D. Ladvala ________________________ Signature of Qualified Person Matthew D. Ladvala ________________________ Full Name of Qualified Person AIPG CPG - 11941 ________________________ Professional Registration 313 I, Kevin Butak, am a Qualified Person pursuant to Subpart 1300 of Regulation S-K of the US Securities Act of 1933 (SK-1300) with the responsibility for the preparation and sign-off of the Mineral Resources for the Stillwater Mine. I hereby consent to the following: the public filing and use by Sibanye-Stillwater of the Technical Report Summary for the Sibanye- Stillwater US PGM Operations effective 31 December 2023; the use and reference to my name, including my status as an expert or “Qualified Person” (as defined by SK-1300) in connection with the Technical Report Summaries for which I am responsible; the use of any extracts from, information derived from or summary of the Technical Report Summaries for which I am responsible in the annual report of Sibanye-Stillwater on Form 20-F for the year ended 31 December 2023 (Form 20-F); and the incorporation by reference of the above items as included in the Form 20-F into any registration statement filed by Sibanye-Stillwater. I certify that I have read the Technical Report Summary of the Sibanye-Stillwater US PGM Operations effective 31 December 2023 being filed by Sibanye-Stillwater that supports the disclosure of the Mineral Resources and Mineral Reserves for the Stillwater and East Boulder Mines. I also certify that the Technical Report Summary of the Sibanye-Stillwater US PGM Operations fairly and accurately represents the information in the sections for which I am responsible. I certify that I have read the Form 20-F and that it fairly and accurately represents the information in the Technical Report Summaries for which I am responsible. Dated this: April 19, 2024 /s/ Kevin C. Butak ________________________ Signature of Qualified Person Kevin C. Butak ________________________ Full Name of Qualified Person AIPG CPG - 12012 _______________________ Professional Registration 314 REFERENCES Blakely, R.J., and Zientek, M.L., 1985. Magnetic anomalies over a mafic intrusion: The Stillwater Complex. The Stillwater Complex, Montana Bureau of Mines and Geology, Special Publication 92, 2002 reprint. Czamanske, G.K., and Zientek, M.L. eds. Boudreau, A., 1999. Fluid Fluxing of Cumulates: the J-M Reef and Associated Rocks of the Stillwater Complex, Montana, Journal of Petrology, Volume 40, pp 755-772. DEQ and USFS, 1985. Montana Department of Environmental Quality and U.S Forest Service. Final Environmental Impact Statement, Stillwater Project, December 1985. DEQ and USFS, 2012. Final Environmental Impact Statement, Stillwater Mining Company's Water Management Plans and Boe Ranch LAD, May 2012. DEQ and USFS, 2012a. Record of Decision for Stillwater Mining Company's Revised Water Management Plans and Boe Ranch LAD, Stillwater and Sweet Grass Counties, Montana (July 2012). DEQ and USFS, 2020. Draft Environmental Assessment East Boulder Mine Stage 6 Tailings Storage Facility Expansion Project, May 2020. DEQ, 2001. Montana Department of Environmental Quality Bonding Procedure Manual. 2001. Jenkins, M.C., Mungall, J.E., Zientek, M.L., Butak, K., Corson, M. Holick, P., McKinley, R., and Lowers, H., 2022. The Geochemical and Textural Transition between the Reef Package and its Hanging Wall, Stillwater Complex, Montana, USA. Journal of Petrology, 2022, 63, pp1-30. Kleinkopf, D.M., 1985. Regional gravity and magnetic anomalies of the Stillwater Complex area. The Stillwater Complex, Montana Bureau of Mines and Geology, Special Publication 92, 2002 reprint. Czamanske, G.K., and Zientek, M.L. eds. McCallum, I.S., 2002. The Stillwater Complex: A review of the geology. In: Boudreau, A.E., (ed.). Stillwater Complex, Geology and Guide. Billings, 21-25 July 2002, 9th International Platinum Symposium, A1-25. Page, N.J., and Zientek, M.L., 1985. Geologic and structural setting of the Stillwater Complex. The Stillwater Complex, Montana Bureau of Mines and Geology, Special Publication 92, 2002 reprint. Czamanske, G.K., and Zientek, M.L. eds. Stillwater Mining Company, Northern Plains Resource Council, Cottonwood Resource Council, Stillwater Protective Association, 2014. Good Neighbor Agreement. Amended December 8, 2014. Zientek, M.L., Czamanske, G.K., and Irvine, N.T., 1985. Stratigraphy and nomenclature for the Stillwater Complex. The Stillwater Complex, Montana Bureau of Mines and Geology, Special Publication 92, 2002 reprint. Czamanske, G.K., and Zientek, M.L. eds.