Source: LatePost, Author: Li Zinan.
Tesla will not launch new car models for sale this year, but there may be new batteries.
We have learned exclusively that Tesla plans to mass-produce the 4680 battery with dry electrode by the end of this year, which will be the 'complete version' of the 4680 battery.
In 2023, Tesla has used the 4680 battery in the cybertruck, but that was a compromise version that failed to achieve the goal of reinventing the battery manufacturing process, using dry electrodes instead of traditional wet electrodes, to eliminate the process of wetting and drying the electrode, and speed up production and reduce costs. Currently, the 4680 battery produced by Tesla only uses dry electrodes for the lower-cost negative electrode, while the higher-cost positive electrode is still purchased from LG new energy and two Chinese battery companies using traditional wet electrodes.
Now, Tesla is just one step away from the complete version of the 4680 battery. We have learned that the design of the 4680 battery with dry positive electrode has been finalized, which is the first step towards mass production. The Tesla battery department will then focus on improving the production yield and efficiency, and expanding capacity.
It is understood that $Tesla (TSLA.US)$Dry positive electrode rolls were already produced in the laboratory by the end of 2022. However, due to technical misjudgments, production could not be carried out for a long period of time. After Drew Baglino, the project leader, resigned in April this year, Tesla adjusted its technical route and achieved a breakthrough in mass production of dry positive electrodes.
'Dry electrodes can change Tesla.' said a Tesla insider.
The 4680 battery is Tesla's self-developed battery released in 2020. Tesla claimed that the new technology could reduce battery costs by 50% and bring cheaper cars.
The key to this significant cost reduction is the dry electrode process. The positive and negative electrode materials of existing power batteries are in a paste form, i.e. 'wet electrodes', which requires drying and solvent recovery in the battery production process, taking long time and occupying a large area of the production plant. Dry electrode production eliminates the above processes, greatly reduces the capital expenditure of unit battery production capacity and plant area, and improves battery performance and production efficiency.
Dry positive electrode is the most important and difficult breakthrough in the entire 4680 process, and positive electrode materials are also the highest cost components in the battery, accounting for more than 35%.
We have also learned that while tackling dry electrodes, Tesla is also continuing to improve the packaging process and material ratio of the current compromised version of 4680 batteries, which will be supplied to cybertruck first. Currently, Tesla's own production of 4680 batteries has a weekly capacity of only 1,000 cybertrucks.
Insiders said that among the material suppliers for the 4680 batteries produced by Tesla in the United States, there are hardly any Chinese companies left, and some of the production equipment has also been switched to Japanese and European and American companies, and the links still using Chinese equipment are also looking for alternative solutions.
On the other hand, Tesla also plans to have LG new energy directly supply complete wet positive electrode 4680 batteries later this year, which will be installed on the Model Y produced in the United States.
The 4680 battery is the core of Tesla's next generation product competitiveness, and dry positive electrodes are the core of 4680. Since its inception, Tesla has spent 5 years on this project.
After overcoming the R&D difficulties, the main problem now is engineering optimization.
'A simple winning rule for manufacturing is to make better things with less money than your competitors.'
Over the past 5 years, Tesla had a clear route to reduce costs and improve efficiency - shorten the body manufacturing time with a larger single-body press, design the next-generation car with fewer and easier-to-manufacture parts, compress battery manufacturing costs with dry electrode technology, shorten automobile assembly time and costs with 'unboxed' technology, and manufacture more efficient super factories.
Tesla has invested billions of dollars and a huge amount of engineering resources in these hardware and manufacturing innovations. If the plan is implemented, Tesla will maintain its leading gross margin and operating efficiency in the entire industry, just like it did 3 years ago.
Since April this year, however, Tesla has gradually suspended these efforts: suspending the production of low-priced models priced at $25,000, suspending the development of larger single-body press cars, and the next-generation super factory in Mexico, which should have been put into operation this year, has yet to begin construction.
