Mitsui Chemicals, Inc. (Headquarters: Chuo-ku, Tokyo, Representative Director and President: Osamu Hashimoto) will officially commence the operation of QR code-enabled yellow cards*1 for the prevention of serious accidents through dynamic monitoring of vehicle activities during the safe transportation of products and the prevention of secondary disasters after an accident occurs.
Since January 2024, a demonstration experiment on vehicle dynamics monitoring and QR codeification of yellow cards has been conducted, and due to the confirmation of its usefulness, full-scale operation has been decided.
The products of the Mitsui Chemicals Group include dangerous goods regulated by domestic laws such as the United Nations 'Recommendations on the Transport of Dangerous Goods'*2, the High-Pressure Gas Safety Law, the Fire Service Act, and the Poisonous and Deleterious Substances Control Law. These products (hereinafter referred to as hazardous materials) are handled and transported safely with the cooperation of logistics companies. However, due to numerous incidents of accidents and fires involving large cargo vehicles, the dynamics of vehicles have been systematized.
For vehicles transporting hazardous materials, Tire Pressure Monitoring Systems (TPMS) have been implemented. Additionally, according to the High-Pressure Gas Safety Law, when transporting liquefied gases, it is mandatory to check for abnormal pressure and leaks at the start and end of the move. Traditionally, crew members manually checked analog gauges. In contrast, a system has been introduced that monitors the temperature and pressure inside the tank of tanker trucks by applying the plant monitoring system of Mitsui Chemicals, converting these values into digital format, allowing crew members and operations managers to remotely detect signs of abnormalities and take preventive measures.
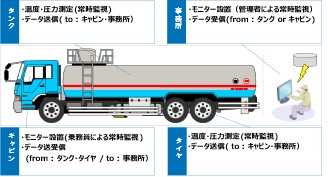
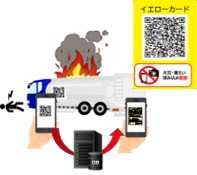
When transporting hazardous materials, it is mandatory to carry an emergency contact card (yellow card) in paper form. Mitsui Chemicals has started to affix QR codes containing this yellow card information to its transport vehicles. This initiative is expected to facilitate quick responses in the event of accidents, thereby reducing damage. Going forward, a highly advanced safety monitoring system utilizing DX technology for dangerous goods transportation will be actively introduced to improve safe and stable transport.
Our Logistics Department will continue to promote logistics DX utilizing digital technologies, with three pillars: DX of logistics RC, joint logistics DX, and visualization through logistics BI, pursuing a robust supply chain that can flexibly respond to changes in the logistics environment.
Our Logistics Department will continue to promote logistics DX utilizing digital technologies, with three pillars: DX of logistics RC, joint logistics DX, and visualization through logistics BI, pursuing a robust supply chain that can flexibly respond to changes in the logistics environment.
*1 Yellow Card: An emergency contact card that outlines the procedures to be followed by truck drivers and related personnel such as firefighters and police in the event of an accident when transporting chemicals and high-pressure gas. Promoted by the Japan Chemical Industry Association.
*2 Recommendations regarding hazardous materials transport: Recommendations issued every two years by the UN's Committee of Experts on the Transport of Dangerous Goods to ensure safety in international transport of hazardous goods. They are classified into the following nine categories based on their transport risks and harmfulness: 1: explosives, 2: compressed gases, 3: flammable liquids, 4: combustible materials, 5: oxidizing substances, 6: toxic substances, 7: radioactive materials, 8: corrosive substances, 9: other harmful substances.
That's all.