The 4680 battery seemed to be at risk for a while, too. In April of this year, Drew Baglino, the project leader and senior vice president of Tesla's Powertrain and Energy Engineering, who had been with Tesla for 17 years, left his post, and the battery team cut about 25% of its staff in the same month, leaving fewer than 800 people.
We have followed up on the layoffs which mentioned that Tesla's management had proposed a clear assessment goal to the battery department earlier this year: if Tesla's self-produced 4680 battery cost cannot be lower than that of suppliers such as LG New Energy and Panasonic by the end of this year, Tesla will consider abandoning the self-produced 4680 battery. This is not a low standard target, and if Tesla can really achieve a lower self-production cost than LG, it will have the cheapest battery produced domestically in the United States. The recent progress in dry positive pole technology has given the battery department the possibility to achieve the year-end goal. After Baglino left, Tesla's battery team decided to take a slightly higher cost, but faster production route. Before that, Tesla's engineering team had already made dry positive pole rolls in the laboratory at the end of 2022, and the next step was to reproduce them on the production line. The rough process of current power battery production is to coat the paste-like positive and negative electrode materials on the foil to make the electrode sheet, then roll it into the electrode roll and put it into the battery shell, inject the electrolyte and complete the welding. However, in the production of the roll, Tesla was caught up by the rolling process. "The dry positive pole process encounters great challenges, the positive pole powder is very hard, and sometimes the equipment for the pole piece is damaged, which we did not expect," Musk said in the 2022 earnings conference call. An engineer who once worked in Tesla's battery department said that Tesla only has a small amount of customized and calibrated dry electrode rolling equipment. Each time this type of equipment fails, it takes at least 45 days to repair, which wastes a lot of time for the battery team. He remembered that when Baglino was still in office, he was questioned by Tesla's former CFO Zach Kirkhorn every week. "On the cost column chart, the cell department is pulled to the top, and other departments are at the bottom." The battery department had discussed leaving some of the engineering problems encountered by dry electrodes to the rolling and winding processes, because there is little room for modification and optimization of the rolling equipment. The source said that if this were done, things would be much simpler, and there are mature solutions from Japanese equipment companies, but Tesla needs to replace some production equipment, involving more equipment spending and other research and development uncertainties. This solution was not previously approved by Tesla's senior management. Recently, Tesla's battery department began to try the previously unapproved plan and used another set of equipment to solve the yield problem of the electrode roll after rolling and winding, making progress. A person close to Tesla said that the reason why the confidence of the battery department has increased recently is that they believe that the most difficult stage of research and development has passed, and the main problem now is engineering optimization. Tesla can improve its efficiency through some detailed improvements, such as a Tesla insider mentioned that when defective electrode sheets appear on the production line, ordinary battery companies will only cut off tens of centimeters of waste sheets, but Tesla will cut off several meters of rolls, which leads to higher defective losses and more difficult positioning of problems. "This is mainly because we don't have enough engineers to do tests," he said, but fortunately these tasks can be done by basic technicians to do more tests to improve. "The path is already relatively clear, and time can solve it."The weather is good today The weather is good today.Please use your Futubull account to access the feature.
The recent progress in dry positive pole technology has given the battery department the possibility to achieve the year-end goal.
After Baglino left, Tesla's battery team decided to take a slightly higher cost, but faster production route.
Before that, Tesla's engineering team had already made dry positive pole rolls in the laboratory at the end of 2022, and the next step was to reproduce them on the production line.
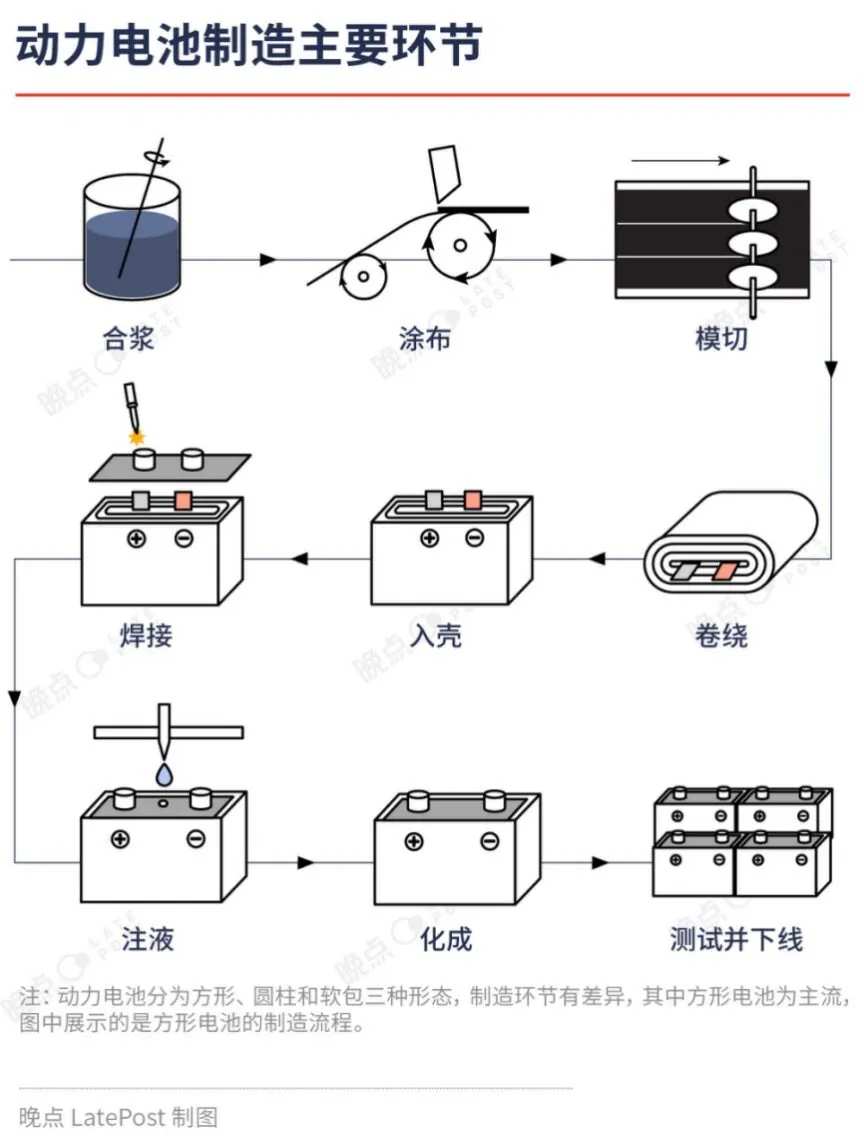
But in the production of the roll, Tesla was caught up by the rolling process. "The dry positive pole process encounters great challenges, the positive pole powder is very hard, and sometimes the equipment for the pole piece is damaged, which we did not expect," Musk said in the 2022 earnings conference call.
An engineer who once worked in Tesla's battery department said that Tesla only has a small amount of customized and calibrated dry electrode rolling equipment. Each time this type of equipment fails, it takes at least 45 days to repair, which wastes a lot of time for the battery team.
He remembered that when Baglino was still in office, he was questioned by Tesla's former CFO Zach Kirkhorn every week. "On the cost column chart, the cell department is pulled to the top, and other departments are at the bottom."
The battery department had discussed leaving some of the engineering problems encountered by dry electrodes to the rolling and winding processes, because there is little room for modification and optimization of the rolling equipment.
The source said that if this were done, things would be much simpler, and there are mature solutions from Japanese equipment companies, but Tesla needs to replace some production equipment, involving more equipment spending and other research and development uncertainties. This solution was not previously approved by Tesla's senior management.
Recently, Tesla's battery department began to try the previously unapproved plan and used another set of equipment to solve the yield problem of the electrode roll after rolling and winding, making progress.
A person close to Tesla said that the reason why the confidence of the battery department has increased recently is that they believe that the most difficult stage of research and development has passed, and the main problem now is engineering optimization.
Tesla can improve its efficiency through some detailed improvements, such as a Tesla insider mentioned that when defective electrode sheets appear on the production line, ordinary battery companies will only cut off tens of centimeters of waste sheets, but Tesla will cut off several meters of rolls, which leads to higher defective losses and more difficult positioning of problems.
"This is mainly because we don't have enough engineers to do tests," he said, but fortunately these tasks can be done by basic technicians to do more tests to improve. "The path is already relatively clear, and time can solve it."
Tesla has the possibility to self-produce a part of the battery and reduce dependence on external battery suppliers.
Before the 4680 battery, Tesla had never fully self-produced batteries. Tesla's first mass-produced cylindrical battery was produced in cooperation with Panasonic. After 2020, when Tesla, which had sold 0.5 million cars a year, formed a relatively stable battery supply pattern:
Among them, all square batteries are supplied by Contemporary Amperex Technology, mainly for the standard range Model 3 and Model Y; Contemporary Amperex Technology supplies not only Shanghai factories but also exports to Tesla's US factories; while cylindrical batteries come from Panasonic and LG, mainly used for long-range and high-end models.
Since 2023, Tesla has changed its battery supply chain by reducing its dependency on external suppliers, including those from China, with the production of its own 4680 batteries.
The 'compromise version' 4680 currently produced at the Texas factory in the US uses wet process positive electrodes from LG and two Chinese companies, as well as Tesla's own dry process negative electrodes.
If the production of dry process electrodes for the 4680 battery is successful and the yield reaches a high level, Tesla will be able to produce the 4680 battery completely on its own without relying on suppliers for core components.
External suppliers will lose some of Tesla's incremental orders. In Elon Musk's optimistic prediction for 2021, Tesla wants to produce at least 30% of its car batteries.
When Tesla starts making more of its own batteries, another opportunity for Chinese supply chain companies is to provide equipment. However, according to our understanding, Tesla has not yet contacted Chinese equipment suppliers for core processes such as dry electrode coating, rolling, and winding, with core suppliers from Japan and Germany.
However, there are still variables as to whether Tesla's dry process 4680 can maintain a cost advantage.
This depends on the speed of improvement in the yield and the speed of expansion. If the yield is too low, it will offset the benefits of reducing the drying and other production processes.
Meanwhile, since Tesla proposed the 4680 plan in 2020, other companies in the industry have followed suit, such as LG New Energy, EVE Energy, and Panasonic. Although Contemporary Amperex Technology is not optimistic about the 4680 route, it also has technical reserves and is studying dry process electrodes. Even if it is a little late, when other companies can also mass-produce dry process electrodes for the 4680, Tesla will face a new round of manufacturing efficiency competition. When all companies are using the same generation of technology, maximizing cost efficiency is not Tesla's strong suit.
Other manufacturers such as Contemporary Amperex Technology are also exploring the next generation of batteries, namely all-solid-state batteries, which also require dry process electrodes. It is an industry consensus that solid-state batteries are the best form of automotive batteries.
While conquering dry process electrodes for the 4680, Tesla is also deepening its cooperation with Chinese companies such as Contemporary Amperex Technology. At the beginning of this year, Contemporary Amperex Technology started co-building a lithium iron phosphate battery plant with Tesla in Nevada for energy storage. Tesla is buying existing battery production lines from Contemporary Amperex Technology, which provides some technical and procurement support and earns technology licensing fees.
At present, the cost of batteries from Contemporary Amperex Technology and BYD is about 0.33 yuan/Wh, which is still the cheapest and most cost-effective battery in the world.
Editor/Lambor